Used TEL / TOKYO ELECTRON Clean Track ACT 12 #293604842 for sale
It looks like this item has already been sold. Check similar products below or contact us and our experienced team will find it for you.
Tap to zoom
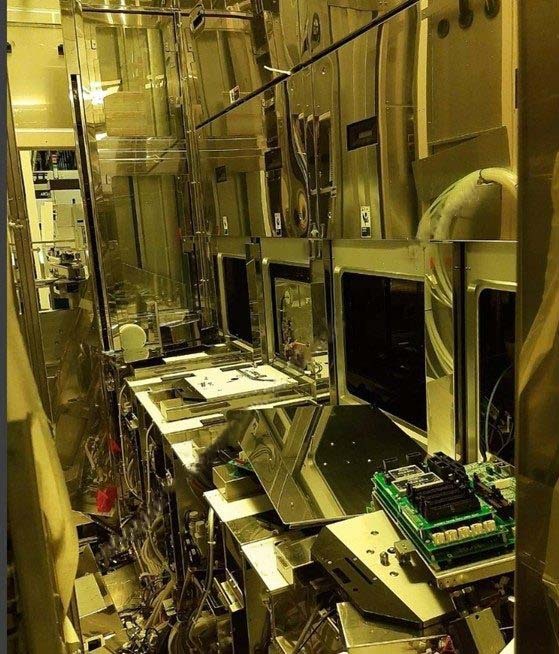

Sold
ID: 293604842
Wafer Size: 12"
Vintage: 2008
Coater / Developer system, 12"
AC Power box
AC Power cable: 3 Phase
SHINWA T & H
Chemical cabinet: COT + DEV
(4) Coater units
(4) Develop units
(12) LHP Units
(2) HHP Units
(9) PHP Units
(9) CPL Units
(3) ADH Units
WEE Unit
(5) PEB Units
IRA Block
CSB
TCU
Coater unit:
Unit 1:
HPT Resist pump
EBR / RRC / BSR: EBR + RRC + Back rinse
Temperature / Humidity sensor
Photo resist temperature controller
Motor flange temperature controller
Unit 2:
(5) Resist nozzles
Resist pump: HPT
EBR / RRC / BSR: EBR + RRC + Back rinse
Temp / Humidity sensor
PR Auto exchange system
Photo resist temperature controller
Motor flange temperature controller
FOC Center photo resist drain
Unit 3:
(5) Resist nozzles
Resist pump: HPT
EBR / RRC / BSR: EBR + RRC + Back rinse
Temp / Humidity sensor
PR Auto exchange system
Photo resist temperature controller
Motor flange temperature controller
FOC Center photo resist drain
Unit 4:
(5) Resist nozzles
HPT Resist pump
EBR / RRC / BSR: EBR + RRC + Back rinse
Temperature / Humidity sensor
PR Auto exchange system
Photo resist temperature controller
Motor flange temperature controller
FOC center photo resist drain
Develop unit:
Unit 1:
Spray H develop nozzle
Rinse left to right develop nozzle move
Developer temperature control
Auto damper
Auto dummy rinse
Cup type: STD DEV
Unit 2:
Spray H nozzle develop nozzle
Left to right develop nozzle
(2) Top rinses
Developer temperature control
Auto damper
Cup type: STD DEV
Unit 3:
Spray H nozzle develop nozzle
Left to right develop nozzle
(2) Top rinses
Developer temperature control
Auto damper
Auto dummy rinse
Cup type: STD DEV
Unit 4:
Spray H develop nozzle type
Left to right develop nozzle move type
(2) Top rinses
Developer temperature control
Auto damper
Auto dummy rainse
Cup type: STD DEV
Hard Disk Drive (HDD) not included
2008 vintage.
TEL / TOKYO ELECTRON Clean Track ACT 12 is a photoresist stripping equipment utilizing ultra high pressure clean technology. This system enables the removal of photoresist without damaging the substrate and without creating particulates. The Clean Track unit is able to remove photoresist from the substrate with minimal damage due to its ultra high pressure clean technology. This ensures that the substrate is not compromised by the cleaning process. In addition to its ultra high pressure clean technology, the machine utilizes a number of cleaning mechanisms to clean the photoresist from the substrate. These include a powerful CO2 laser, a nebulizer for chemical removal, a wafer cleaner for particle removal, and an agitation station for mechanical action. The CO2 laser is able to selectively cut out and remove photoresist from the substrate without causing damage to the underlying layer. The nebulizer is used to add an appropriate chemical solution to the substrate to dissolve the photoresist and ensure that it is completely removed. The wafer cleaner is designed to remove any particles left on the substrate by the cleaning process. Finally, the agitation station allows for mechanical action to further facilitate the cleaning process. The Clean Track tool is also engineered to provide automation, allowing for efficient and consistent results. An integrated control asset and automated wafer handling ensures that the cleaning process is performed quickly and accurately. Additionally, vacuum pump technology offers high air removal capacity and rapid drying times, ensuring that photoresist is completely removed from the surface of the substrate. TEL Clean Track ACT 12 model is a reliable and efficient photoresist stripping equipment. Its combination of ultra high pressure clean technology and other cleaning mechanisms provides a clean, accurate, and consistent system for the removal of photoresist from substrates. By providing automated, consistent results, the Clean Track unit can help improve the efficiency of photolithography processes and enable manufacturers to produce higher quality substrates.
There are no reviews yet