Used ASYNTIS Silicon Star 8 #9114174 for sale
URL successfully copied!
Tap to zoom
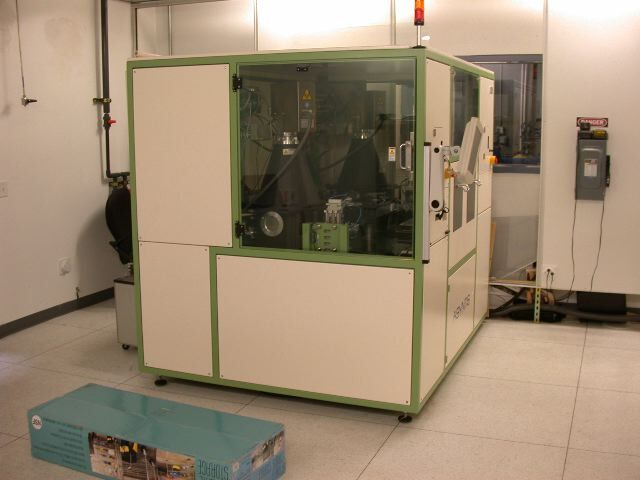

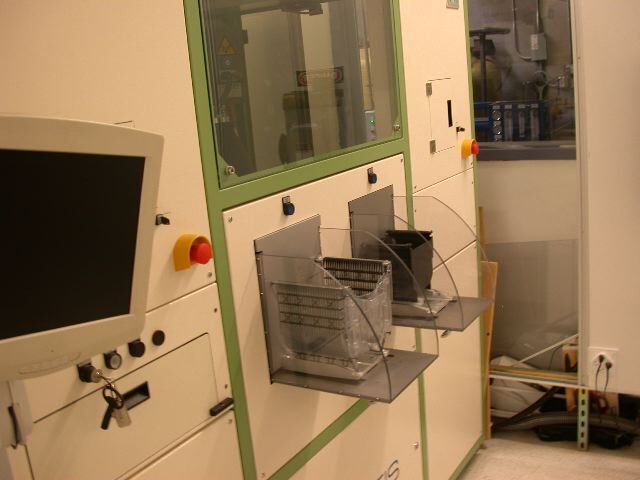

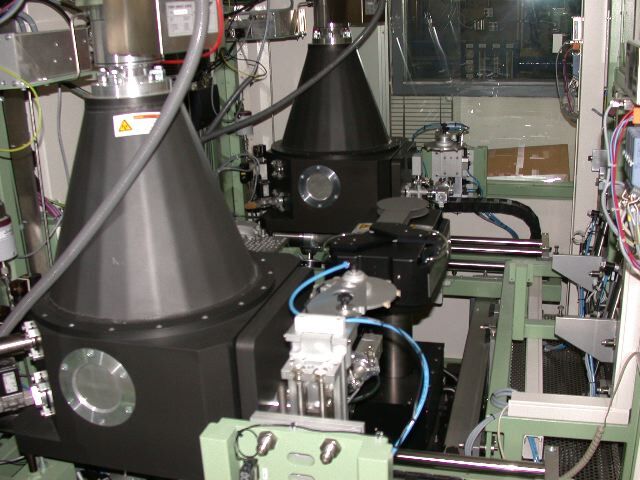

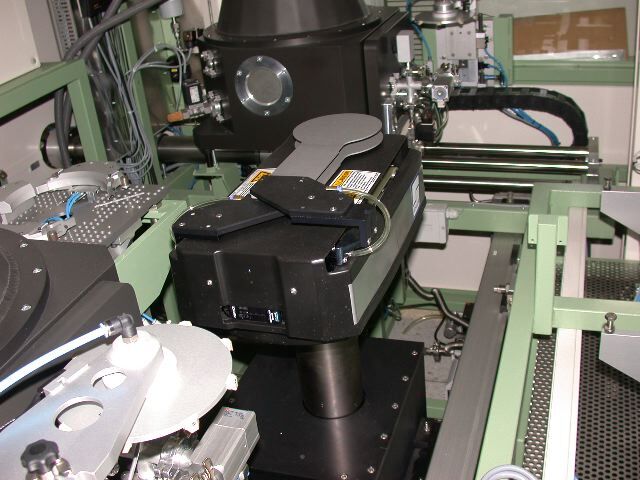



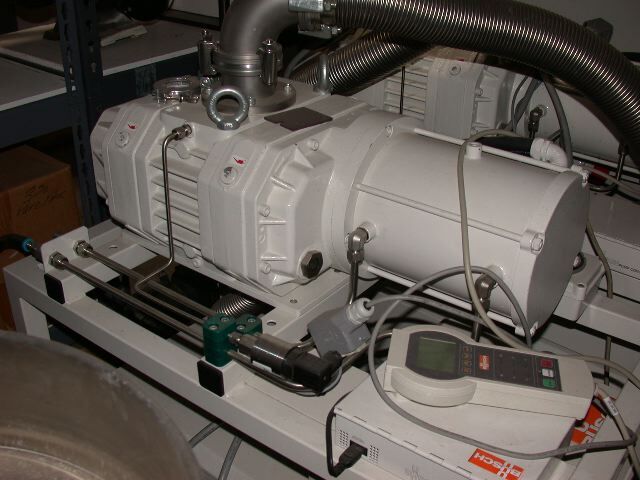

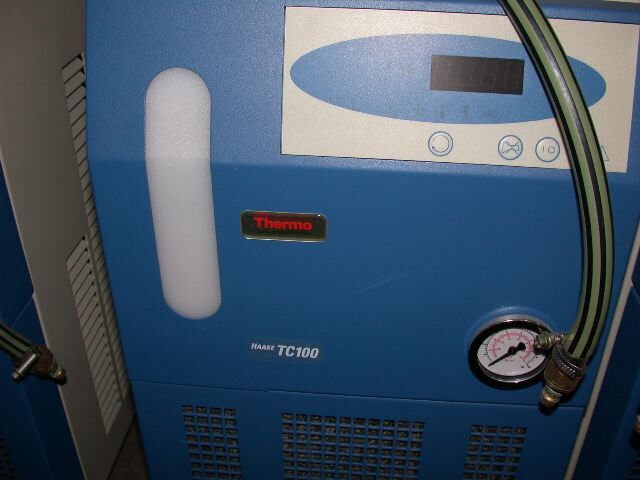

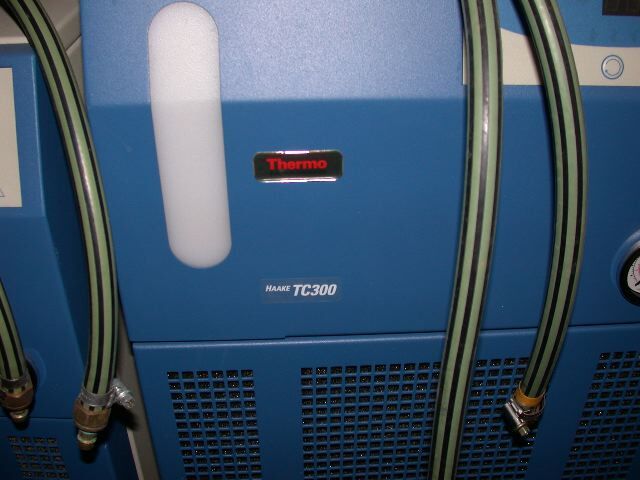

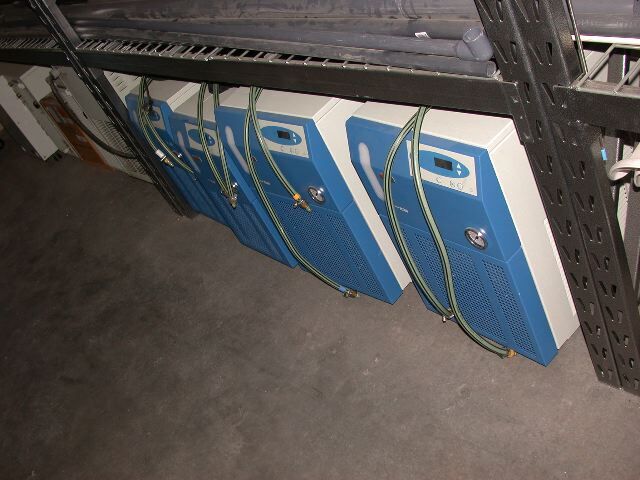

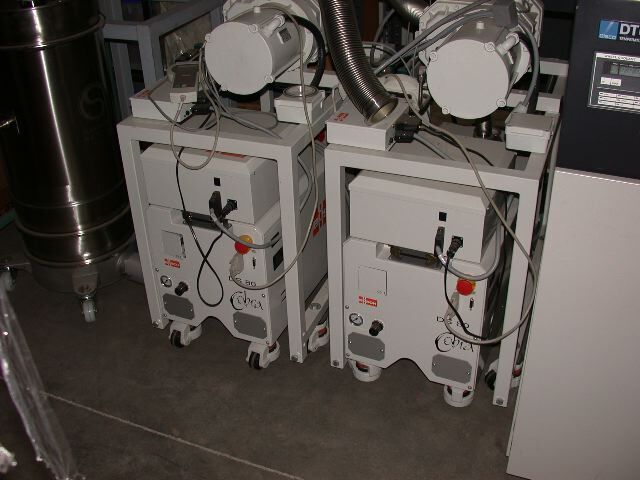

ID: 9114174
Wafer Size: 8"
Stress relief system for plasma etching, 8"
Process data:
Etch rate: up to 3 µm/min at process temperatures less than 70°C
Throughput: 40 wafers/hour at 3 µm removal
Process chamber:
Inner diameter: 400 mm
Chamber volume: 40 L
Radical source on chamber top (remote plasma)
Vacuum outlet with solenoid valve DN 63 ISO-K on bottom
Automatic drawer door
Viewing window
Chamber leak rate: less than 5 Pa L/sec
Radical generator:
Water-cooled microwave radical generator
Maximum power consumption: 2 kW
Frequency: 2.45 GHz
Water-cooled magnetron
Gas supply:
(3) Gas channels with solenoid valves and MFC's
Stainless steel piping with 6 mm SWAGELOK fittings
Down stream controller: butterfly valve DN 63 ISO-K
Chuck system:
Top plate for 8" wafers
Water-cooled base
Chamber controller:
PLC controller and LCD display
Multiple process programs
Online viewing of process parameters
Status and error messages
Vacuum measurements:
Capacitive vacuum gauge: gas type independent
Measuring range: 1 to 1,000 Pa
Main control unit:
SIEMENS Simatic S7
Graphical user interface
Online control of all parameters
Robot system: 3-axis robot with servo drives
Safety precautions:
Emergency stop switch
HF and UV absorbing view port
Safety interlock system
CE assembly and wiring regulations compliant
(2) Cassette loaders
(6) THERMO ELECTRON / HAAKE chillers: TC100 / TC300
(2) BUSCH Cobra DS 80 hivac pumps
Facilities requirements:
Cooling water for plasma source: 1/4" brass, 3L/min, 26°C, 0.5 to 1 bar
Cooling water for chuck system: 1/4" brass, 5 L/min, 5 to 40°C, power: 2kW
Process gas: 6 mm SWAGELOK, stainless steel, input: 2 bar
Compressed air: 12 mm SWAGELOK, stainless steel, input: 4 to 6 bar
Nitrogen purge: 12 mm SWAGELOK, input: 2 bar
Currently in storage
230/400 VAC, 50/60Hz, 3-phase, 63A
2005 vintage.
ASYNTIS Silicon Star 8 is an etcher/asher designed to meet the needs of a variety of industries. It is suitable for a wide range of applications and processes. The machine is equipped with a high-precision spatial optical equipment, which supports a wide range of resolutions. This allows users to achieve very precise and accurate measurements. The system provides 8 simultaneous high-resolution optical beams, with a possibility of further division of beams up to 80 million times for accurate etching and ashing. The accuracy provided by the unit exceeds 5nm in vertical direction and 1nm in 2D direction, making it perfect for highly precise lithography. The machine is further equipped with a variable focus lens. This feature enables simultaneous control of depth of field and intensity, which is particularly useful in the semiconductor industry. The etcher/asher is also equipped with a low-loss and vibrational resistant optical head movement machine. The tool is capable of positioning with an accuracy of 1µm in horizontal direction. Positioning accuracy on the vertical axis is within a 500nm band, allowing for considerable accuracy of application. Silicon Star 8 has a multi-functional cooling asset, designed to cool the optical components in an efficient manner. Although the model is designed to utilize natural air convection to cool components, the equipment is able to actively cool the optical components by regulating the air flow. This, in turn, ensures that the system is running at optimal performance at all times. The unit is further equipped with a high-precision optical tracking machine. This tool is capable of tracking the material being etched or ashed in a real-time. Position, orientation, and thickness can be tracked for accurate and precise etching or ashing. Finally, the asset is equipped with an automatic selective etching technology. This feature enables users to etch materials selectively, without the need for manual intervention. This feature is very useful when dealing with complex and intricate patterns. Overall, ASYNTIS Silicon Star 8 is a powerful etcher/asher that provides users with a high degree of precision and accuracy. The model is suitable for a wide range of industries and processes, and its features make it highly sought after for demanding applications in the semiconductor industry.
There are no reviews yet