Used HELLER 1809EXL #9247414 for sale
URL successfully copied!
Tap to zoom







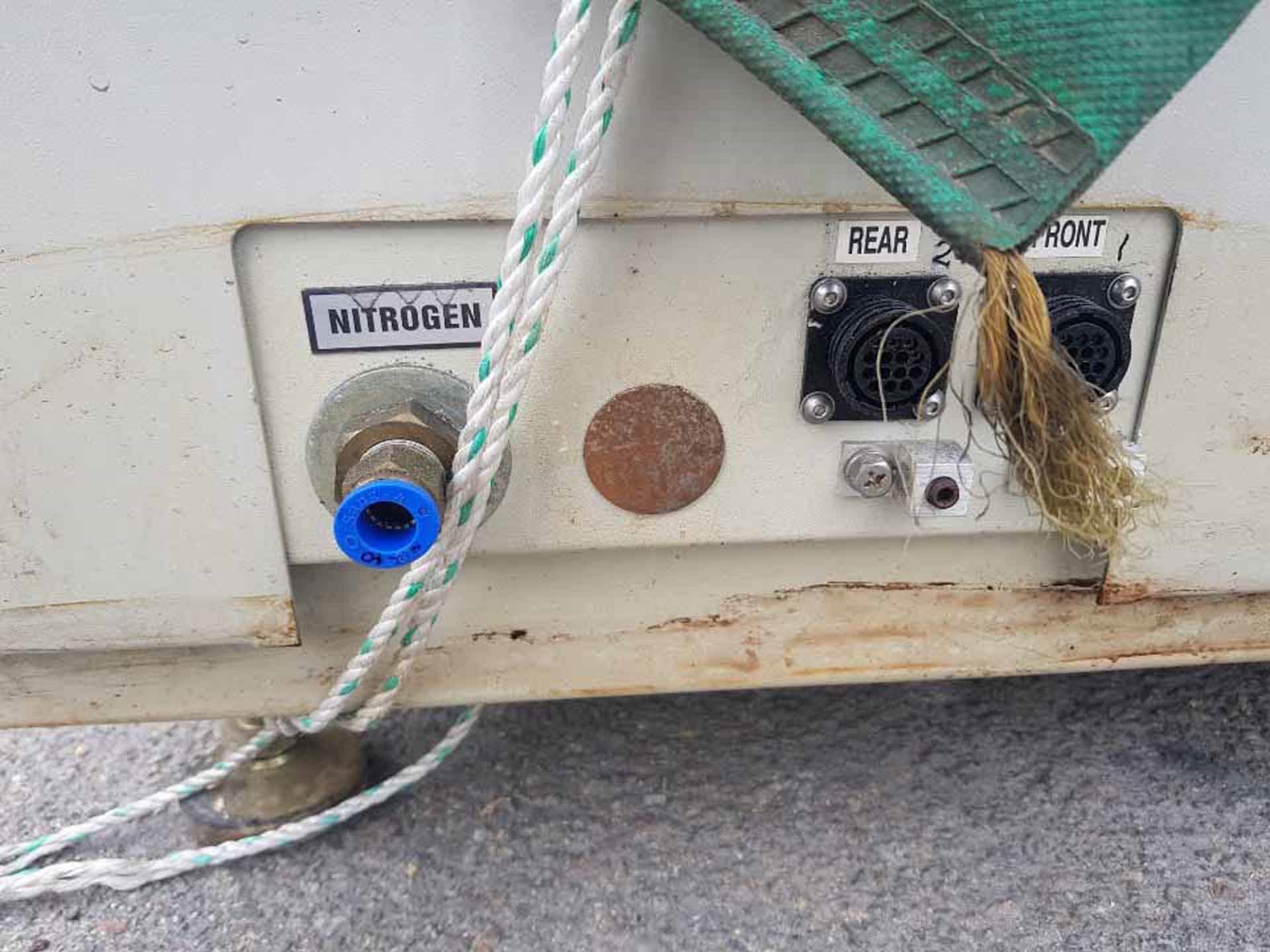

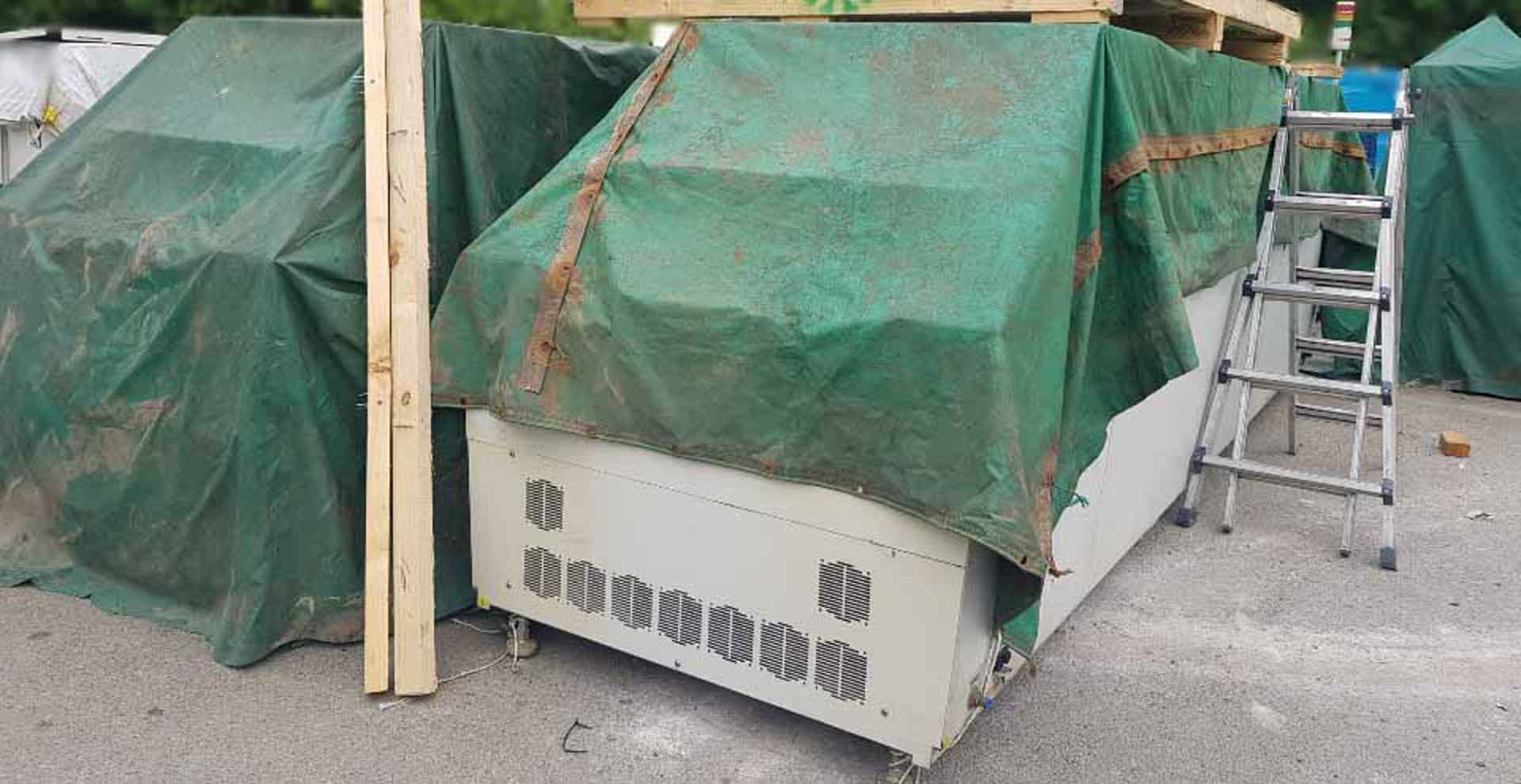

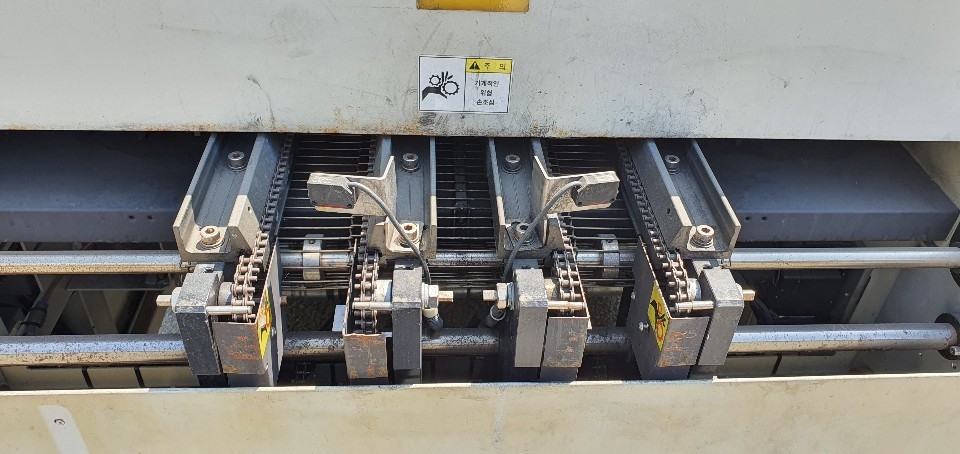






ID: 9247414
Vintage: 2003
Reflow oven
Atmosphere: Nitrogen
Conveyor type: Mesh
Computer control:
Standard computer
Recipe storage: >500
Flat screen monitor
Operating system: Windows XP
Monitor mount
Data logging
Password protection
Inert atmosphere:
Minimum PPM oxygen: 10-25 PPM
Nitrogen cooling
Sample port in reflow
Typical nitrogen consumption: 700-900 SCFH
Mesh belt conveyor:
Height from floor: 35.5" + 2.0" (90 cm + 5 cm)
Maximum PCB width: 10" (25 cm), 15" (38 cm), 18" (46 cm)
(Requires 30" heater modules) 22" (55.8 cm), 26” (66 cm)
Space required between PCB's: 0.0" (0.0 cm)
Conveyor length on-load: 6" (15 cm)
Conveyor length off-load: 6" (15 cm)
Heated tunnel length: 105" (254 cm)
Process clearance above mesh belt: 2.3" (5.8 cm)
Mesh belt pitch: 0.5" (1.27 cm)
Maximum conveyor speed: 74"/Min (188 cm/min)
Conveyor direction: Left to right
Conveyor speed control type: Closed loop
Edge hold conveyor system option:
Height from floor: 37.0" + 2.0" (94 cm + 5 cm)
Clearance above conveyor pins: 1.15" (2.9 cm)
Clearance below conveyor pins: 1.15" (2.9 cm)
Length of PCB support pins: 0.187" (4.75 mm)
Minimum / Maximum board width: 2.0" - 20" (5 –50.8 cm)
Requires 30” heater modules: 24" (61 cm)
Power width adjustment
Auto lubrication system
Forced convection zones:
(9) Top zones
(9) Bottom zones
Heater type: Instant response open coil
Heater material: Ni chrome
Temperature control:
Accuracy of temperature controller: +0.1°C
Cross-belt temperature tolerance: +3.0°C
Heater wattage per zone: 6000W
Temperature range standard: 25-350°C
Insulation type: Calcium silicate
Cooling systems: (2) Cooling zones
Features:
Signal light tower
Powered hood lift
(5) Thermo couple profilings
Power input: 480V, 3-Phase, 11-13 kW
Breaker size: 100 amps@480V
Typical run current: 25-30 amps@480V
Frequency: 50/60 Hz
Sequential zone turn on: Standard
No single phase operation
2003 vintage.
HELLER 1809EXL is an advanced reflow oven designed for precision soldering of electronic components. It utilizes a convection heating equipment that can reach temperatures of up to 350°C (662°F). The oven features a highly efficient heat distribution system that ensures optimal temperature profiles for all boards being processed. The oven can achieve a maximum ramp rate of 8°C (14.4°F) per second, making it ideal for lead-free processes. Additionally, the furnace comes with a nine-zone heating profile for reliable and repeatable thermal profiles. Furthermore, HELLER 1809 EXL features a self-inflating belt technology, which allows components to have precise force applied, optimizing placement accuracy and thermal transfer. The oven also features integrated nozzle interface and pneumatically driven conveyor sections, for quality control of the entire process. It additionally has temperature sensing capabilities, and can accommodate boards over 20" in length by 14" wide. 1809EXL is designed for robust designs with high level of durability for a variety of industrial soldering applications. It has a built-in active cooling unit that allows for rapid cool-downs, as well as an integrated exhaust machine for ideal air-flow and ventilation. The internal insulation design ensures thermal and process repeatability while providing an extremely durable furnace. It is constructed using sheet steel and aluminized steel for greater durability. The control tool for 1809 EXL is equipped with a powerful Allen Bradley® PLC and comes with Push-Buttons, LCD Displays and LED Indicators for convenience and user-friendly operation. Additionally, it is equipped with a 10" HD Touchscreen placed for easy access. The software can store and recall up to 40 thermal profiles and process recipes can also be stored for consistent repeatability. The furnace can be monitored and accessed remotely using Modbus/TCP Ethernet protocol capabilities. HELLER 1809EXL is certified to UL and CE standards and is designed with an exclusive lifetime warranty on its stainless steel chamber. This makes HELLER 1809 EXL the perfect choice for advanced reflow soldering needs.
There are no reviews yet