Used CUSTOM Ion Beam Depostion #9140925 for sale
URL successfully copied!
Tap to zoom
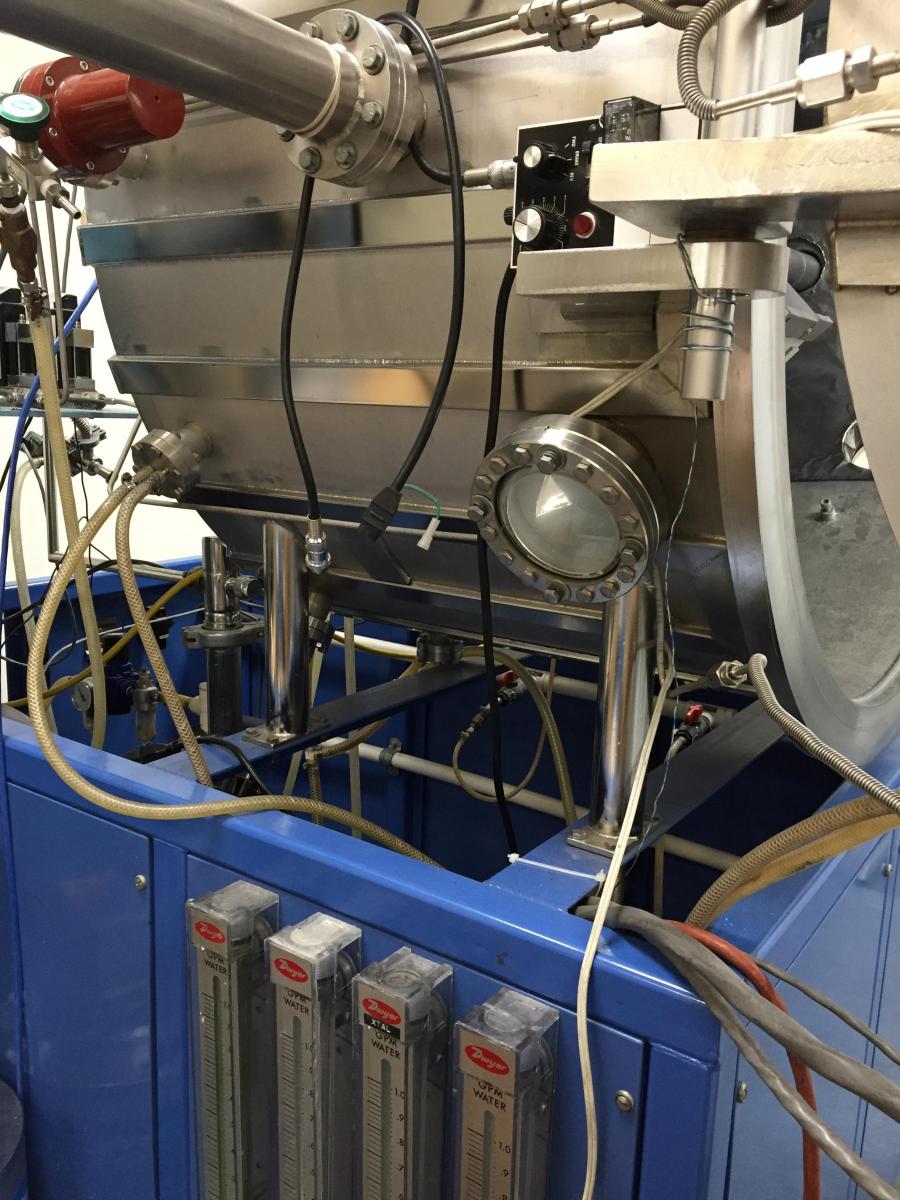

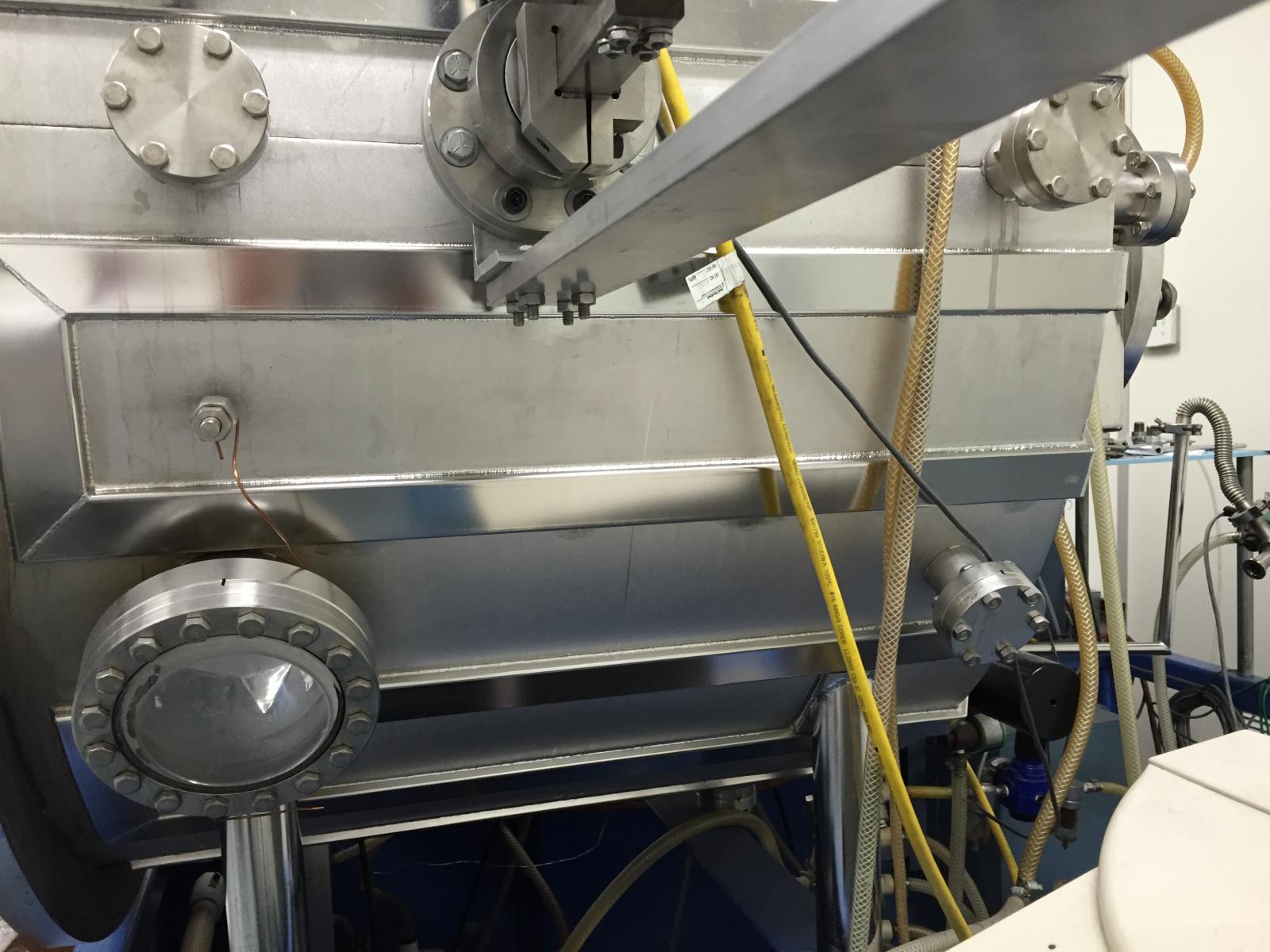

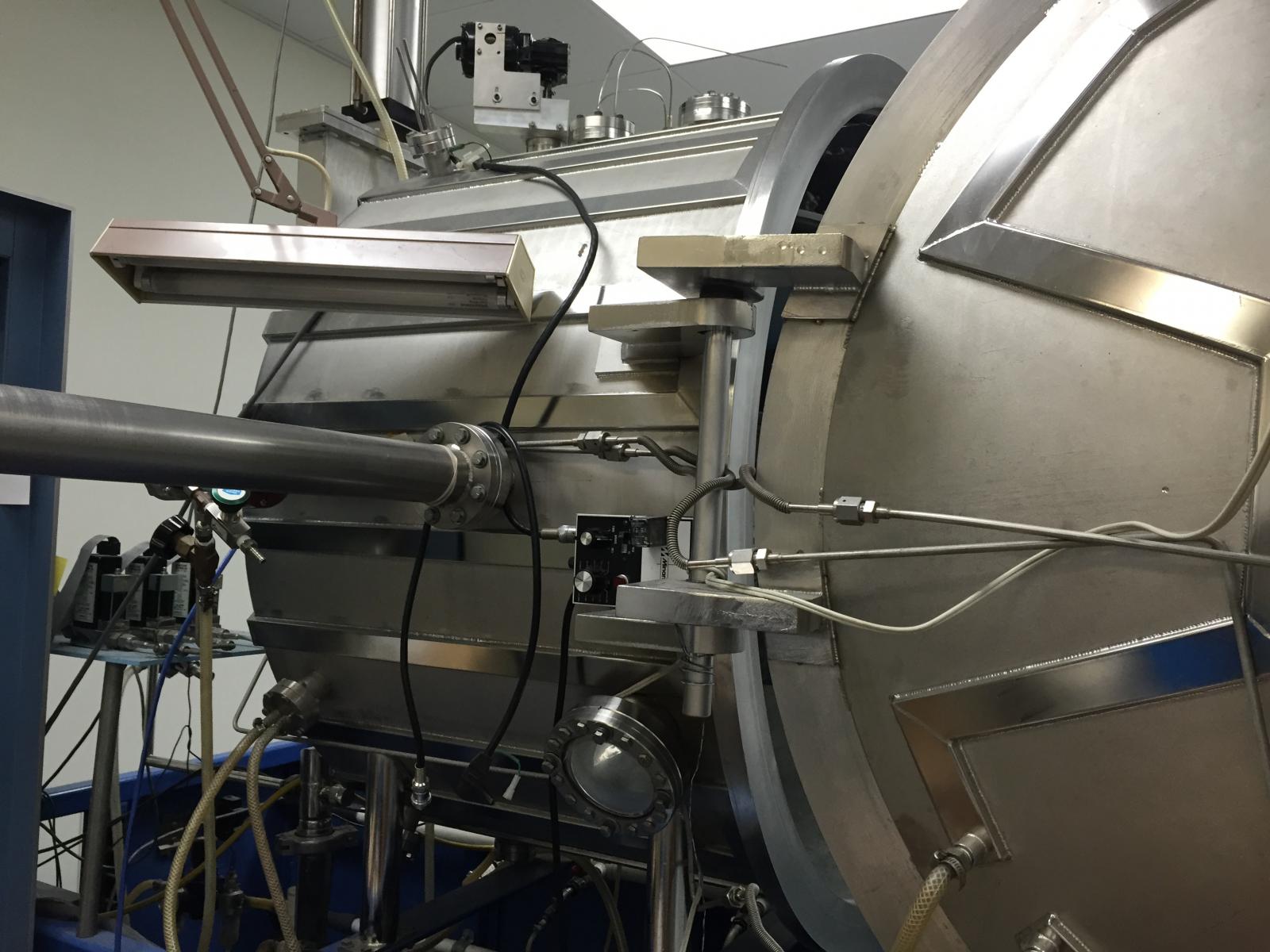

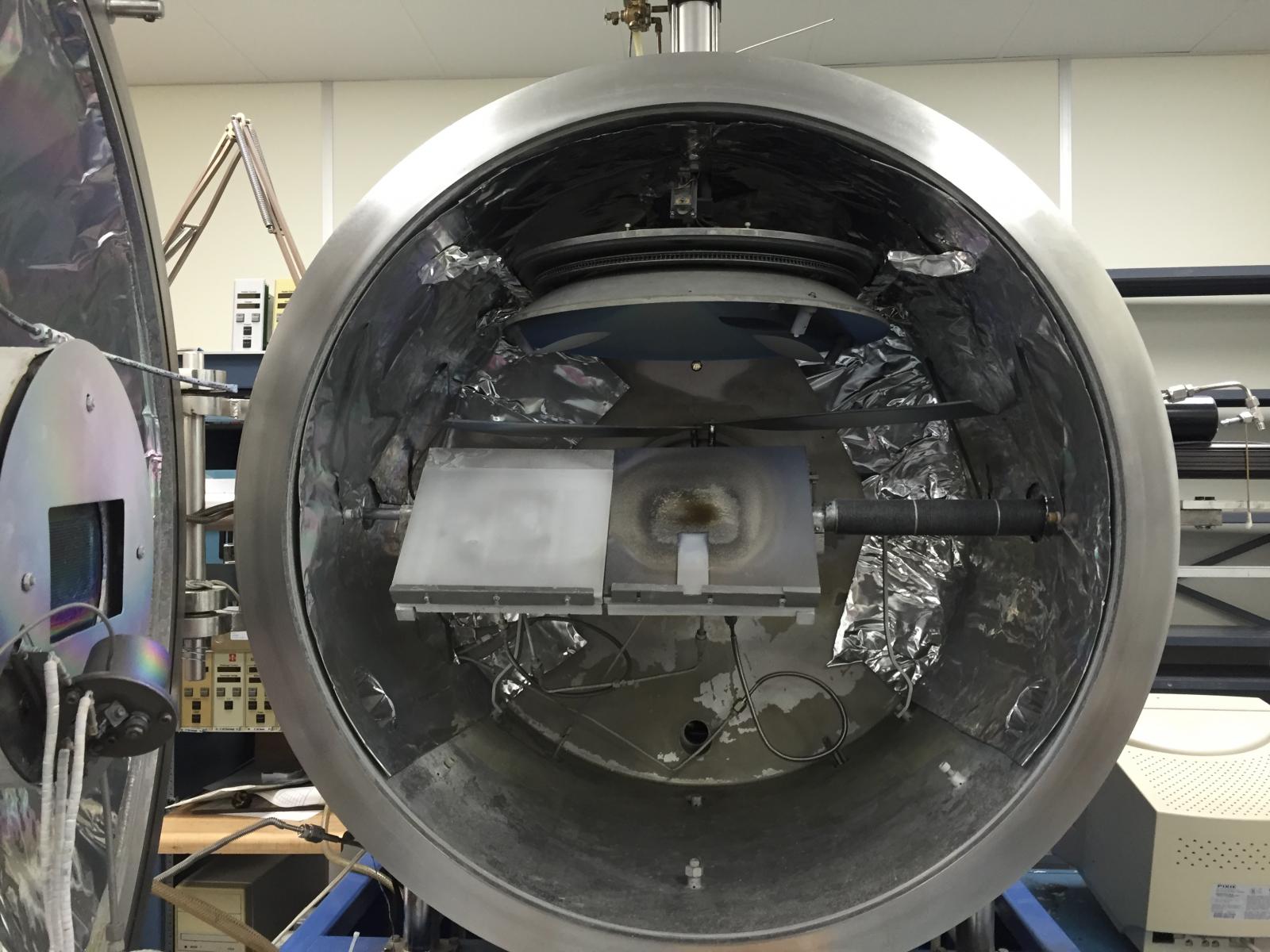

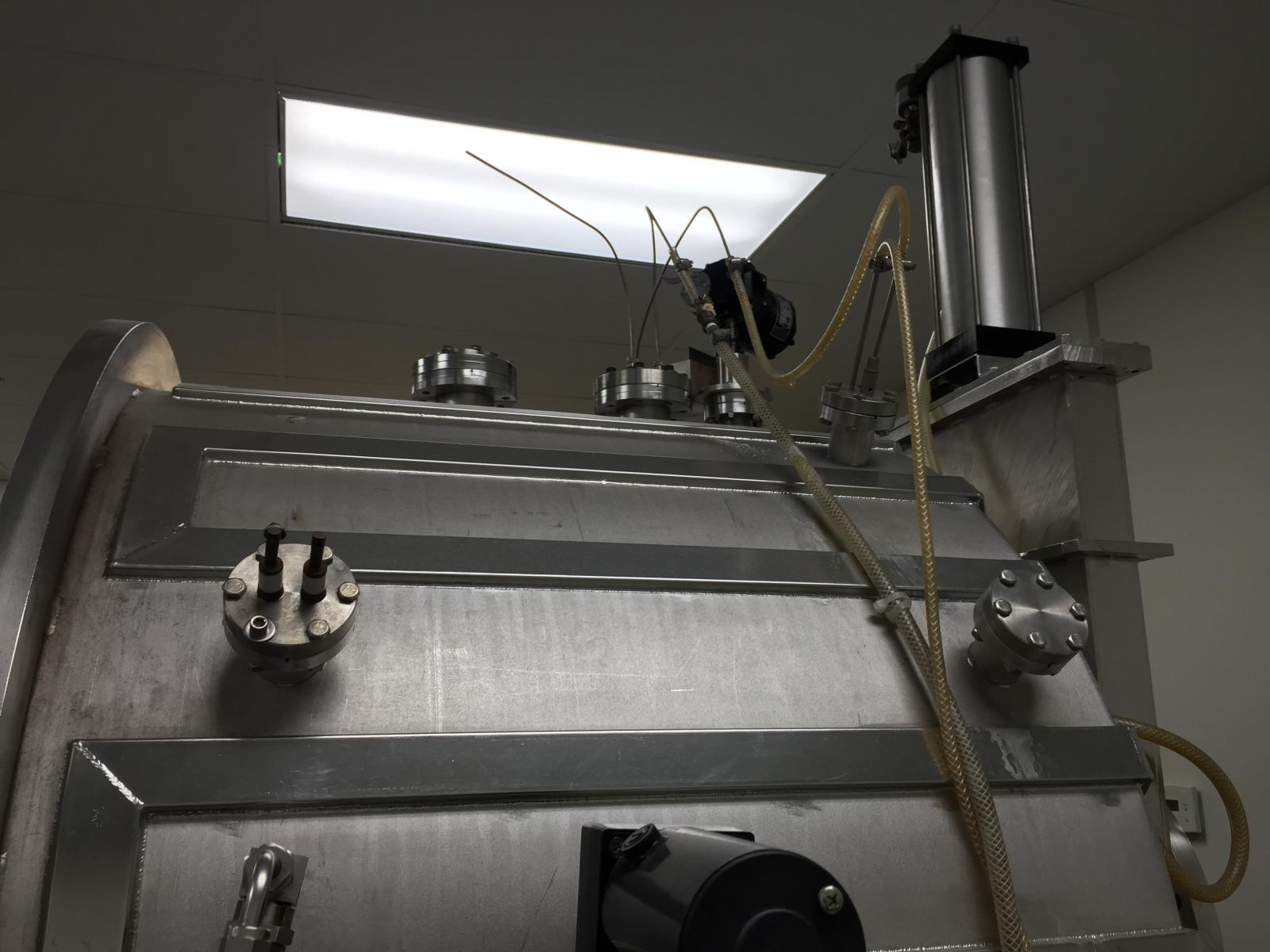

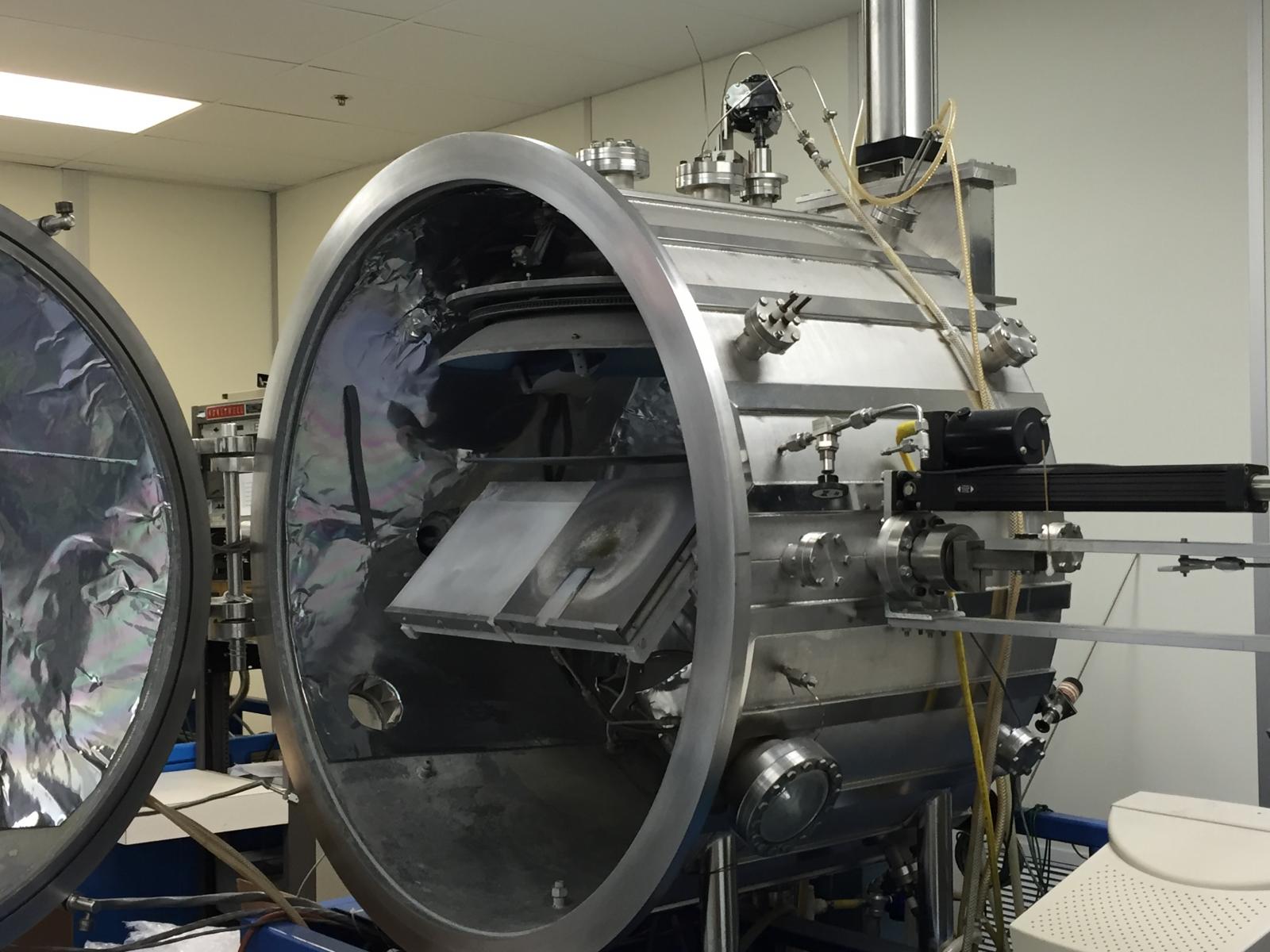

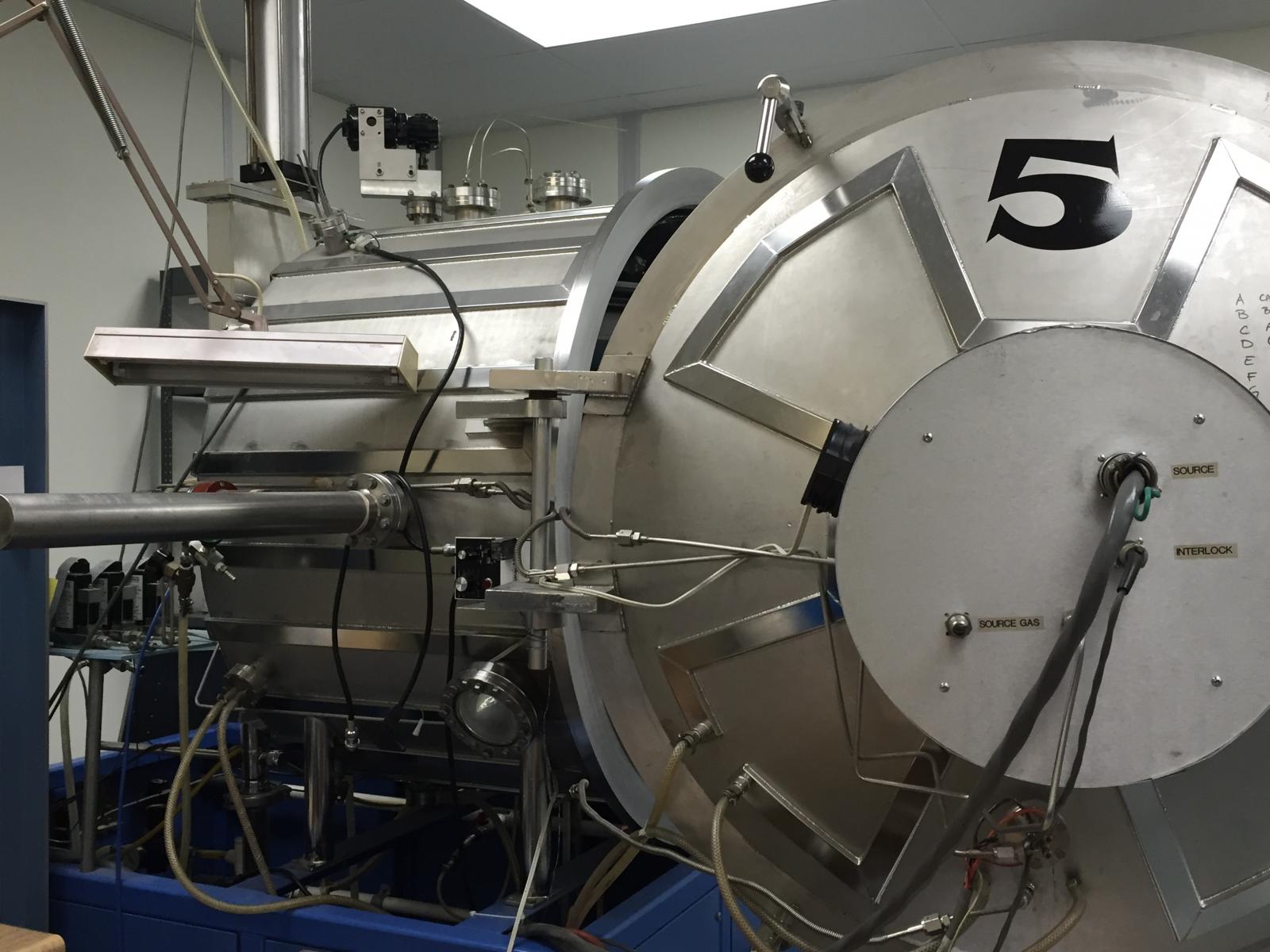

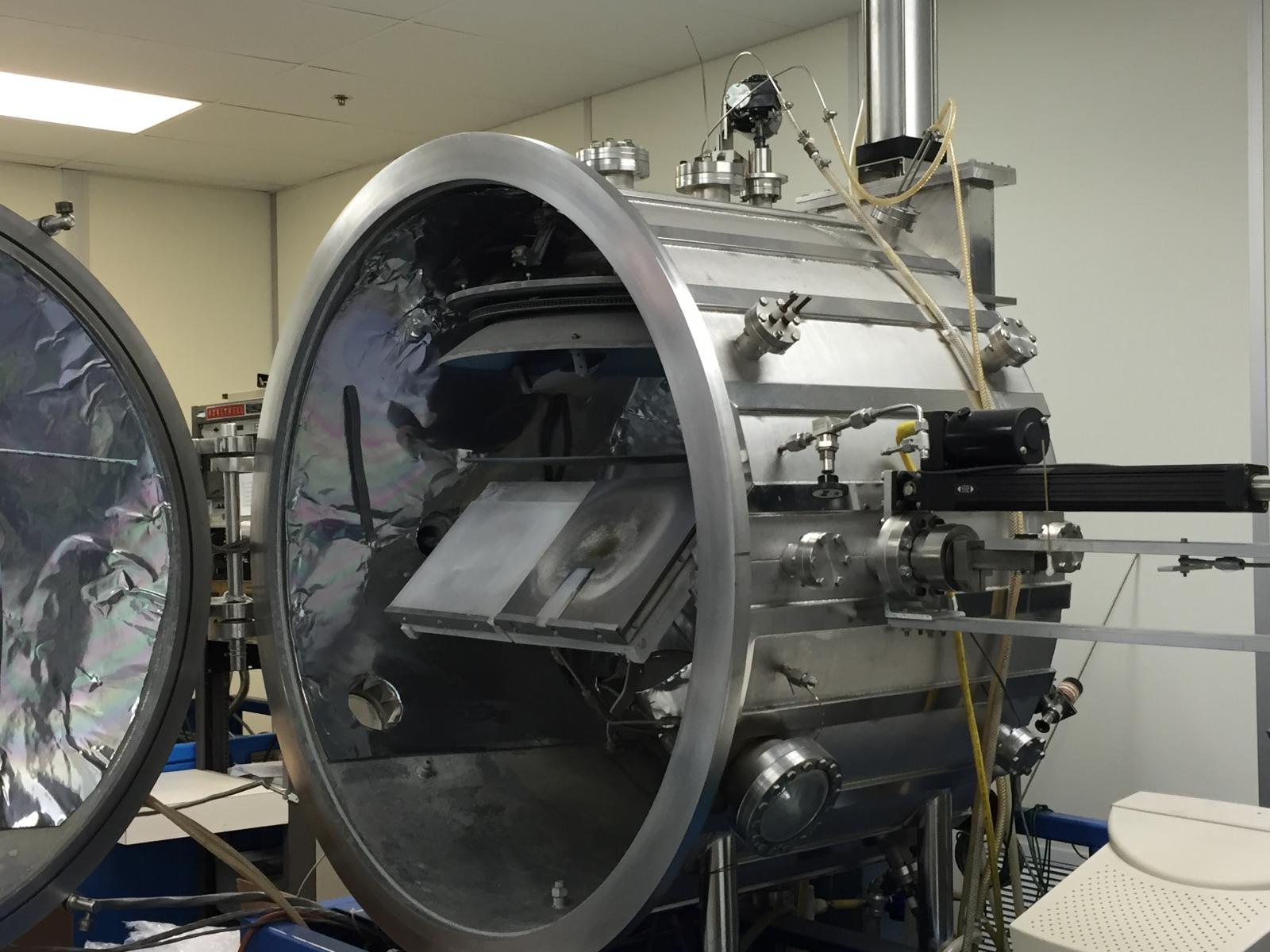

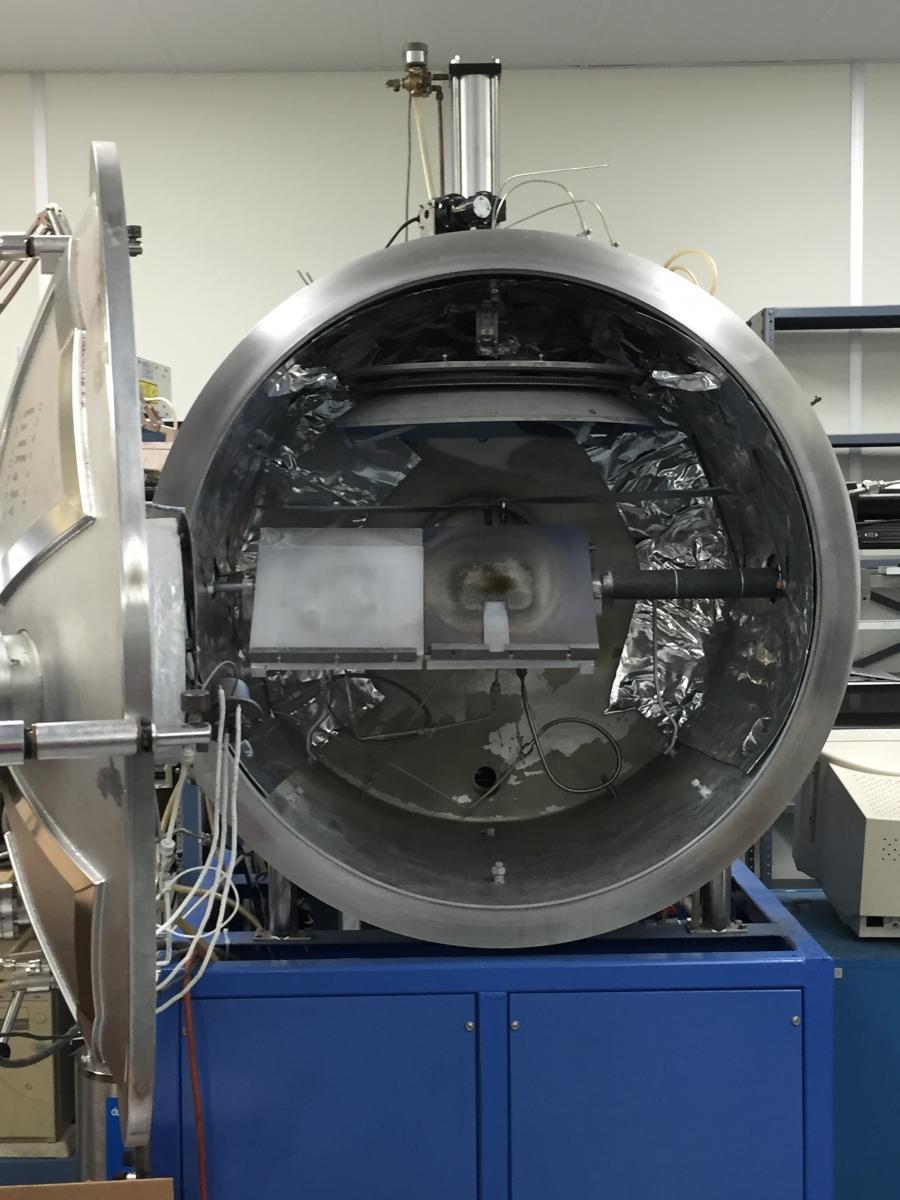

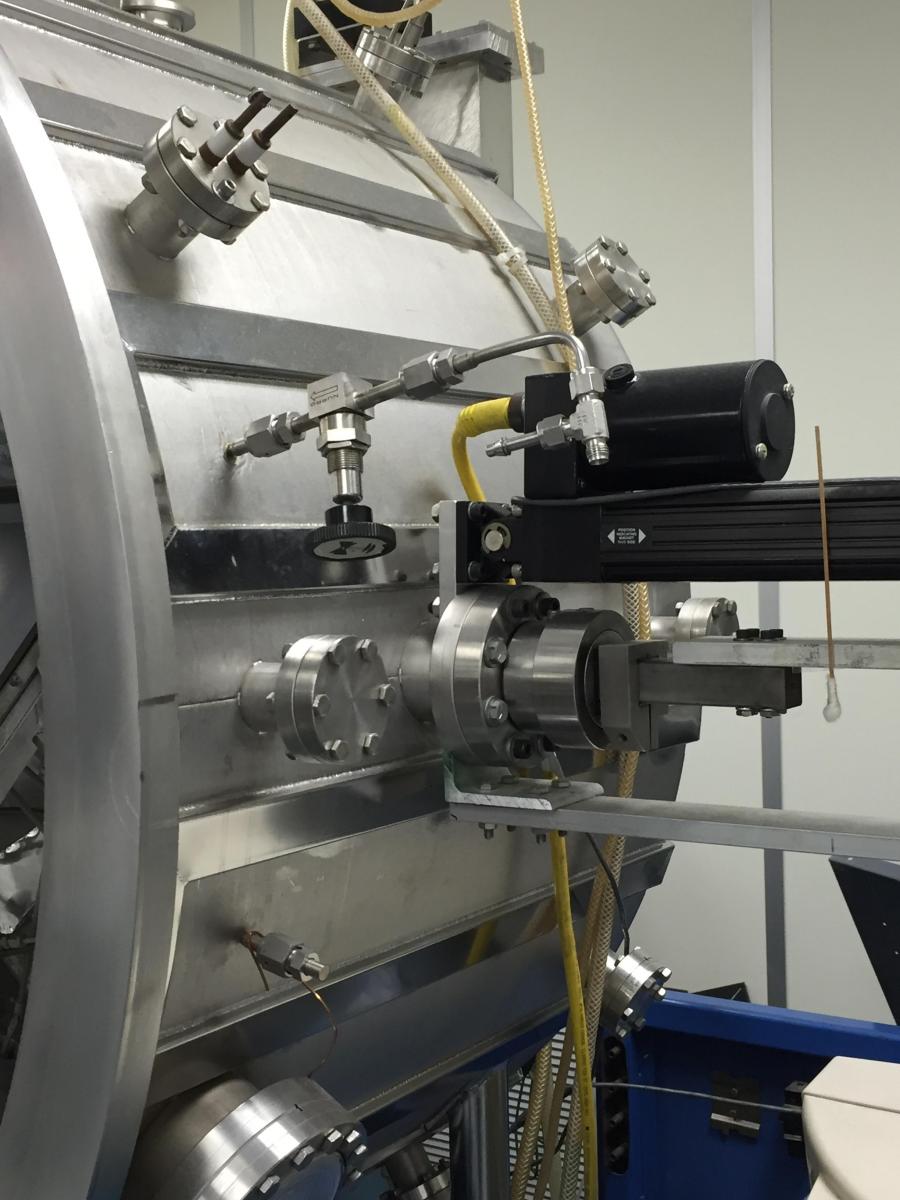

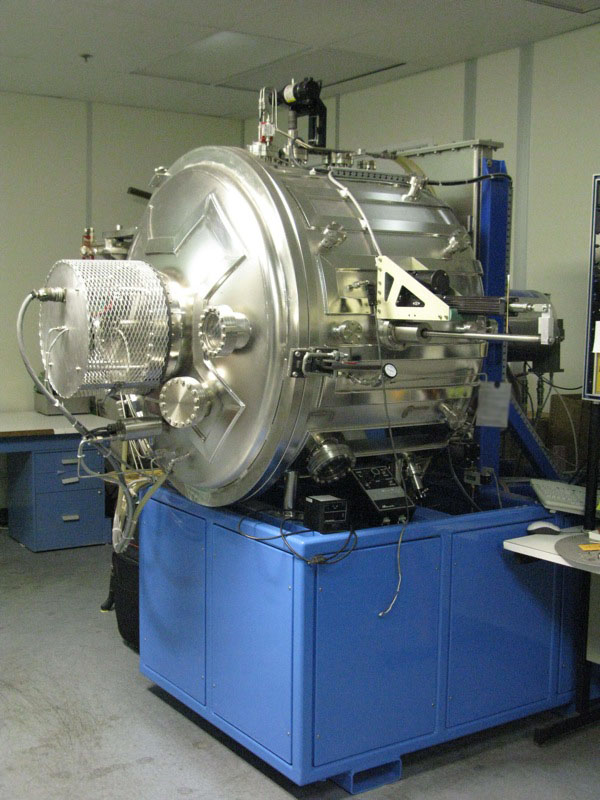

ID: 9140925
Vintage: 1987
System
Internal dimension: 41.5" x 27"
(1) Ion Tech MPS5001 power supply
(1) ION TECH 15cm ion beam gun
Substrate rotation system: Two sets at different coating distances. The upper is 3 planets of approximately 6.5" squares. The lower 3 planets of approximately 6" diameter.
(2) Crystal thickness monitors, one for each of the planetary tooling sets.
Sputtering Target: Max of 2 materials at a time, 10" x 10".
Materials previously used: TiO2, SiO2, HfO2, Si, Al203, B, Ta Cryopump and compressor have been removed. When unit was hooked up to pump and running, the pressure was 2x10-6 Torr and pump-down time was approximately 4 hours.
Valves and controls: Gas metering valves, mass flow controller.
Does not include: Cryopump and compressor or substrate heaters.
1987 vintage.
CUSTOM Ion Beam Deposition (Ion Milling) is a process where ions are deposited onto a substrate surface in a vacuum environment. The ions are generated from a beam of electrons that are accelerated toward a target material in the substrate. The ions then move across the substrate at speeds up to several hundred kilometers per second by the electric and magnetic fields present in the milling chamber. The milling process is highly controlled, allowing for a wide range of applications in the fabrication of nano-scale and/or ultra-thin films and materials. Ion beam deposition (IBD) is essentially a form of physical vapor deposition (PVD) where a beam of ions provided by the ion milling equipment deposits material on the substrate surface. This method of deposition is more precise, and allows for CUSTOM deposition of materials in one of two ways. The first is known as ion-assisted deposition, where the ions energize the target material during its deposition, allowing it to more easily adhere to the substrate. The second is known as ion-enhanced deposition, which increases the deposition rate due to the increased density of ions and increased diffusion of beam material to the substrate. IBD systems typically have a few common components to them, such as an ion source, substrates, a deposition chamber vacuum system, and a beam generation unit. The ion source is the device that produces the beam of ions. This is typically a high-voltage negative ion source. The substrates can be any number of materials, such as metals, semiconductors, glasses, and polymers. The substrates are inserted into the vacuum chamber, which is then pumped down to near vacuum levels to allow for a high degree of control over the deposition process. The beam generation machine is the device which accelerates the beam of ions towards the substrates. This tool typically uses electromagnetic fields and/or electrostatic focusing elements to control the beam dynamics. Once the ions reach the substrate, they become embedded and form a nano-composite material layer. The deposition process is a delicate one which closely monitored in terms of the exact parameters like pressure, current, and field intensities. The thickness of the deposited layer can be accurately controlled, as well as the number of layers and the deposition rate. CUSTOM ion beam deposition is a versatile tool for fabricating CUSTOM nano-scale materials, with the ability to create CUSTOM layers of almost any material. IBD can provide materials for applications such as MEMS, optical, and tribological components, as well as highly ordered arrays of molecules. This process is really just in its infancy as researchers continue to experiment and innovate with CUSTOM ion deposition.
There are no reviews yet