Used ESC ELAS #9131115 for sale
URL successfully copied!
Tap to zoom
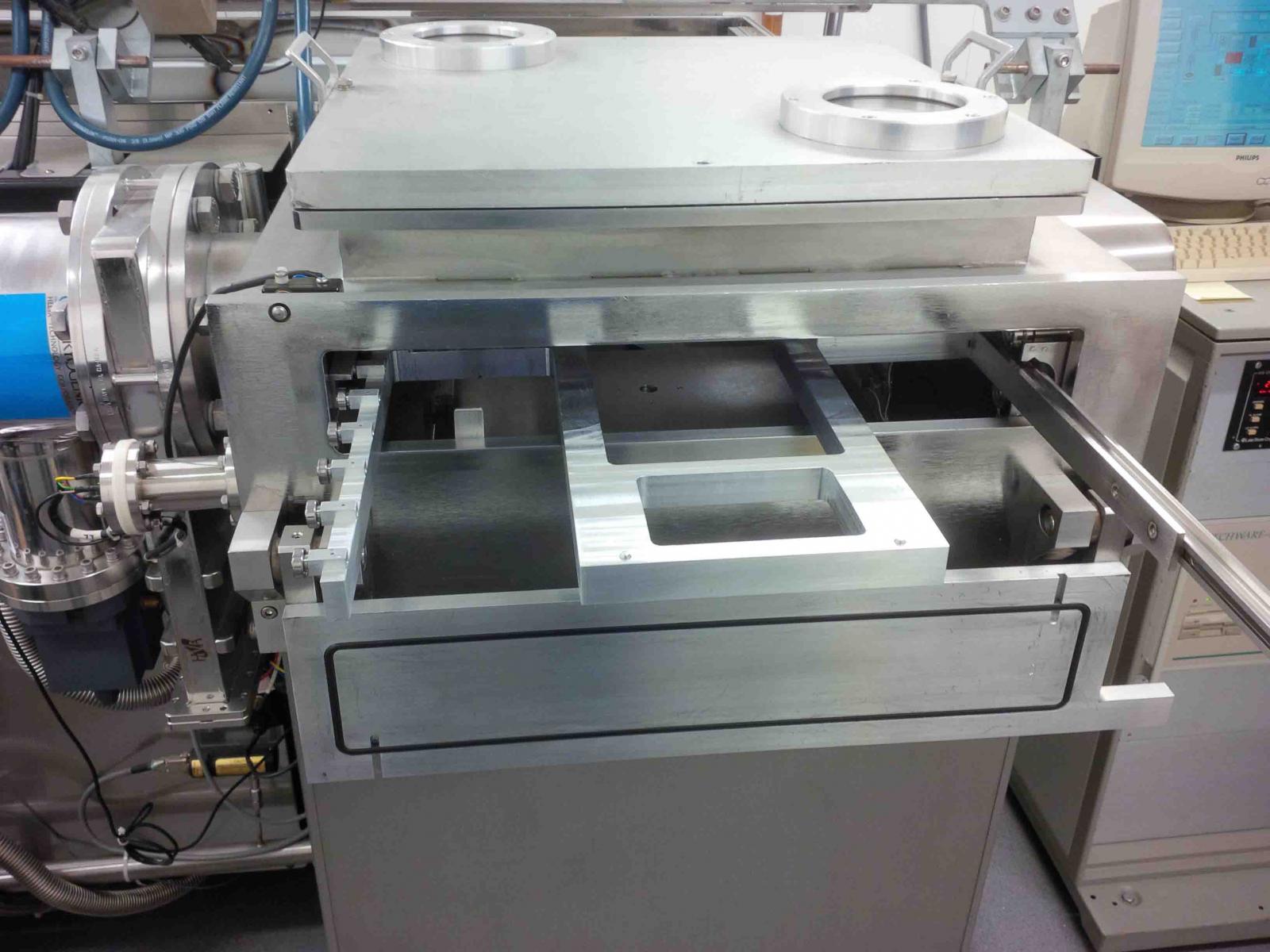

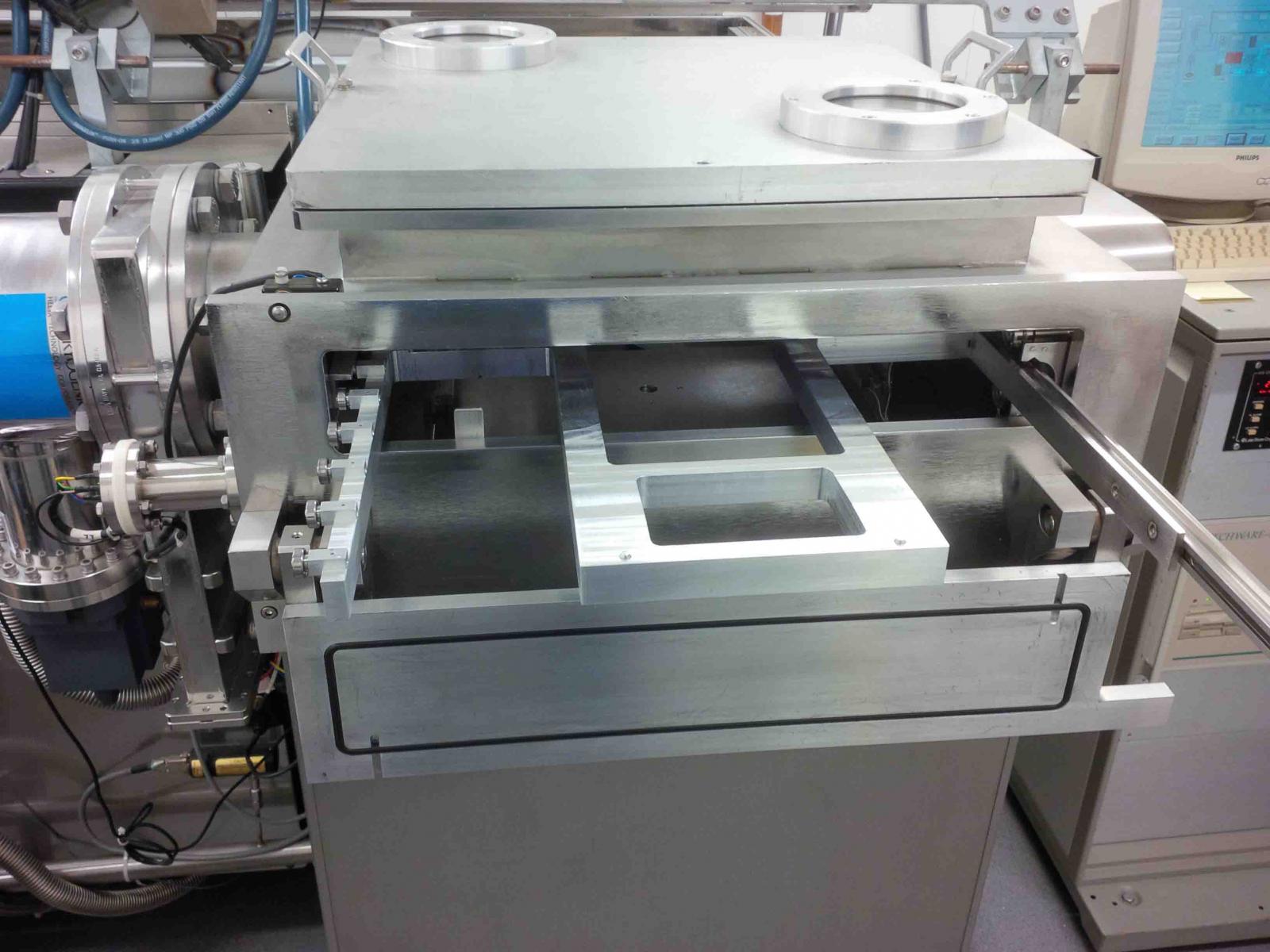

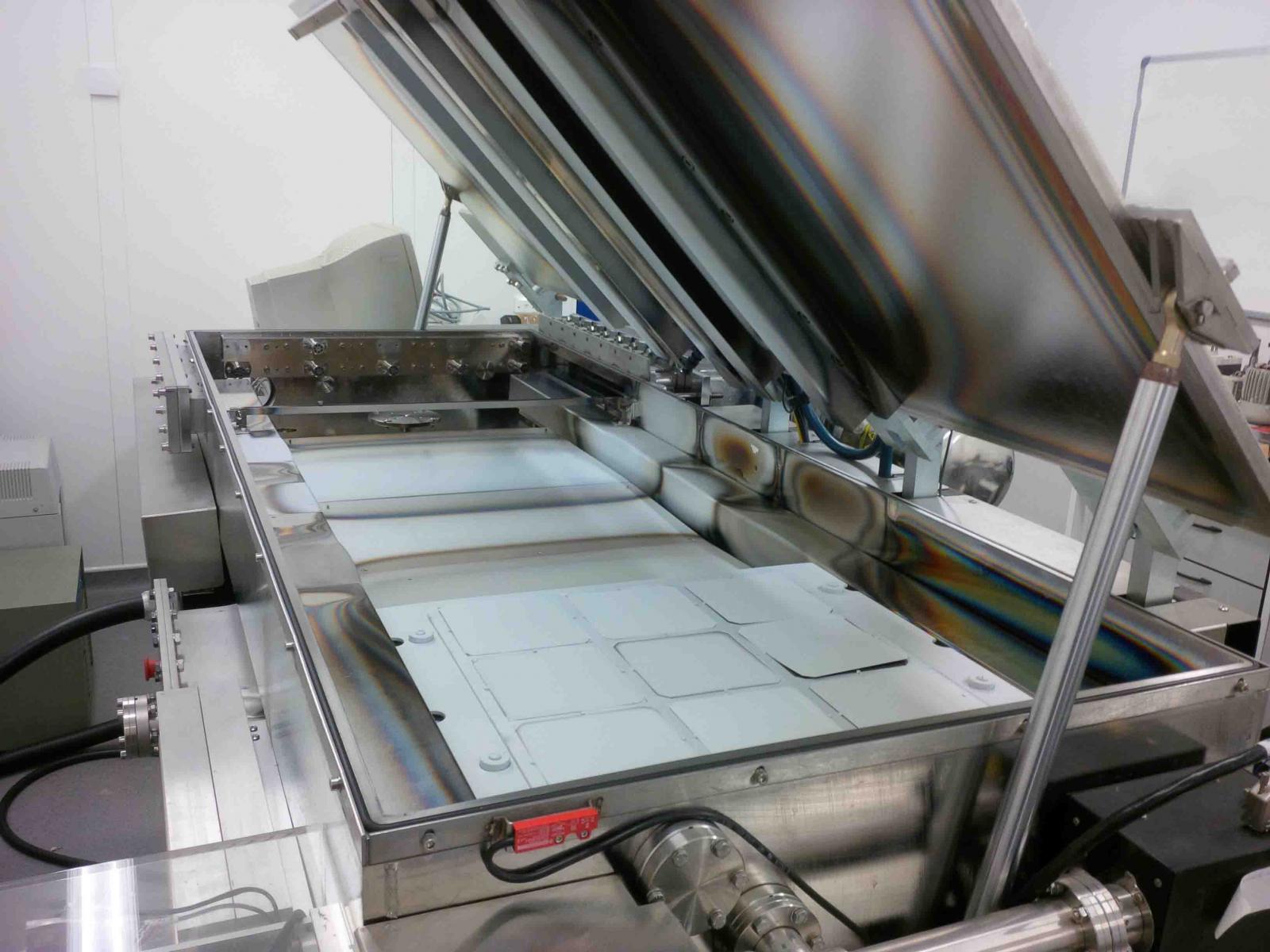

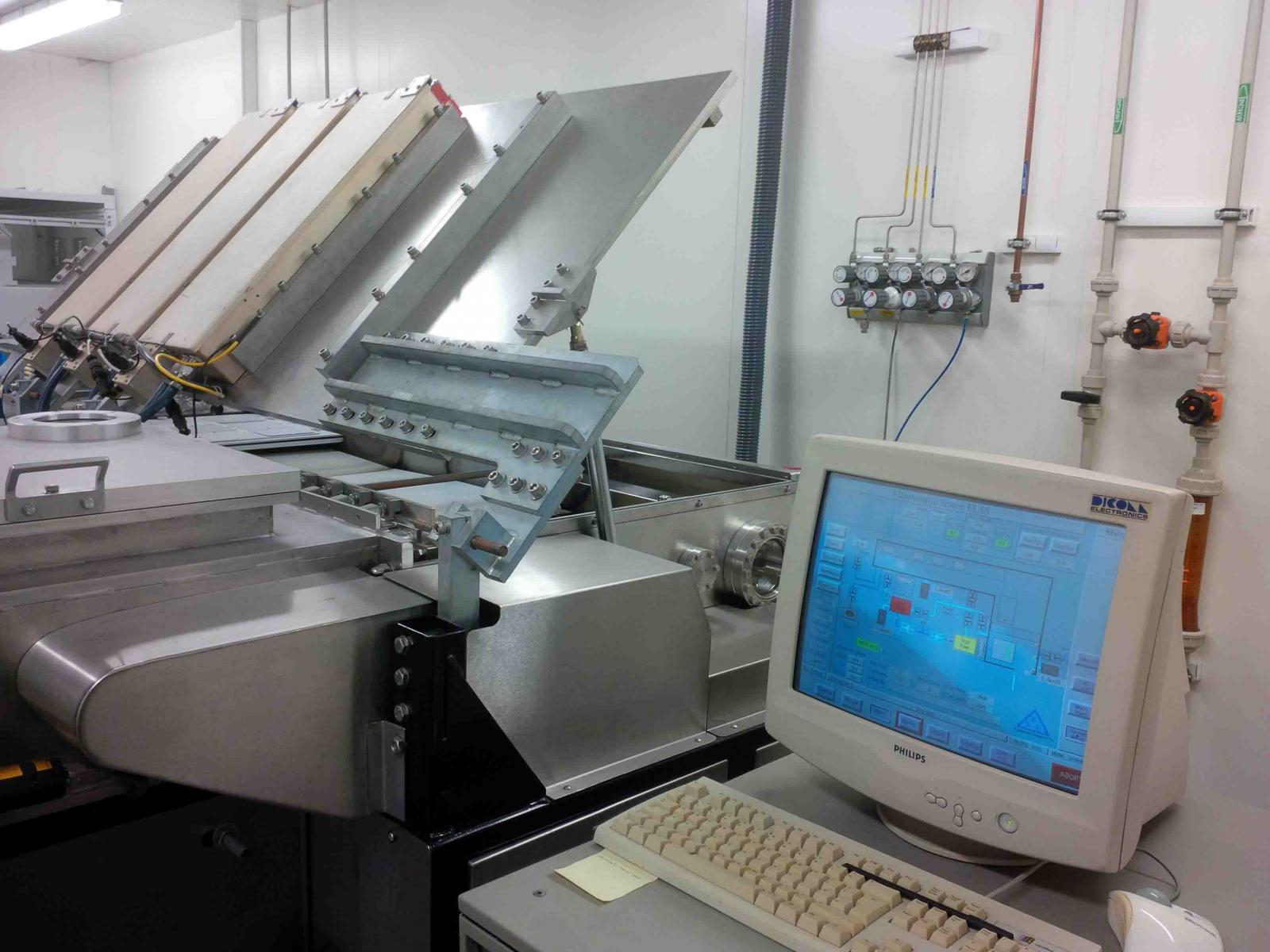

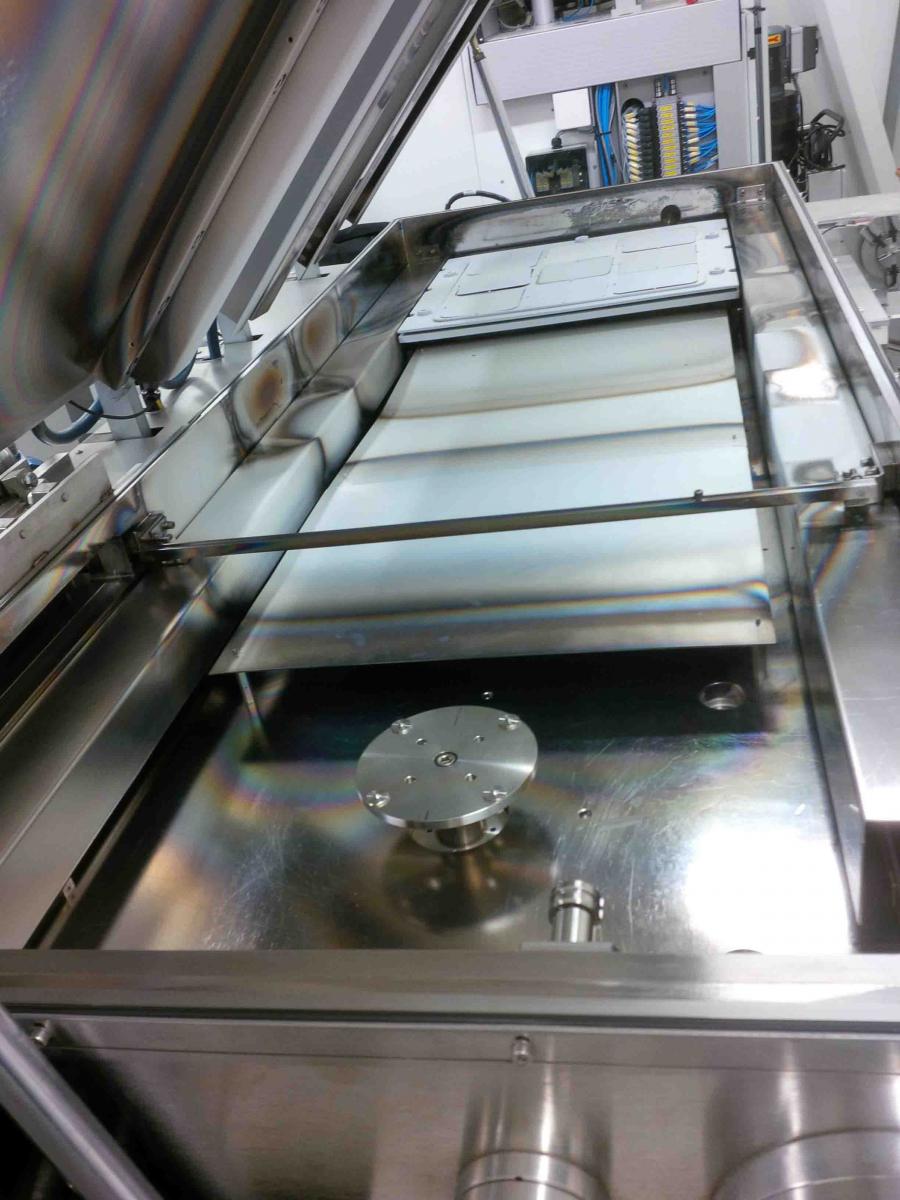

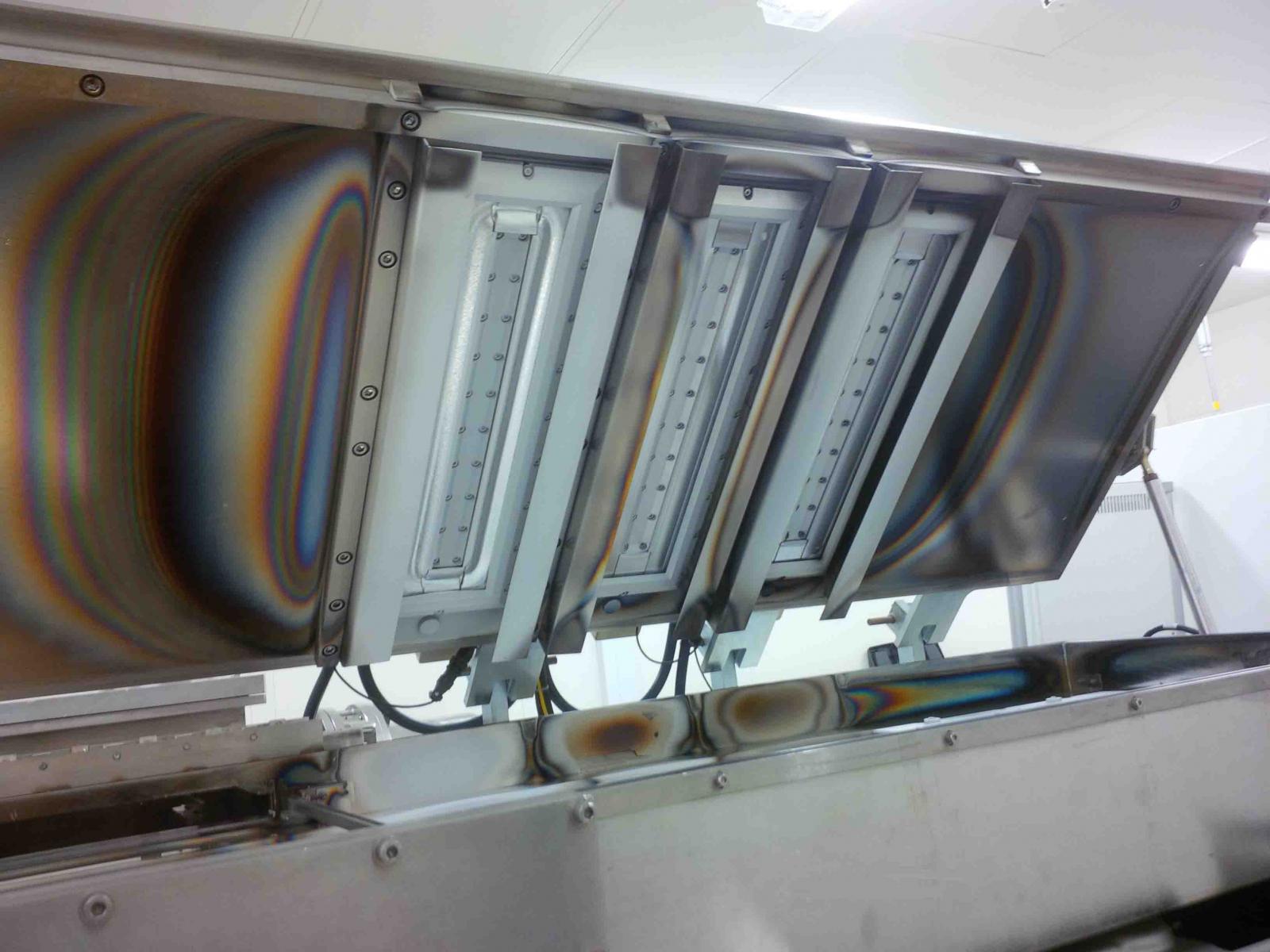

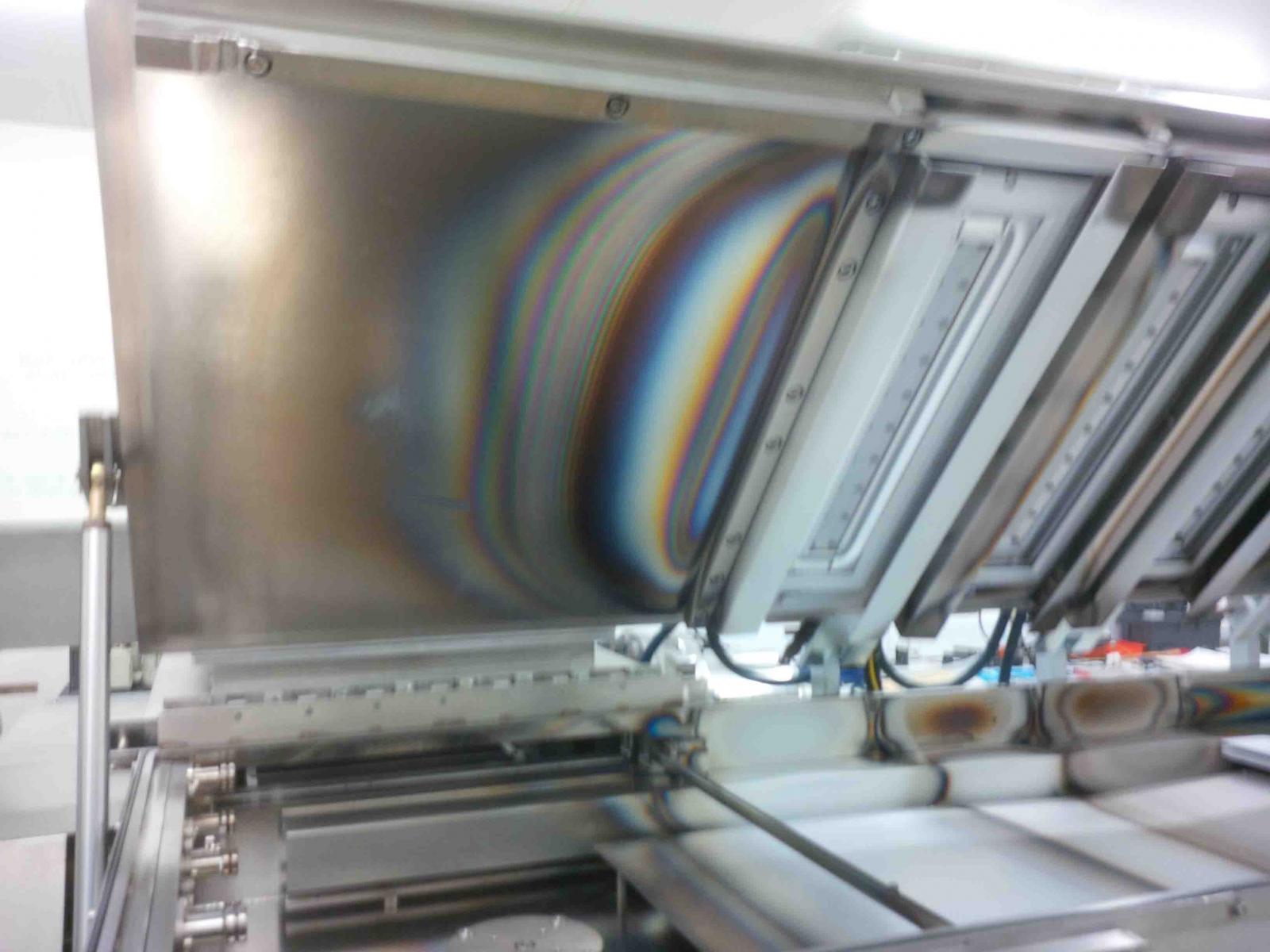

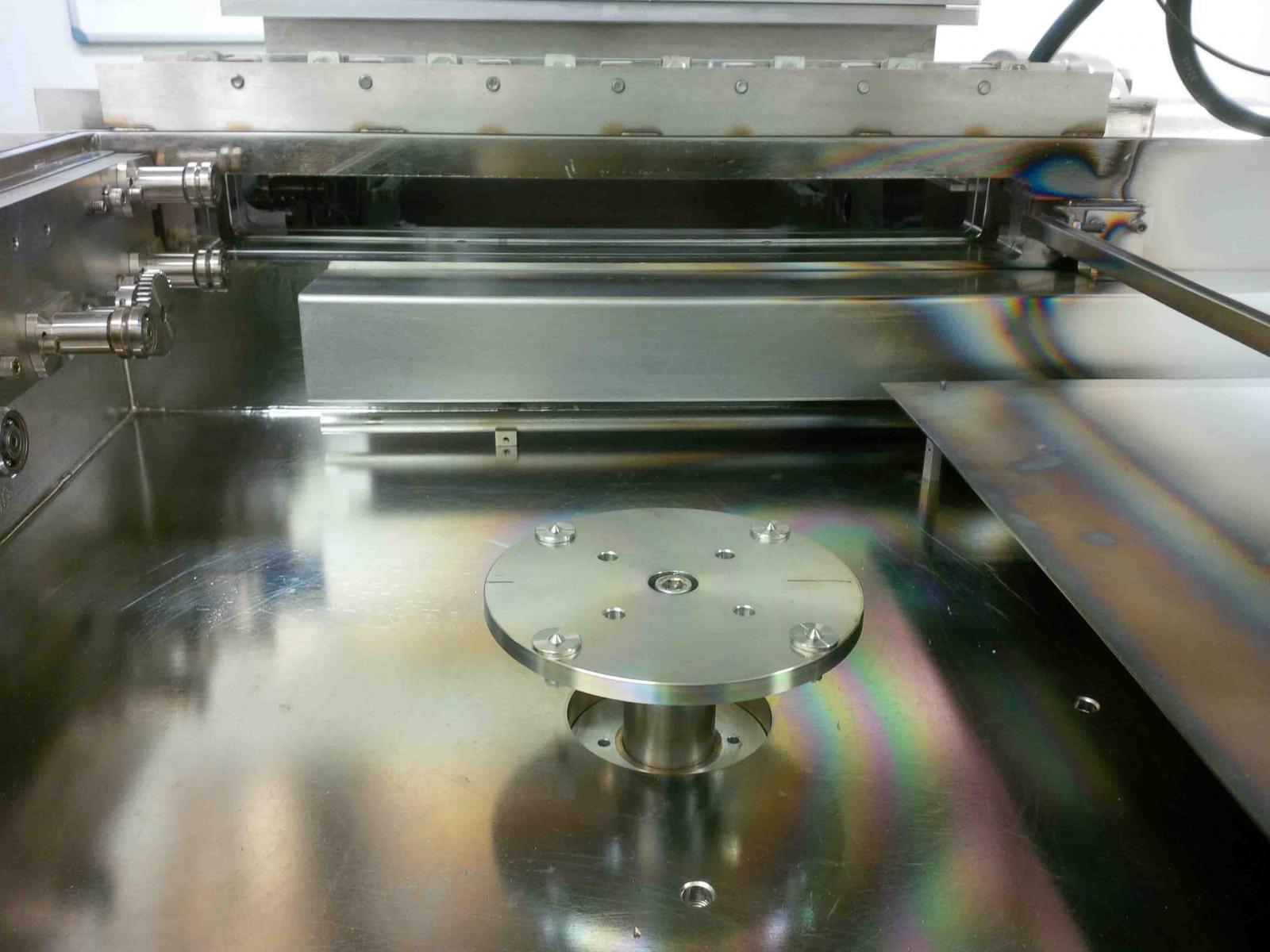

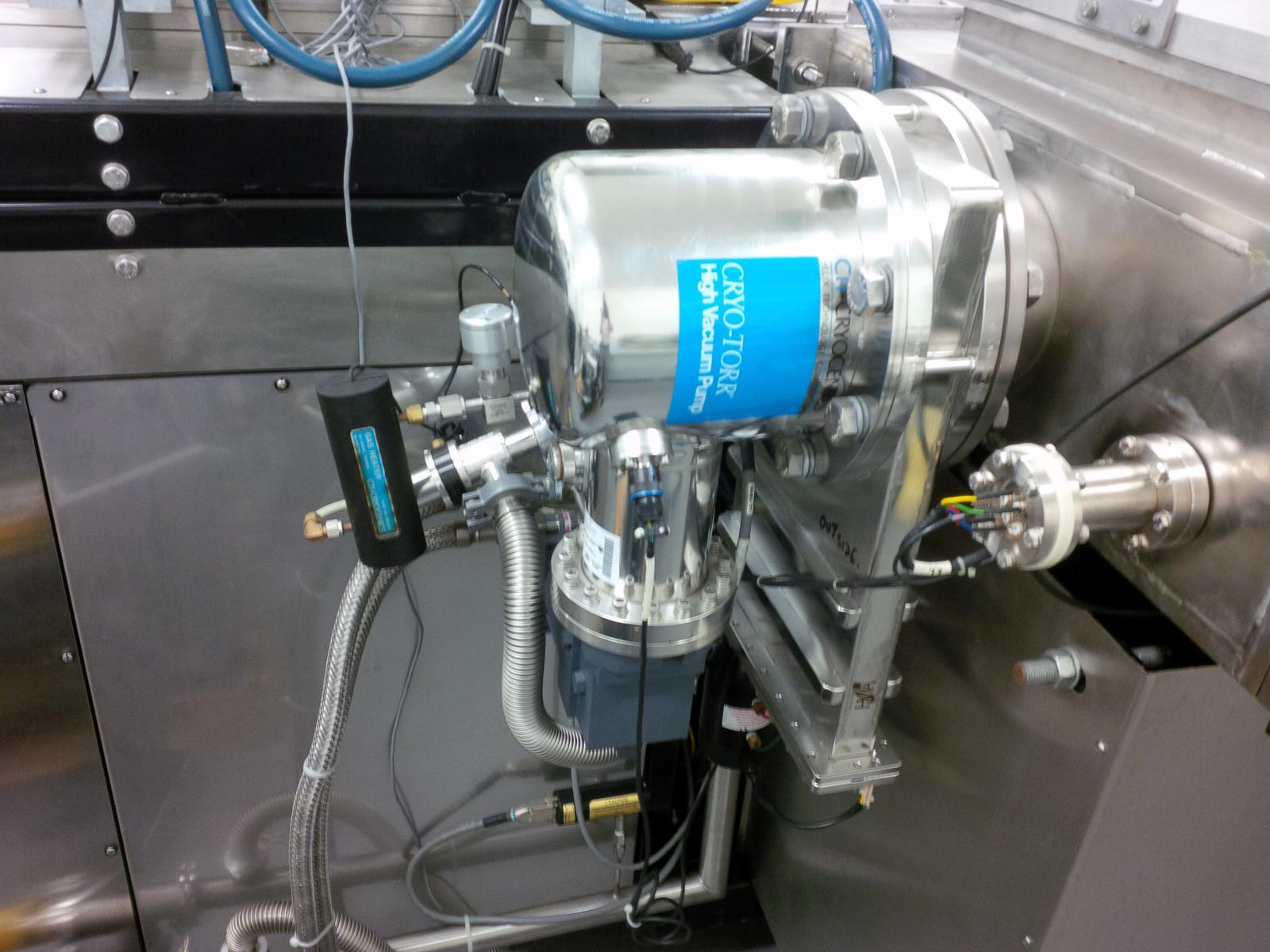

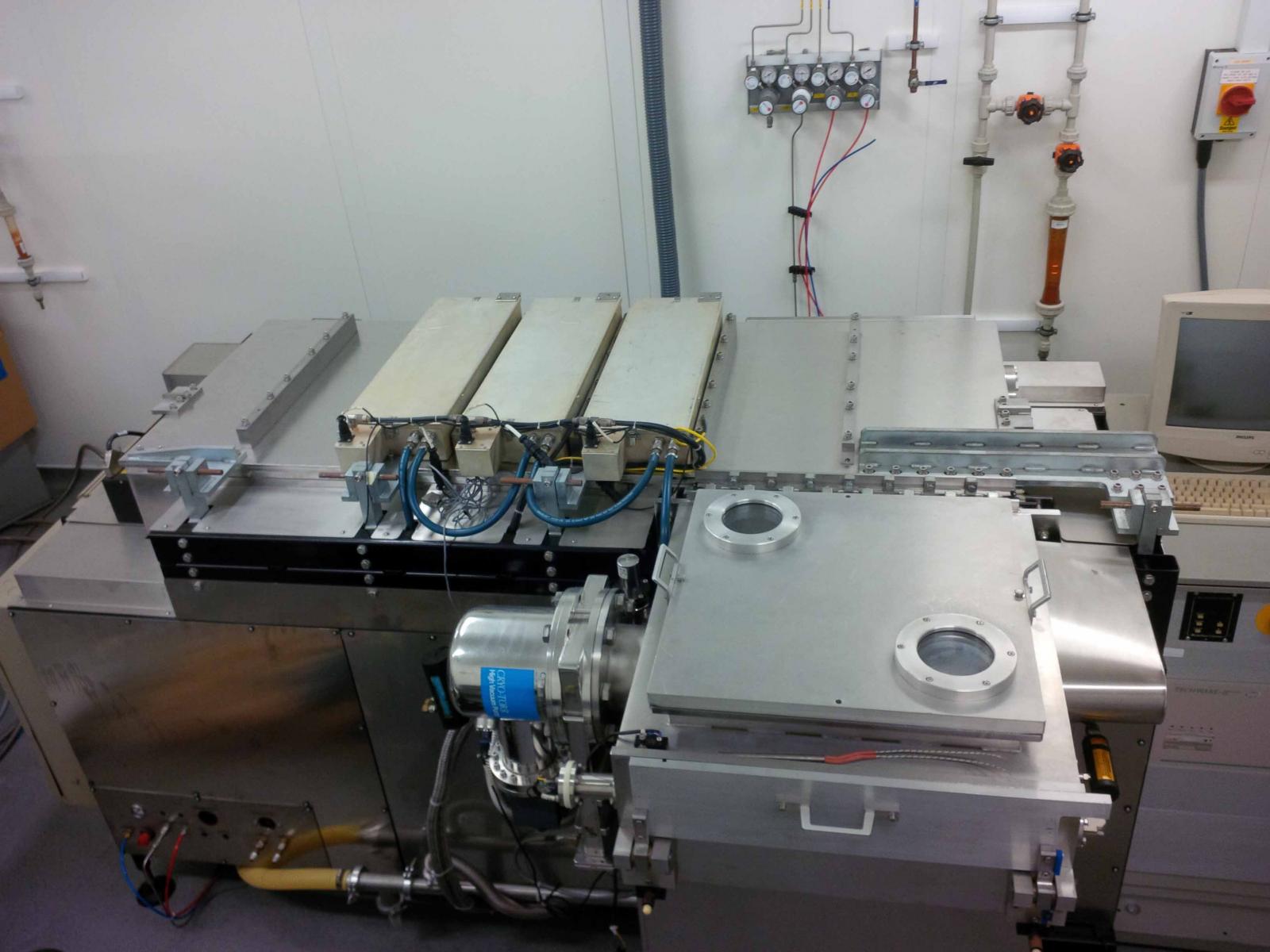

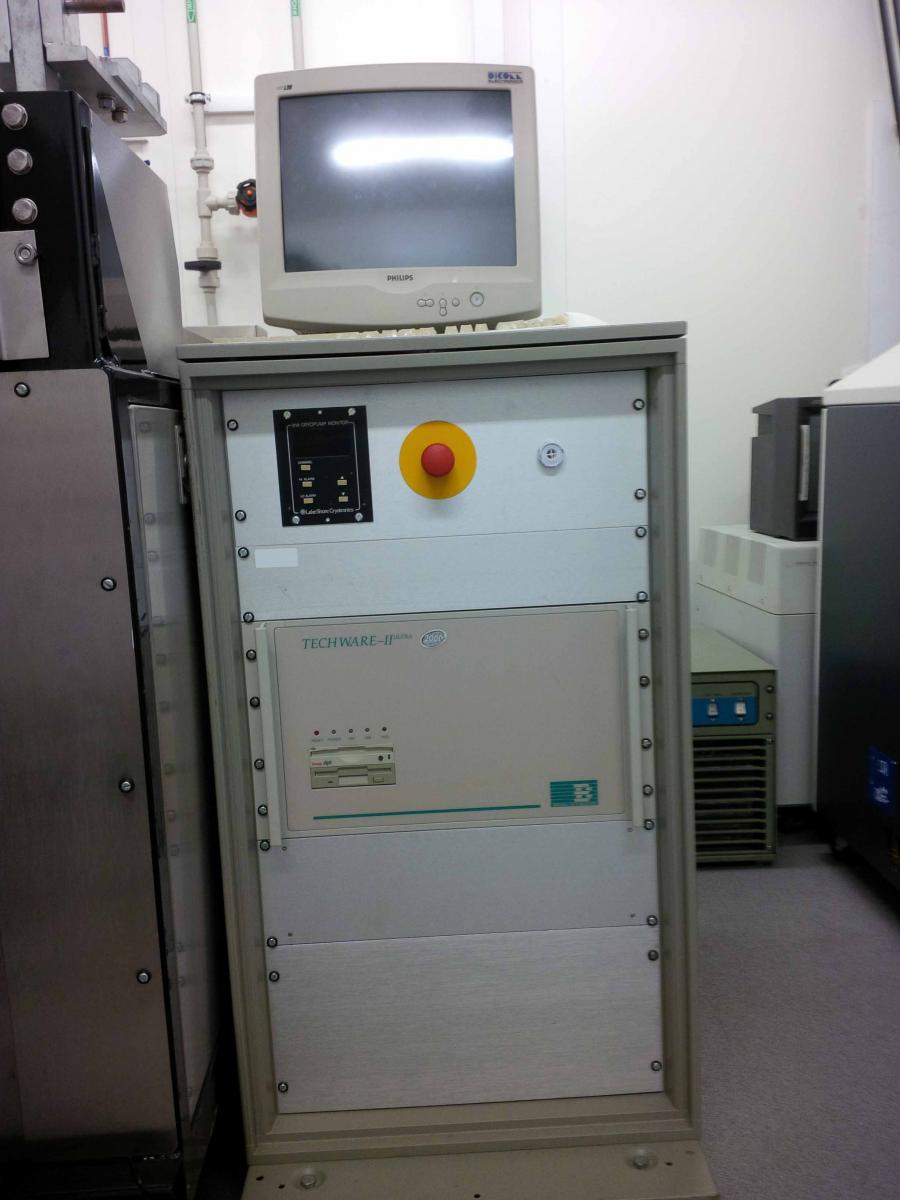

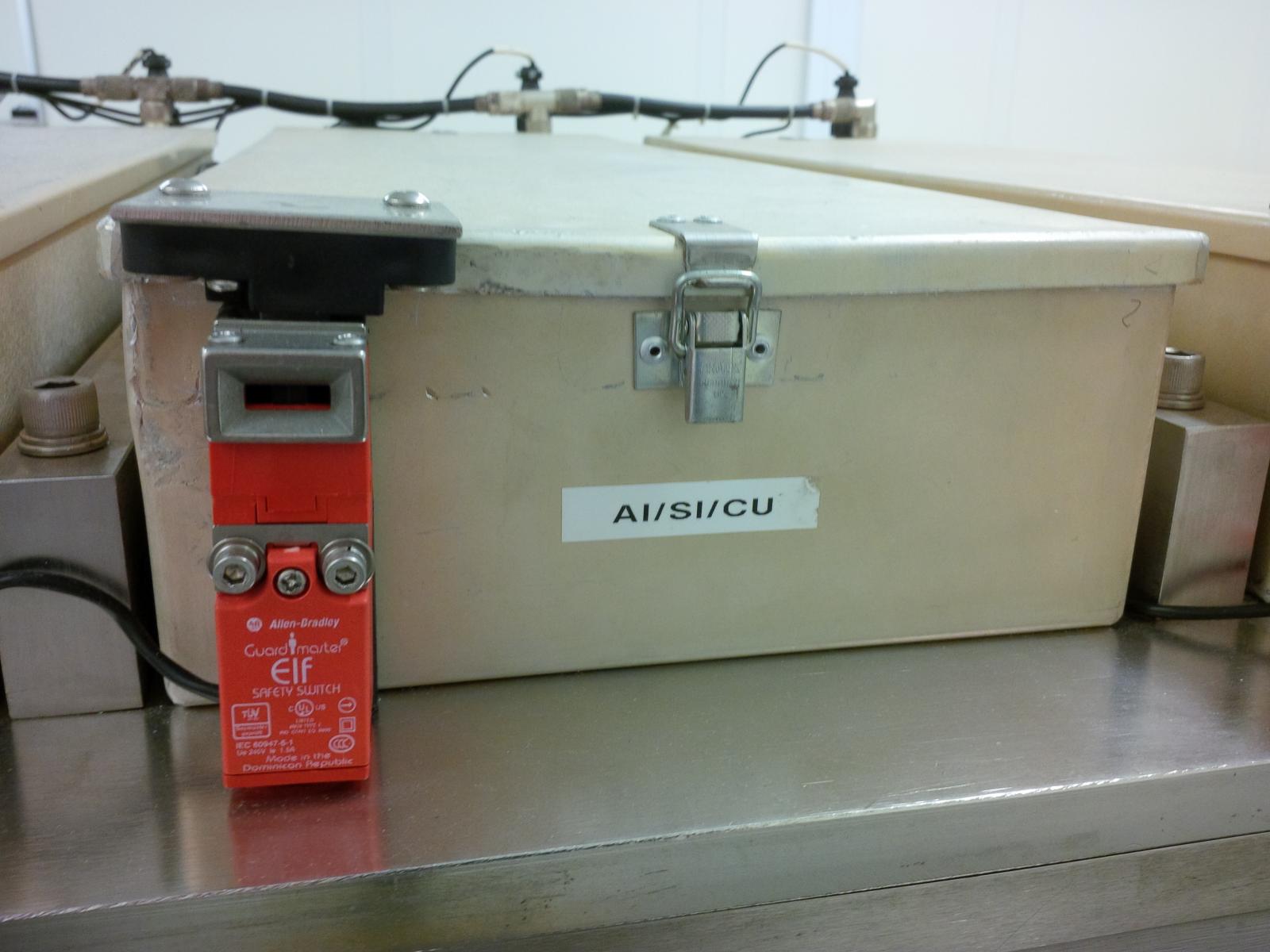

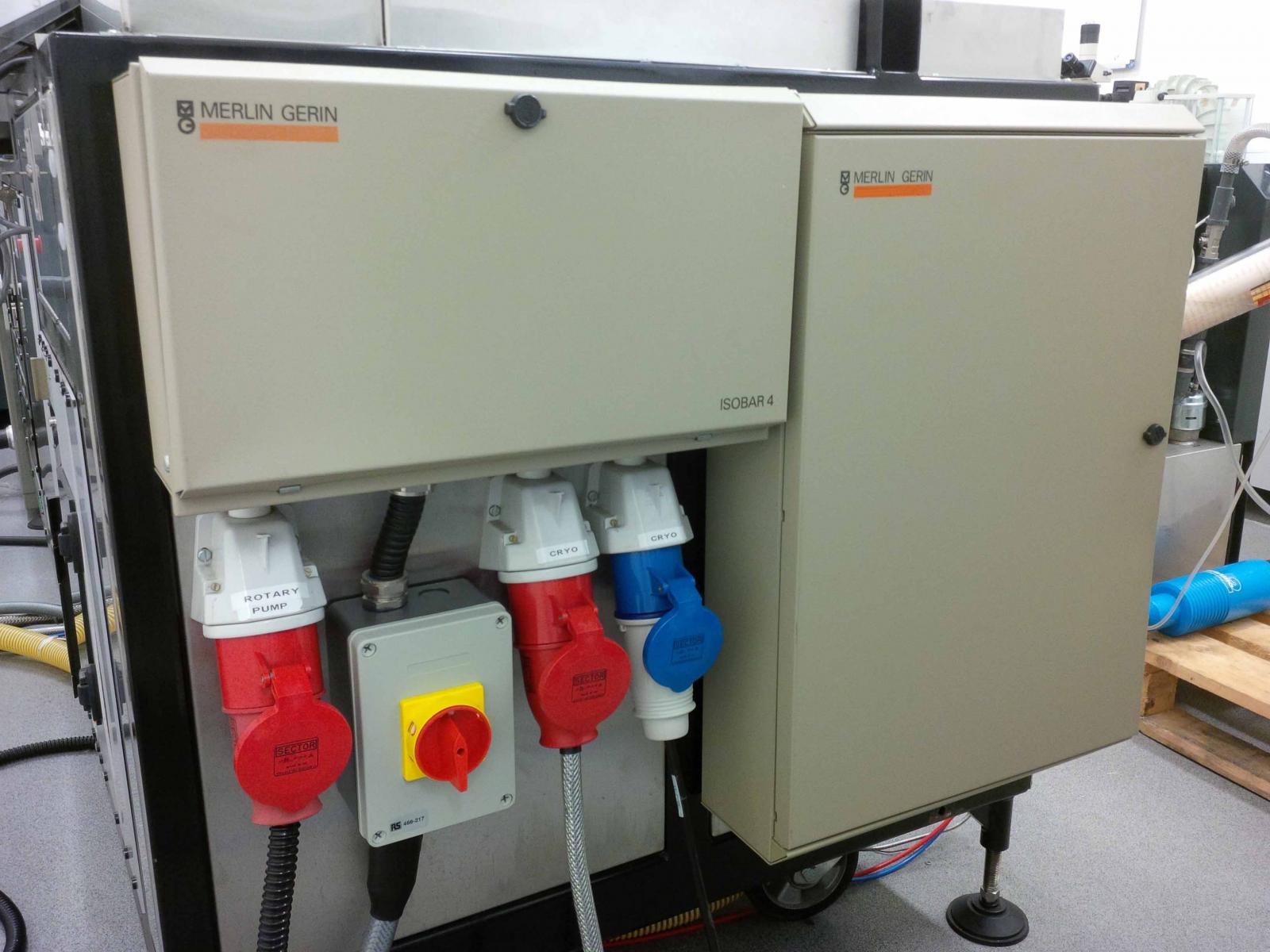

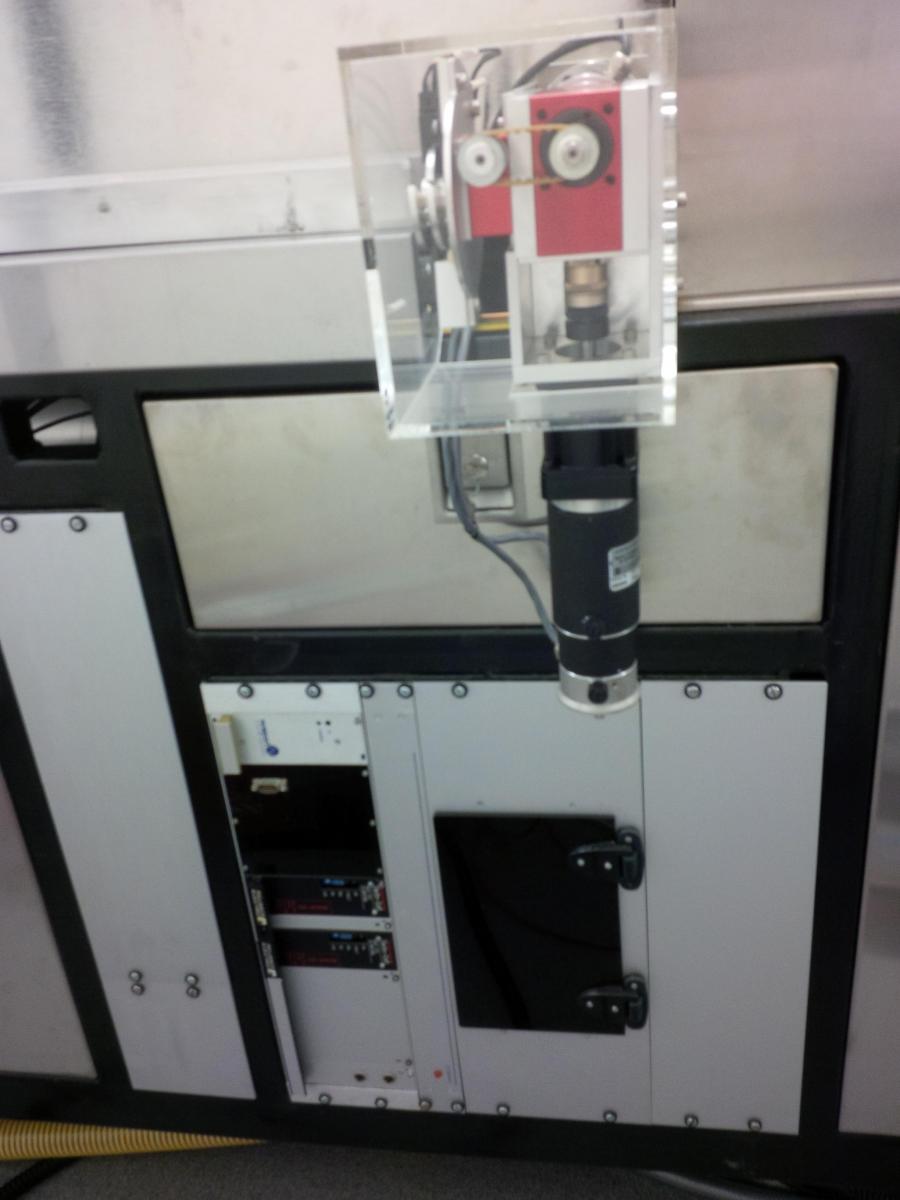

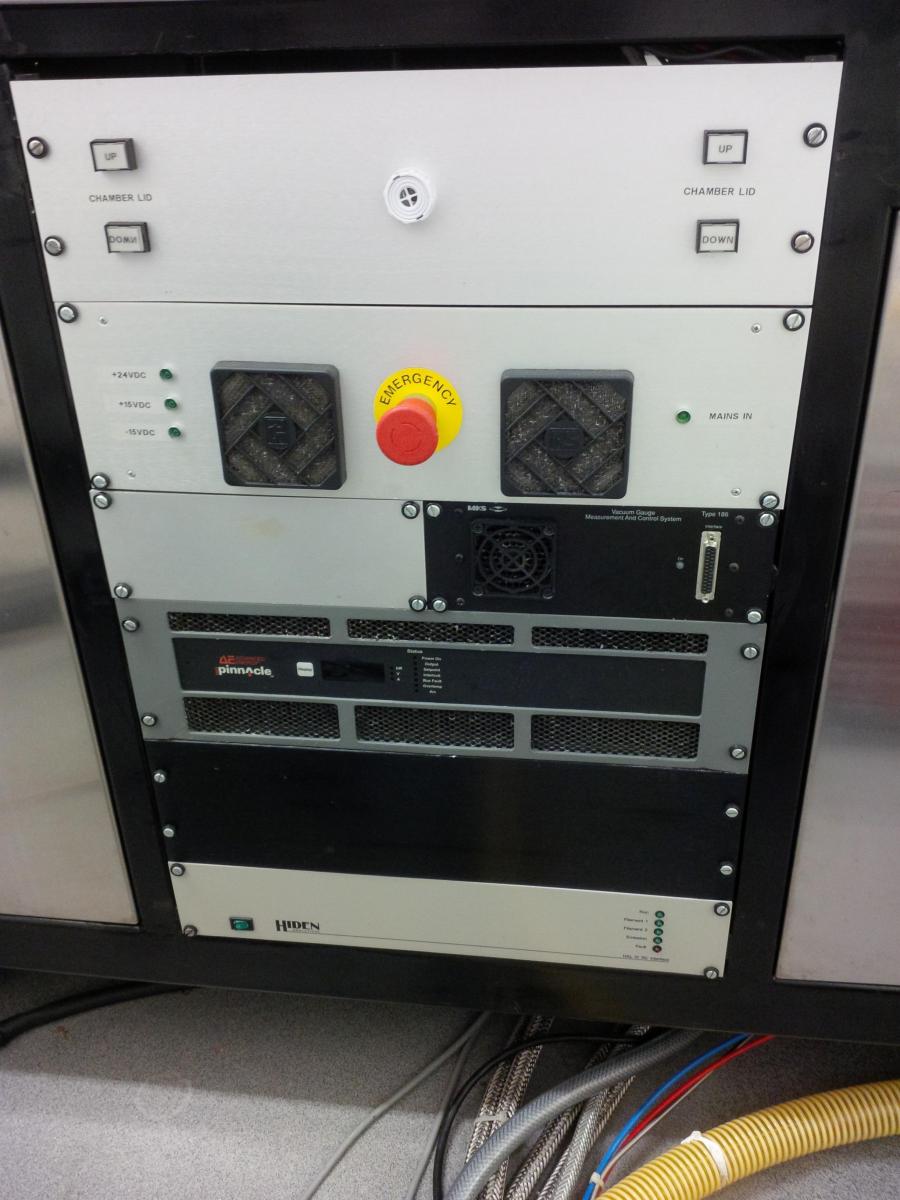

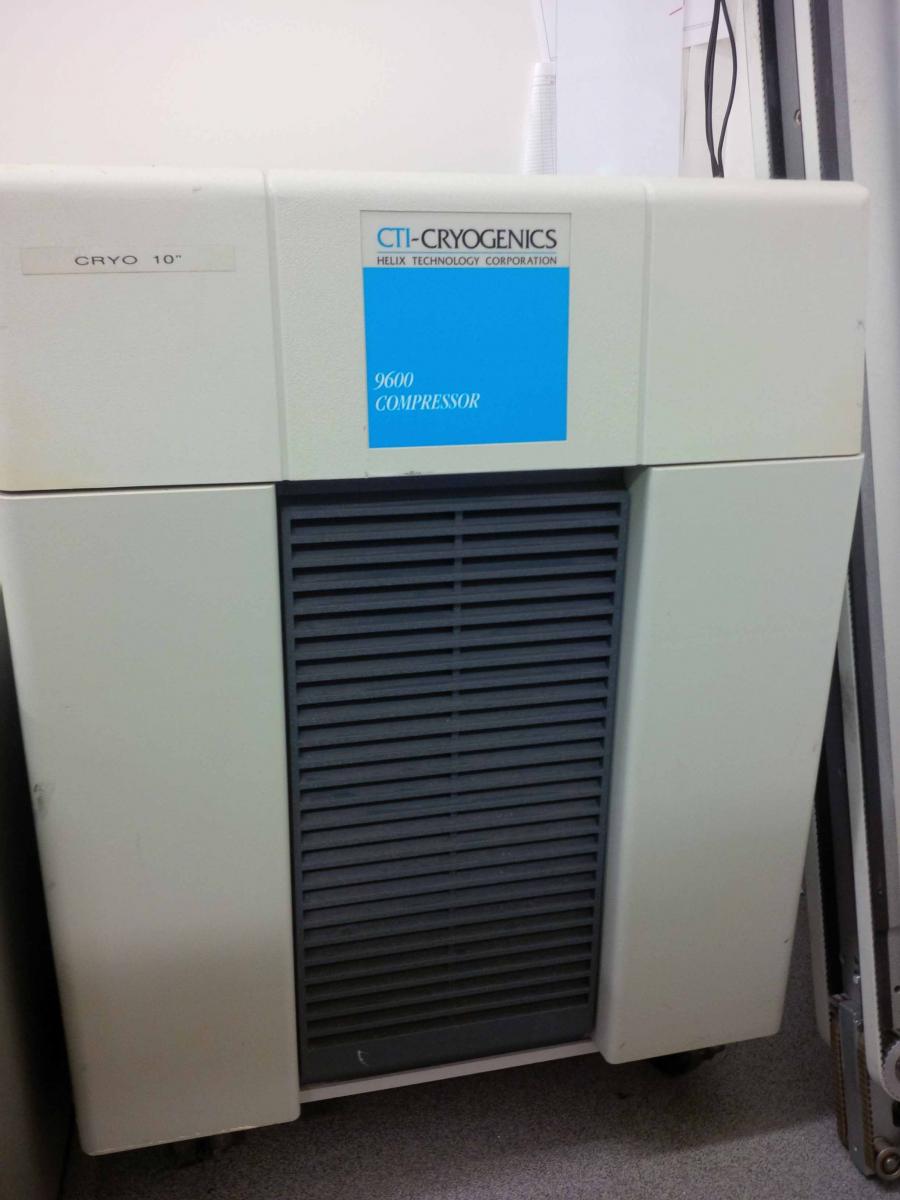

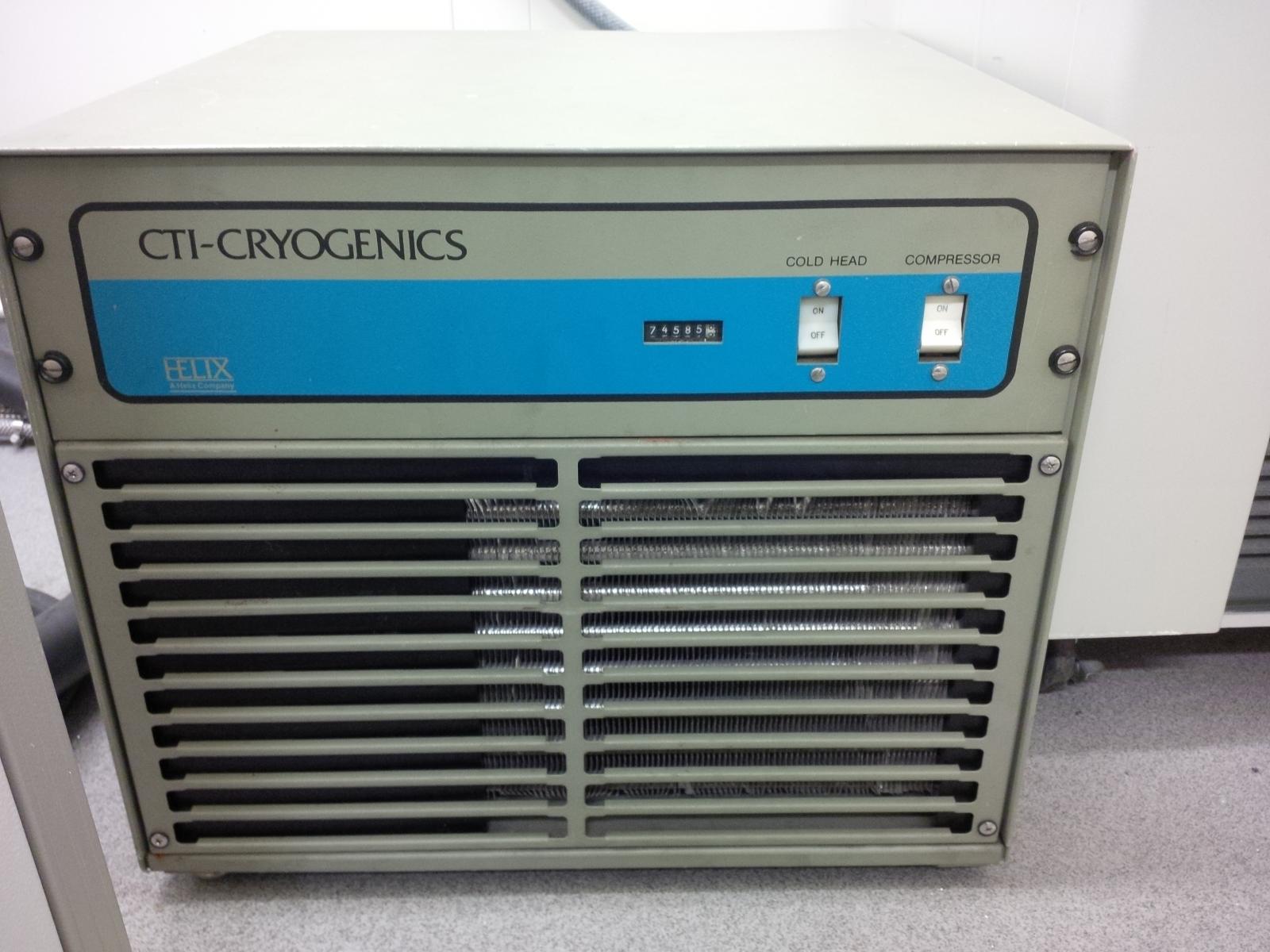

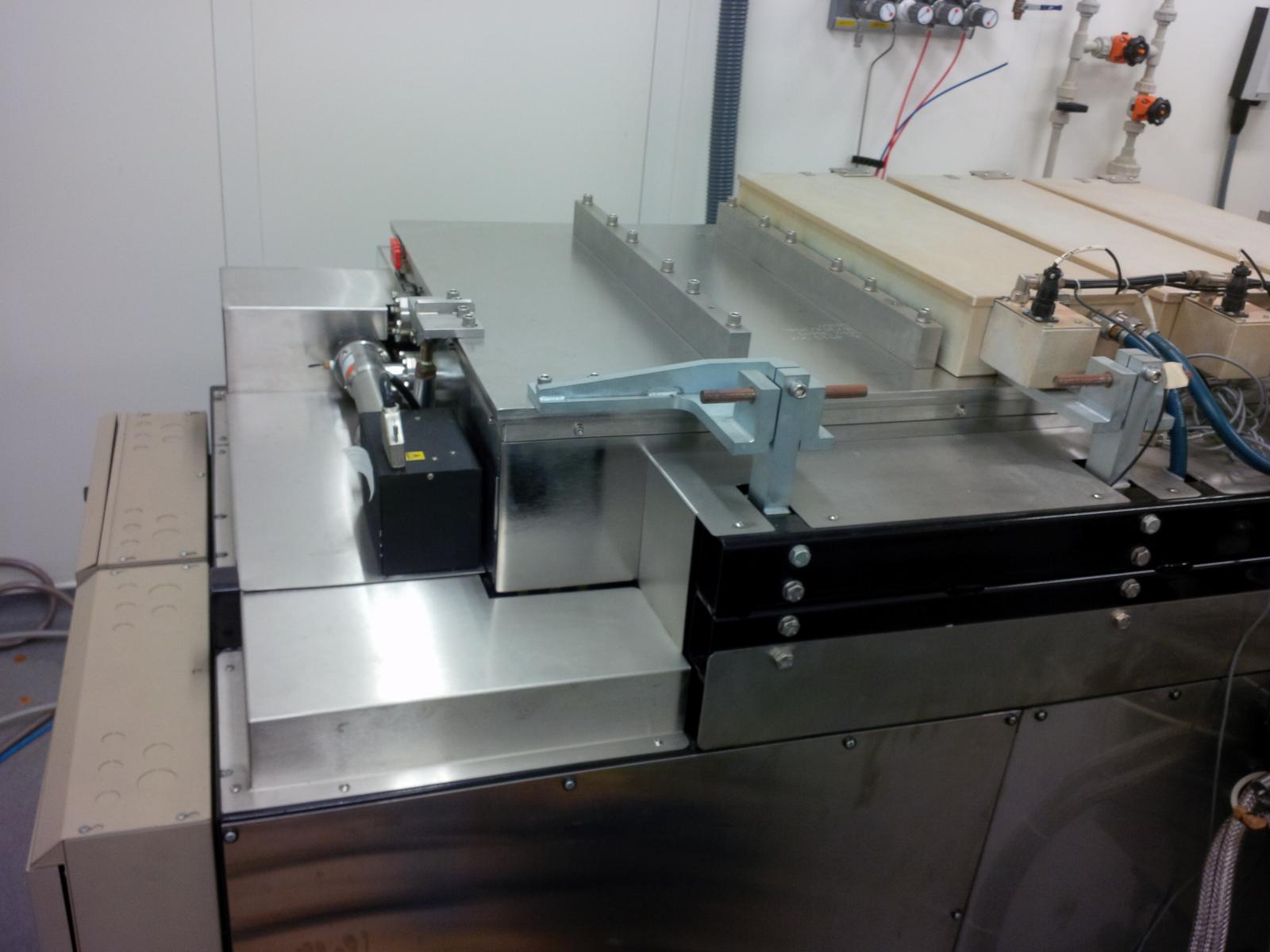

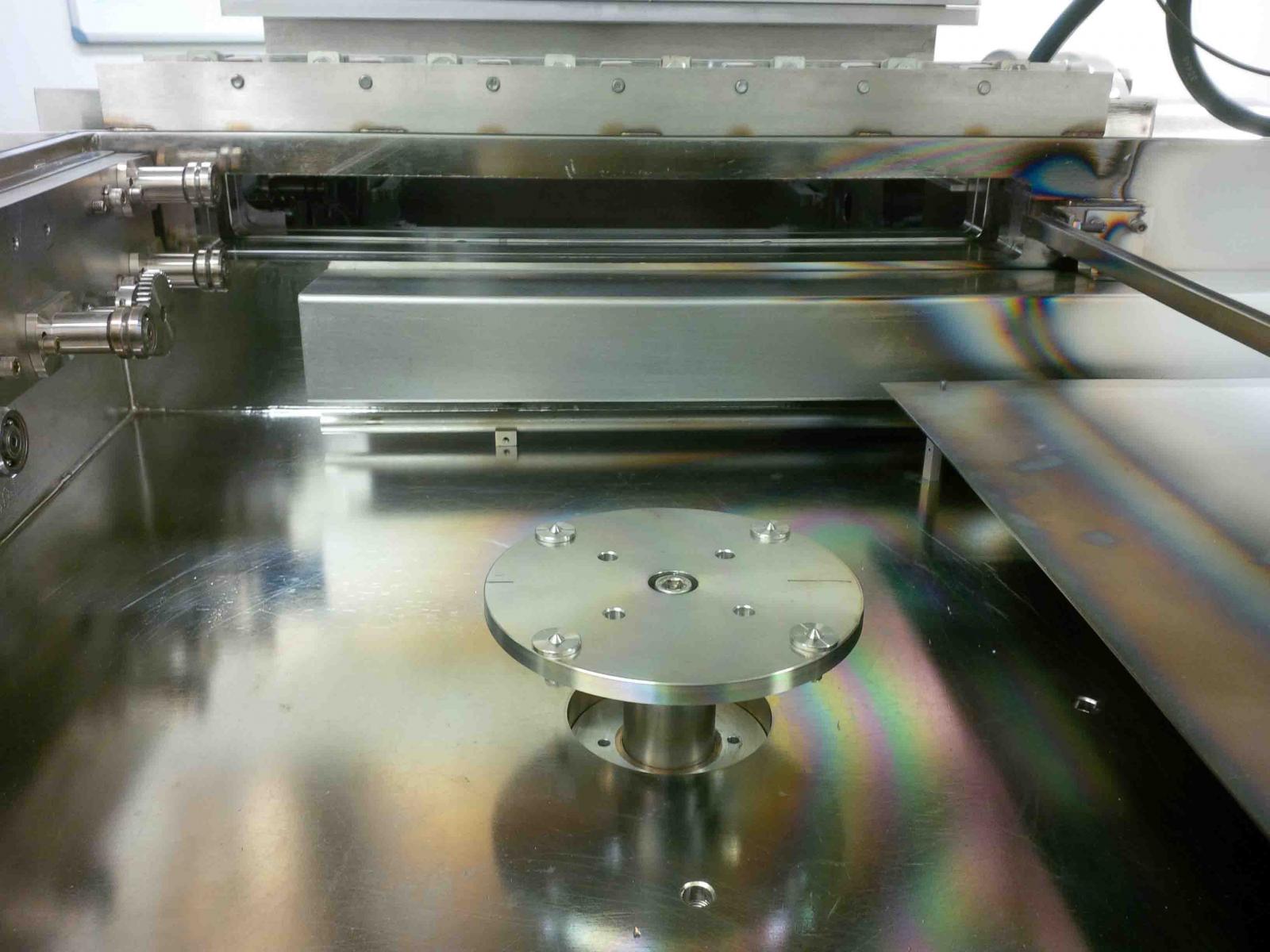

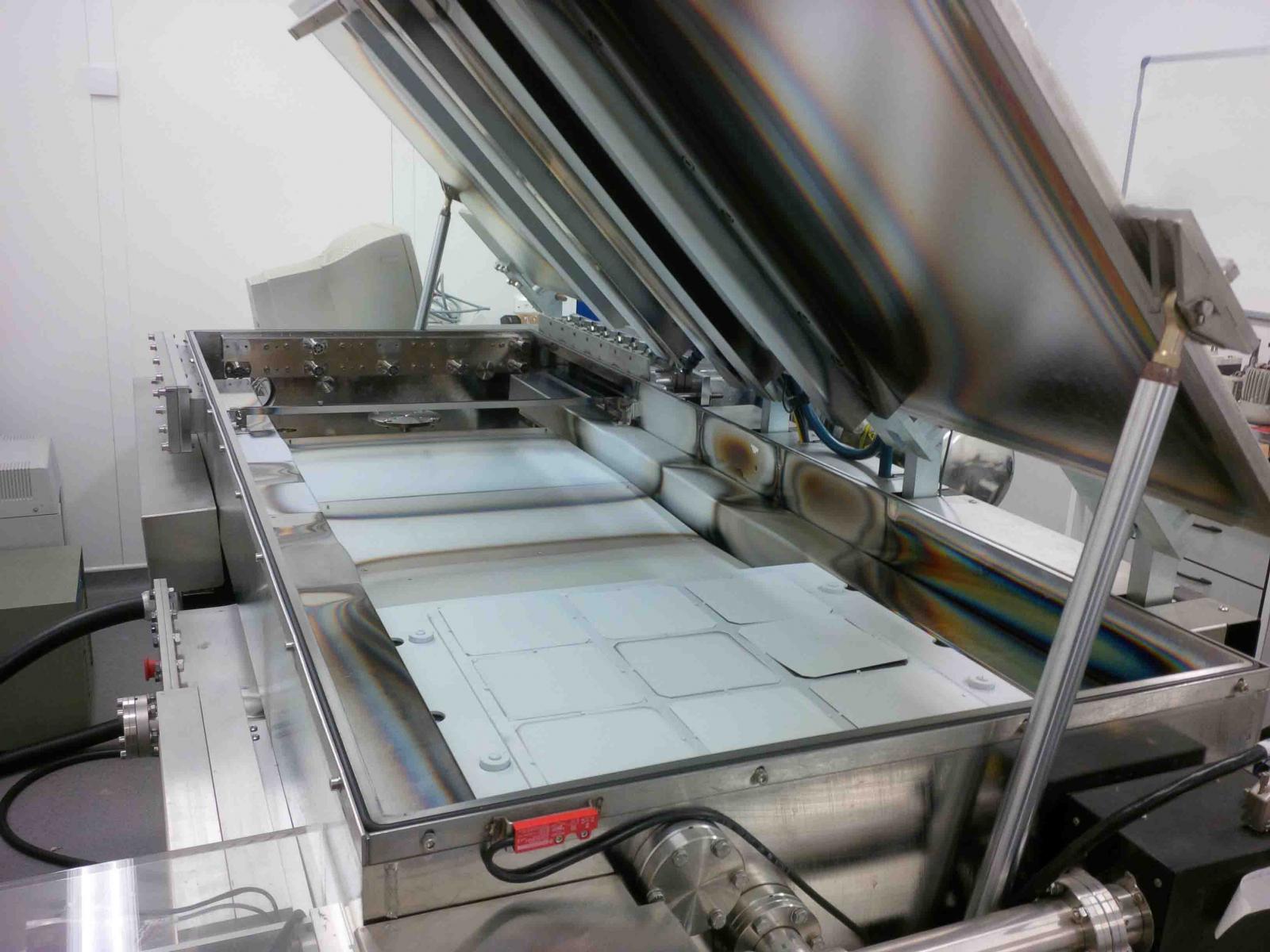

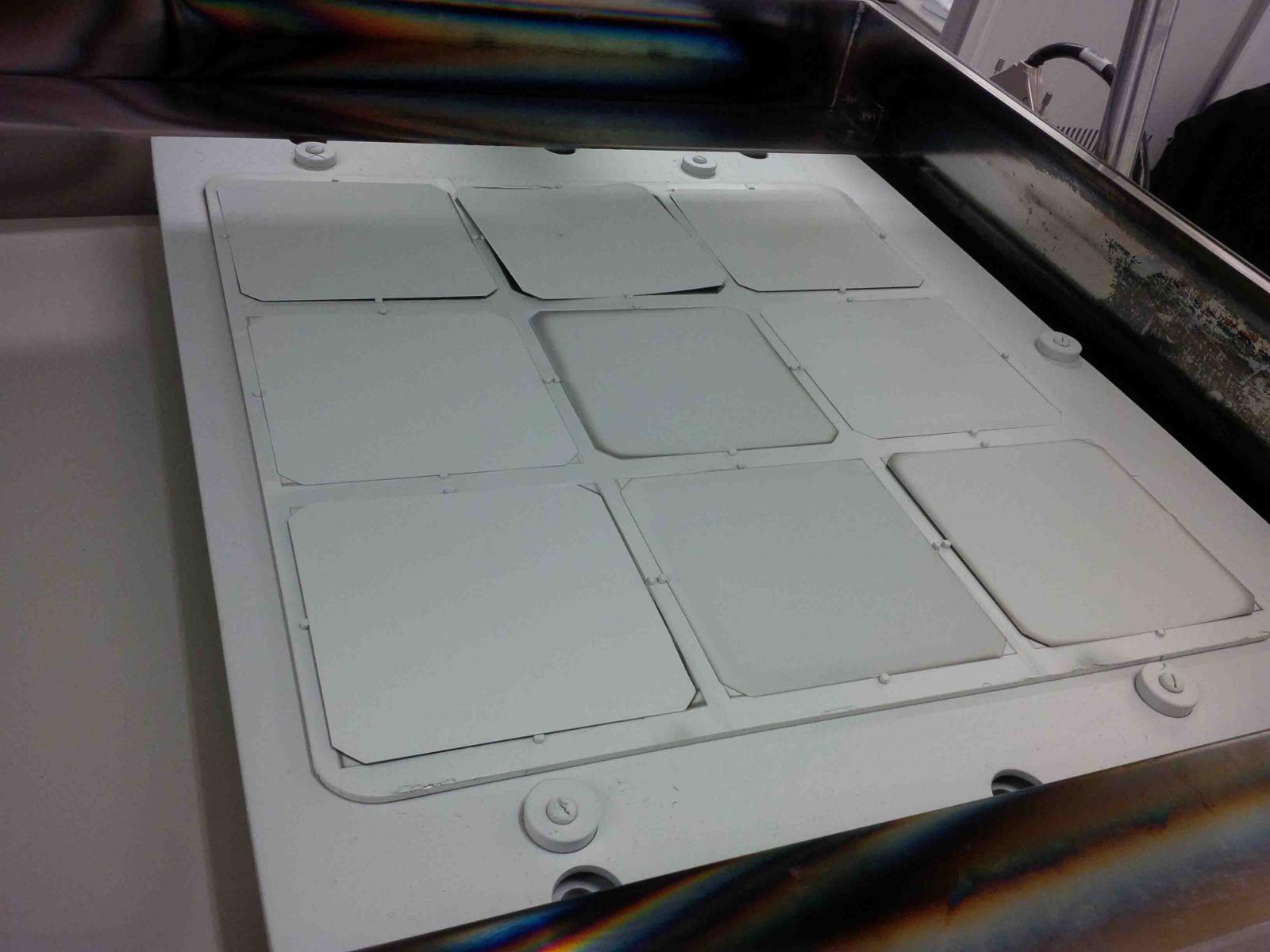

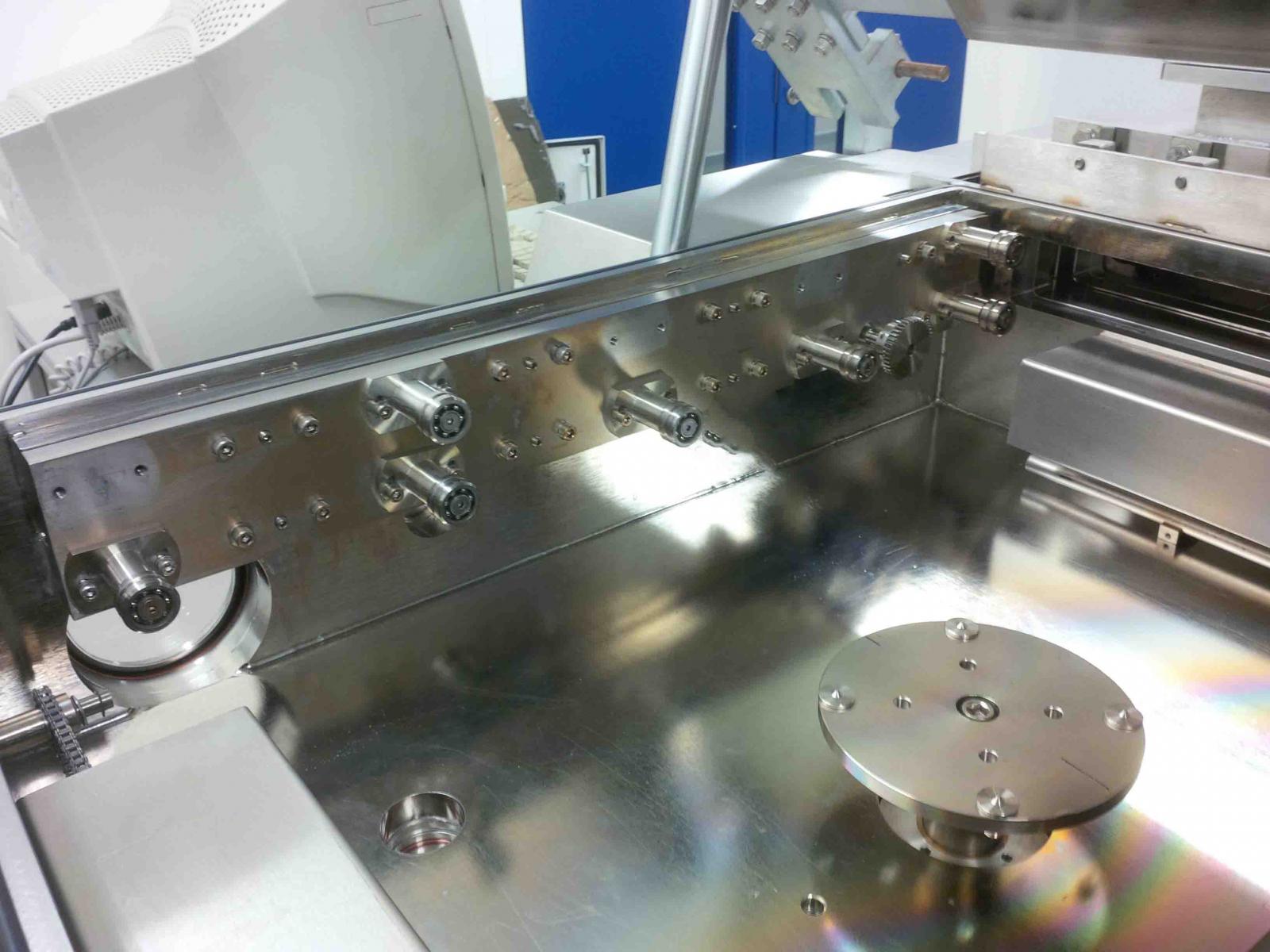

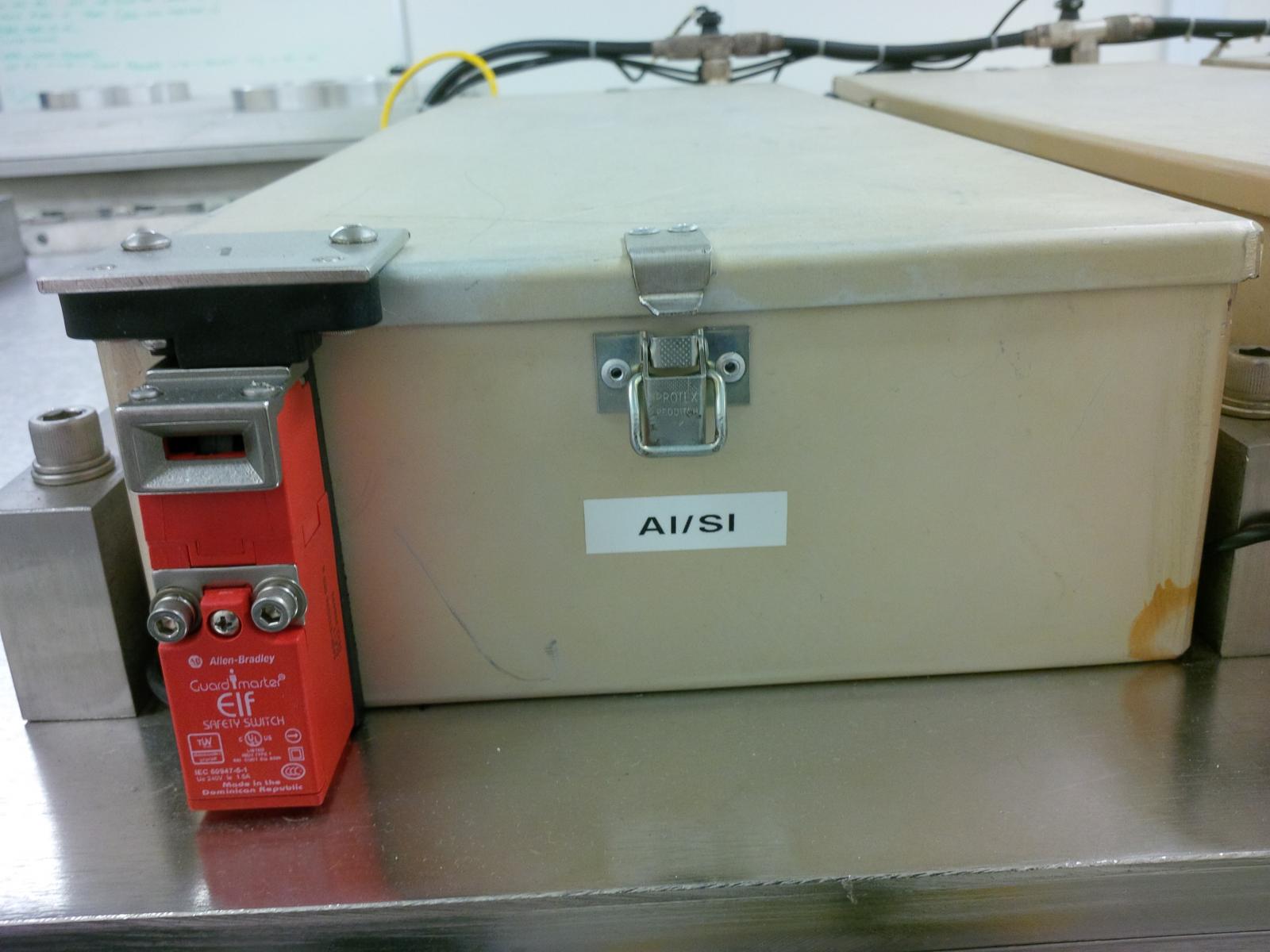

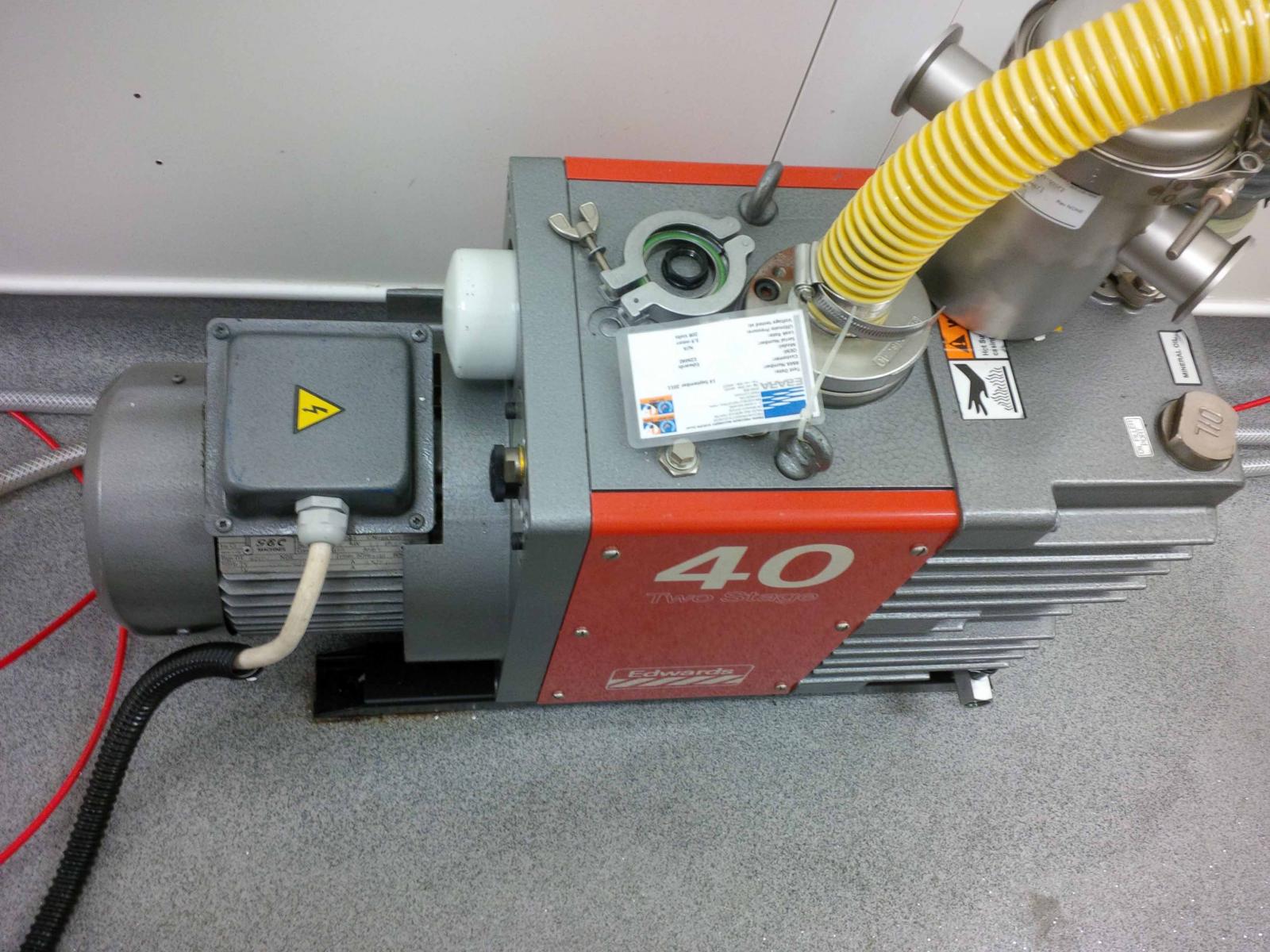

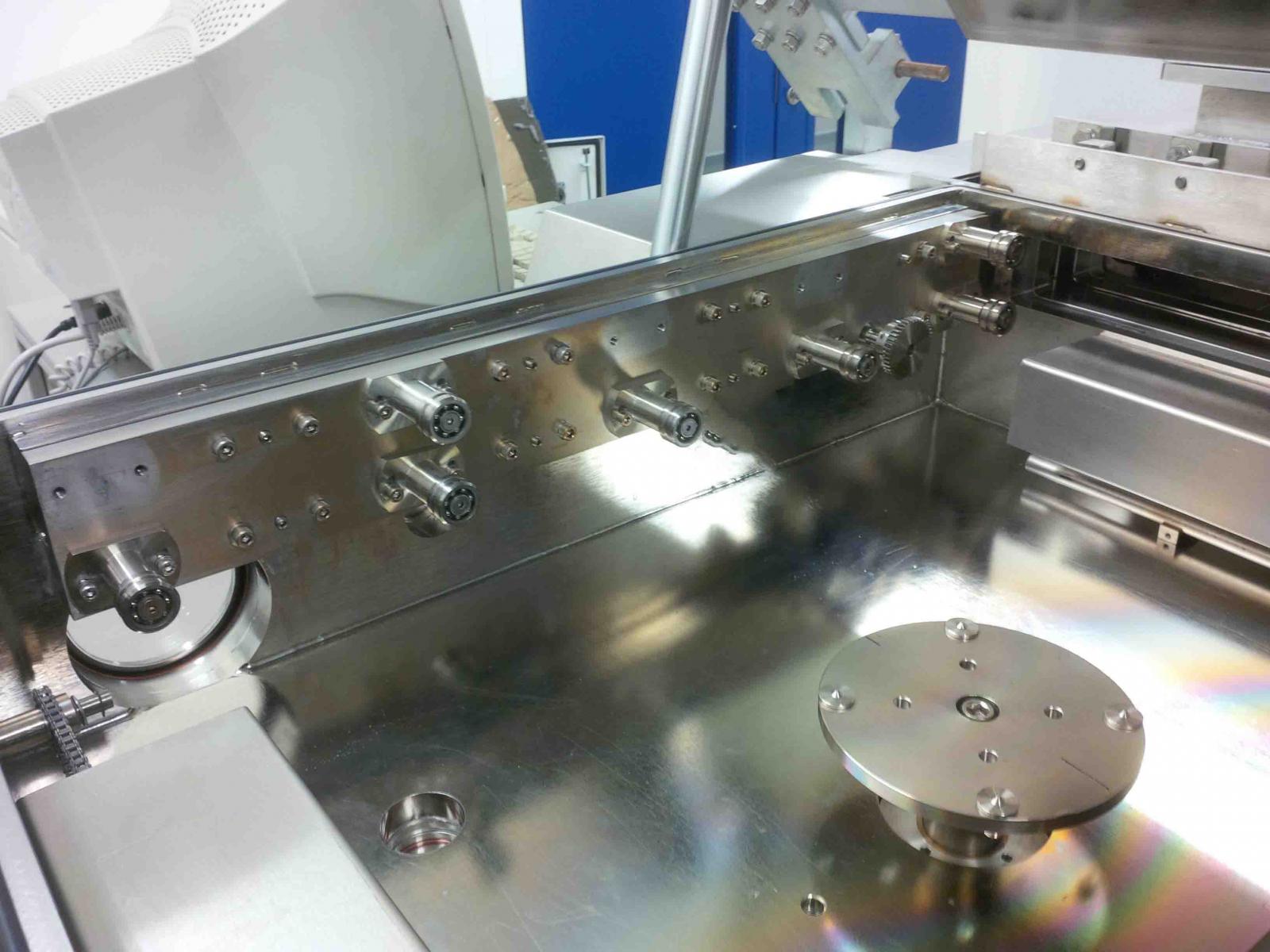

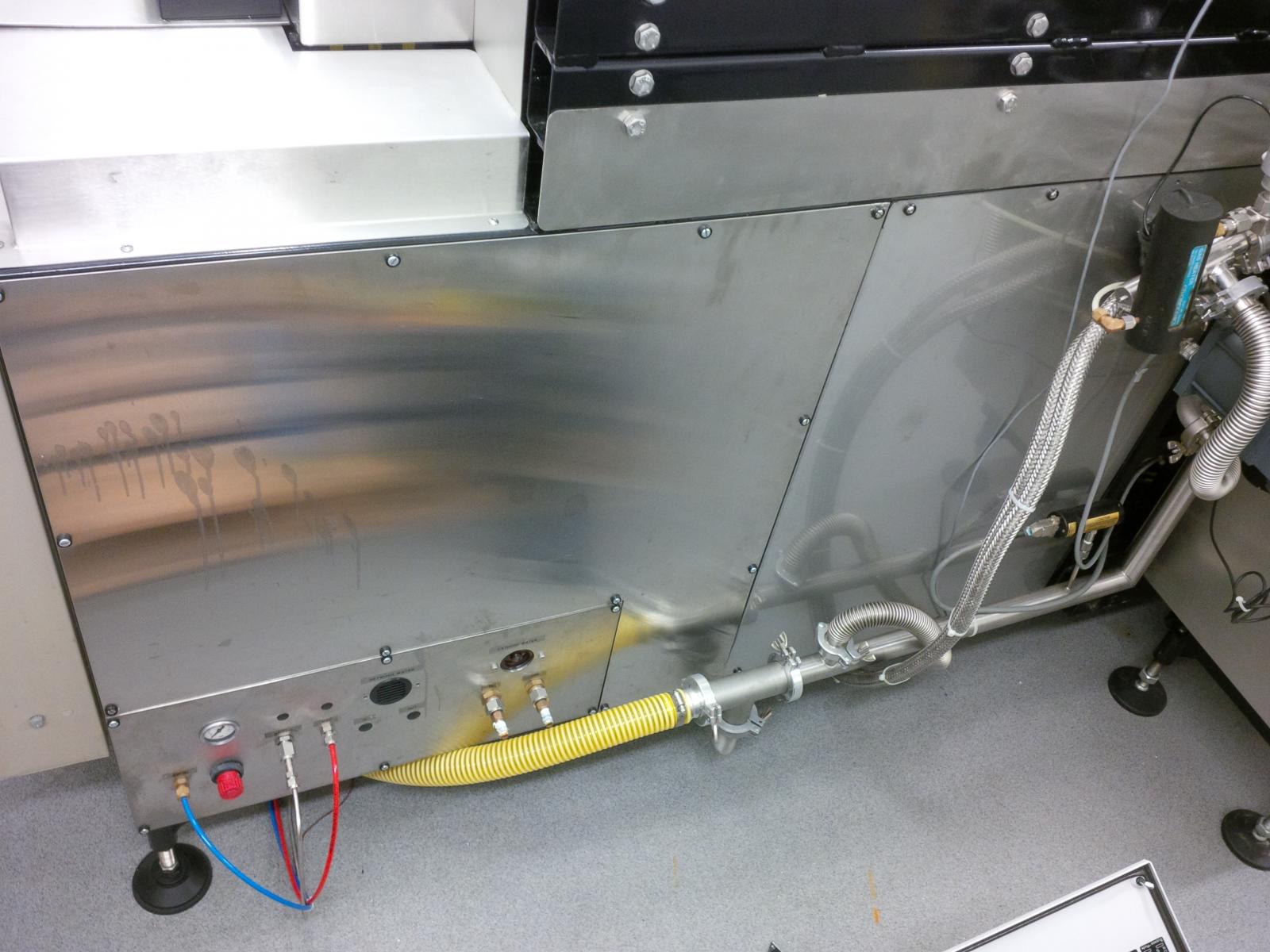

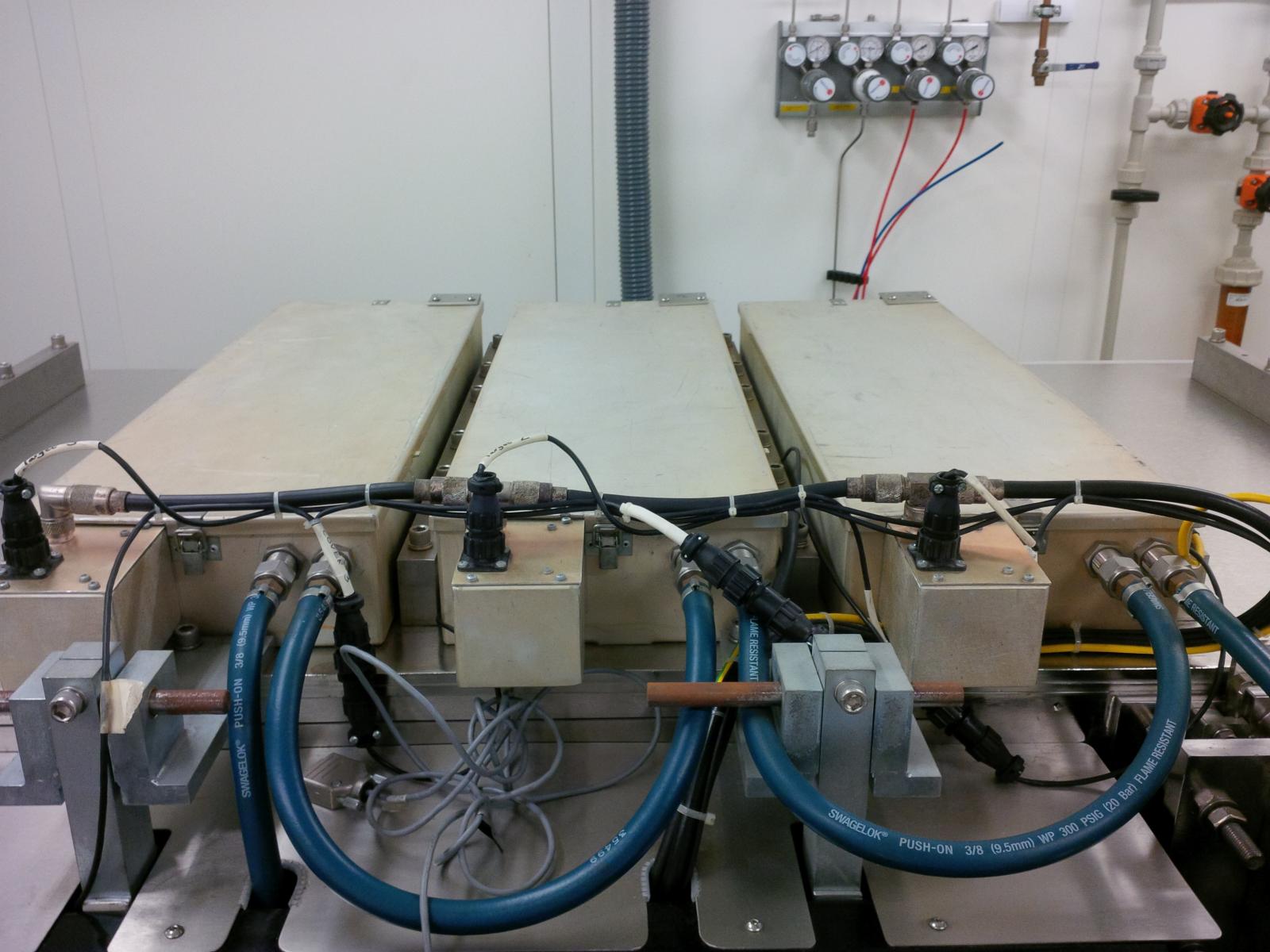

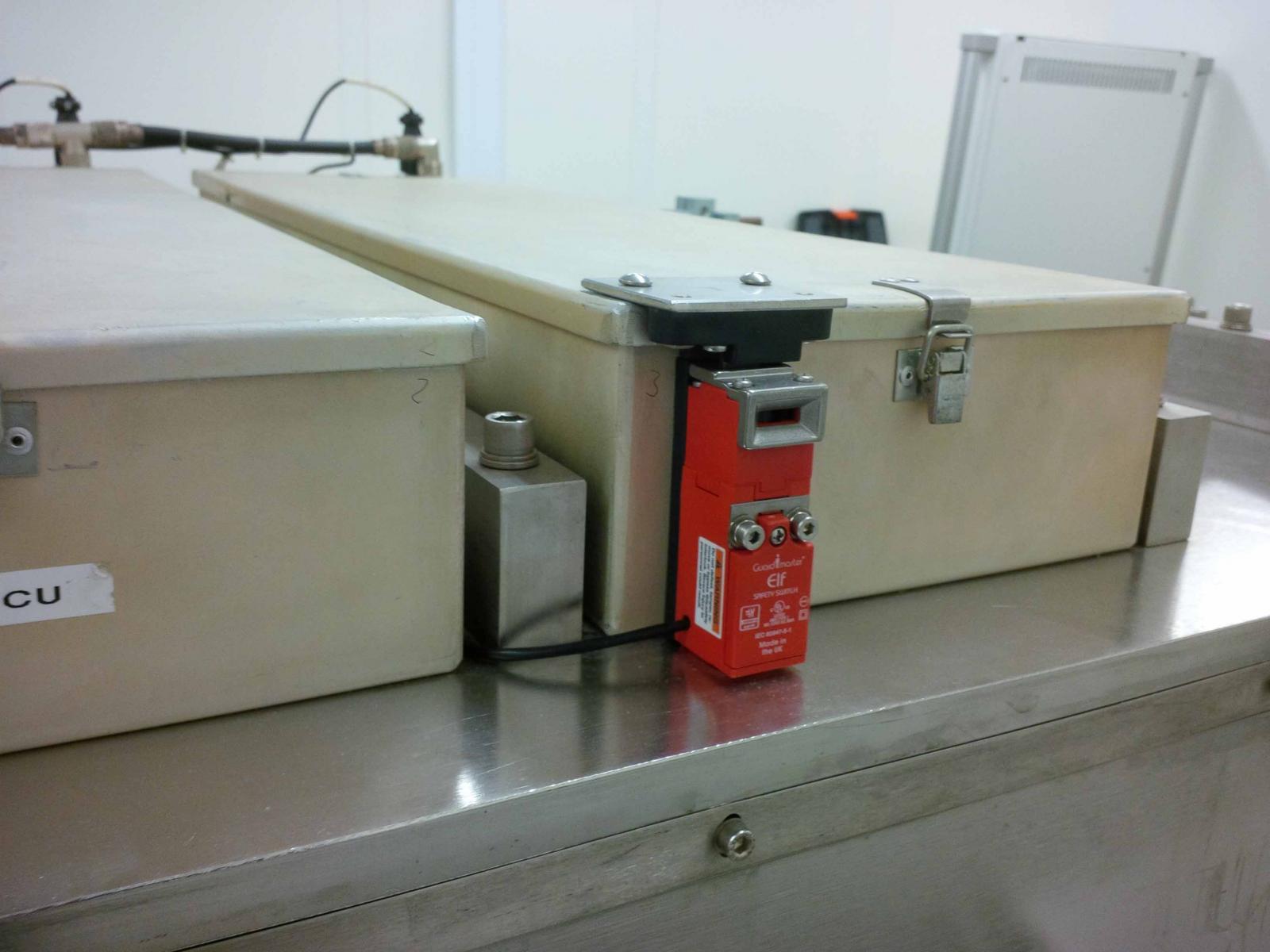

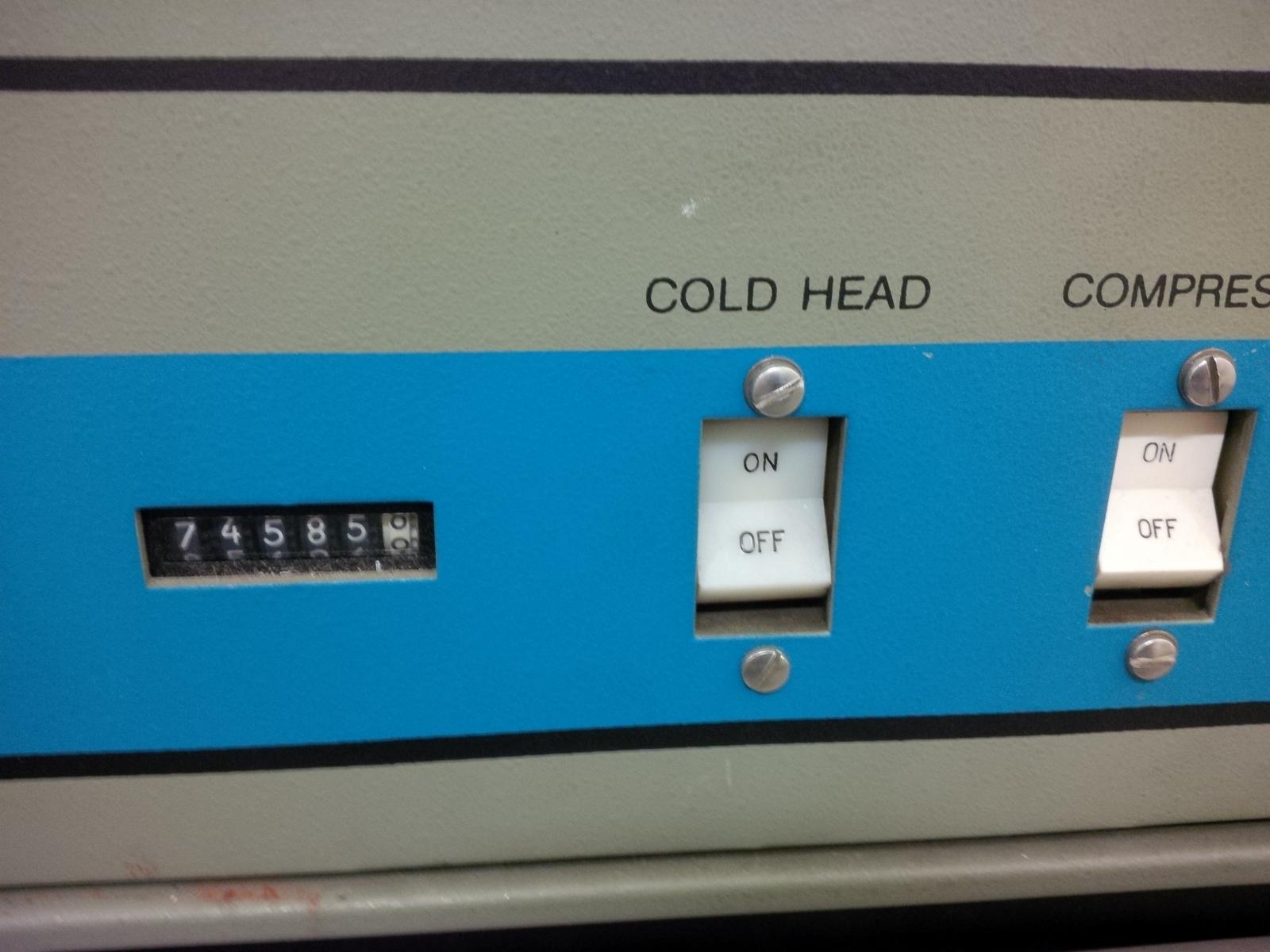

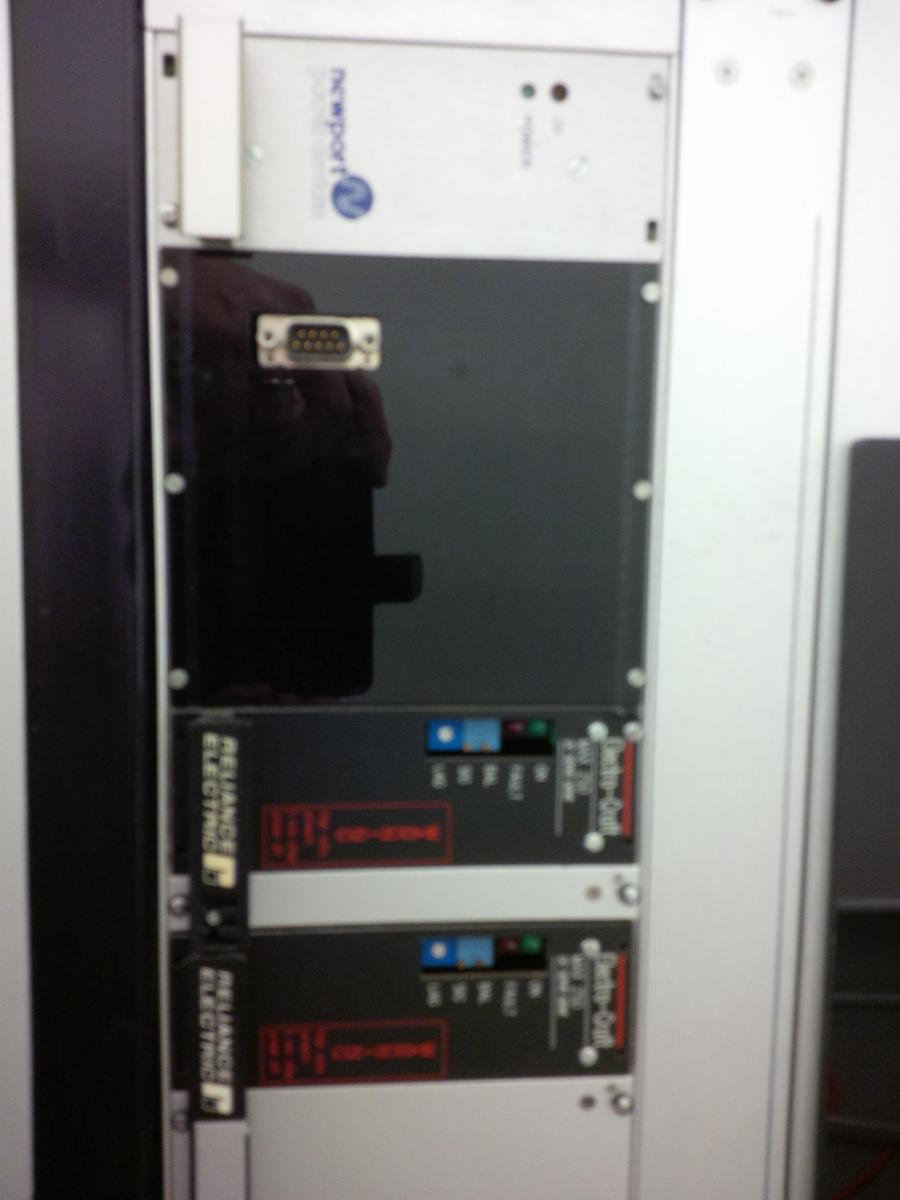

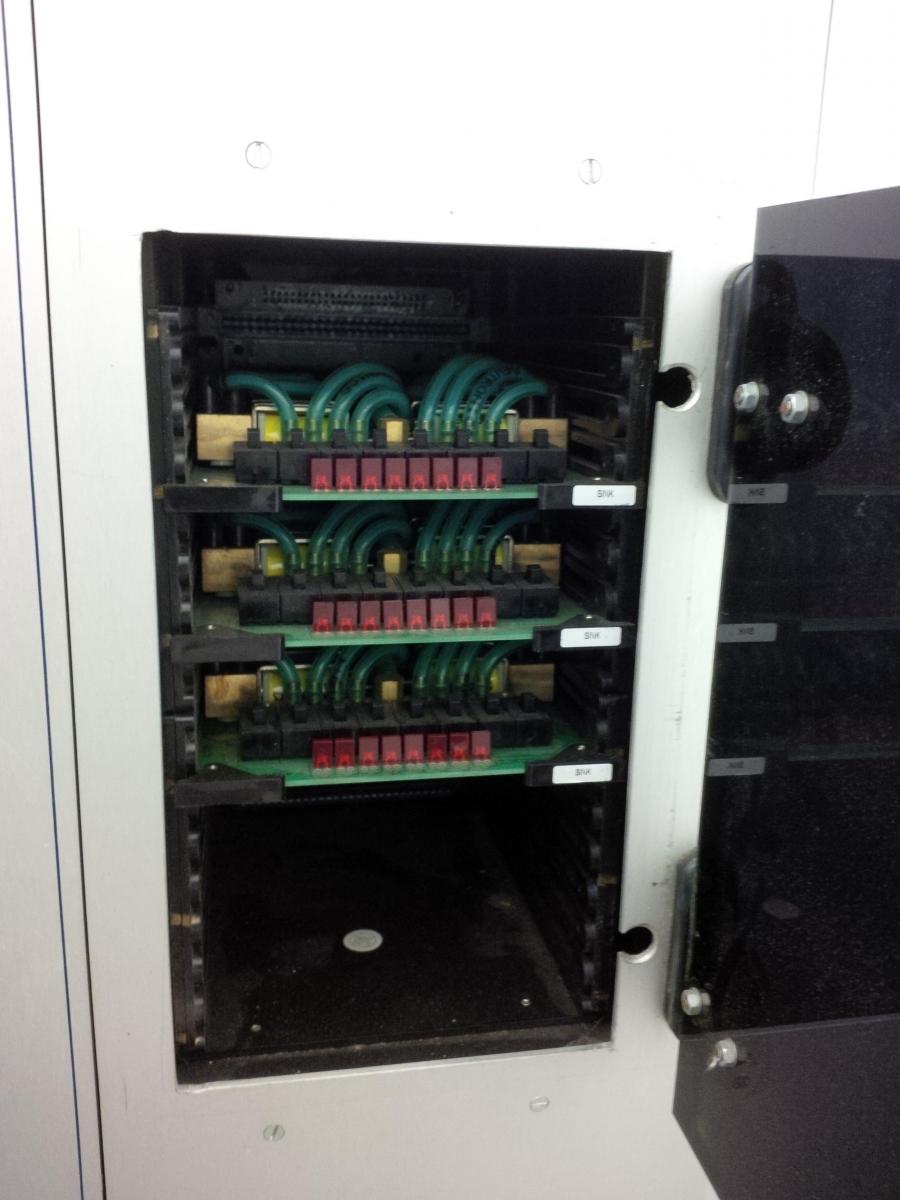

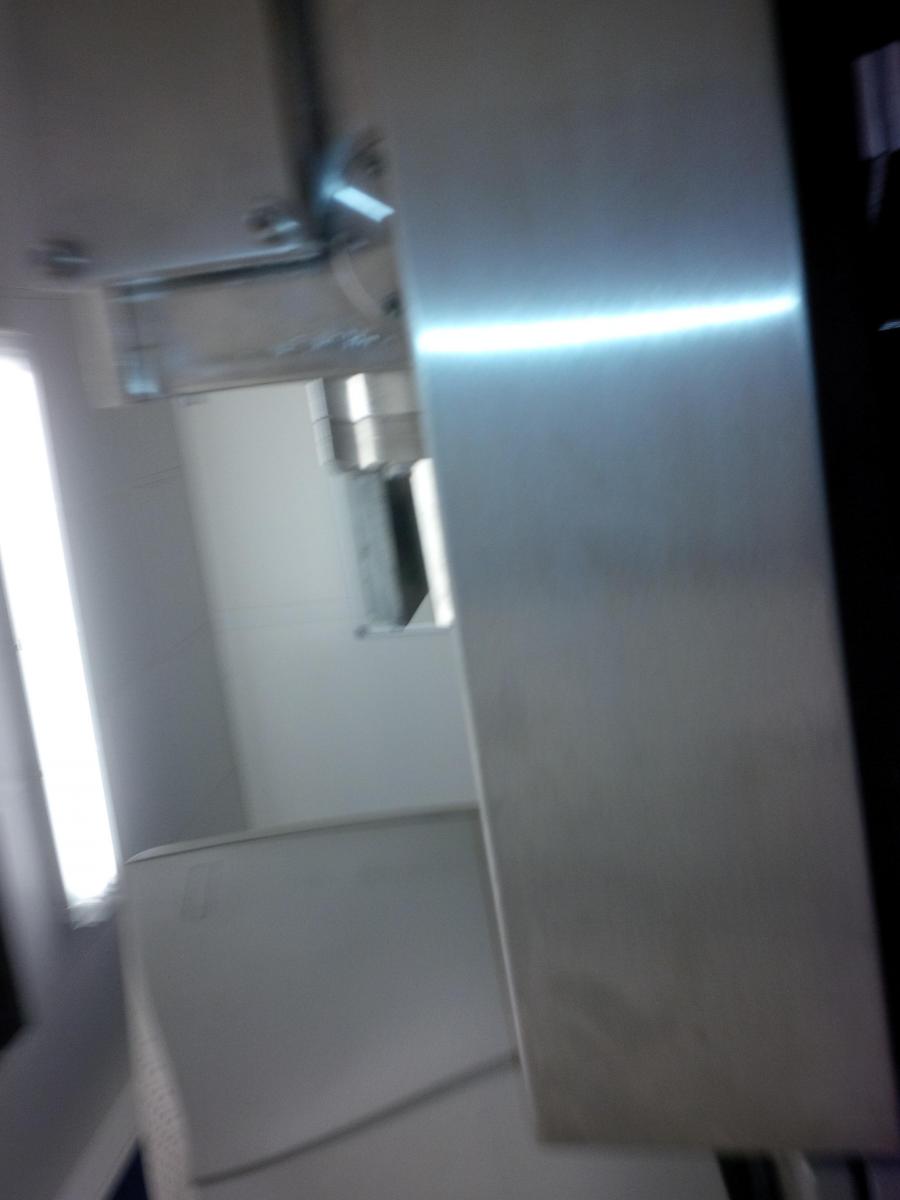

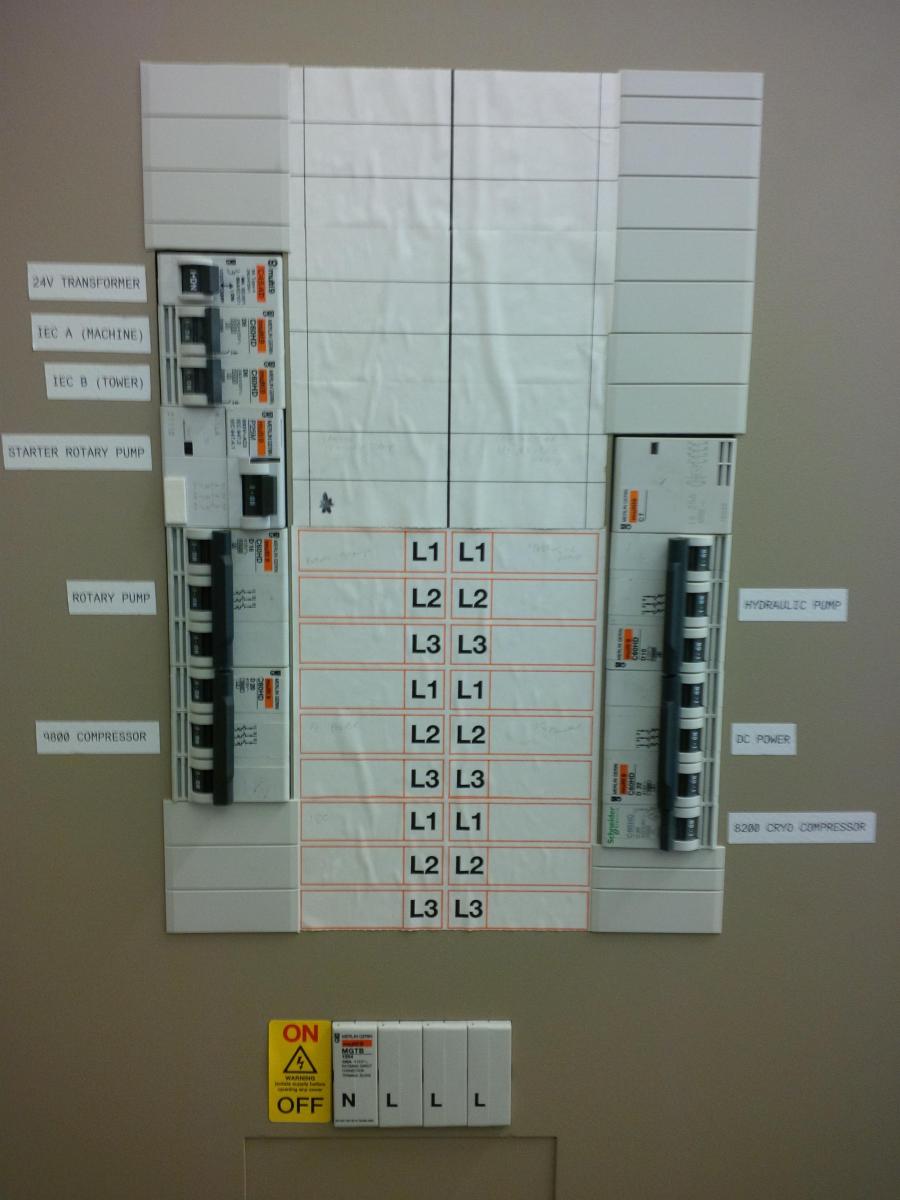

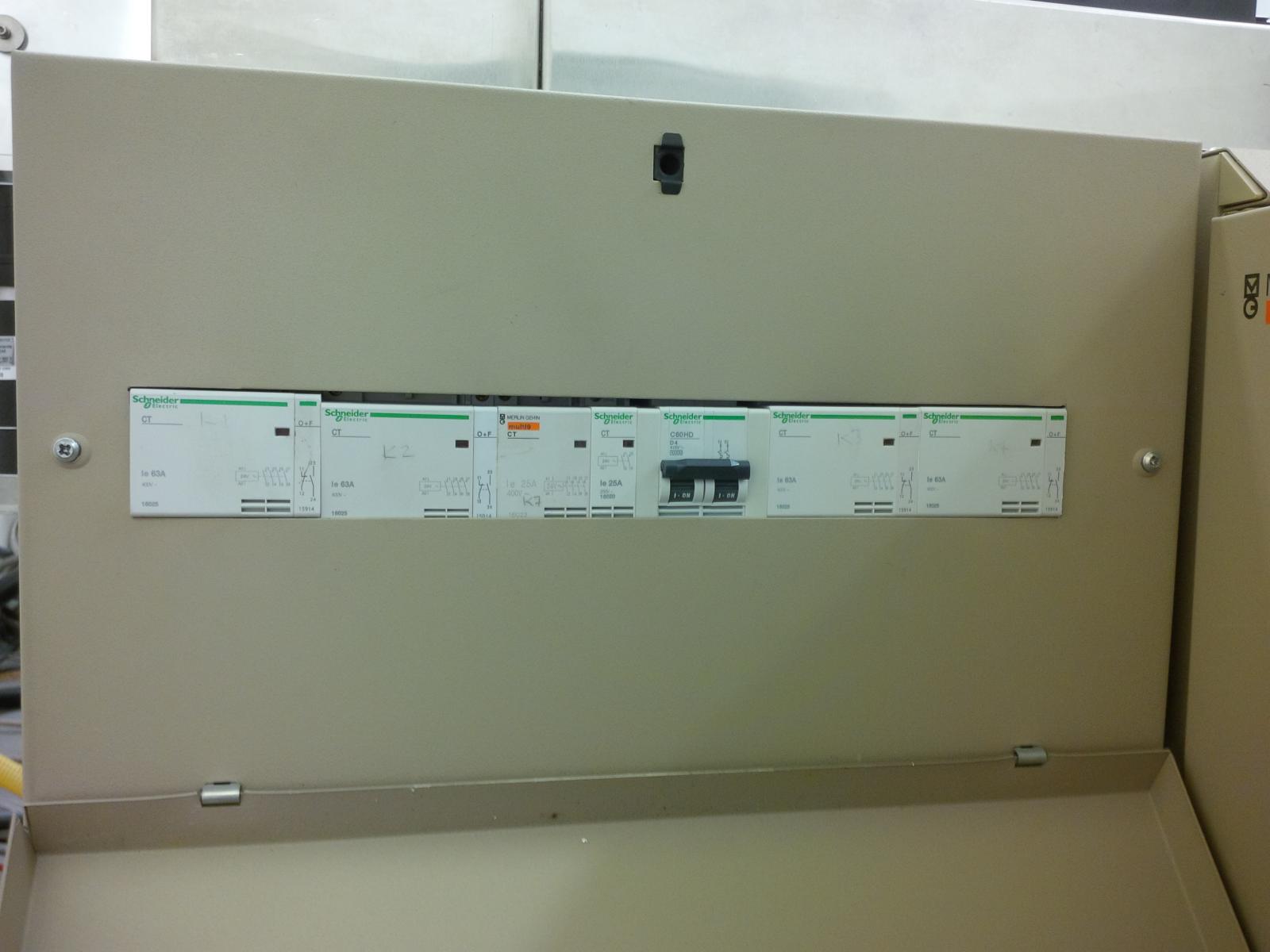

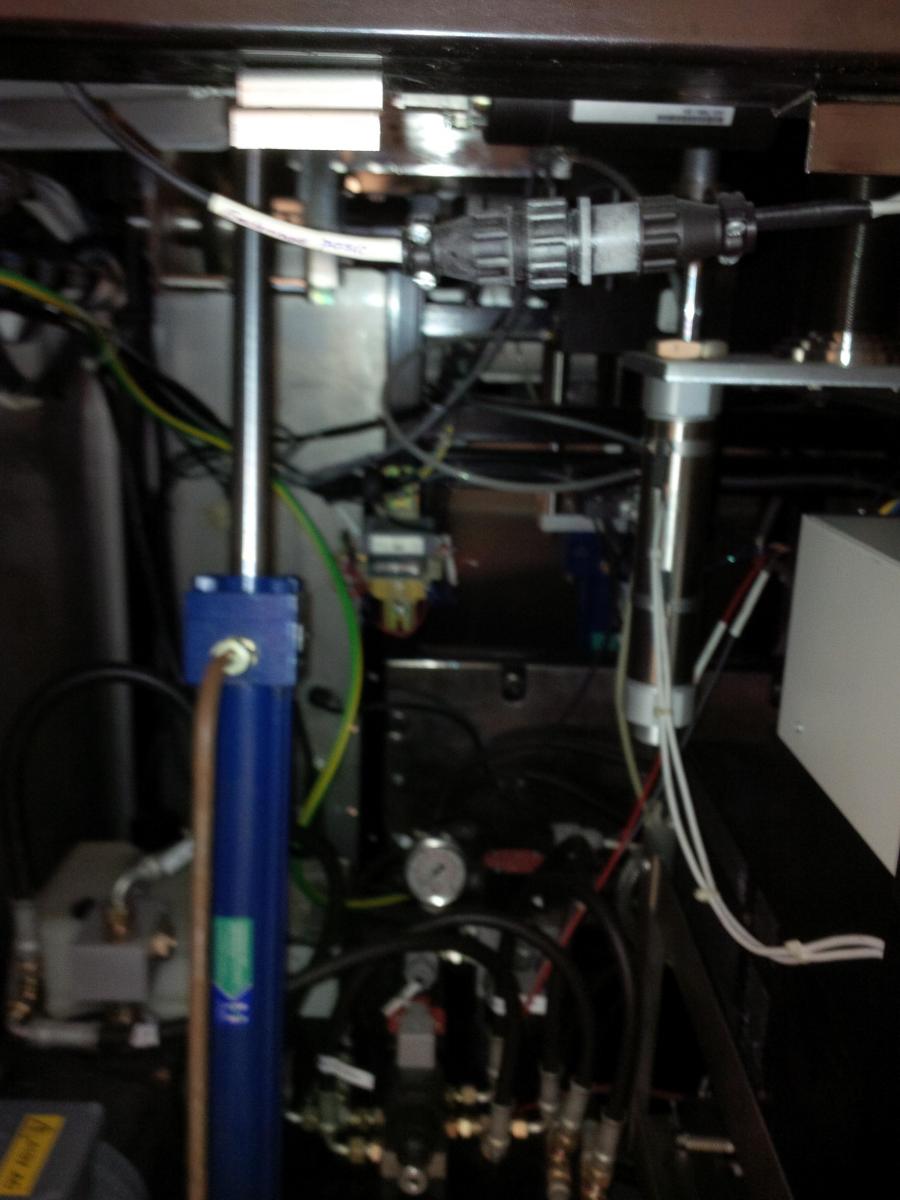

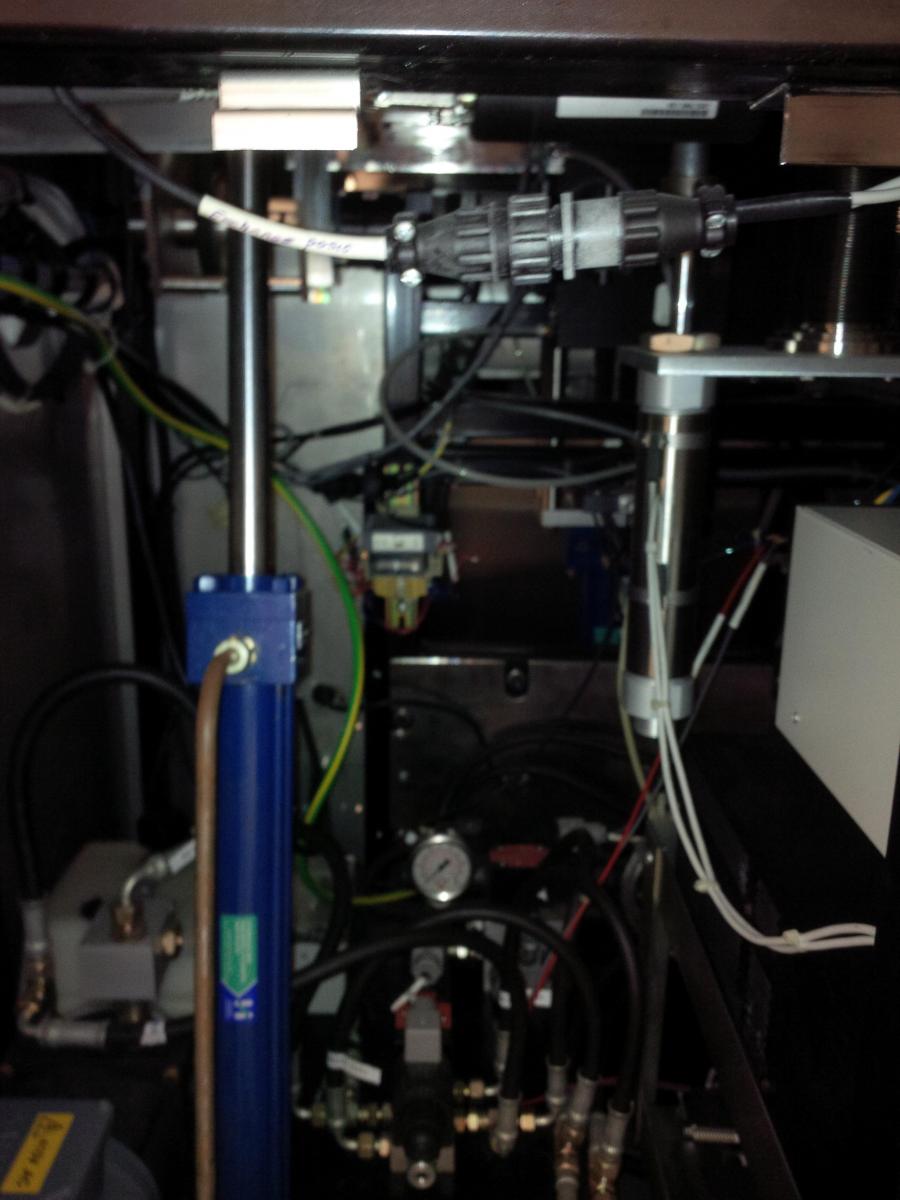

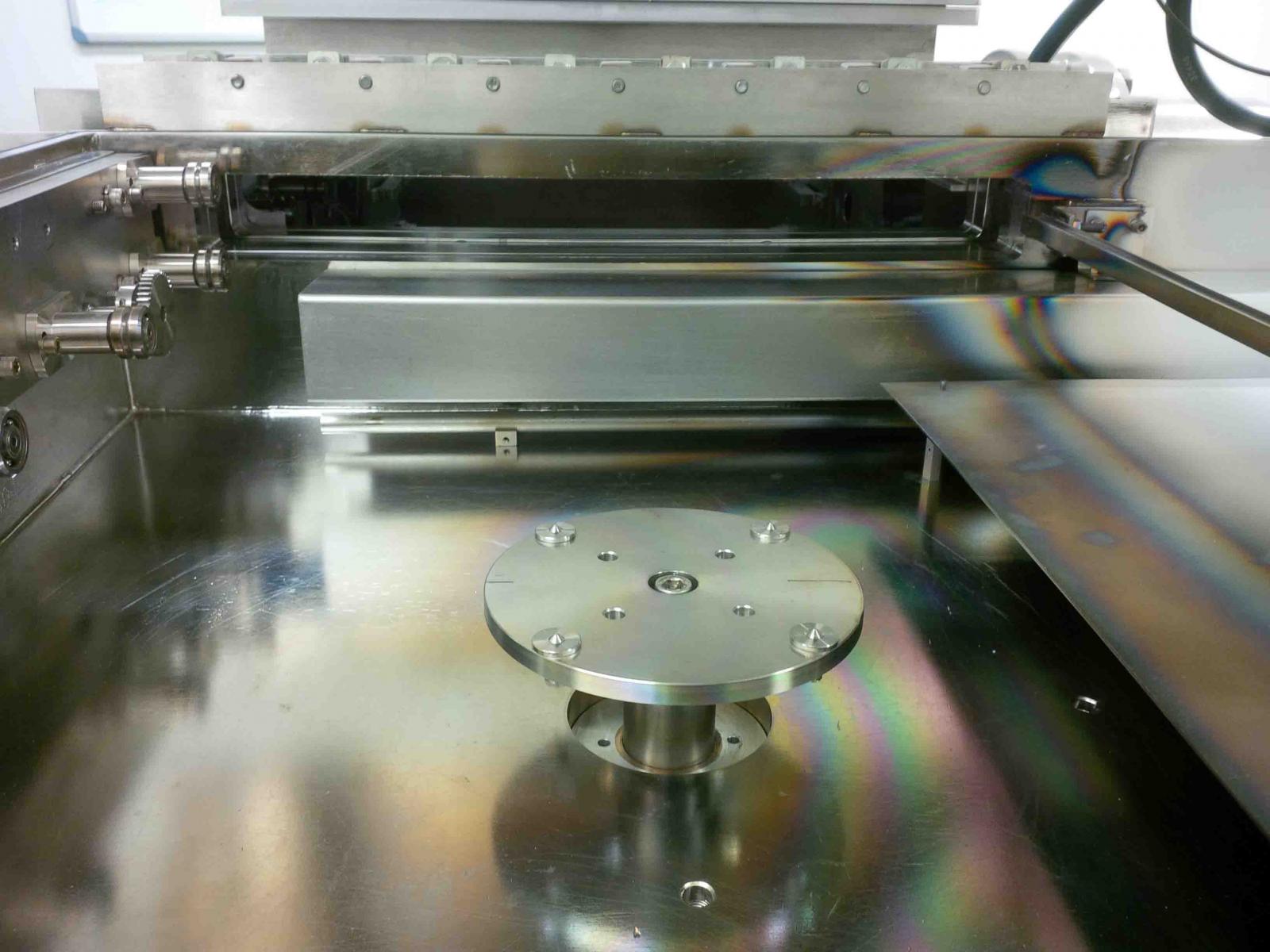

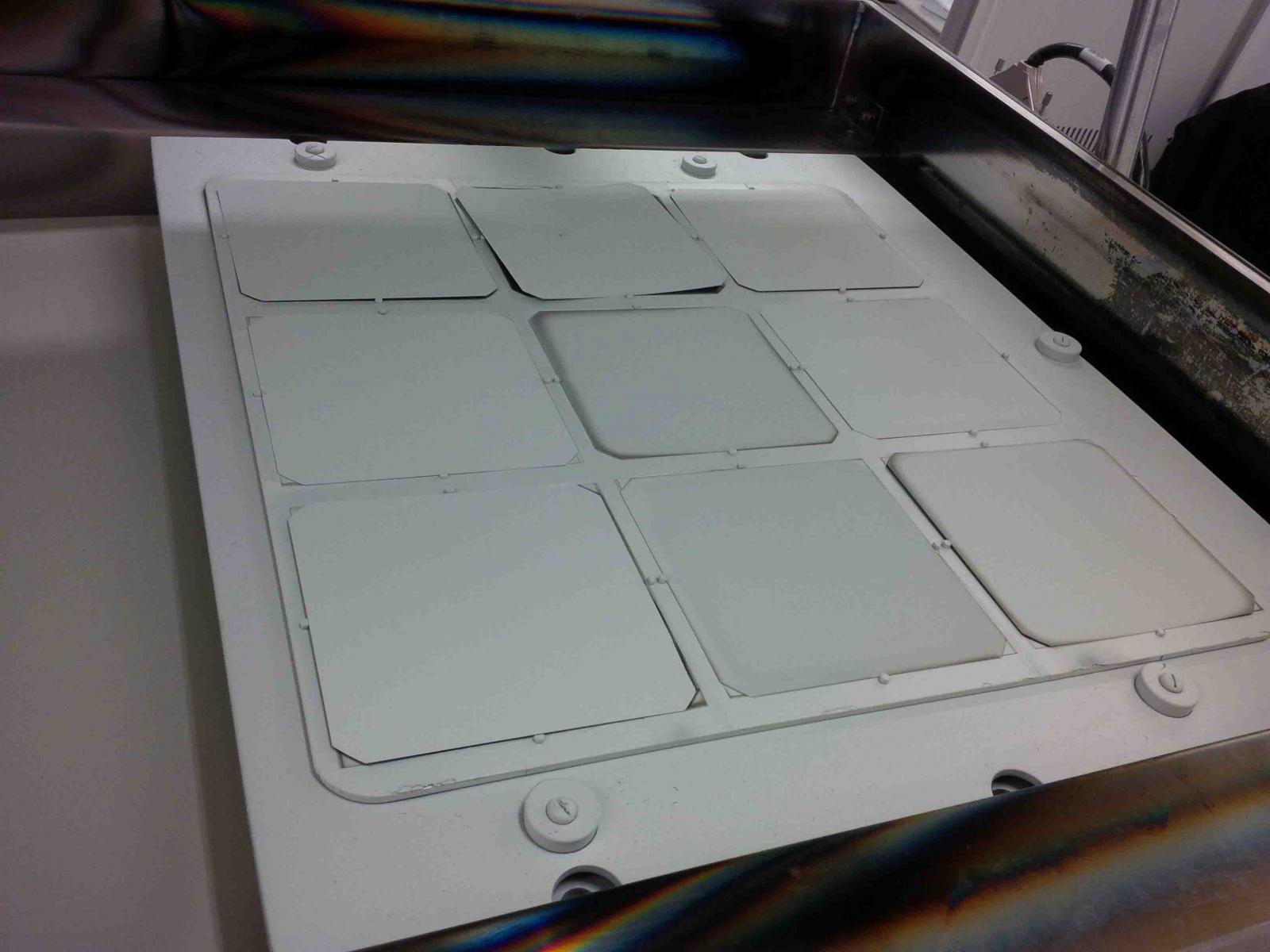

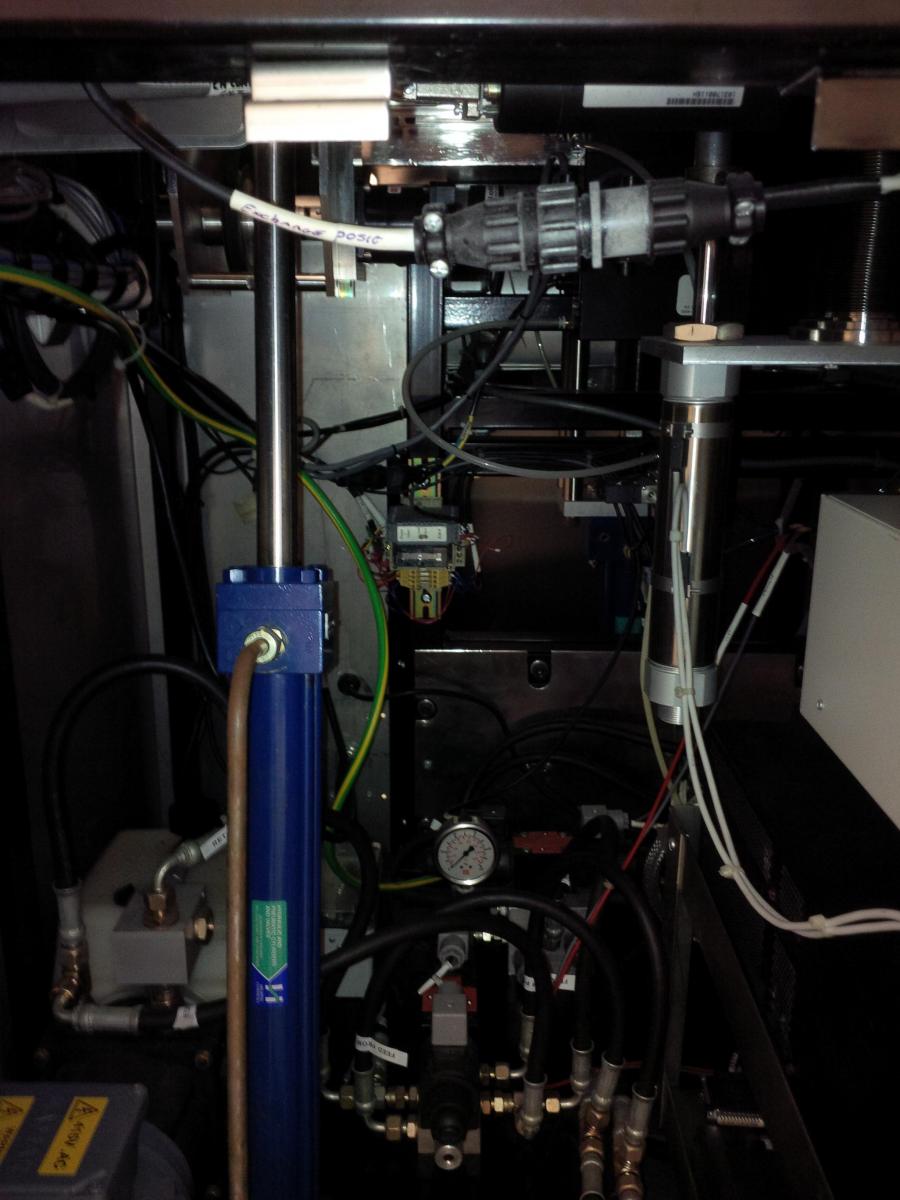

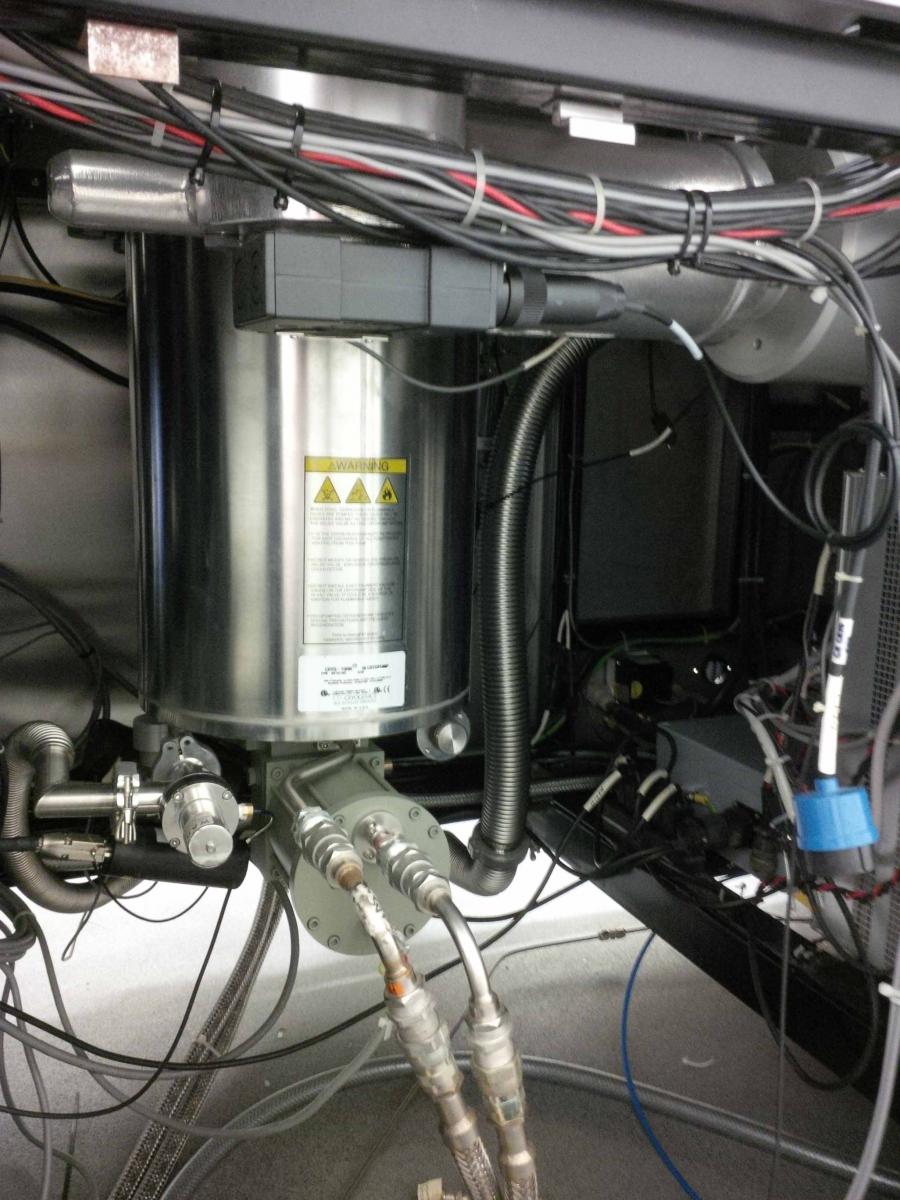


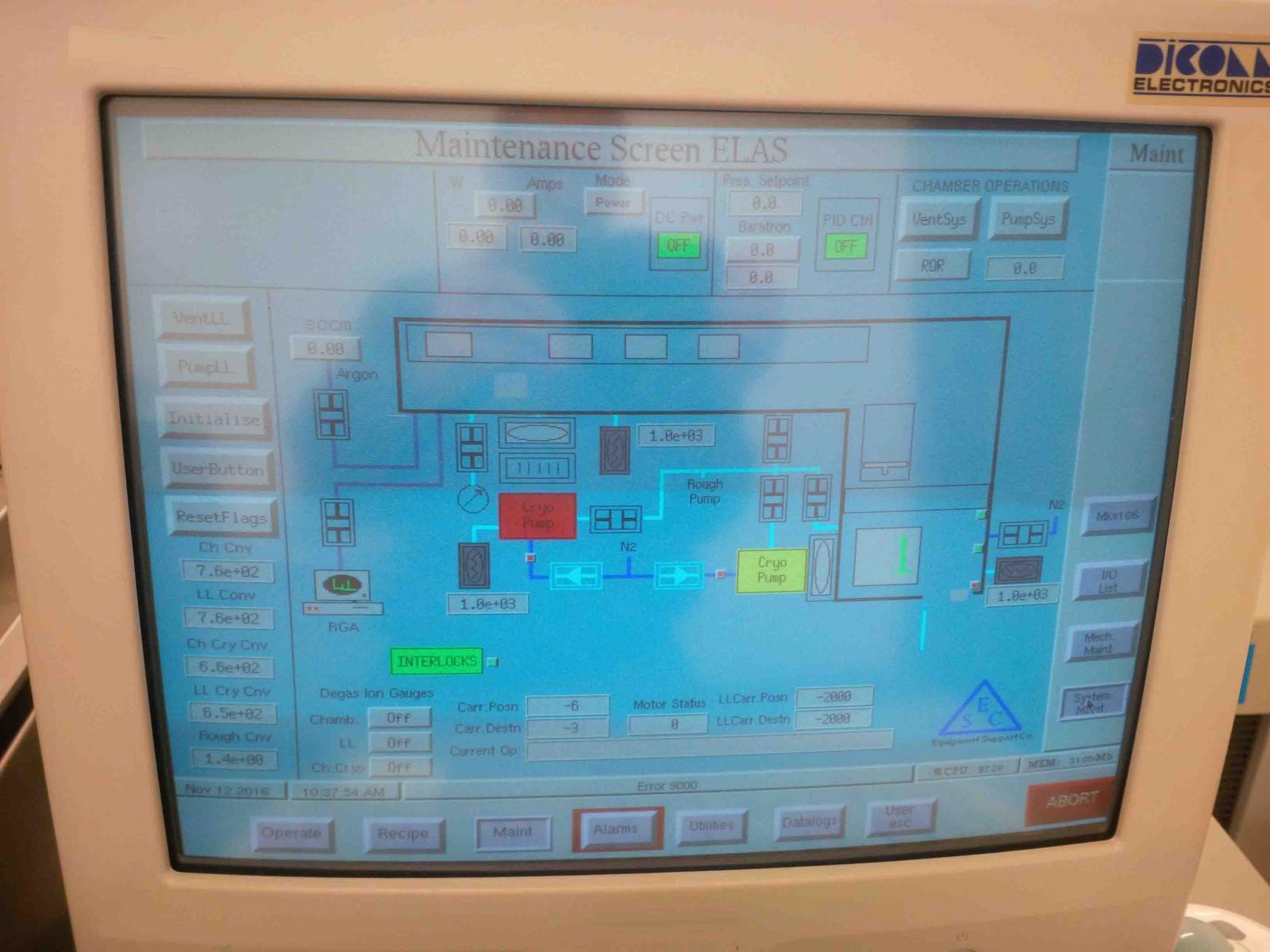

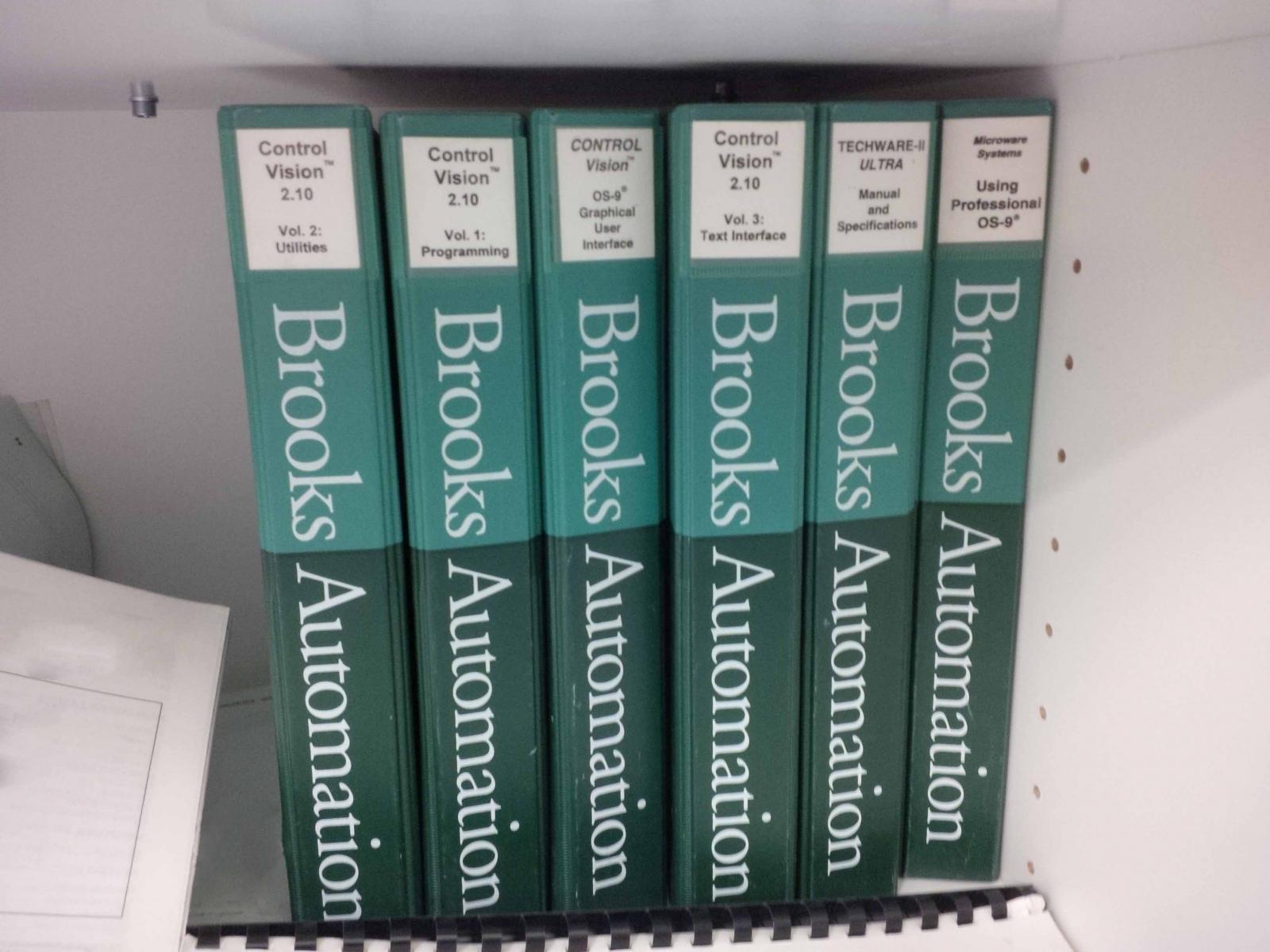

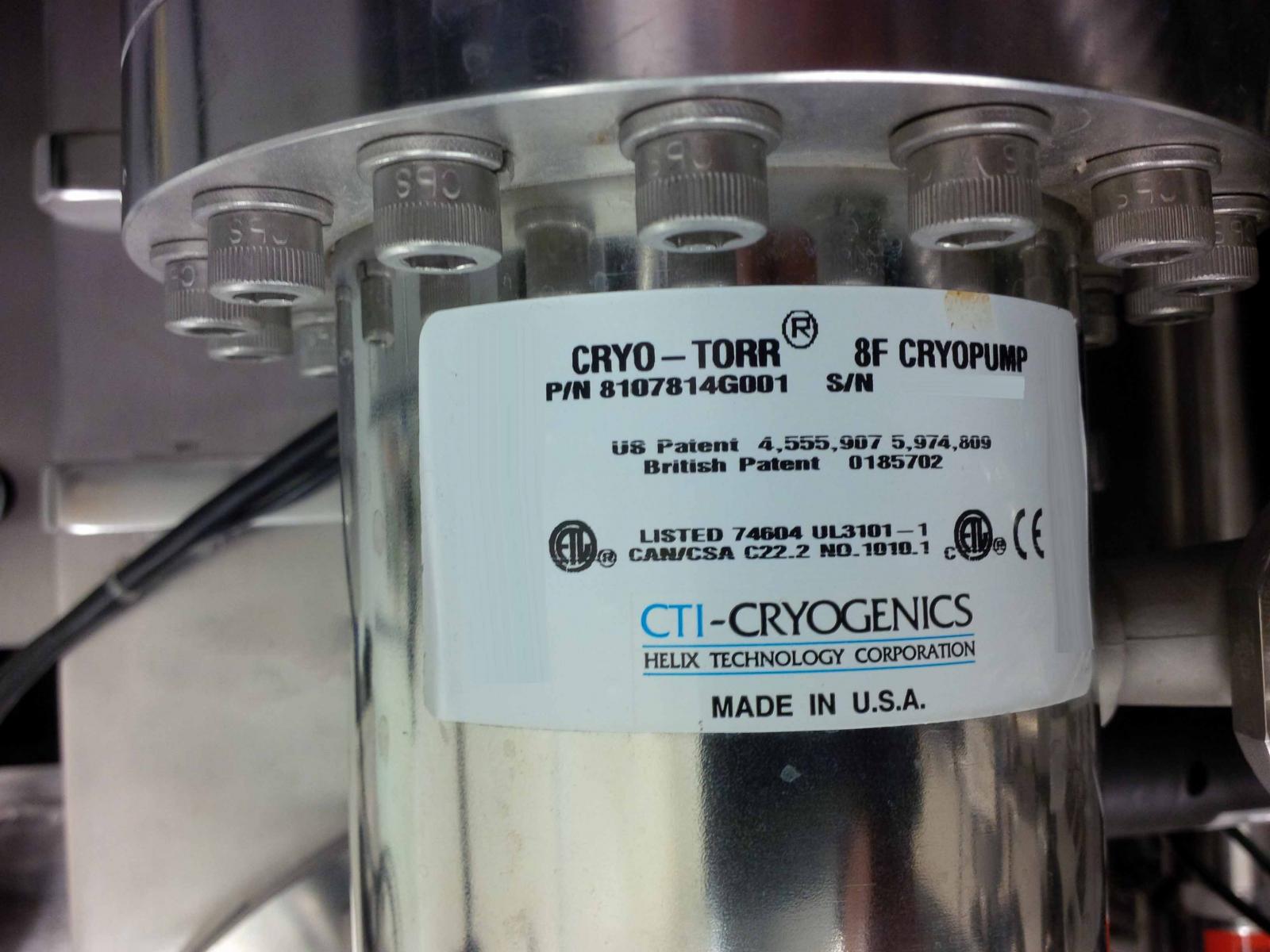

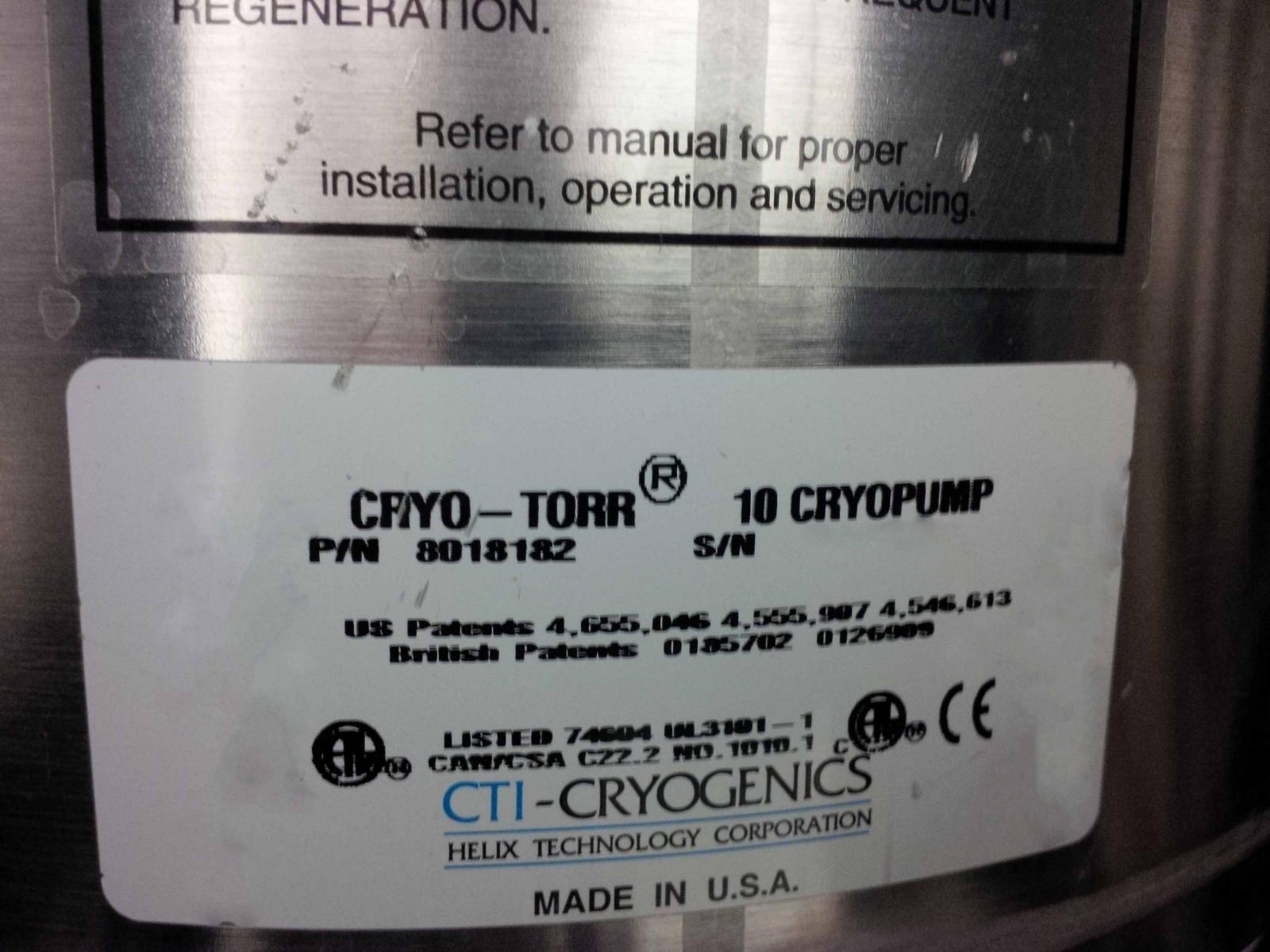

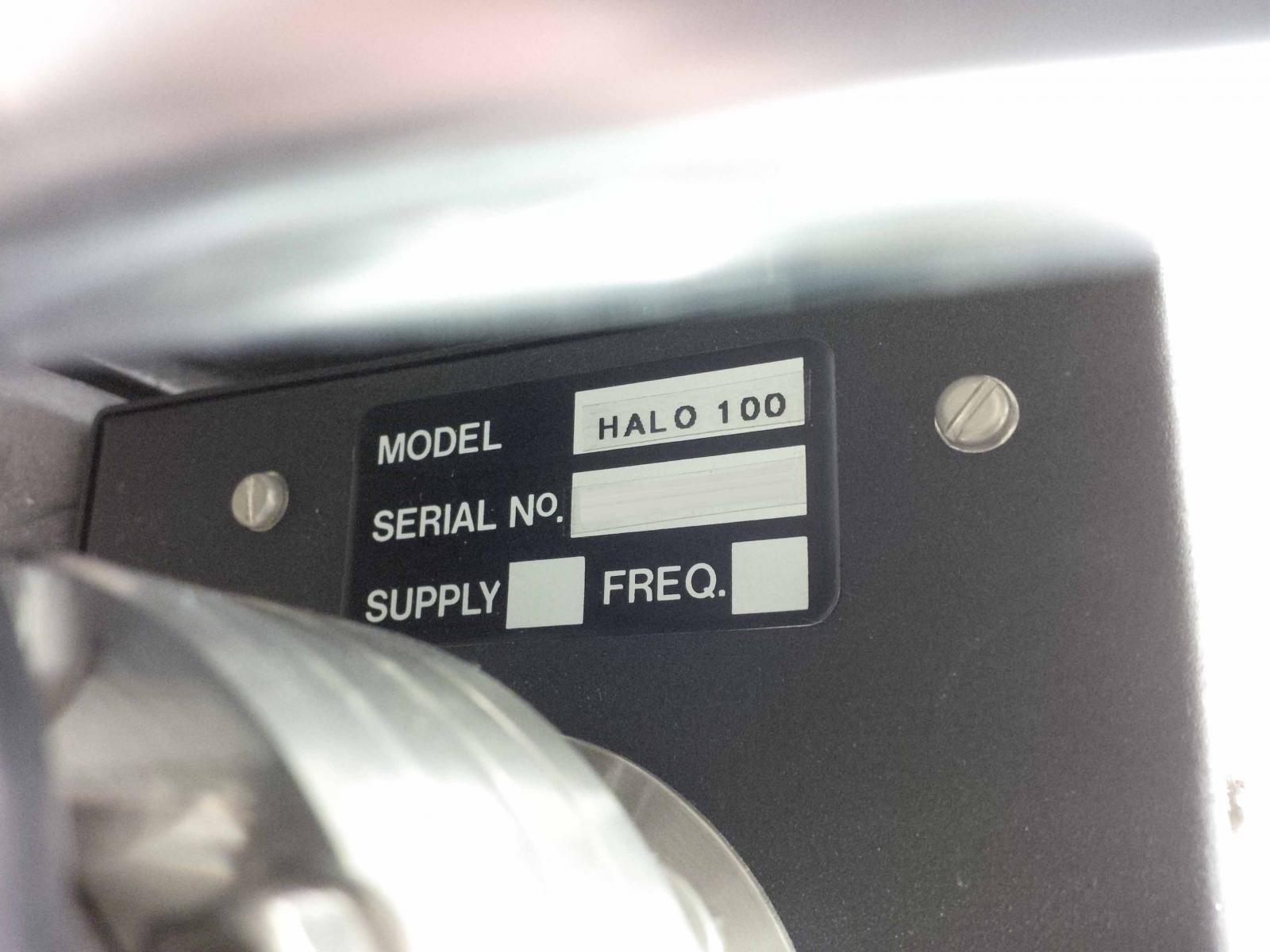

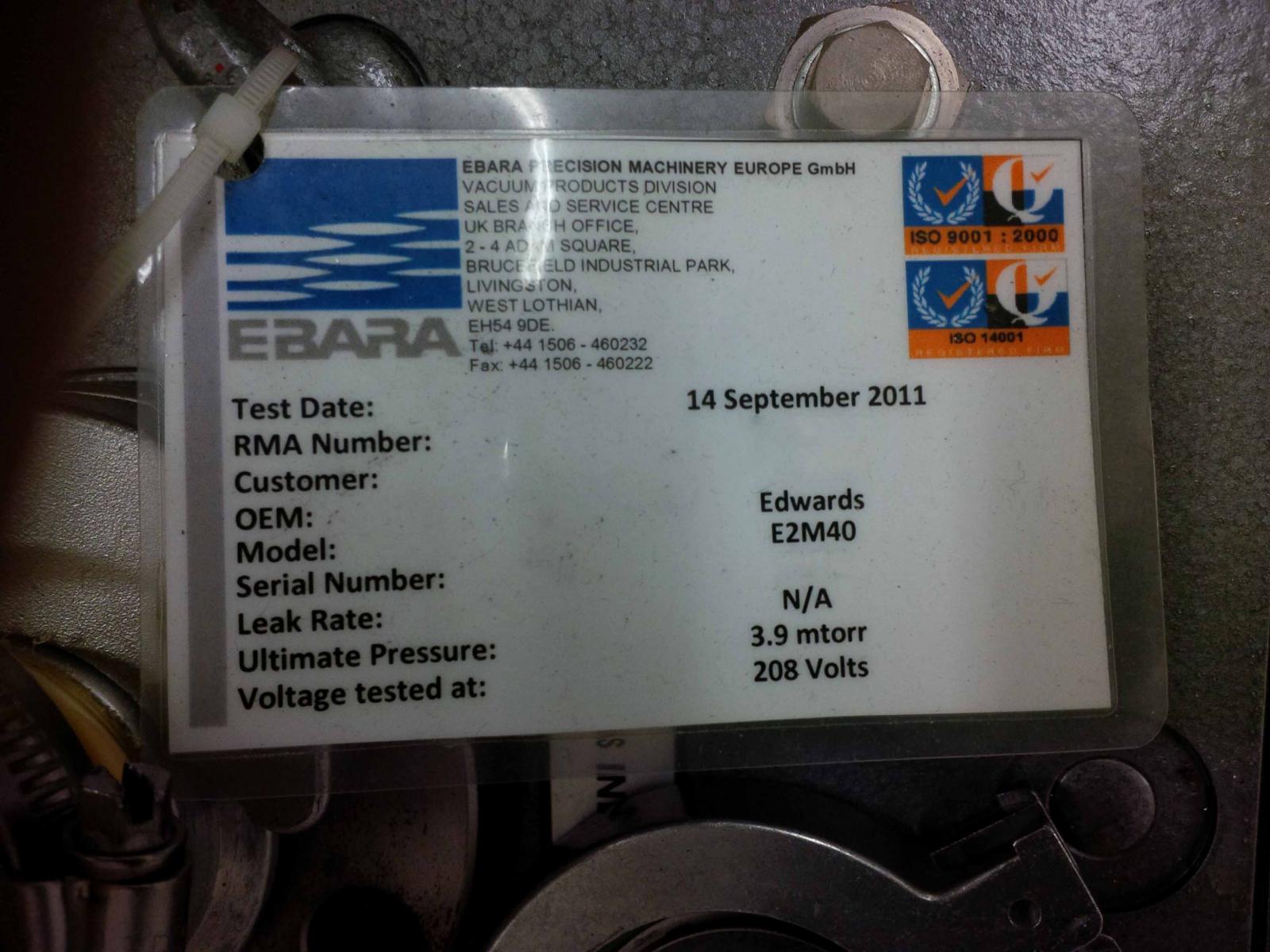

ID: 9131115
Wafer Size: 6"-8"
RF / DC Sputtering system, 6"-8"
RF Magnetron
RF Diode operation
Loadlock cryo pump, 8"
Chamber, 10"
Rectangular
Heliarc welded
304 Stainless steel plate: 16 mm
View-port: Pyrex window
Pump-out port: 225 mm Diameter
Load lock:
2-Level elevator
Non-coated pallets loaded on upper level
Processed pallets unloaded from lower level
VITON O-ring
Feedthrough:
Linear bellows
Magnetically coupled drive
Drive:
Hydraulics
Low pressure drive
Motion:
Loading and unloading
Fully-automatic computer controlled
Capacity:
Diameter wafers: 6-150 mm
Diameter wafers: 4-200 mm
Drive:
Precision DC motor
With optical encoder feedback control
Chain drive
Labyrinth shielded
Option: DC Bias / RF Bias
Coating speed: 3-350 cm/min, Bi-directional
Vacuum system:
Load lock
CTI-CRYOGENICS Cryo-Torr 8 Vacuum pump
Vacuum valve: 6" ASA (7-1/8" Diameter) Gate valve
Electro-pneumatic operation
Valves: 1-1/2" Bellows sealed
Electro-pneumatic operation
Roughing pump: 27 CFM (762 l/min)
With process chamber
Main chamber:
CTI-CRYOGENICS Cryo-Torr 10 Vacuum pump
Vacuum valve: ASA Gate valve, 10"
Electro-pneumatic operation for gas throttling
Load lock and cryo regeneration: 27 CFM Mechanical pump
Anti-back-streaming trap for mechanical pump
1-1/2" Bellows sealed electro-pneumatic operation
Etch platform:
Moves vertically to engage / Disengage the pallet
Cooling: Water-cooled
Material: Stainless steel
Insulator: Pyrex
Dark space shield: Stainless steel
Residual gas analyzer
RF Generator:
Continuously-rated and specifically designed for sputtering: 1 kW
ISM Frequency: 13.56 MHz
FCC and OSHA
DC Magnetron power supply:
ADVANCED ENERGY Pinnacle Power supply, 12 kW
System performance specifications:
Process parameter control ranges:
Description / Minimum / Maximum / Units
Sputtering pressure / 1 / 90 / Millitor
Scan speed (bi-directional) / 3 / 350 / cm/min
DC Sput / 100 / 12,000 / Watts
RF Sput / 0.02 / 2.10 / kVA
- / 0.1 / 2.00 / kW
Etch revel (Note 2) / 0.02 / 1.50 / kVA
- / 0.1 / 1.50 / kW
DC Bias capability:
Internal mechanism: DC Power
DC Bias activated during DC sputtering
Power supplies: 150 V.
ESC ELAS is an electrochemical etching / ashing equipment designed to meet the precision etching requirements of modern thin-film electronics. It is a robust and highly efficient etching system that uses high-density, pulsed DC power for fast, uniform processes. The unit is designed for a wide range of etching applications, including etchable thin-film materials like metals, oxides, and polymers. The process is capable of achieving an etch rate of up to several hundred nanometers per minute, with very precise control over selectivity, depth, line width, and surface roughness. ELAS machine is built on proven technology that includes a hermetically sealed, copper-jacketed torso for insulation and corrosion resistance. The unit is also equipped with an integrated heating element to maintain a stable temperature and a power-regulated etching chamber with self-adjusting pressure adjustments. This ensures uniform etching processes and facilitates repeatable results that are extremely precise. To achieve an optimal etching rate, the tool employs a wide variety of etching agencies, including chemical vapor deposition, or CVD, and high-temperature furnace processes. A separately controlled, inert atmosphere allows for longer etching times, producing deeper etches. Alternatively, short-duration etches with higher efficiency can be achieved using plasma etching in a vacuum environment. ESC ELAS asset can process a wide range of wafer sizes, from small, chip-sized pieces to large, rectangular panels. It is also equipped with an XYZ stage that allows for precise placement and fixturing of the worker during processing. The model also includes E-Beam and X-ray etching process, for more accurate etching results. All of these features combine to make ELAS an excellent choice for precision etching needs. The unit is very reliable and capable of consistently producing high-quality etching results. Furthermore, it allows users to continuously monitor the etch process through advanced diagnostics and offers high reproducibility of results. Therefore, it is ideal for high-precision electronics production applications in the industrial market.
There are no reviews yet