Used DMC SA/4m #143323 for sale
URL successfully copied!
Tap to zoom
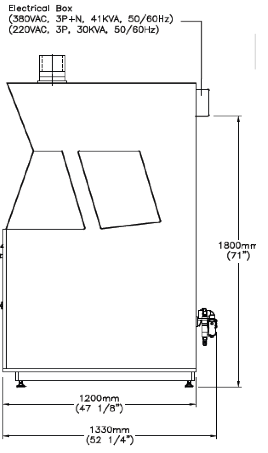

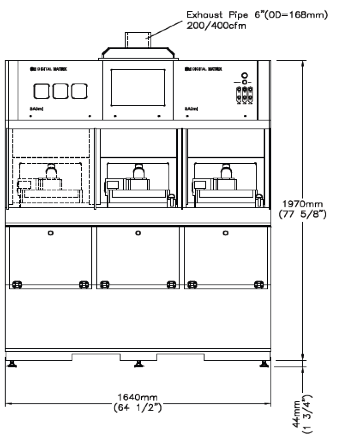

ID: 143323
Wafer Size: 8"
Vintage: 2006
Wafer-level Electro Plating system, 8"
Used for Stamper and micro pattern electro-plating
Can be implement as high uniformity
Using cathode head rotating system can produce high-quality products
This equipment can be applied to MEMS type and performed on the trench fill electroplating
Process automation can be set with Independent program for each cell
Various plating condition can be set with Independent program for each cell
DC, pulse, pulse- reverse current can be supplied in the resolution ±1 mA
Ni, Ni-CO, Cu Electroplating can be performed with this equipment
Total solution volume: 500 liters
Features:
Small Footprint
Independent Pump/Filtration for each cell
Patented adjustable cathode head and workholder for precise control of thickness variation
Front access for maintenance
Integrated all-in-one design, integrated sump & electronics
Enclosed work area for process control
Industrial PC control with large flat panel touch-screen display
Switch mode rectifiers
Easy operator interface
All digital Control system
(Qty 3) Cells:
Pump: 1 HP
Heater: 6 kW
Rectifier: Standard 65 Amps, 24VDC
Filtration: 2 Stage
Pre-filter: 5 micron DOE, 20"
Final-filter: 0.45 micron DOE, 20"
Flow: 50 liter max (Adjustable)
2006 vintage.
DMC SA/4m is a photoresist equipment manufactured by DuPont MicroCircuit Materials. This system uses a photosensitive polymeric layer over an organic base and is commonly used in the production of copper and aluminum substrates found in electrical circuit boards and other electronic applications. DMC SA/4m photoresist unit is composed of an organic film coated onto a flexible polyester substrate. This base layer provides rigidity and protection for the photosensitive polymeric layer on top. The polymeric layer includes resins, such as polyimide, polymethylmetacrylate, polyacrylate, polycarbonate and polystyrene, all of which can be coated on the base layer in various thicknesses to accommodate different substrate configurations. The photoresist is activated with light which causes a photochemical reaction wherein certain areas are exposed while others are protected. The protected areas remain in their original form while the exposed areas undergo a chemical change to become either soluble or insoluble depending on the composition of the polymeric layer. The soluble polymers are etched off in the wash-off process and then the remaining, insoluble areas are chemical milled away. This process removes the unwanted material and creates the desired shapes for the product. DMC SA/4m photoresist machine is typically applied in a wet lamination process involving a uniform film thickness followed by thorough drying and chemical pre-treatment. Once the film has been applied, it can be exposed with a light source and developed, prior to chemical etching. After the development process, quality control can be performed to ensure that the desired configuration has been achieved. This process involves examination of the film pattern through optical or x-ray microscopy, as well as secondary tests to measure the accuracy and integrity of the development process. In conclusion, DMC SA/4m photoresist tool is an advanced asset that is used in the fabrication of circuit boards and other electronic products. Its ability to accurately expose and develop photoresist films provides the necessary design accuracy for creating quality products. The model is composed of a flexible base layer, a photosensitive polymeric layer, and a photolithographic process involving various pre-treatments and processes including light exposure, development and chemical etching. Quality control processes are used to verify that the patterned film meets specifications throughout the process.
There are no reviews yet