Used TEL / TOKYO ELECTRON Clean Track ACT 12 #9278612 for sale
It looks like this item has already been sold. Check similar products below or contact us and our experienced team will find it for you.
Tap to zoom
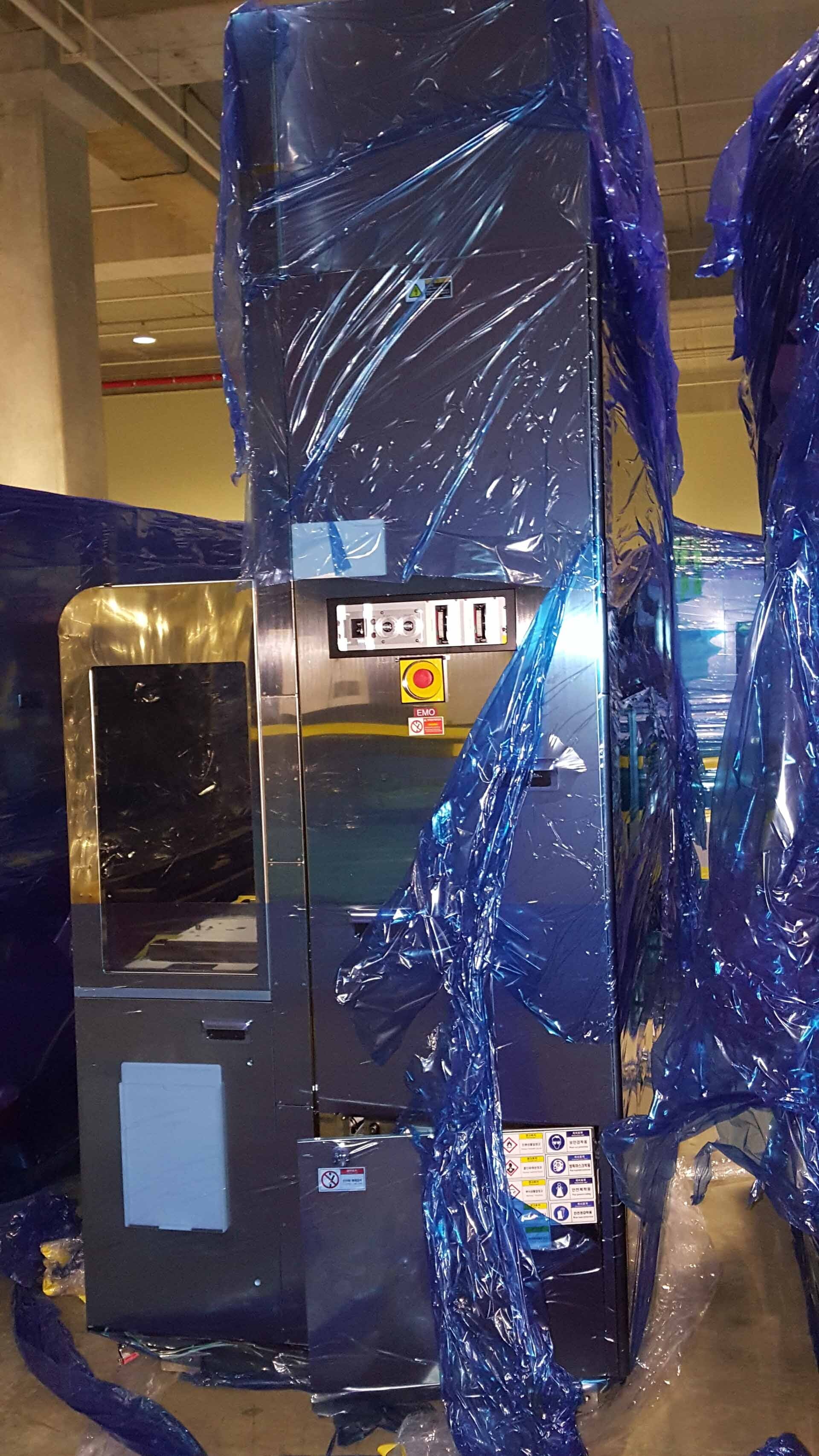

Sold
ID: 9278612
(4) Coater / (4) Developer system, 12"
Right to left
Carrier type: Notch
25-Slots
(3) Main controllers
(2) Processor blocks
(2) PRB's
(2) Thermo controllers
NIKON Stepper
H-Type nozzle
CSB
IFB
Main system:
Main frame with system controller
(4) ASYST RFID FOUP Systems
Normal cassette type
Coater unit (2-1, 2-2, 2-3, 2-4):
(4) Dispense nozzles with temperature control lines
RDS pump
Rinse nozzle: EBR / Back rinse / Solvent bath
(2) Rinse systems: (2) Buffer tank systems (3 Liters)
Degas system
Programmable side rinse
Direct drain type
Developer unit (3-1, 3-2, 3-3, 3-4) NDP type:
NLD Nozzle
Stream nozzles for DI rinse
2-Points for back side rinse
(2) Developer systems: (2) Buffer tank systems (3 Liters)
Degas system
Developer temperature control system
Direct drain type
(2) Adhesion units:
100% Sealing closed chamber (Built-in hot plate)
HMDS Tank with float sensor
Local HMDS supply
(12) Low Temperature Hot Plates (LHP)
(2) Cup Washer Holders (CWH)
(13) High-Speed Cill Plates (HCP)
(6) High-Precision Hot Plates (PHP)
Transition Chill Plate (TCP)
(2) Transition Stages (TRS)
(2) Wafer Edge Exposures (WEE)
Chemical cabinet 1: HNDS and Solvent supply system
Chemical cabinet 2: DEV Solution and DIW supply system
(2) Temperature Control Units (TCU)
MFC
Missing parts:
IRA Z-Axis driver
IRA Y-Axis driver
IRA TH-Axis driver
Temperature and humanity controller
Hard Disk Drive (HDD)
Power supply: AC 200/220 VAC, 3 Phase
2004 vintage.
TEL / TOKYO ELECTRON Clean Track ACT 12 is a photoresist processing equipment developed by TEL (TOKYO ELECTRON). It supports both lithographic processes and post-processing steps involved in the manufacture of semiconductor devices. The system combines a laser scanner, liquid immersion unit and automatic dispense and aligner, making it a versatile tool for photoresist processing. The laser scanner is used to expose the photoresist layer on a silicon wafer using ultra-short laser pulse-widths. The laser pulse is finely tuned to reflect the photoresist layer for exacting feature patterns. The liquid immersion machine ensures uniform photoresist coating by taking advantage of the natural buoyancy of the liquid dispensed within the processing chamber. The dispense and aligner allows precise application of additional resist layers as needed. TEL Clean Track ACT 12 allows different exposure and resist processing parameters which can be adjusted to vary the desired feature patterning. It provides a choice of both high density feature patterning or line width control for etch processes. This provides the user with the versatility to tailor the processing to specific design requirements. The tool has built in safety features. The in-line camera sensors in the laser scanner ensure that the wafer is correctly positioned and that there are no contaminations present. Additionally, the immersion asset provides an effective means to reduce photoresist contamination, so that the users do not need to worry about contamination of the wafer or processing chamber. Built for accomodating 300 mm wafer processing, TOKYO ELECTRON Clean Track ACT 12 offers improved throughputs over its predecessors. The model uses low cost consumables, and is extremely efficient in the use of energy, enabling users to reduce their production costs while also reducing their environmental footprint. Overall, Clean Track ACT 12 is a state-of-the-art photoresist processing equipment designed to meet modern semiconductor device demands. Its laser scanning, liquid immersion and aligner technology enables rapid turnaround for production, while its built-in safety features ensure the highest levels of process control are maintained. The system's low cost and energy efficient design make it a valuable cost-effective tool for any semiconductor production process.
There are no reviews yet