Used AMAT / APPLIED MATERIALS P5000 Mark II #9389403 for sale
URL successfully copied!
Tap to zoom
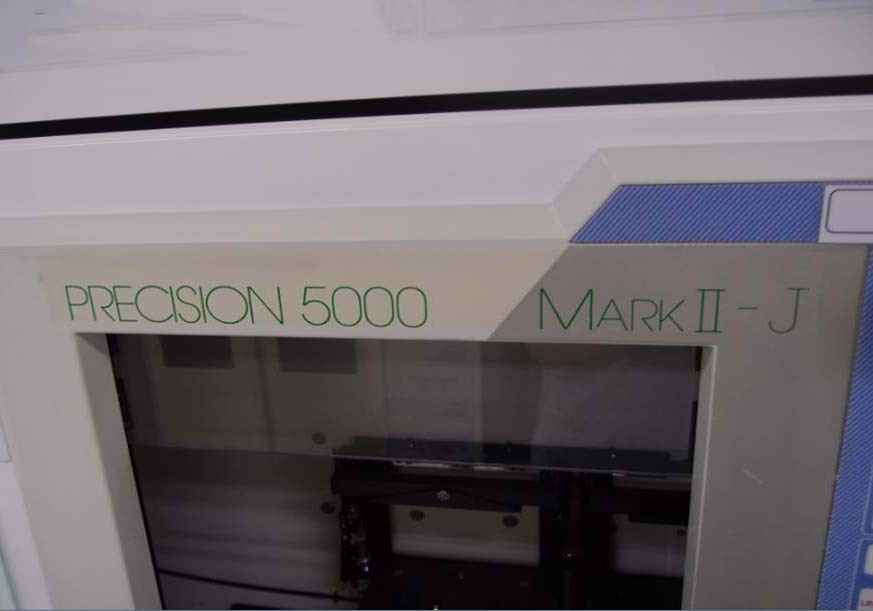

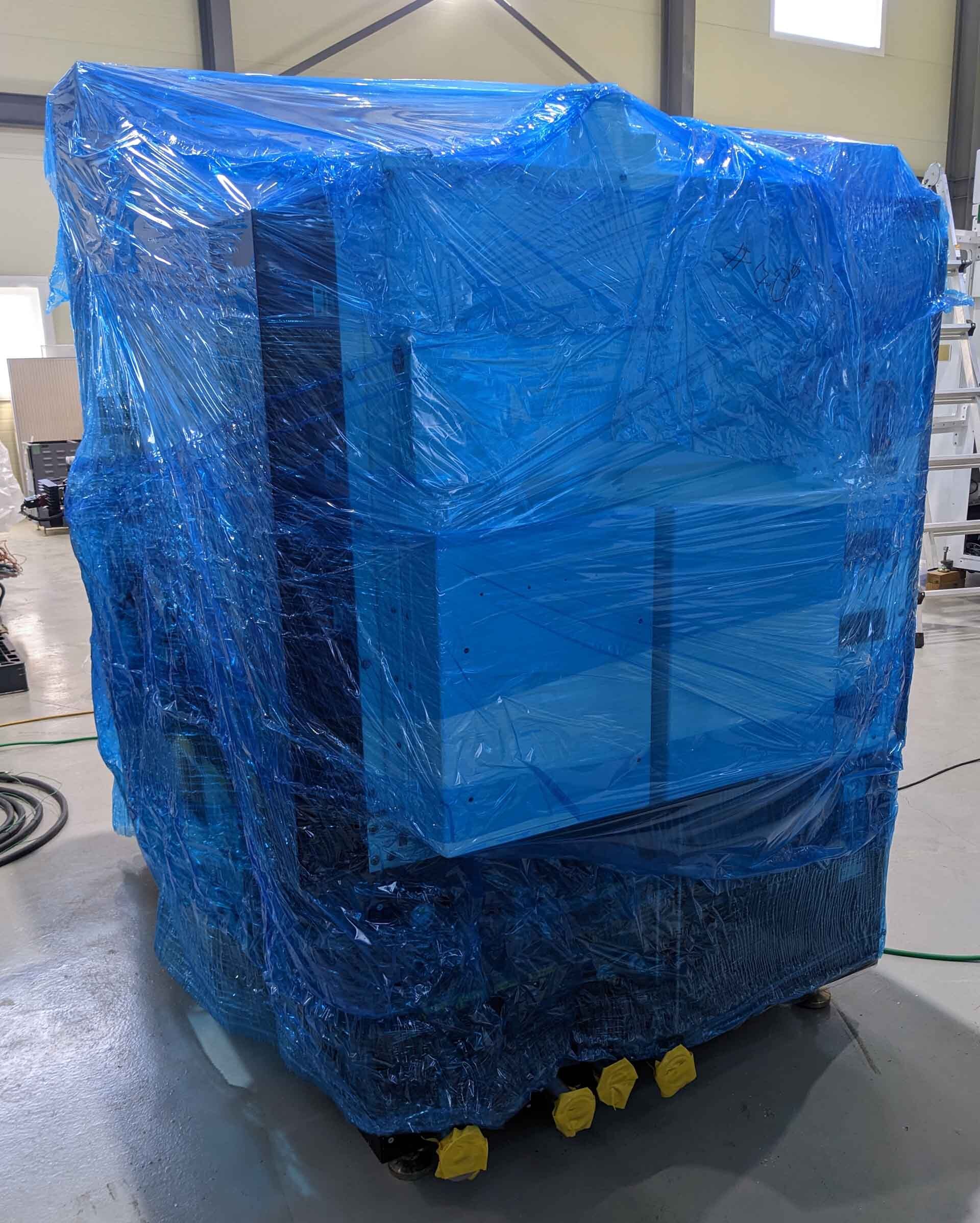

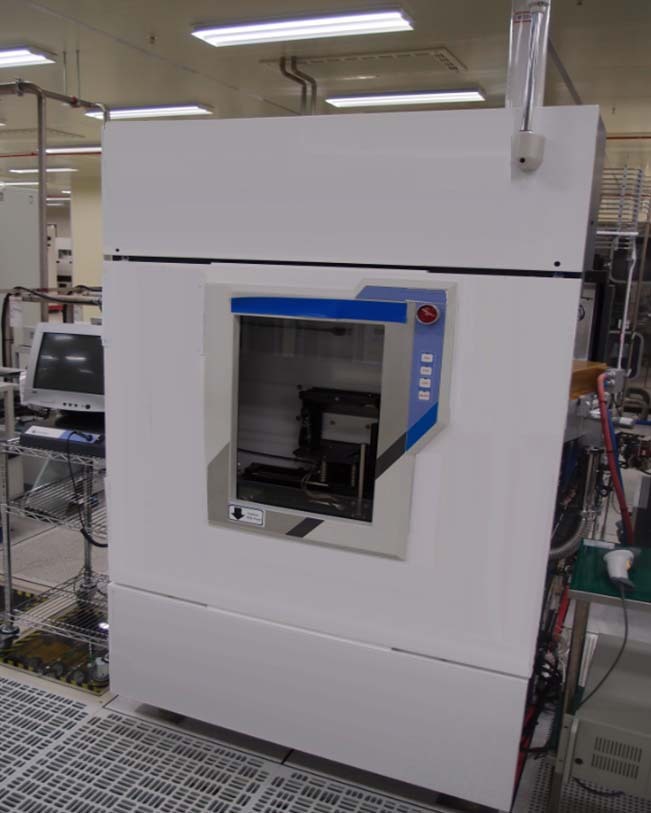

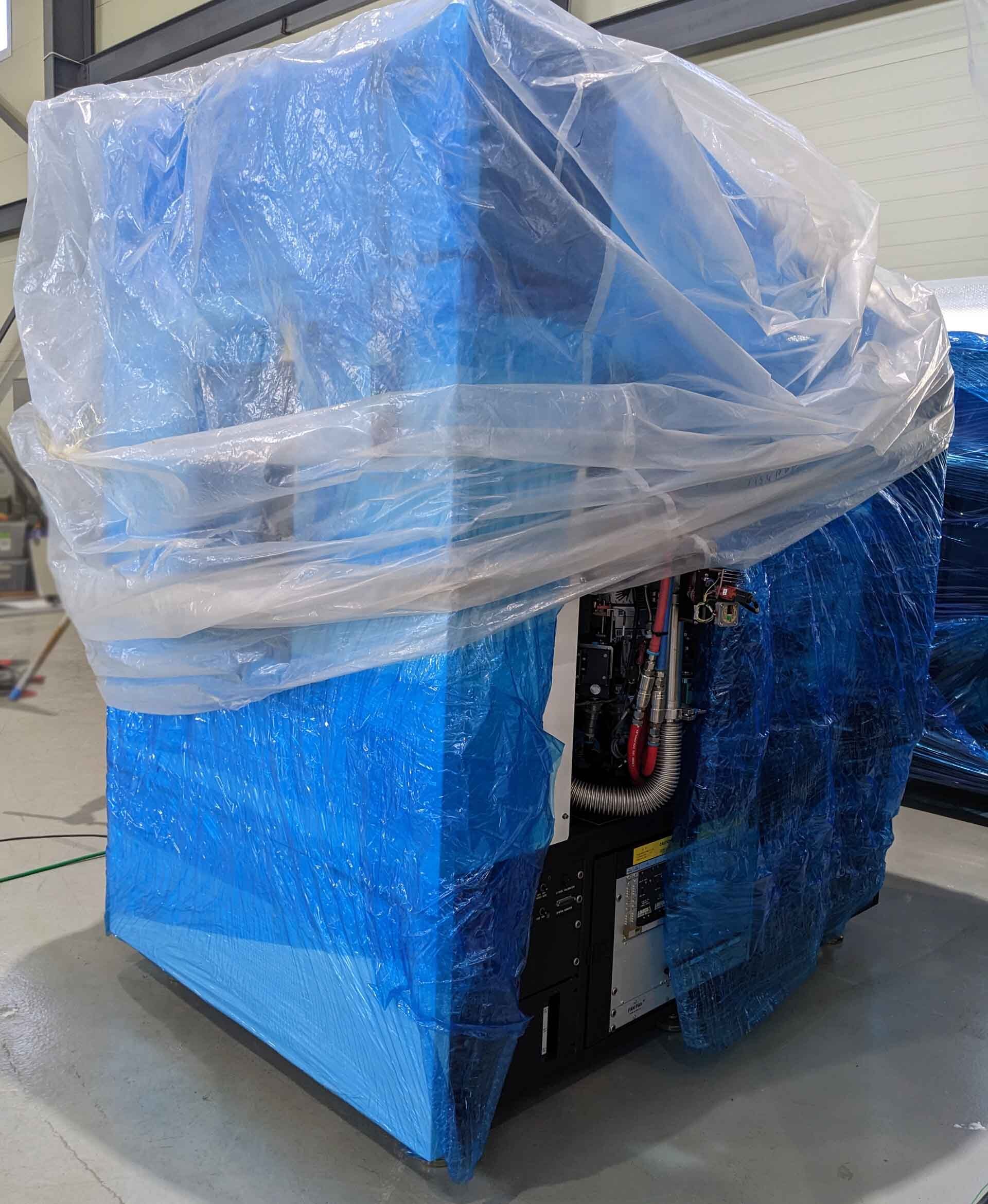

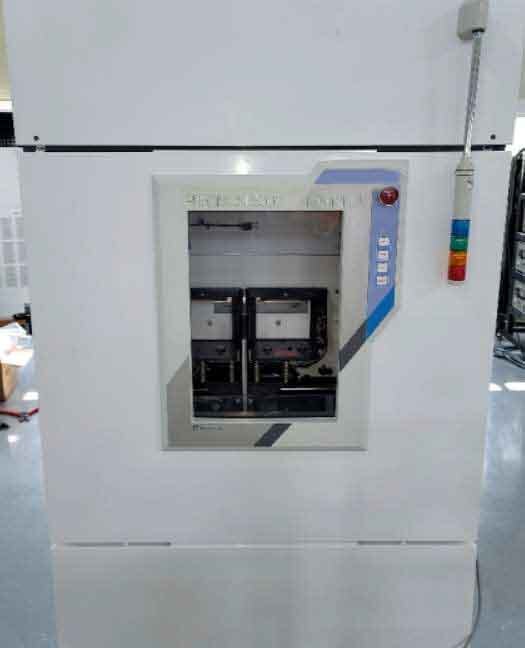

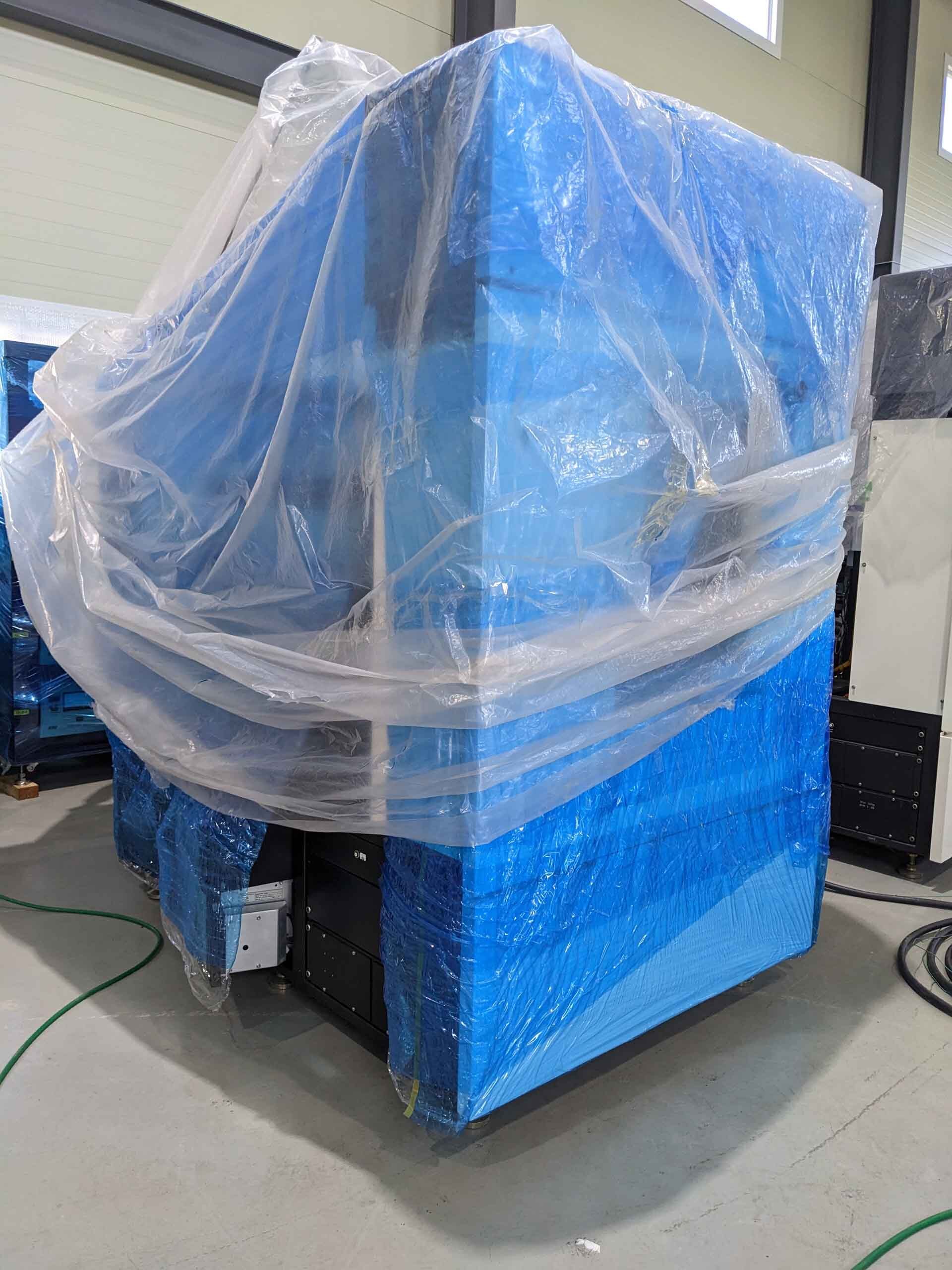

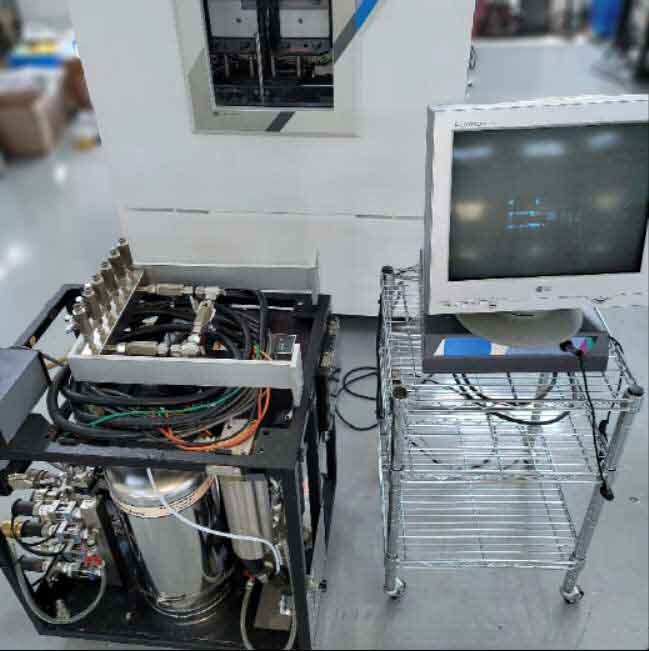

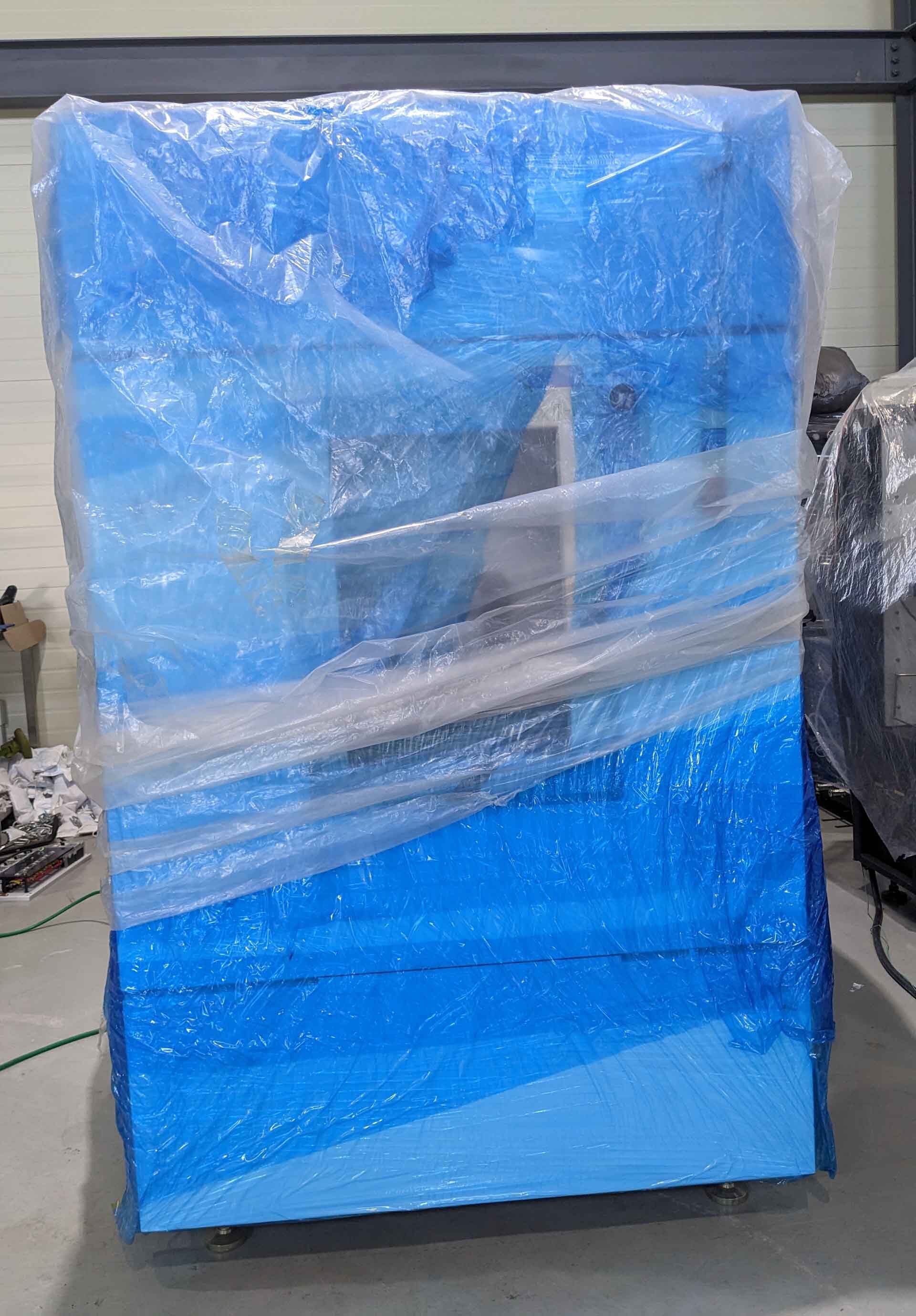

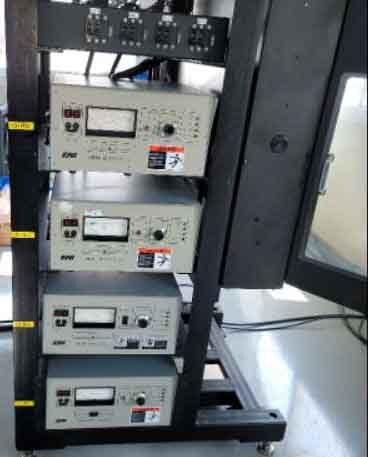

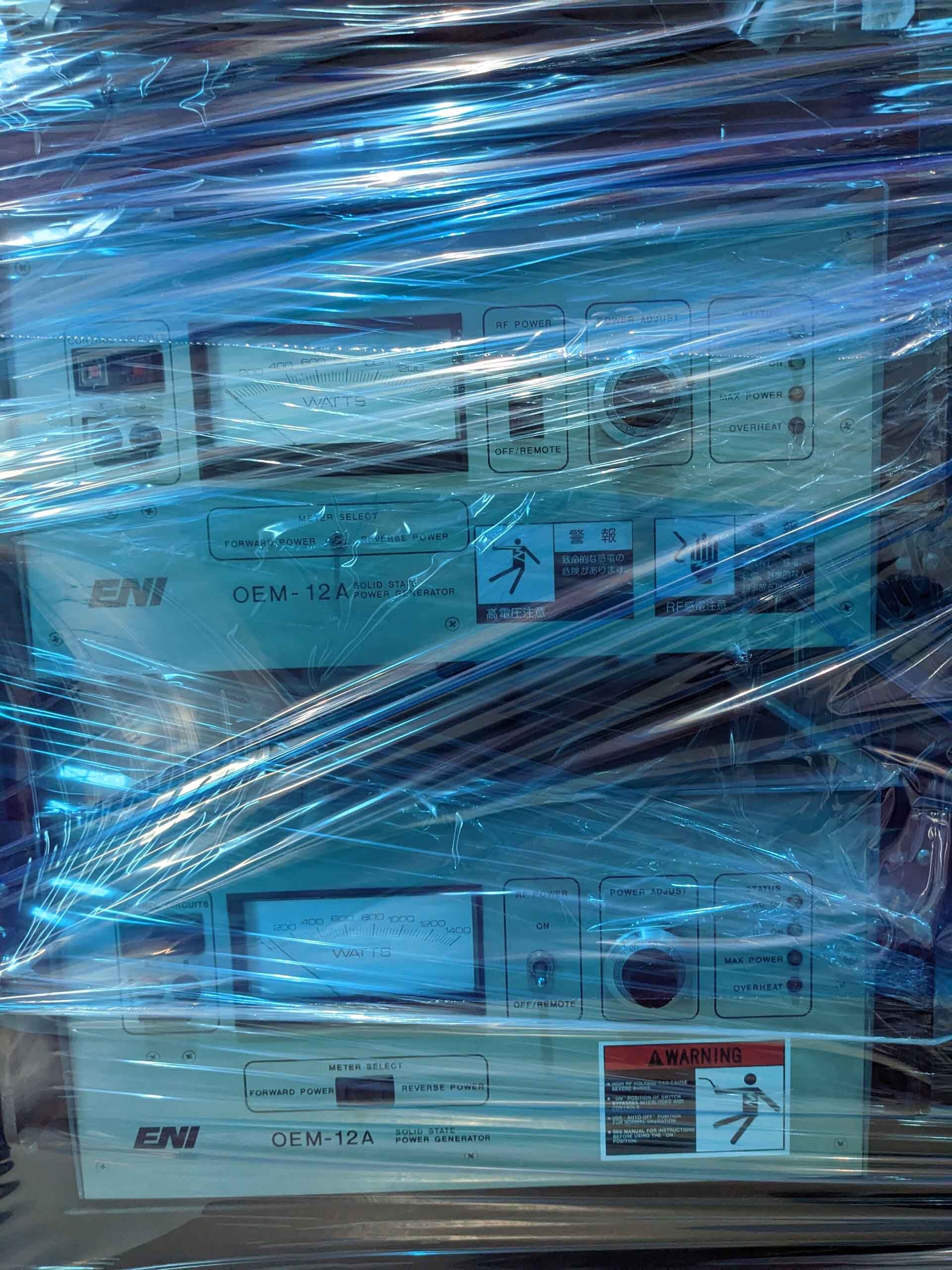

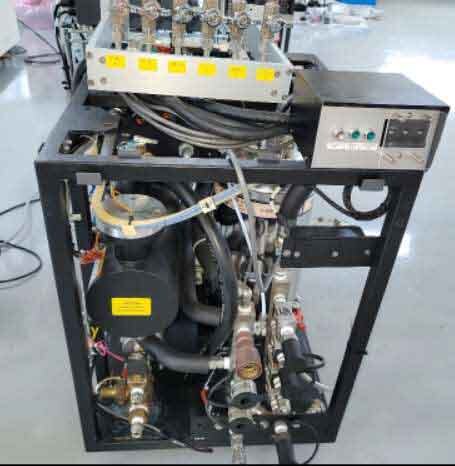

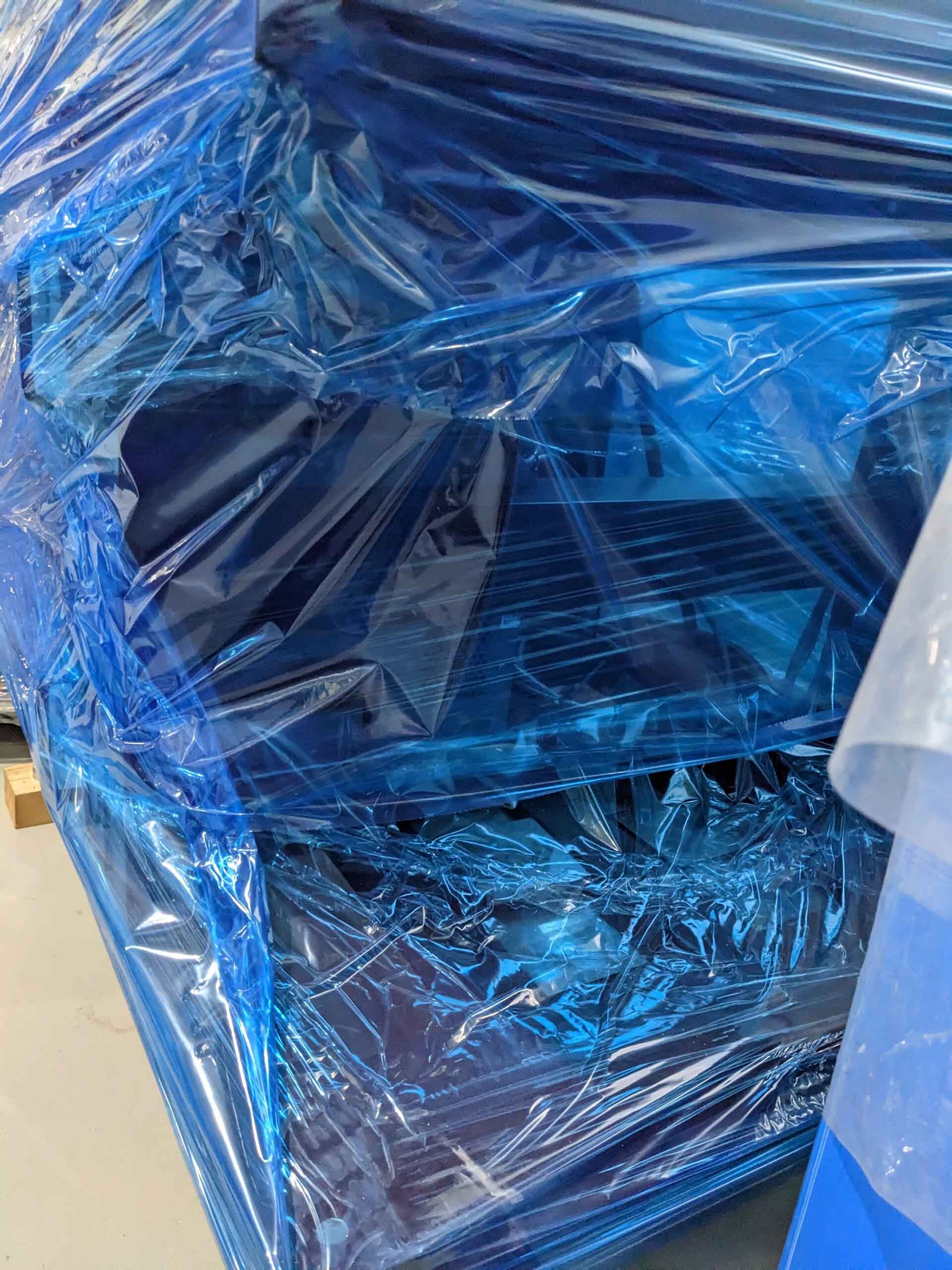

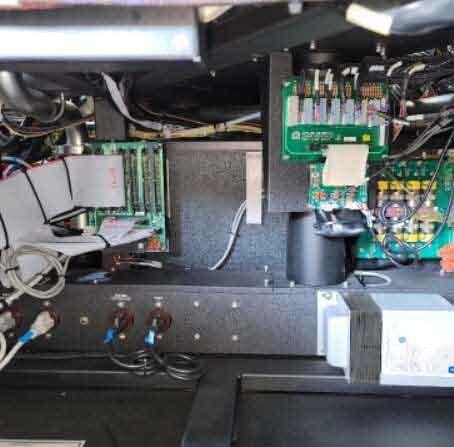

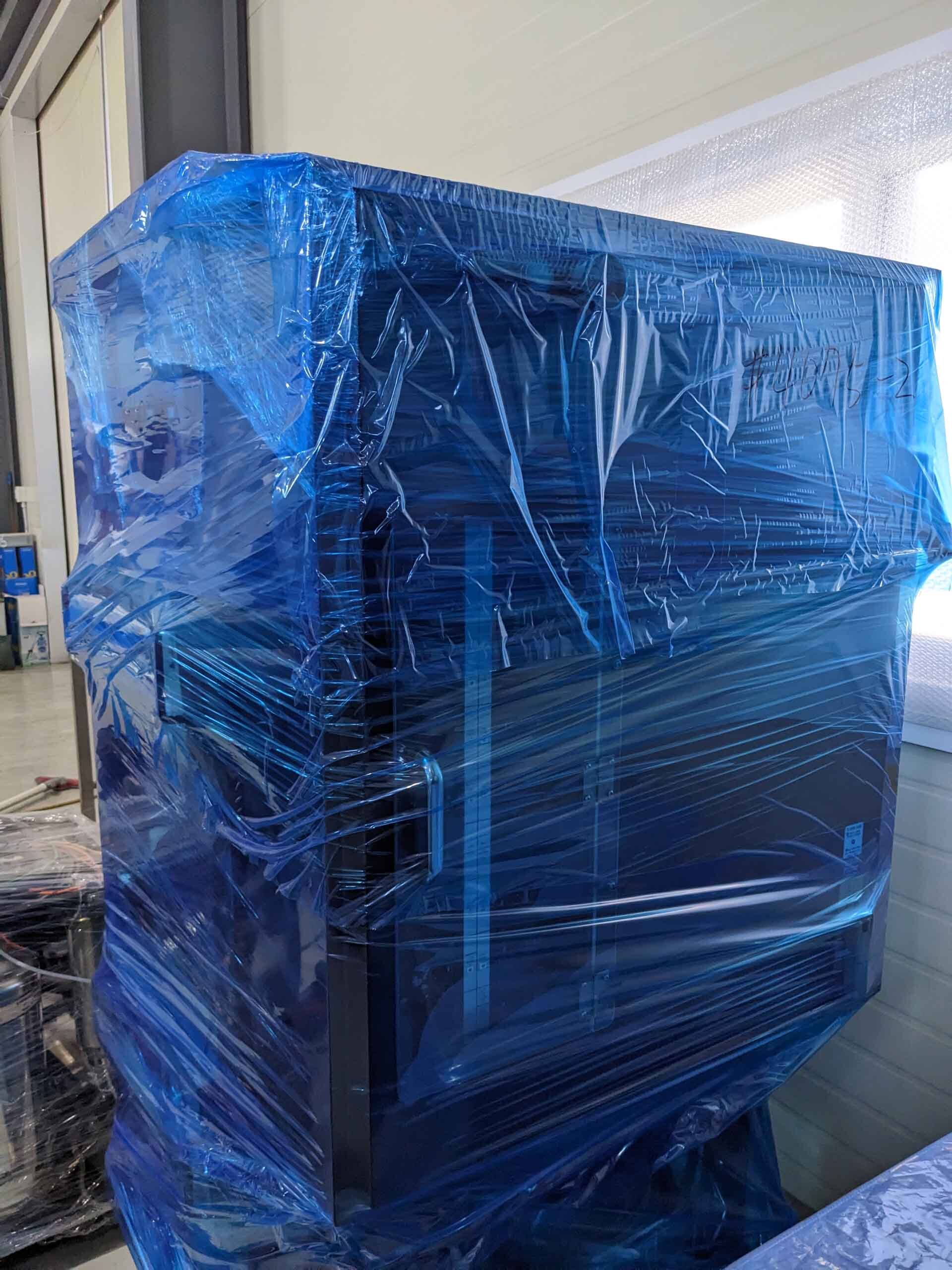

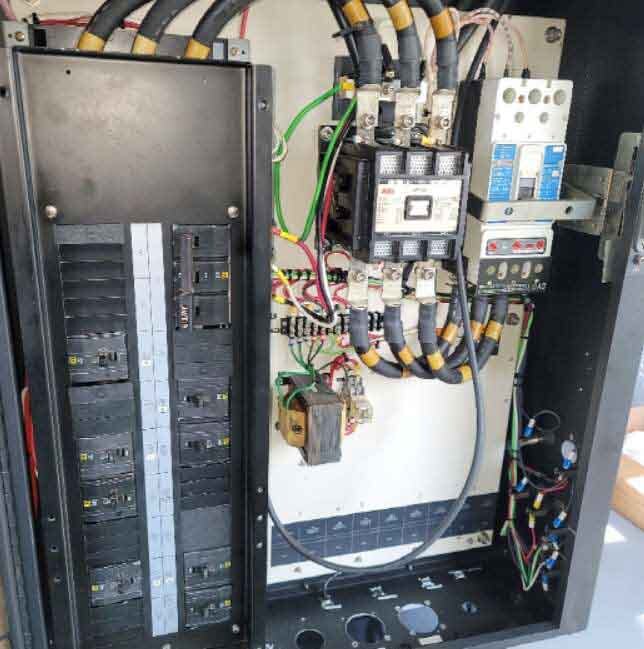

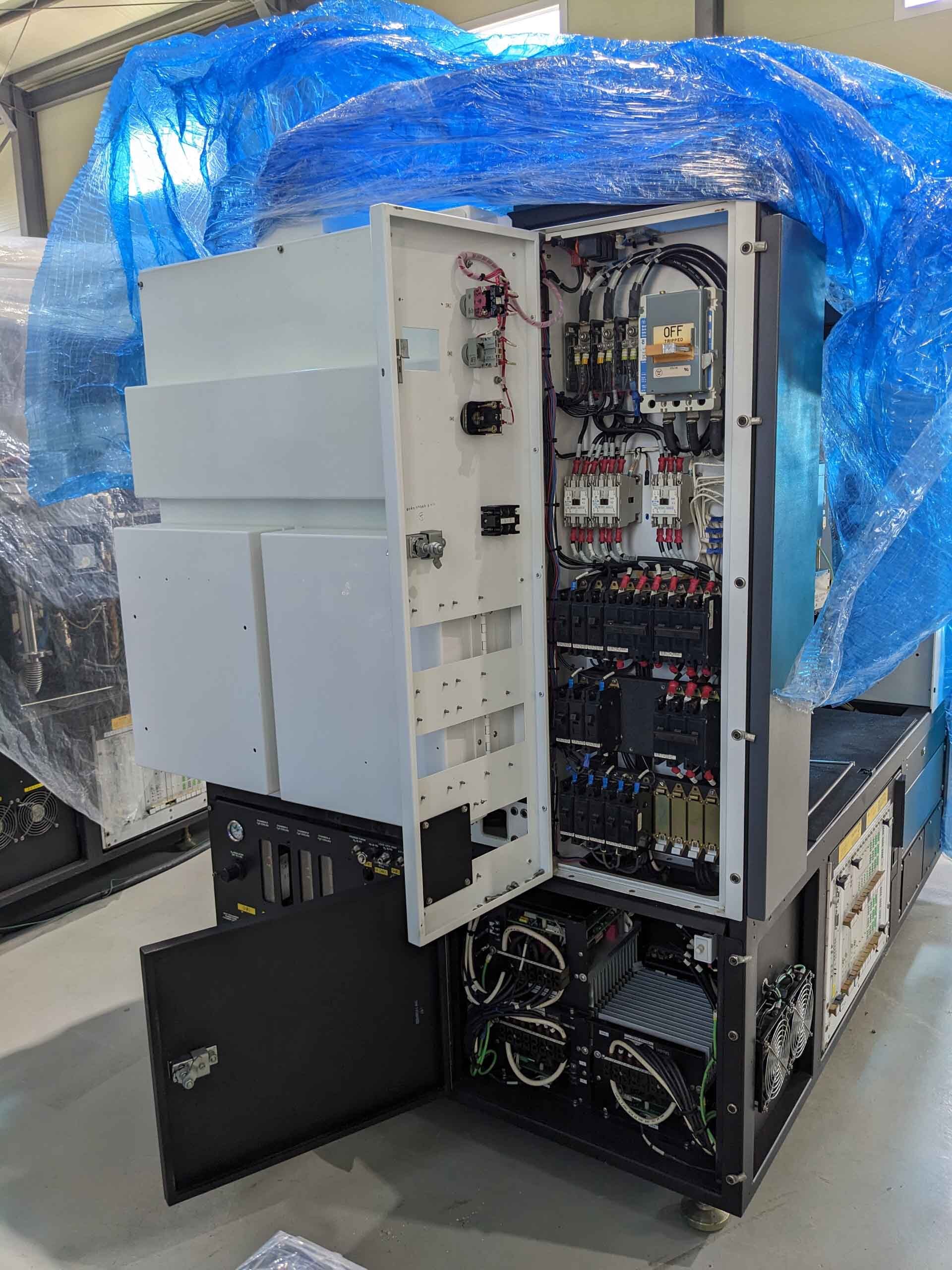

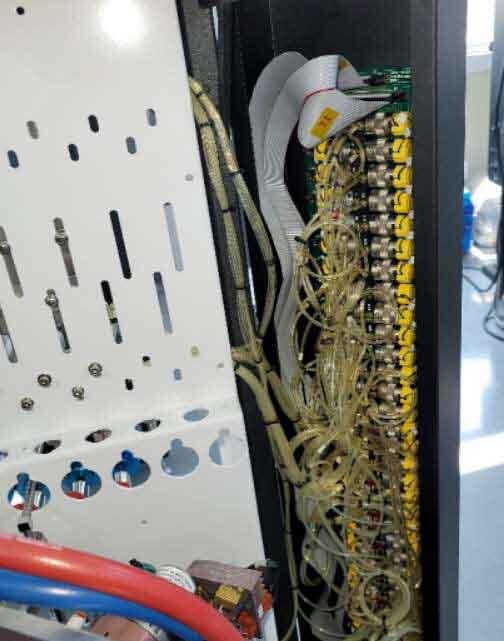

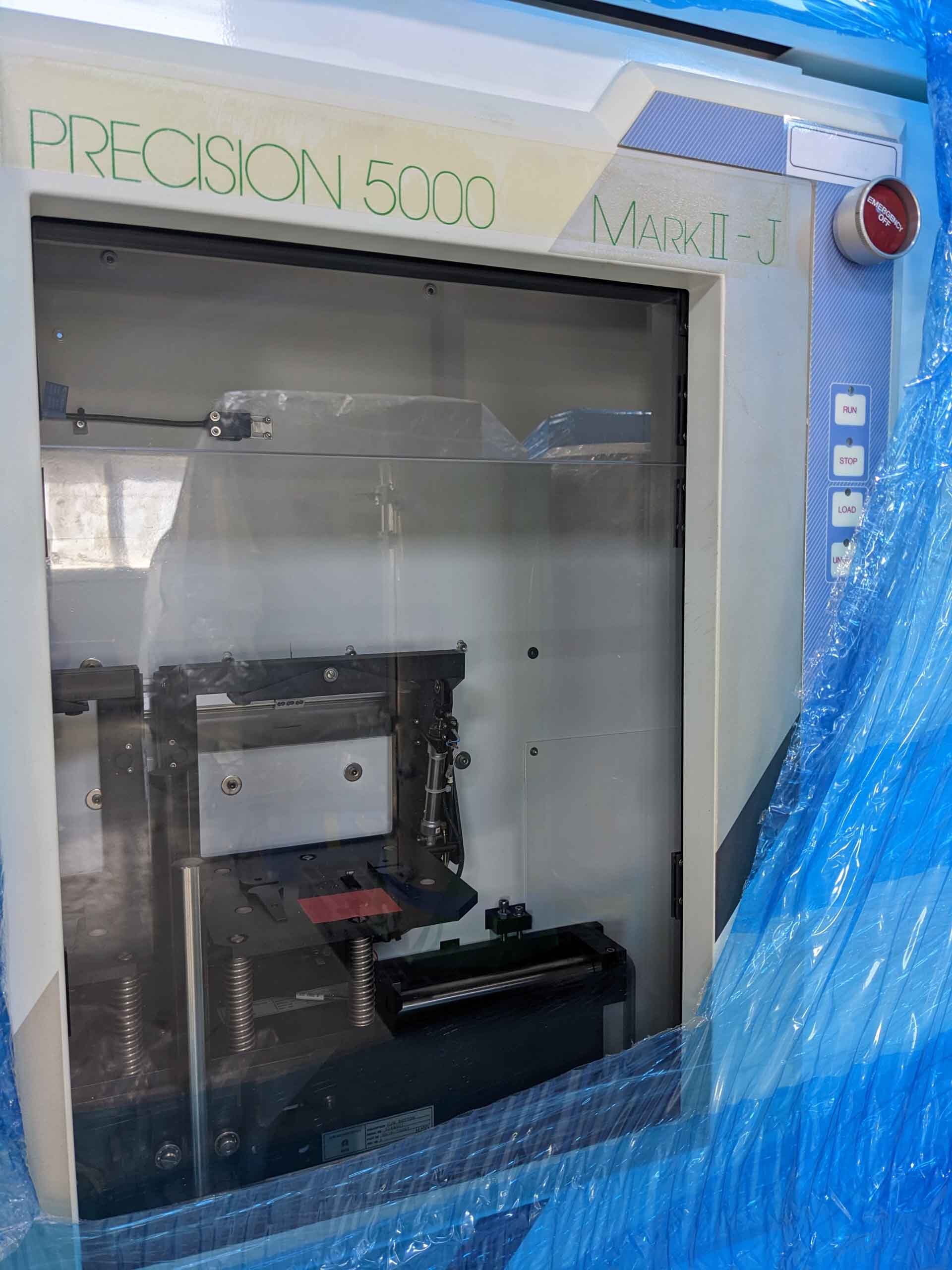

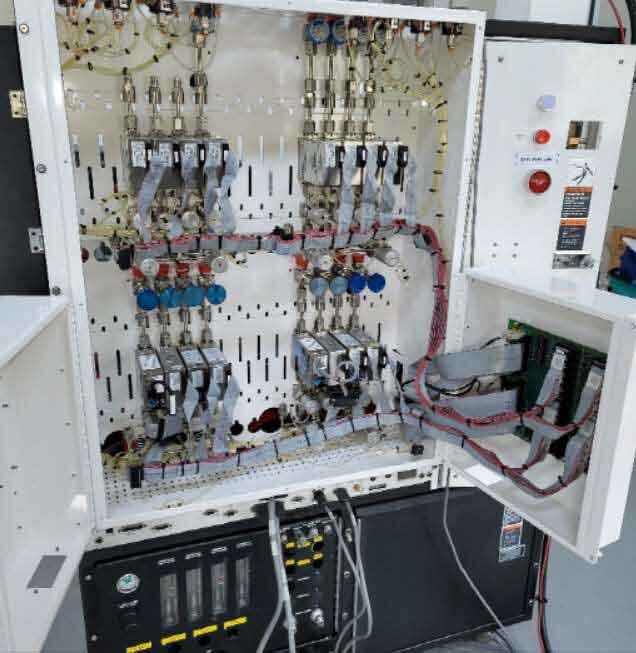

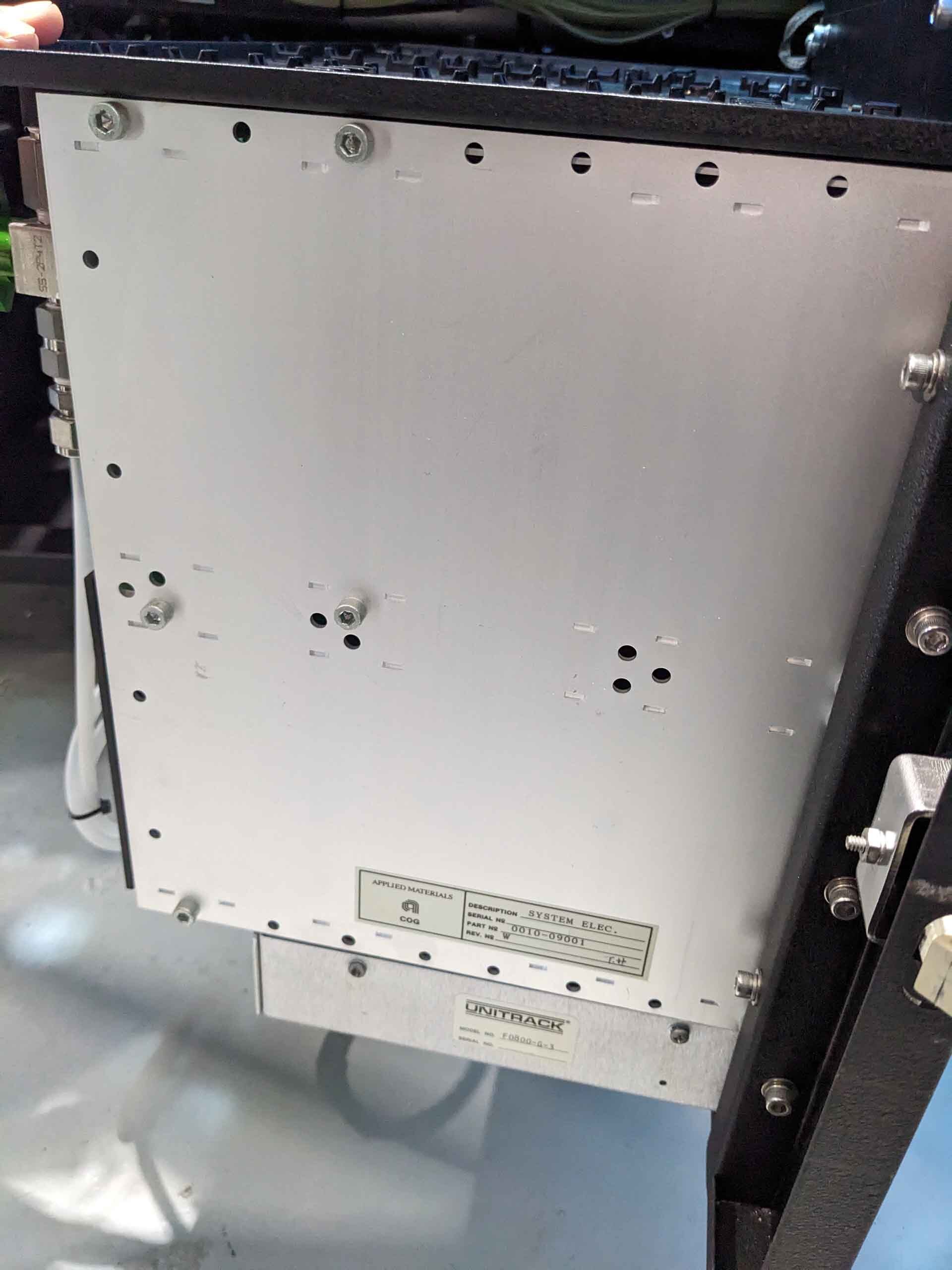

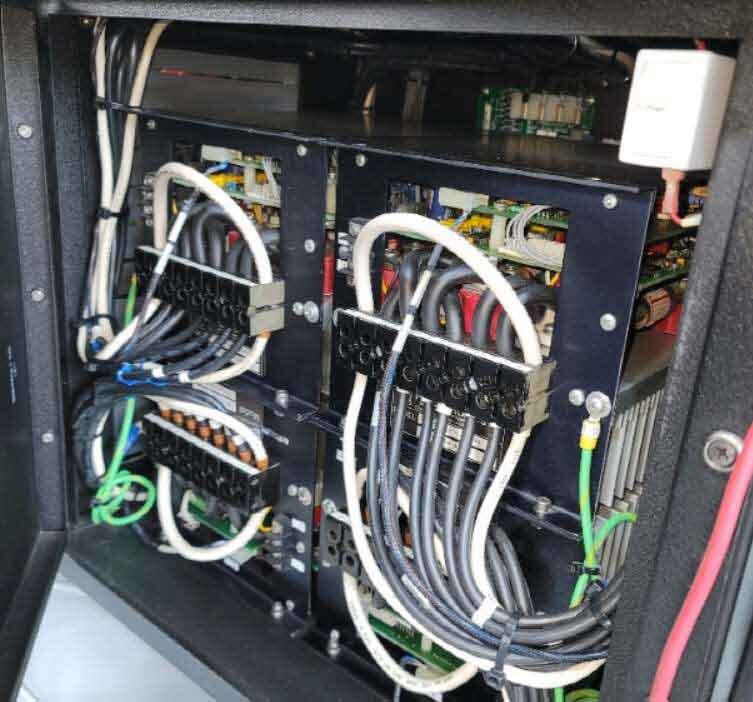

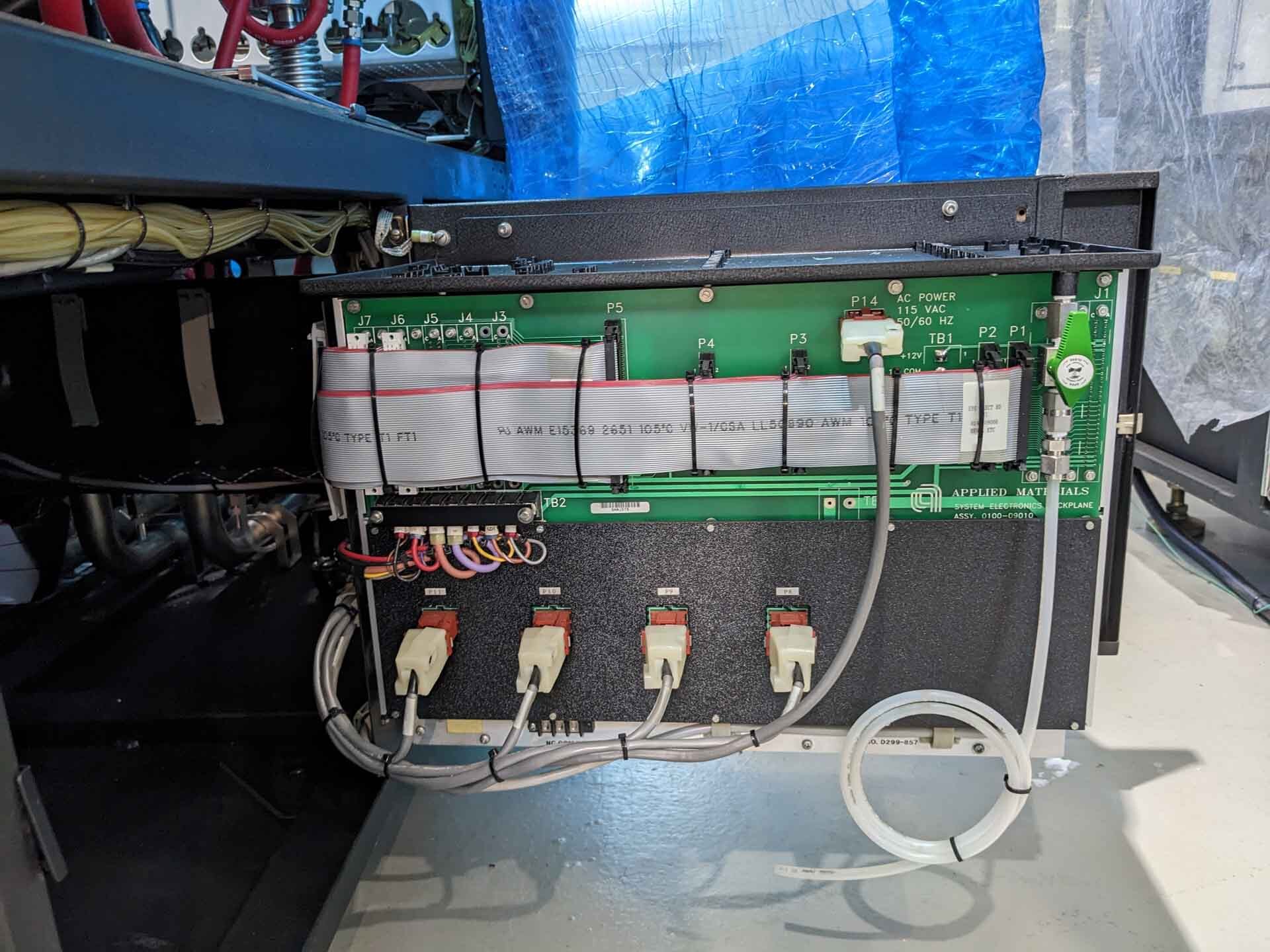

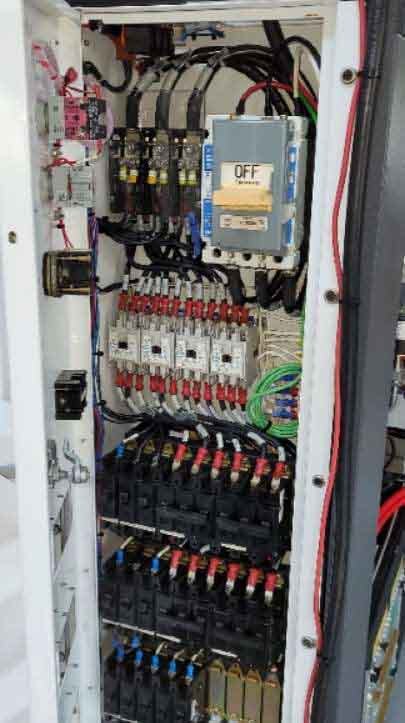

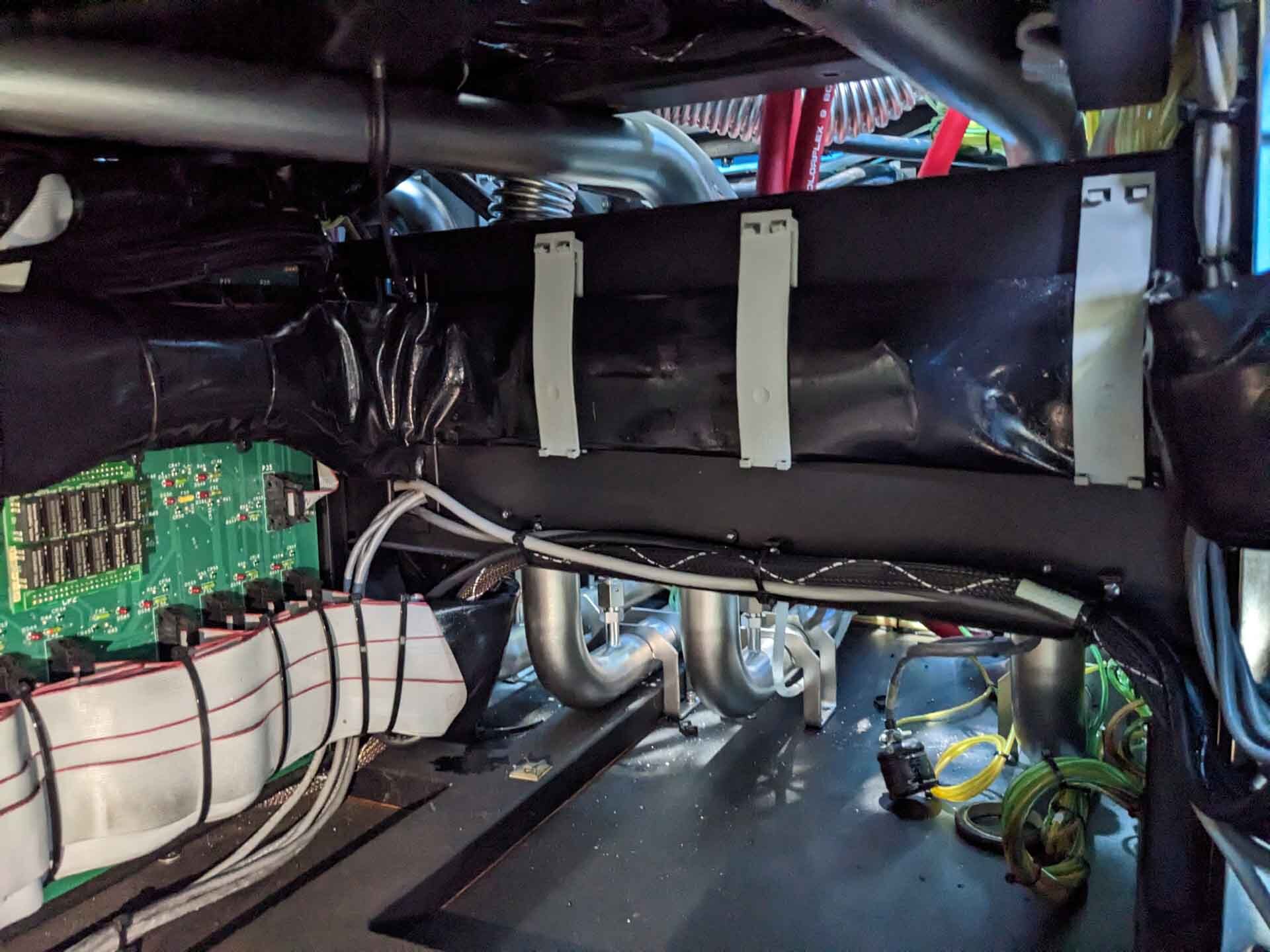

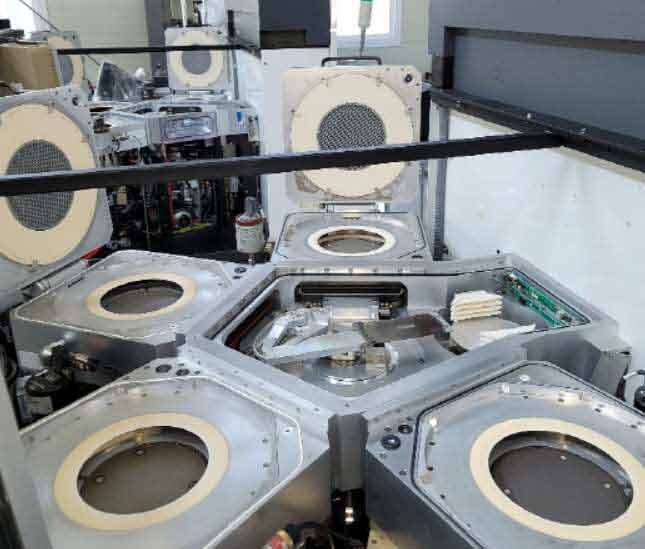

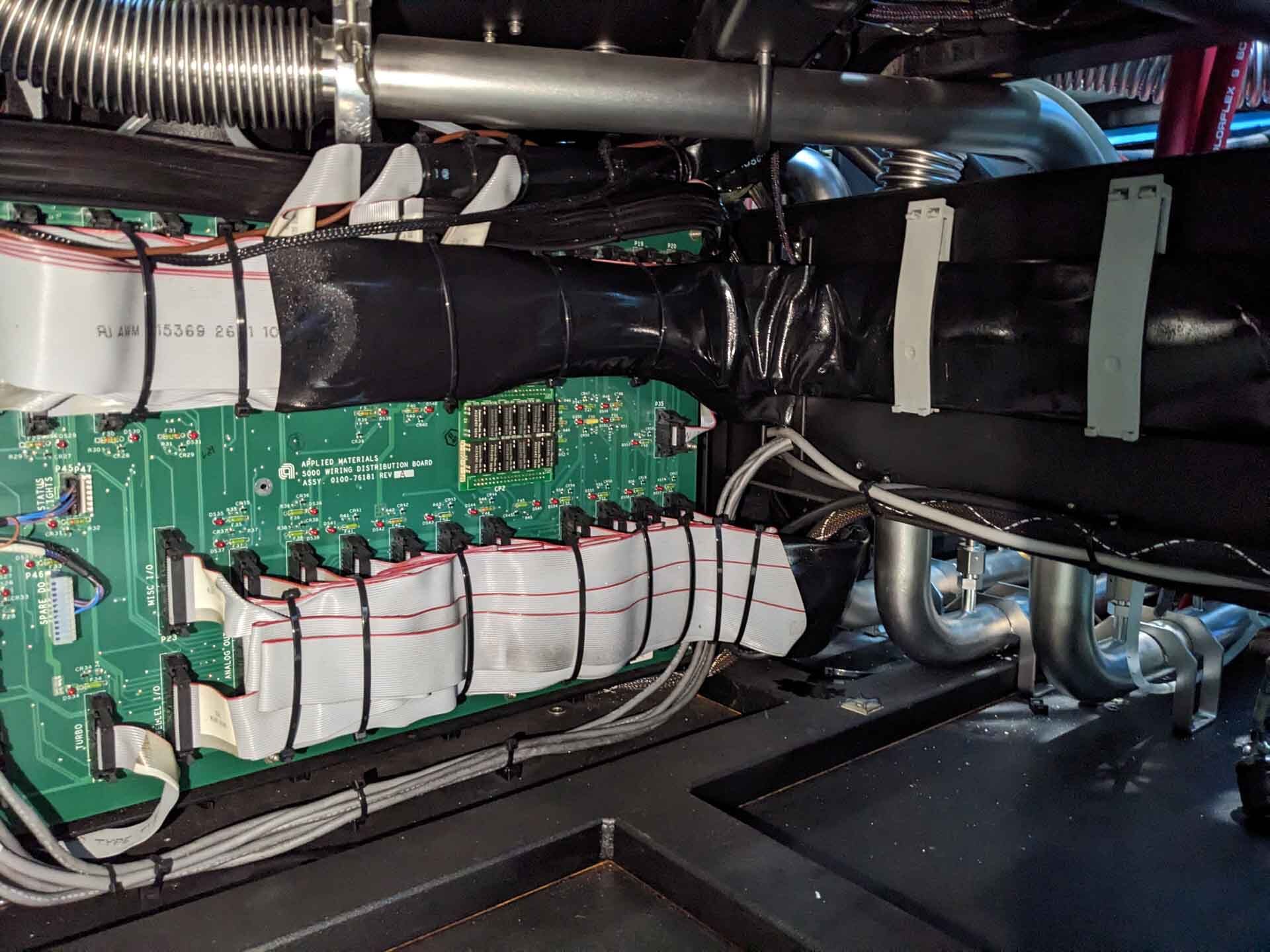

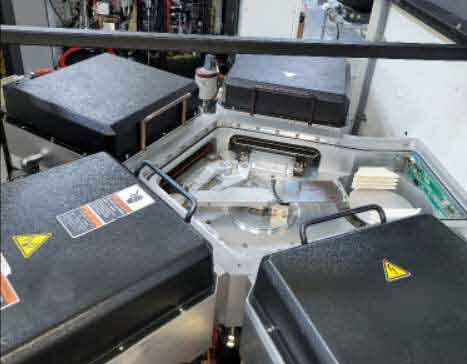

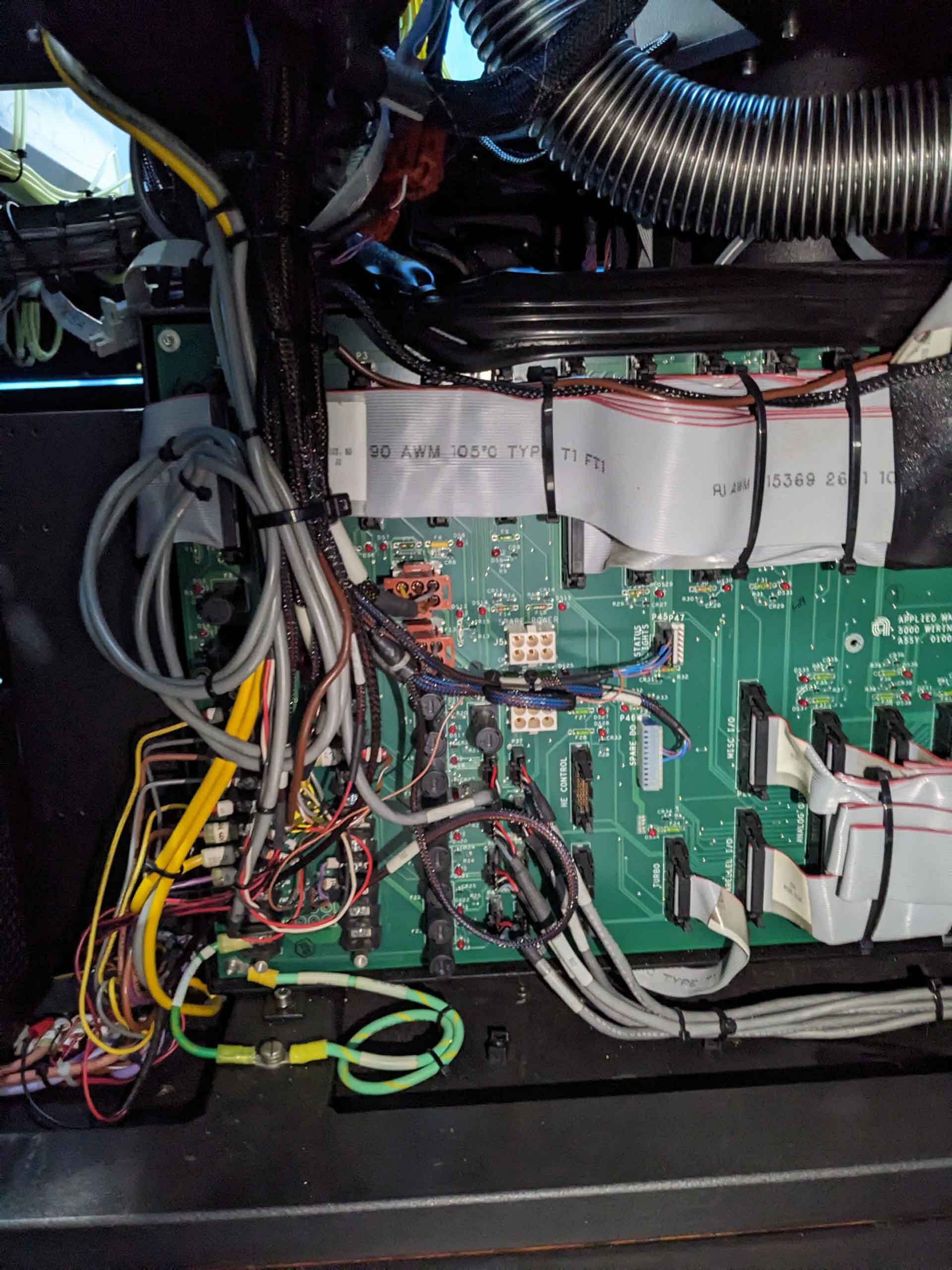

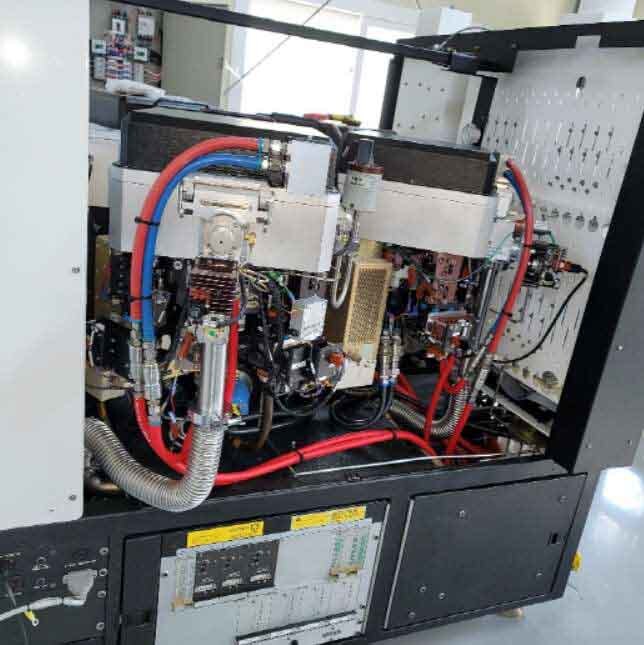

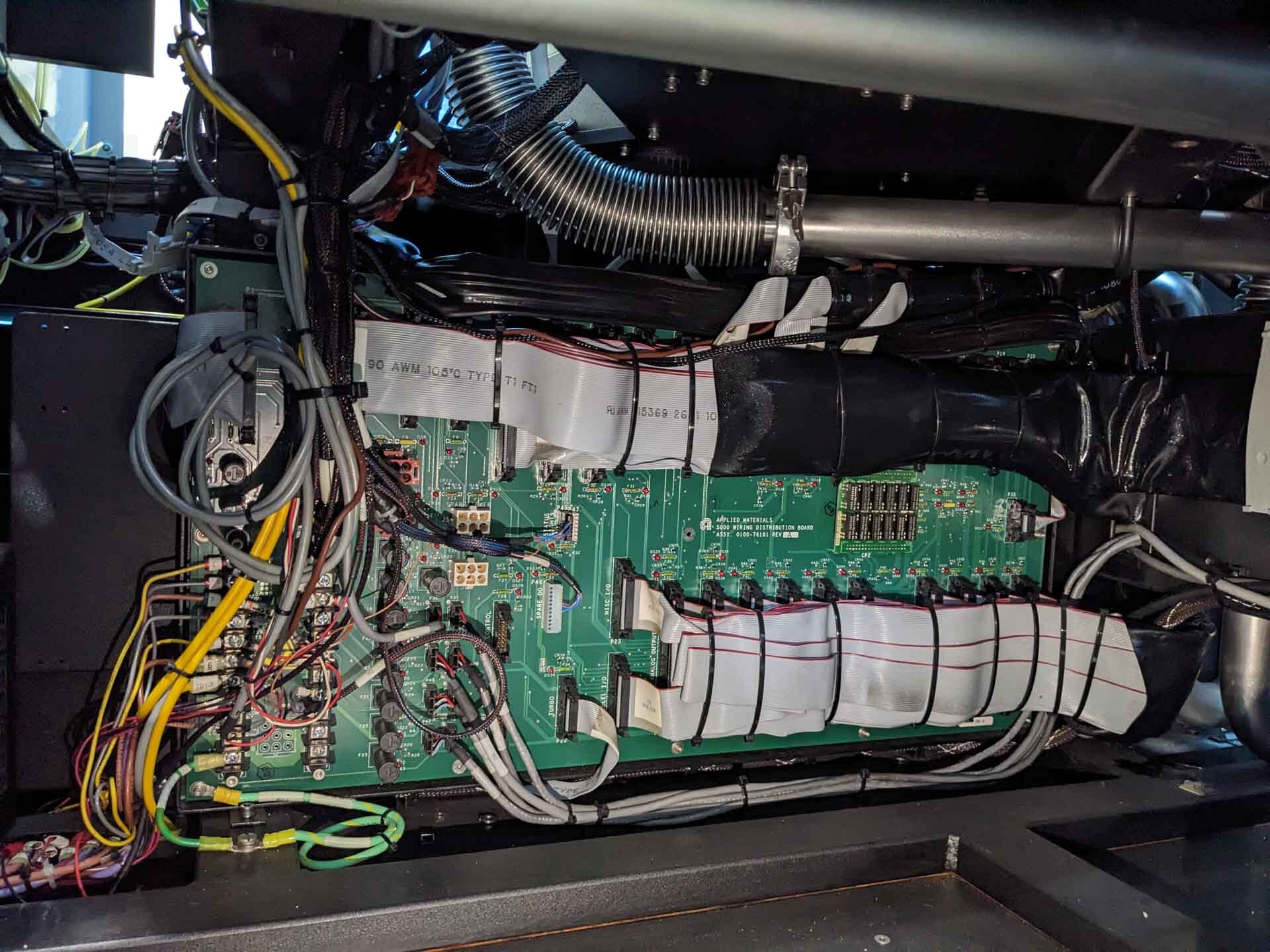

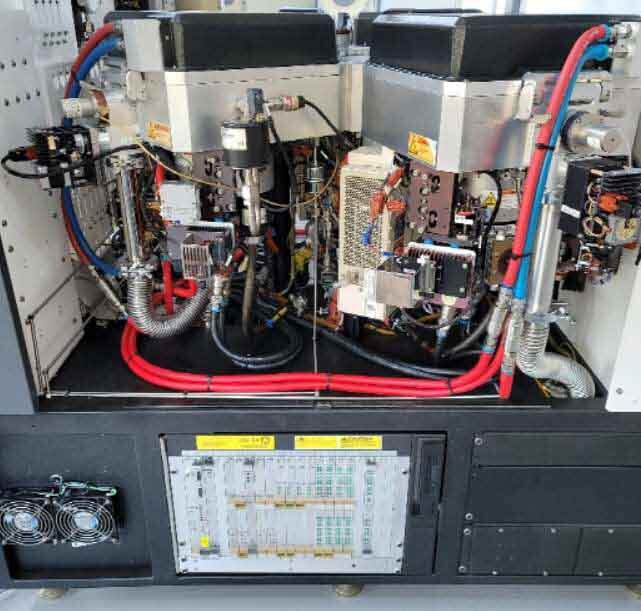

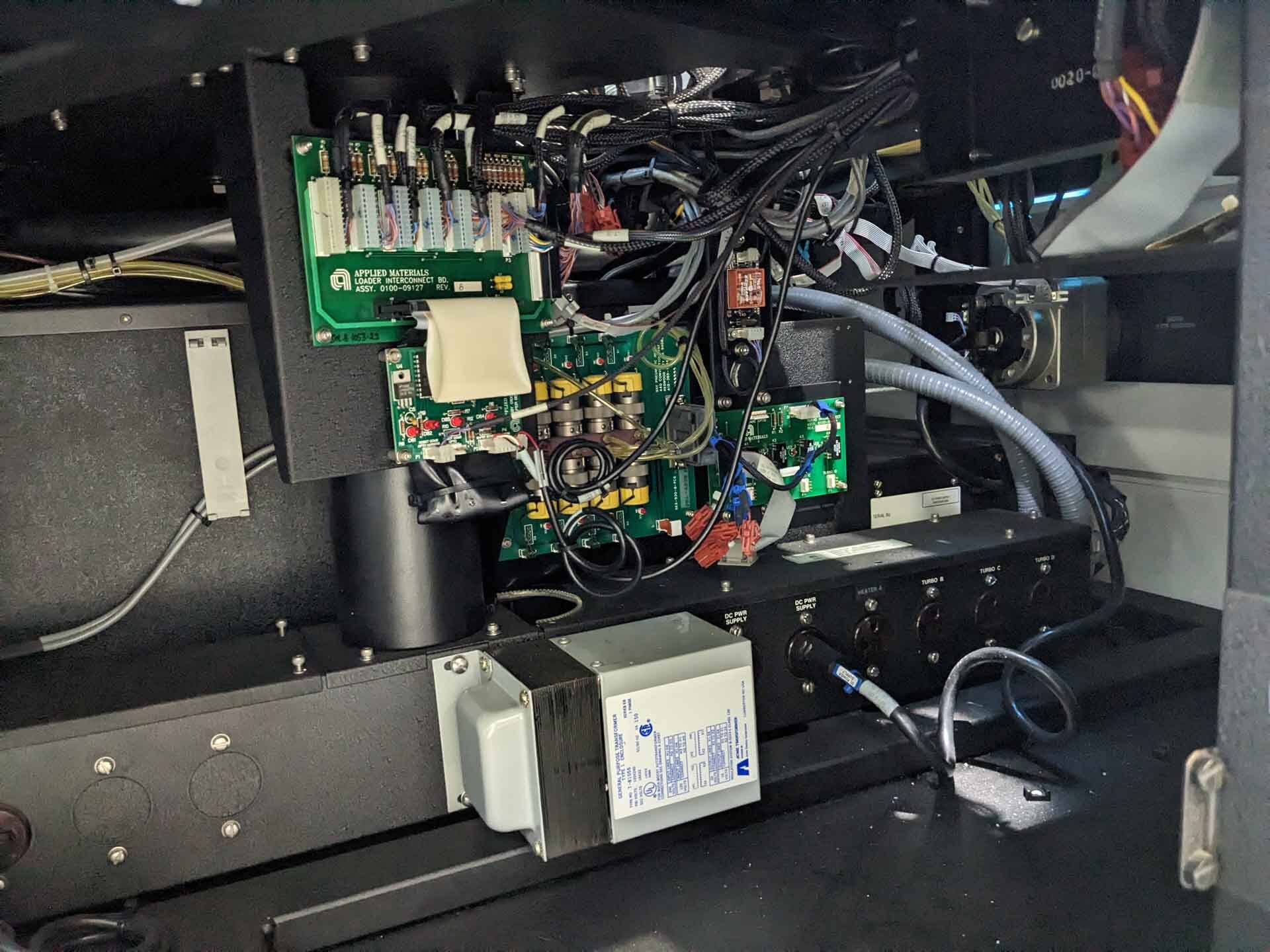

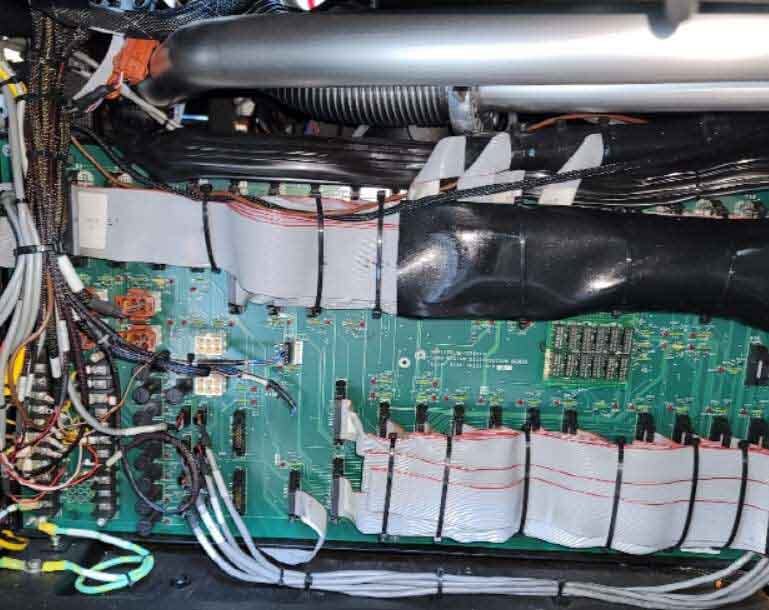

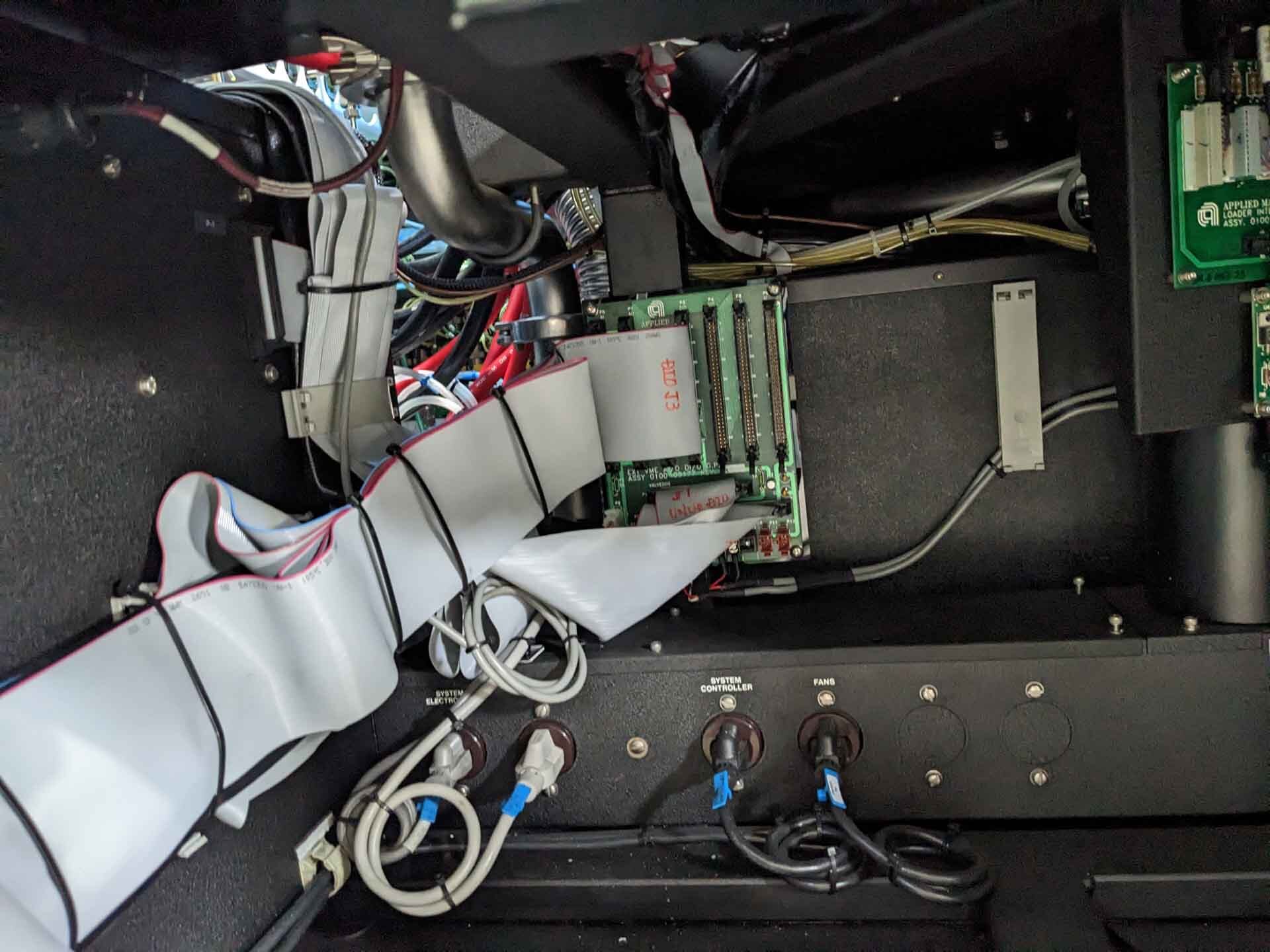

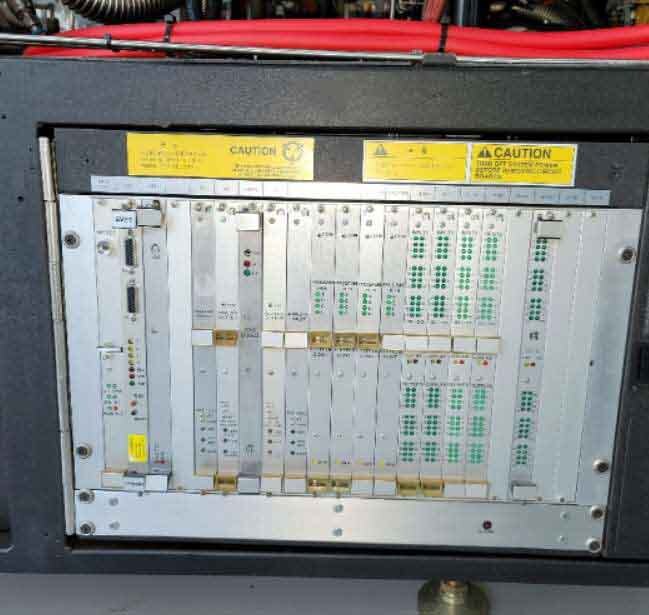

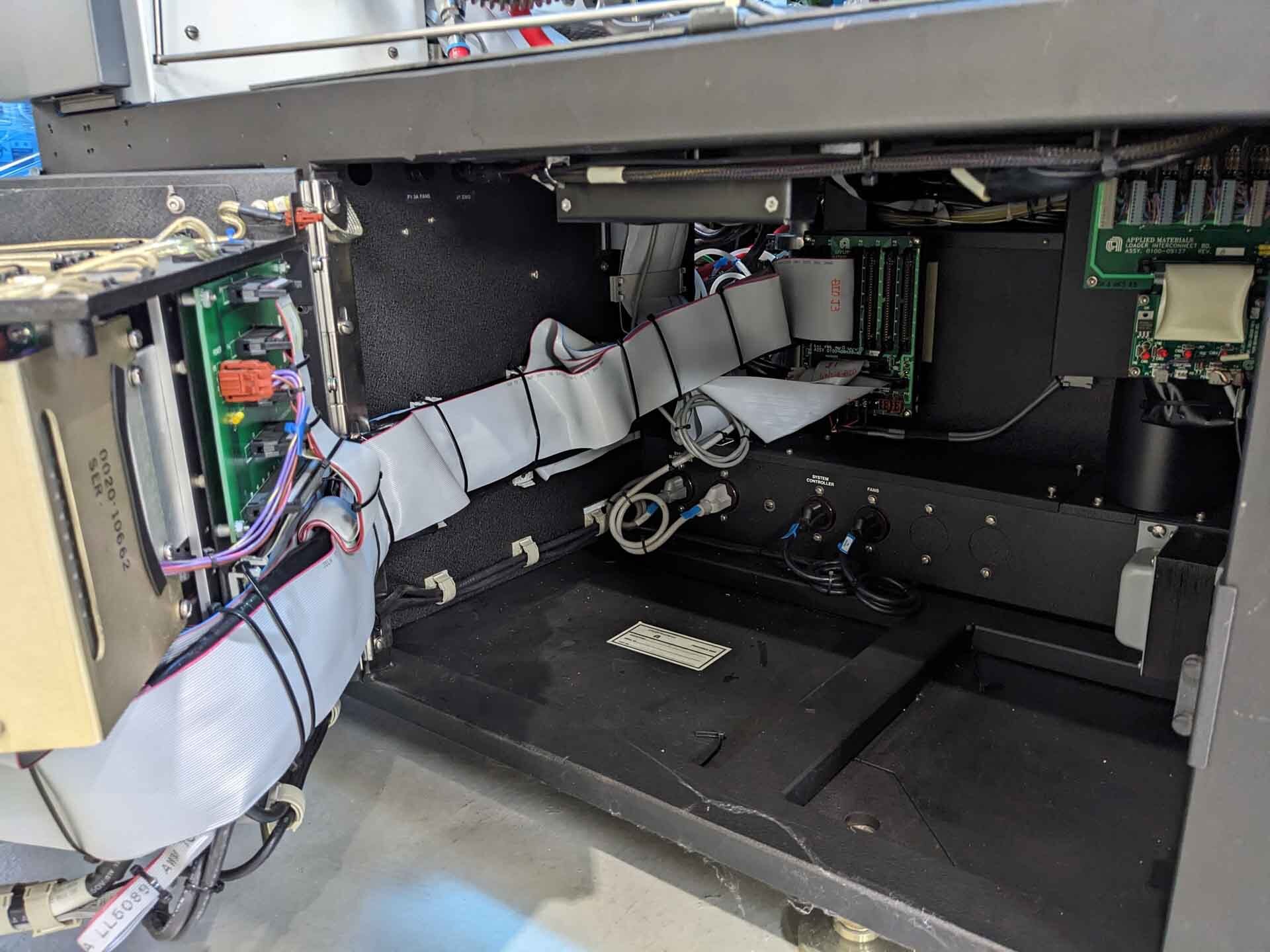

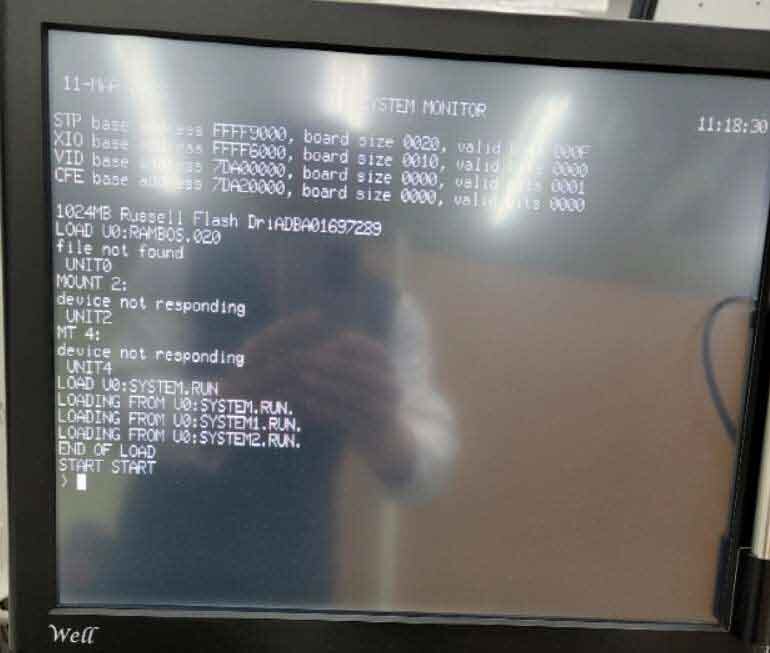

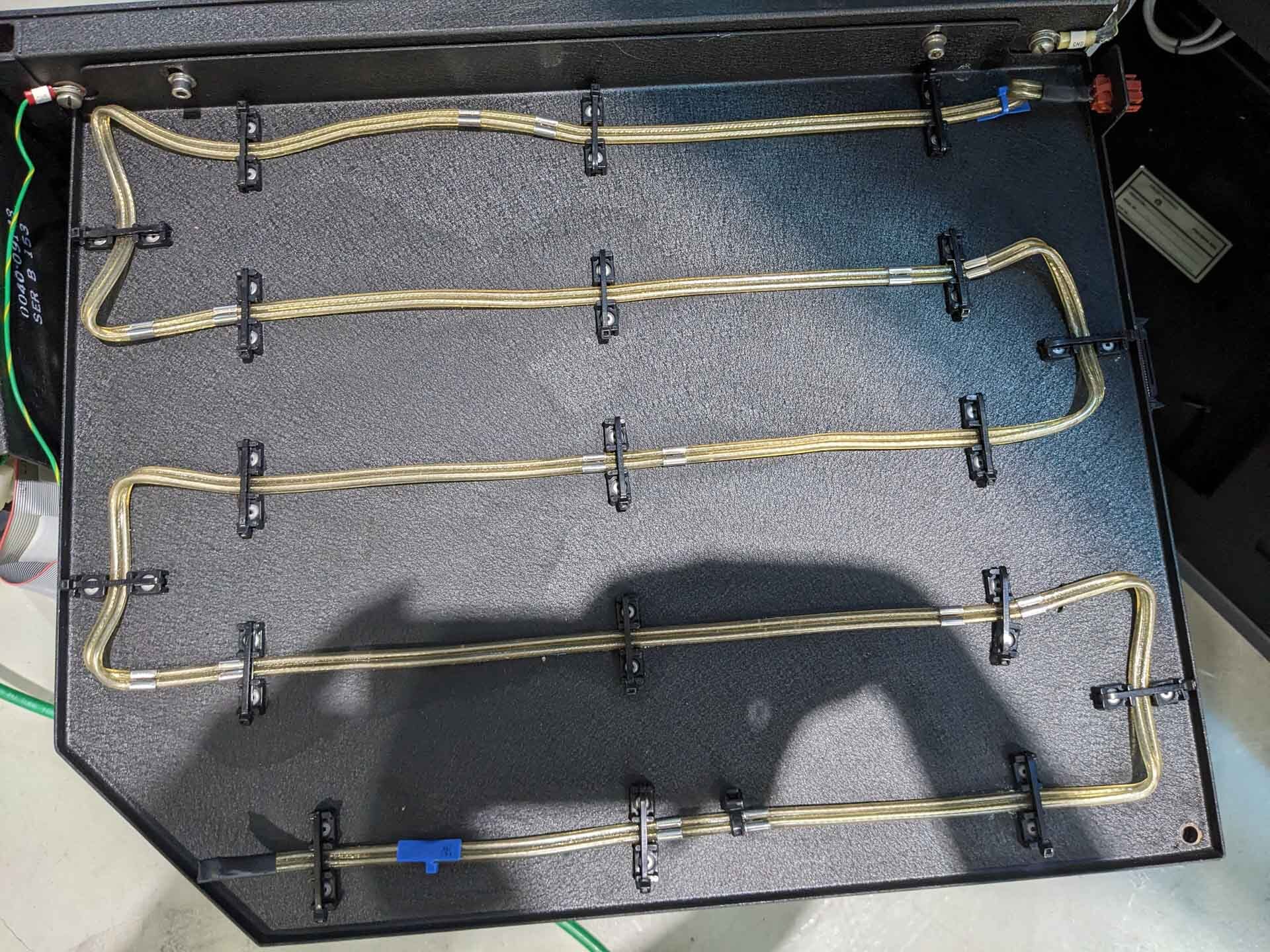

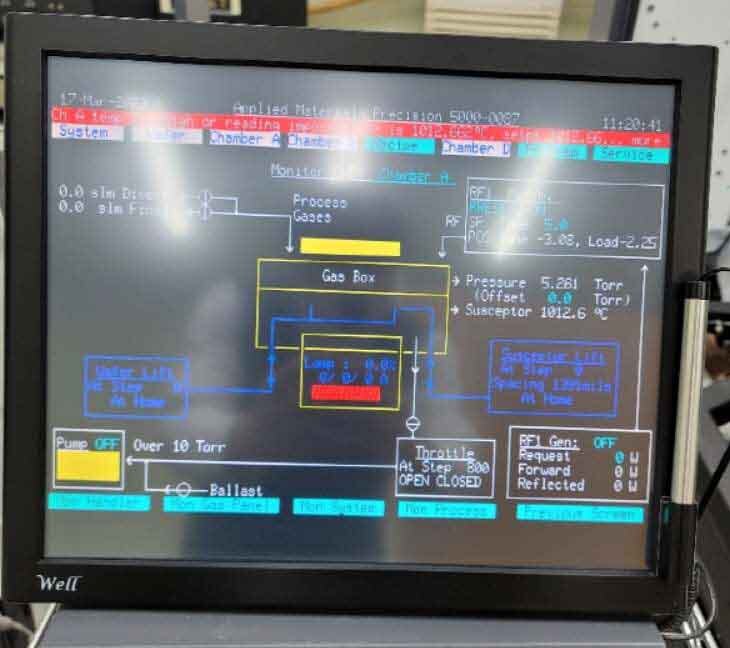



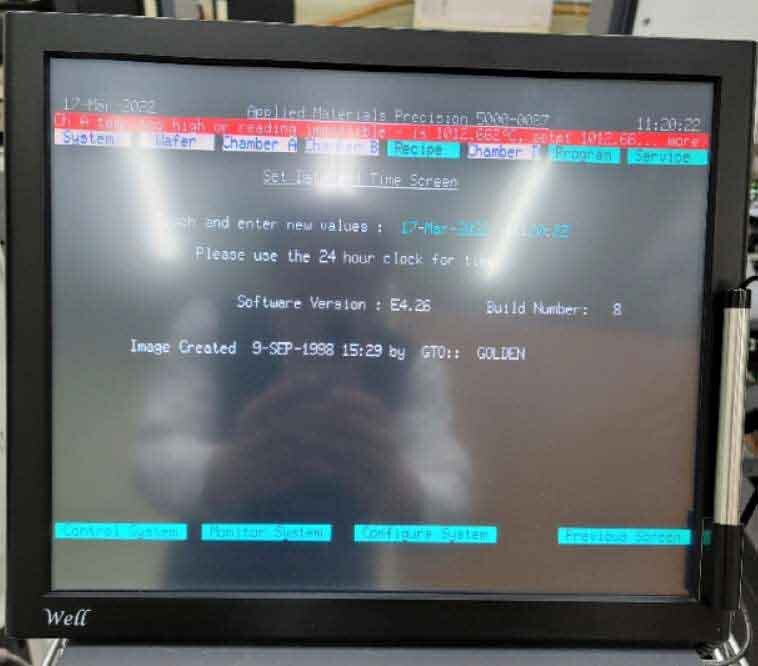

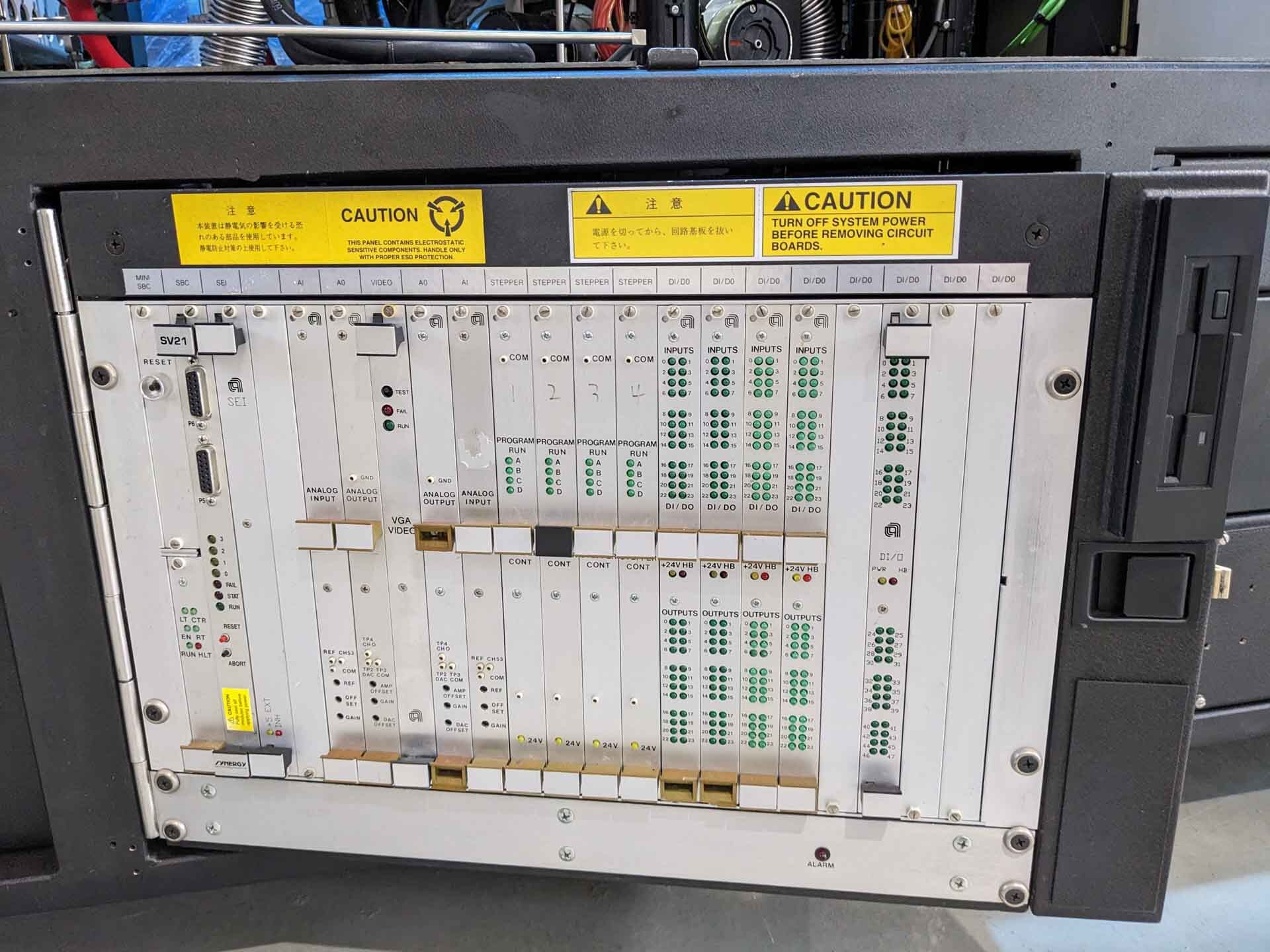

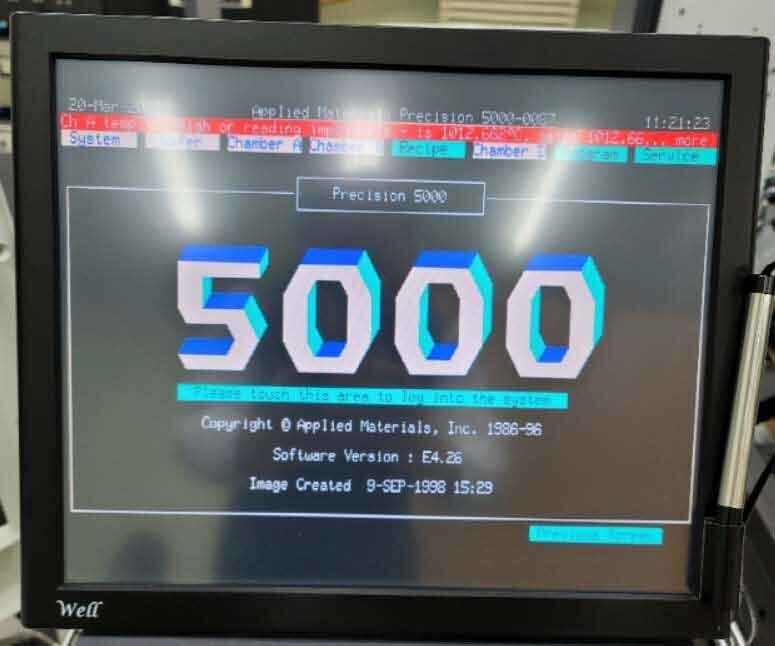

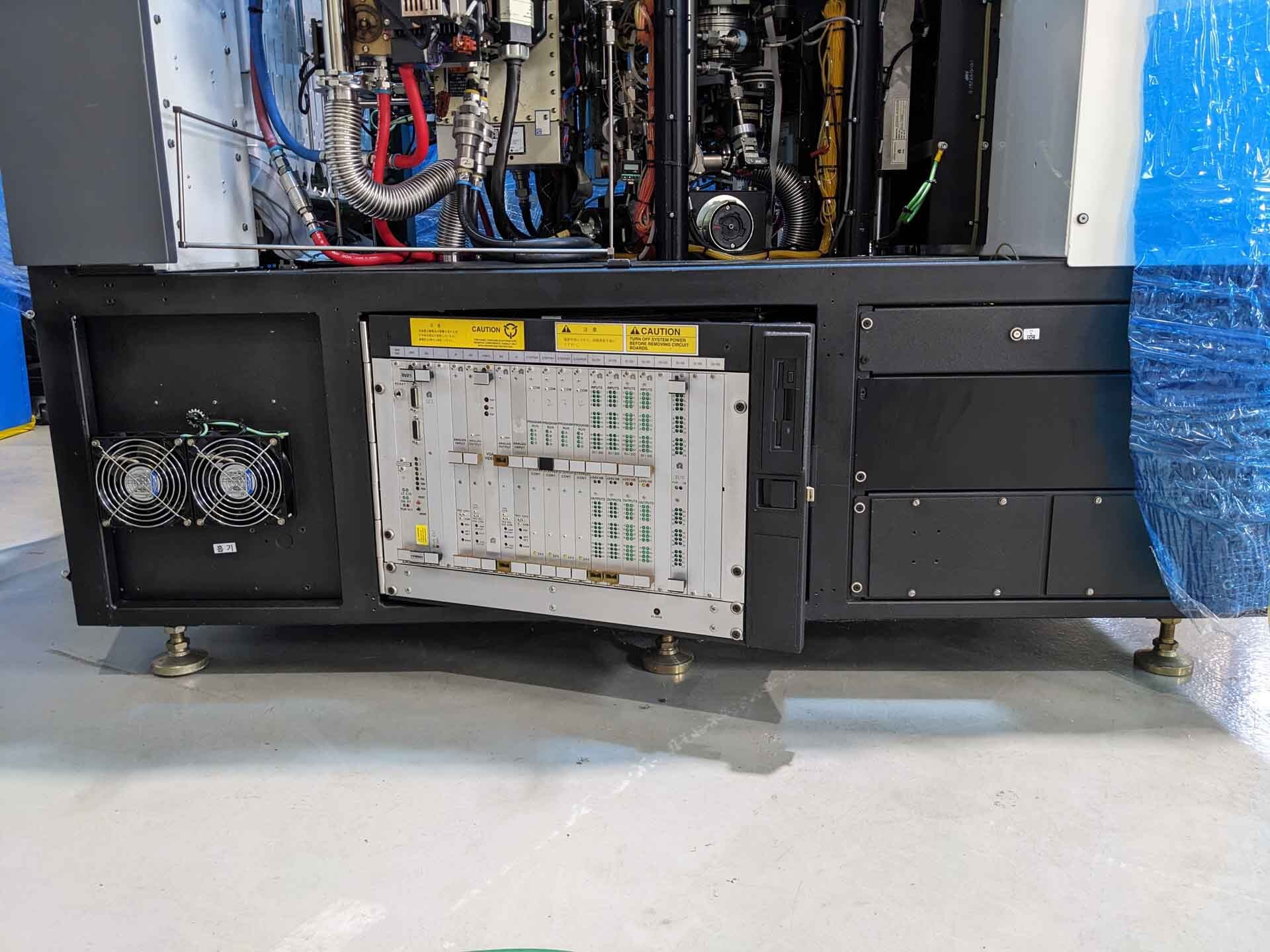

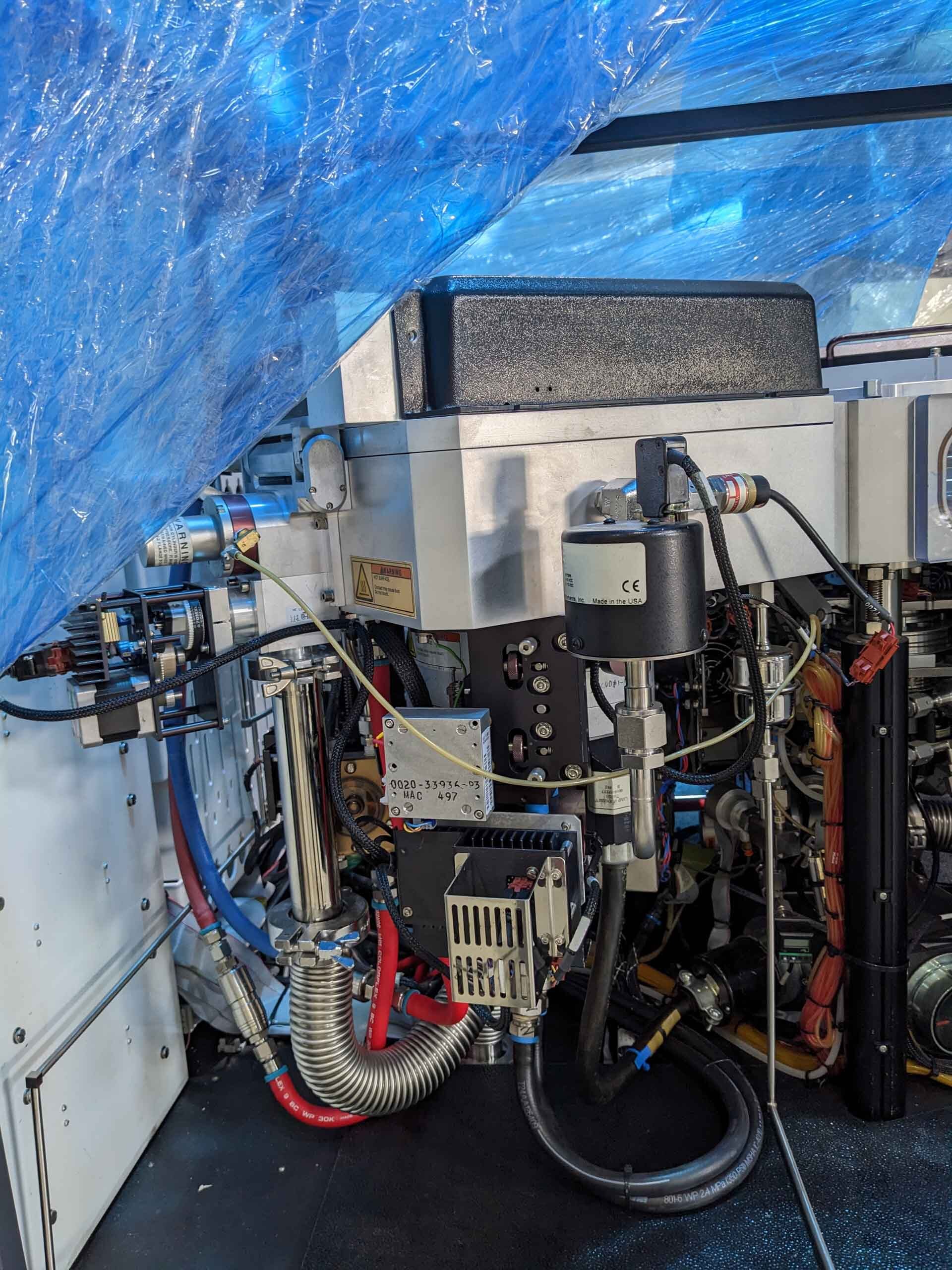

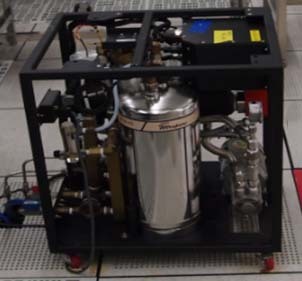

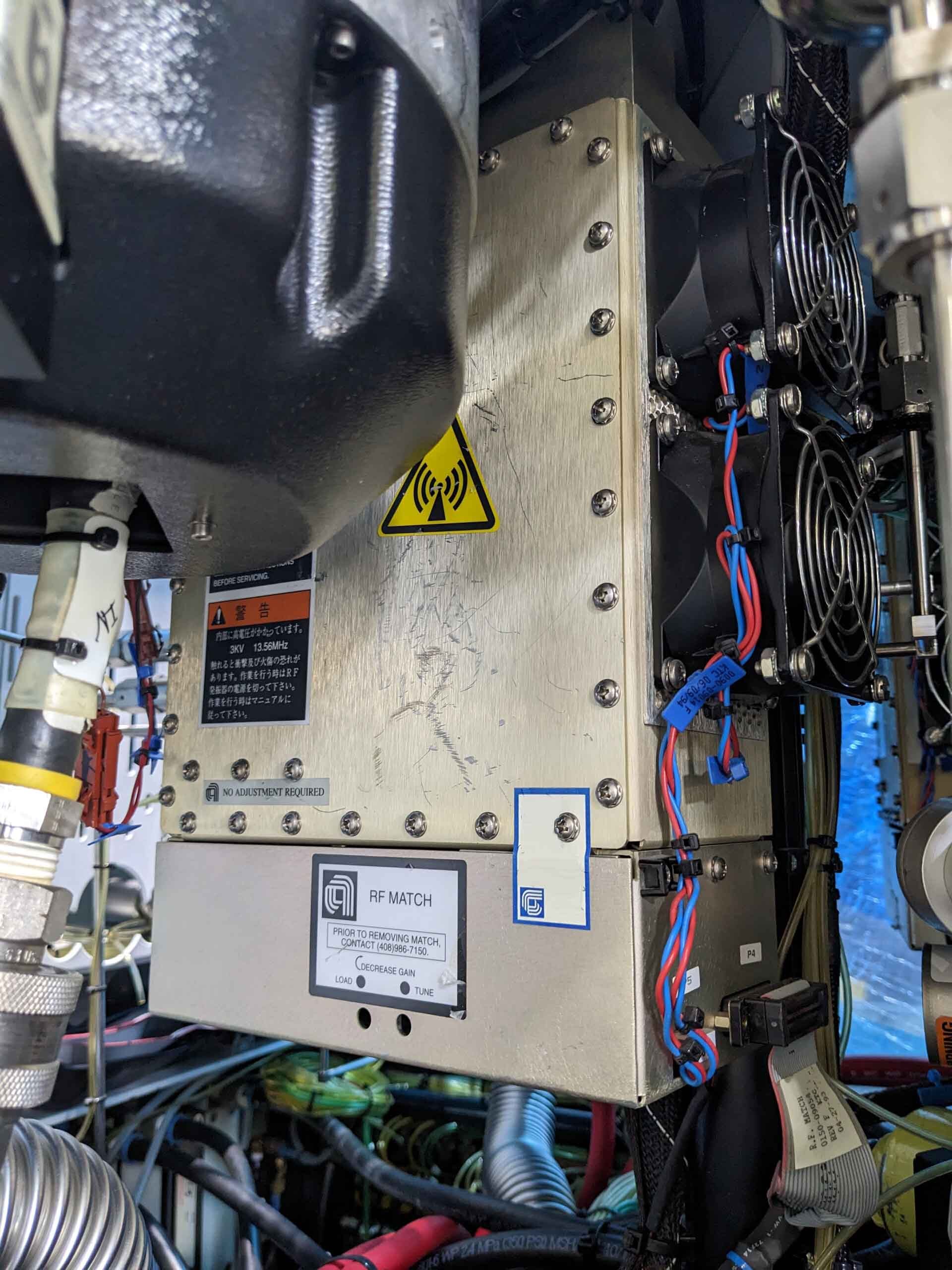

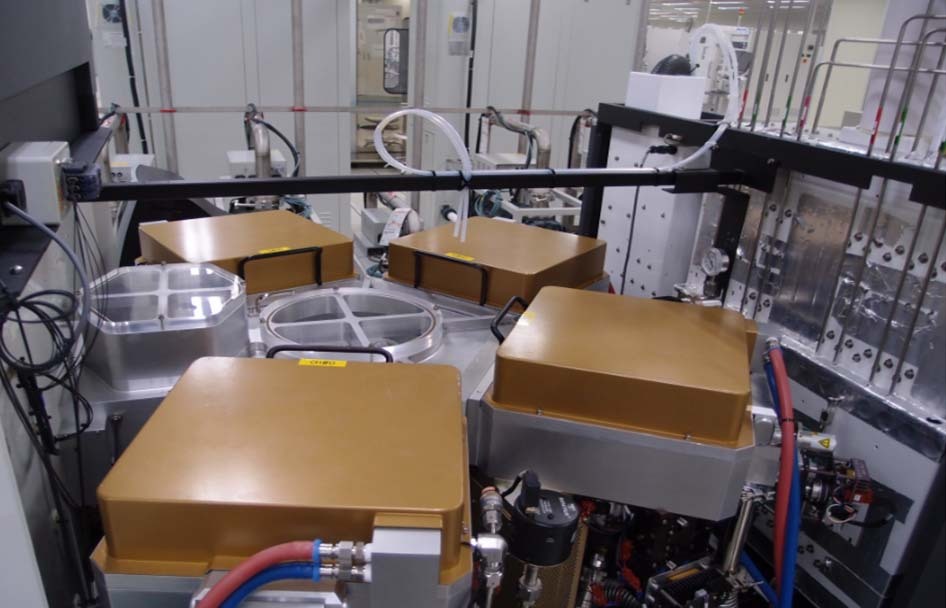

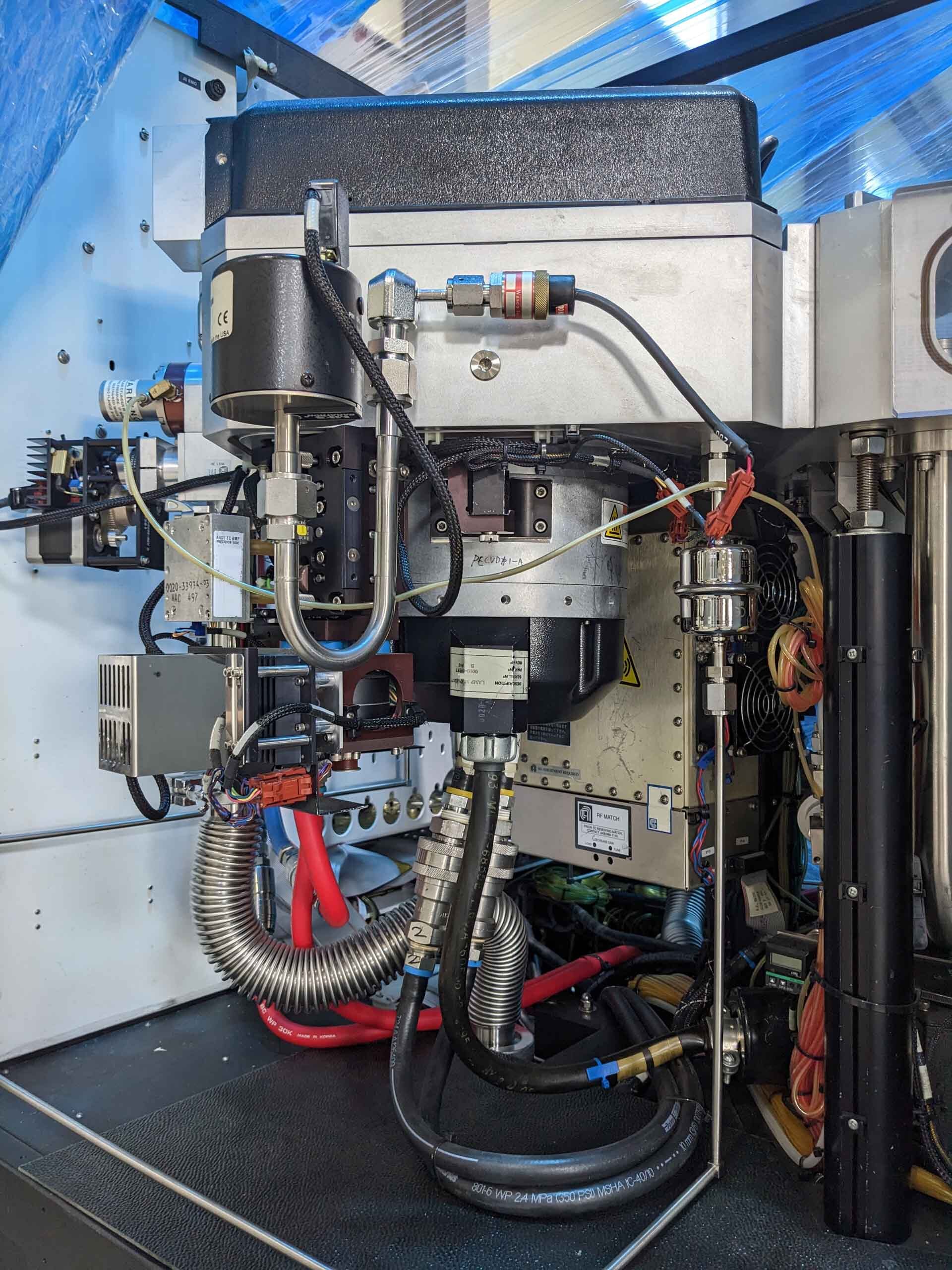

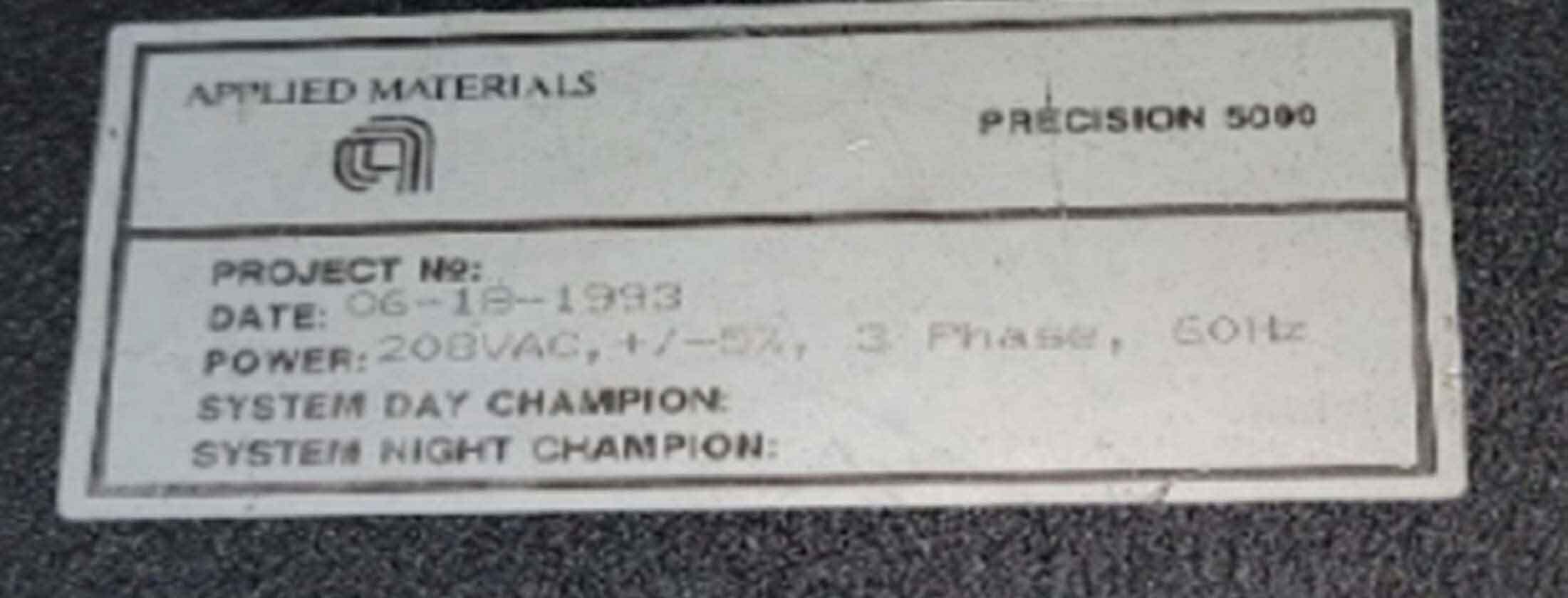

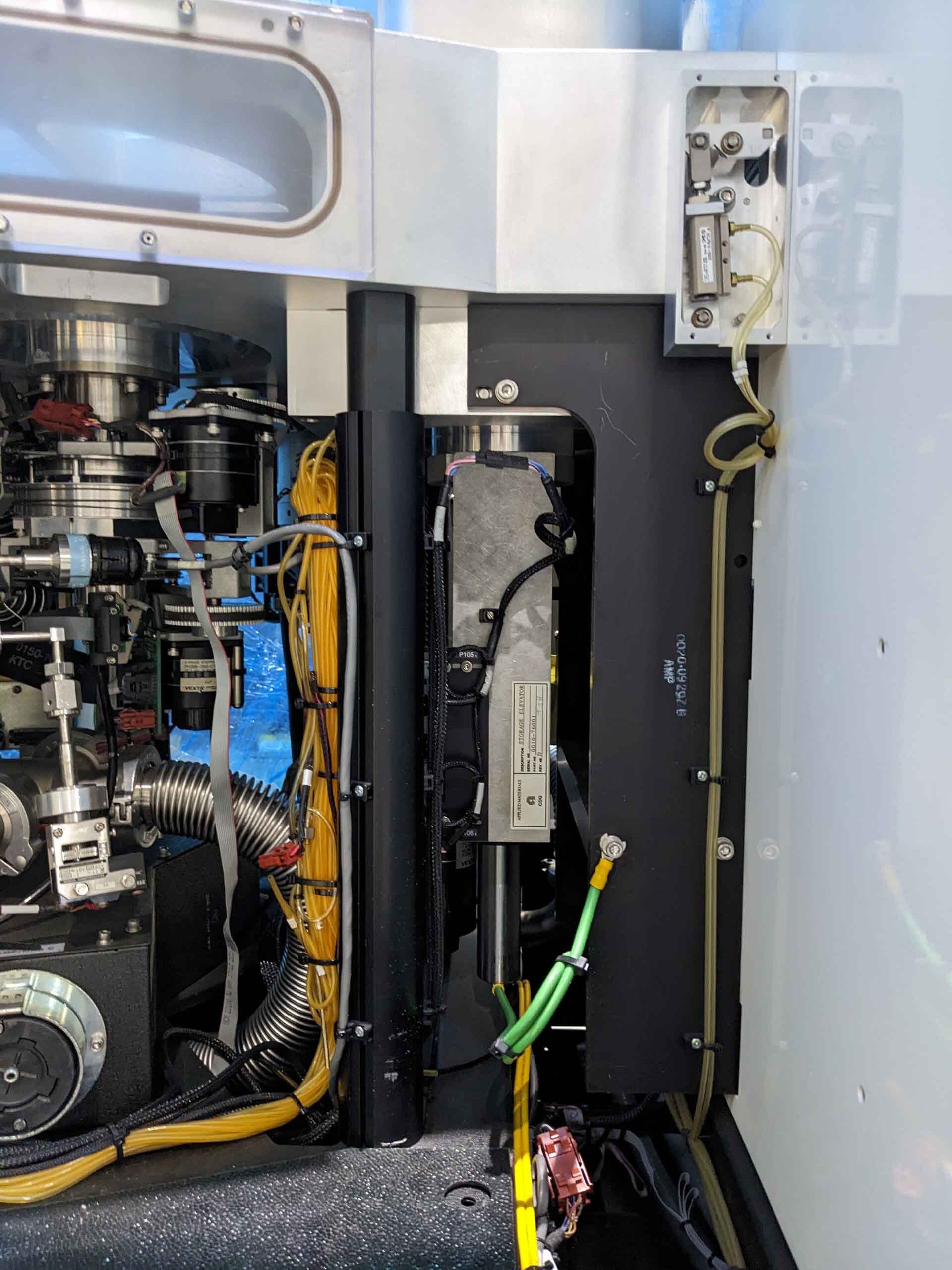

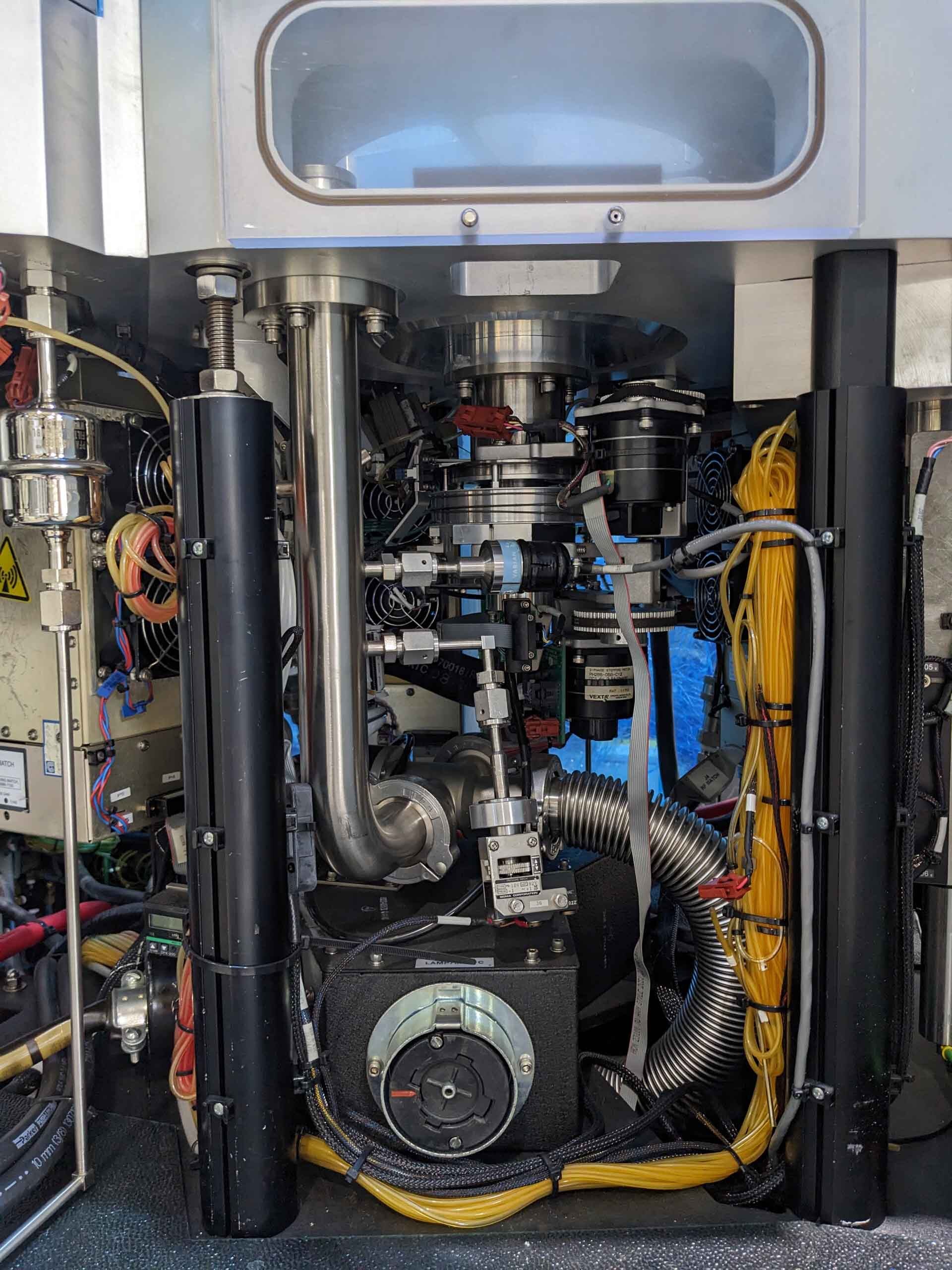

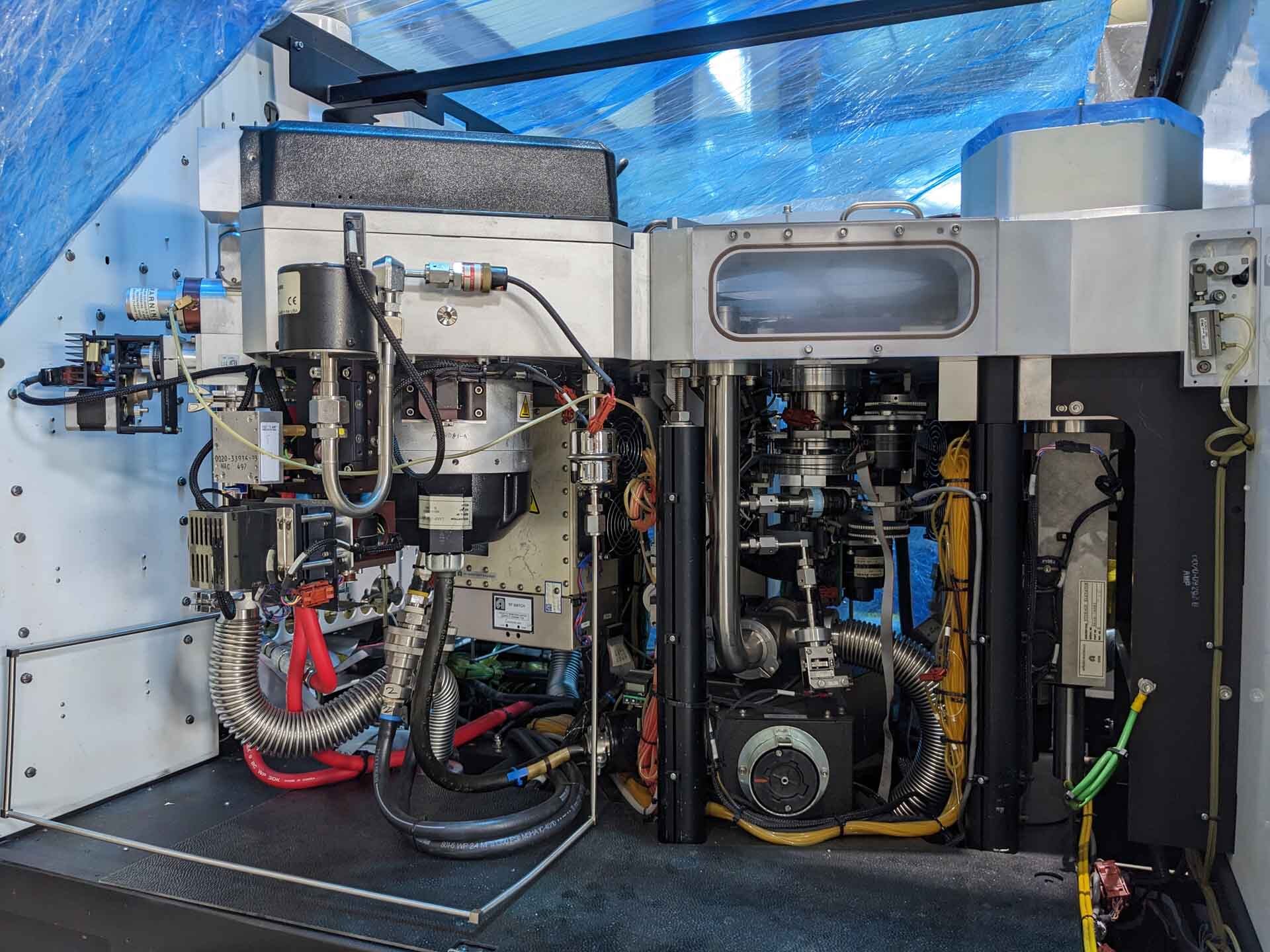

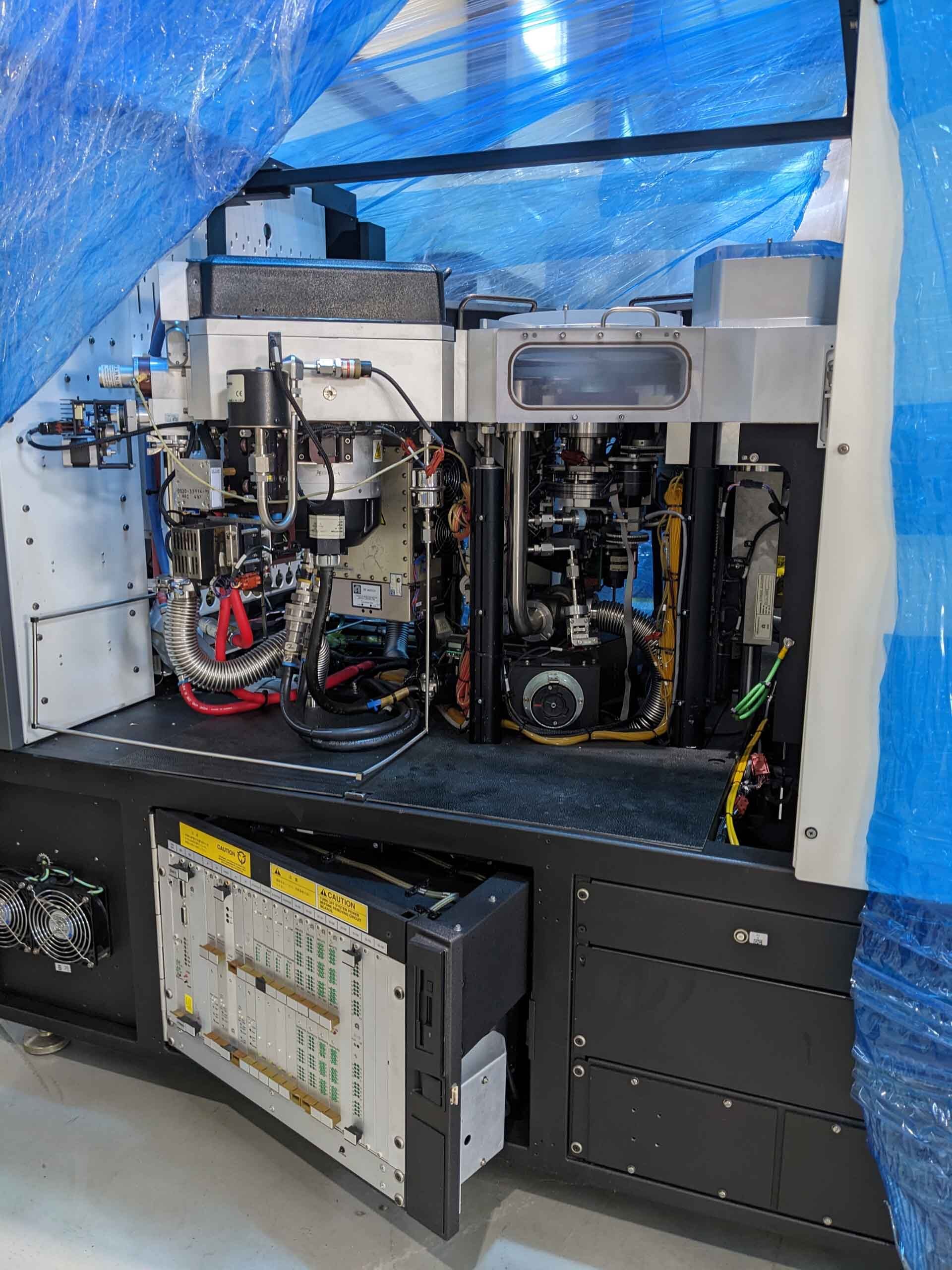

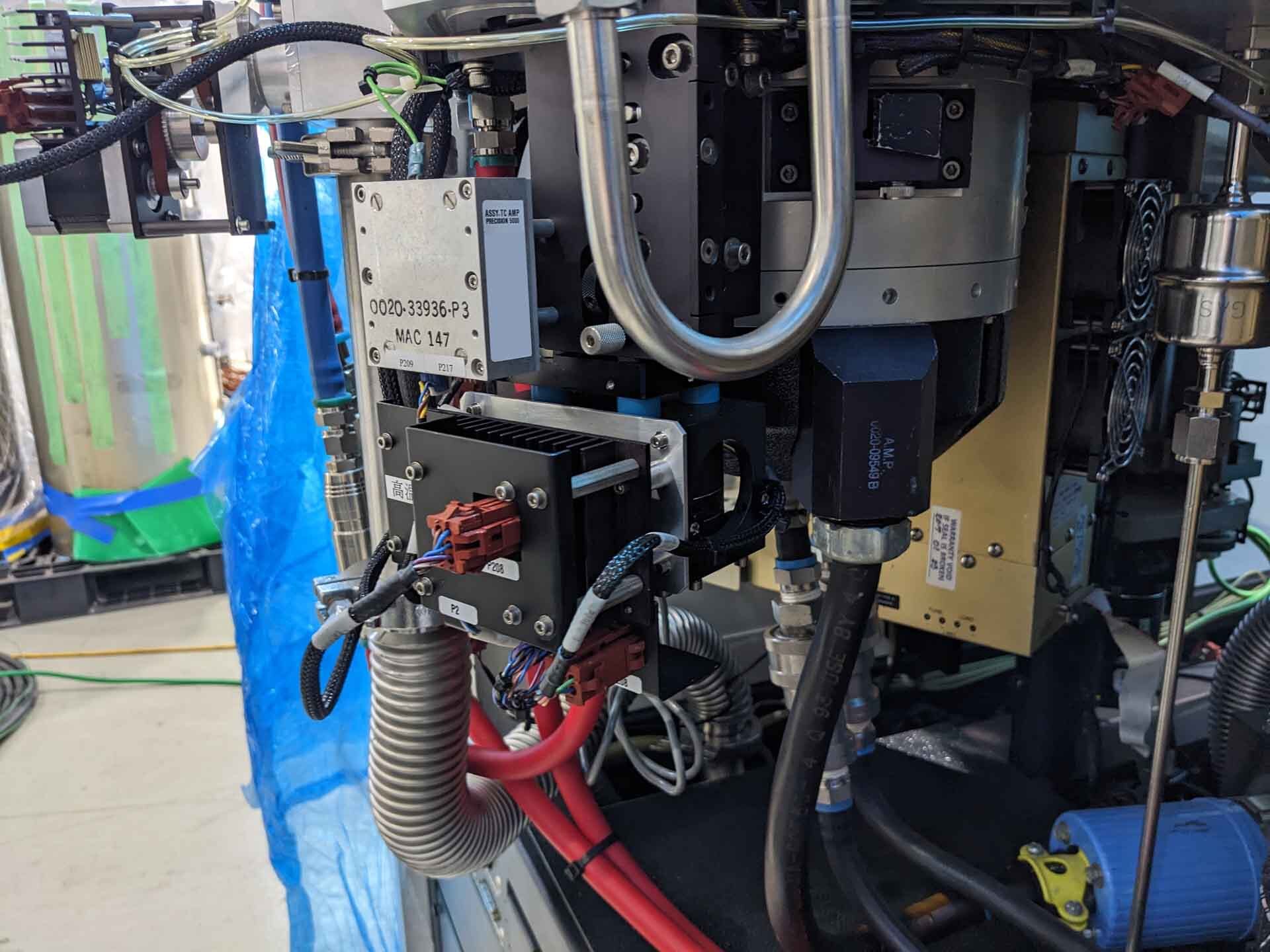

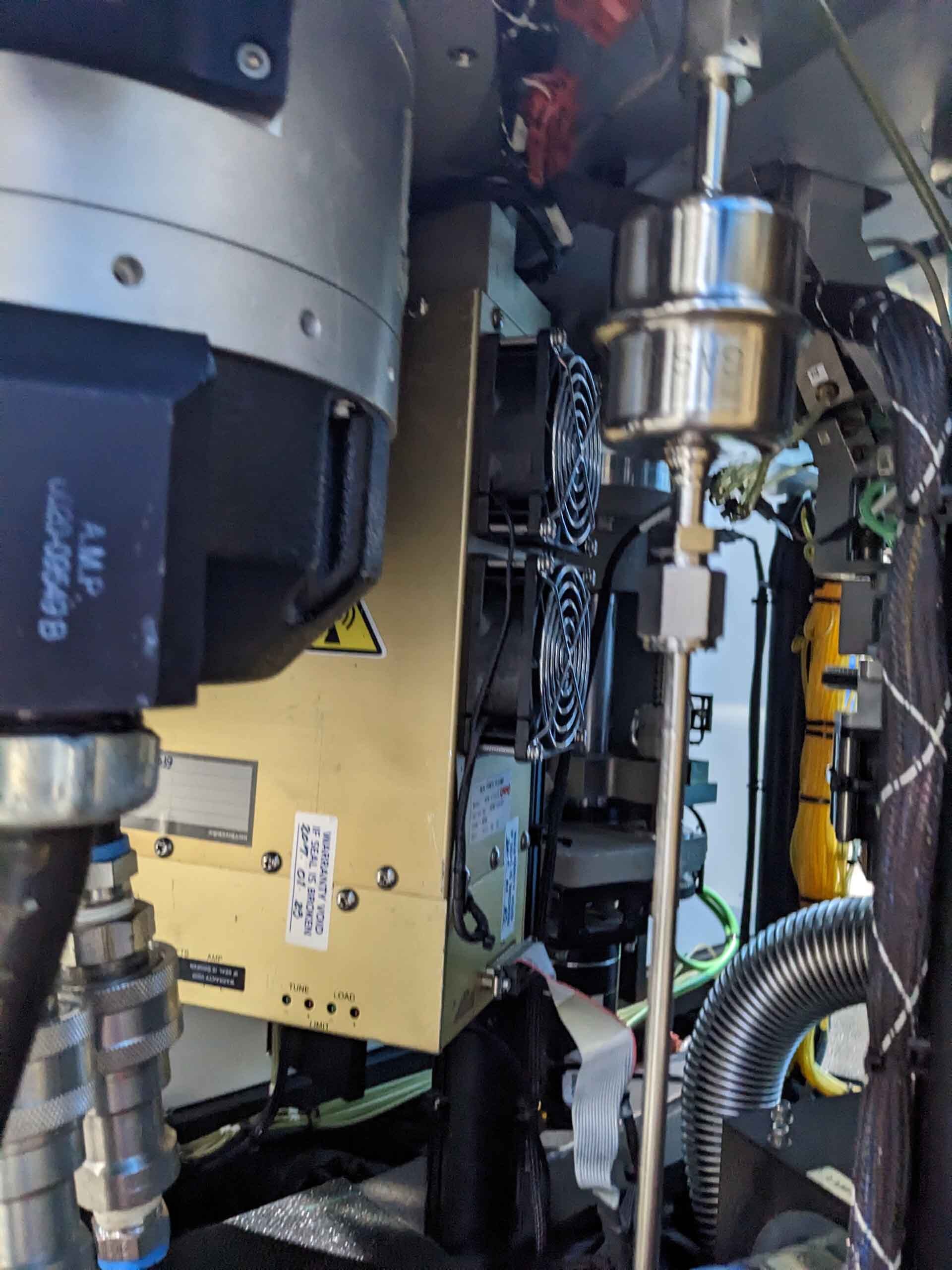

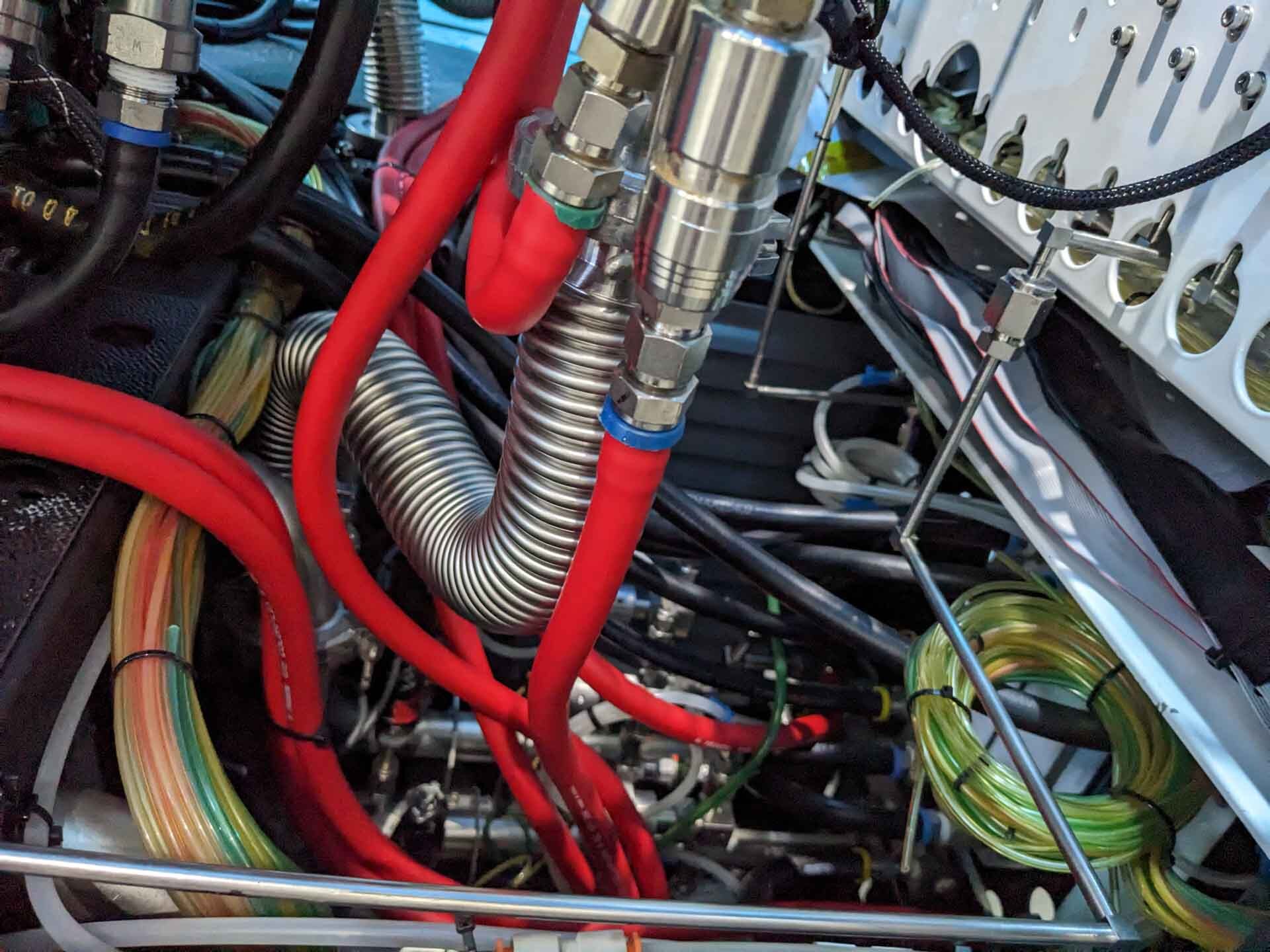

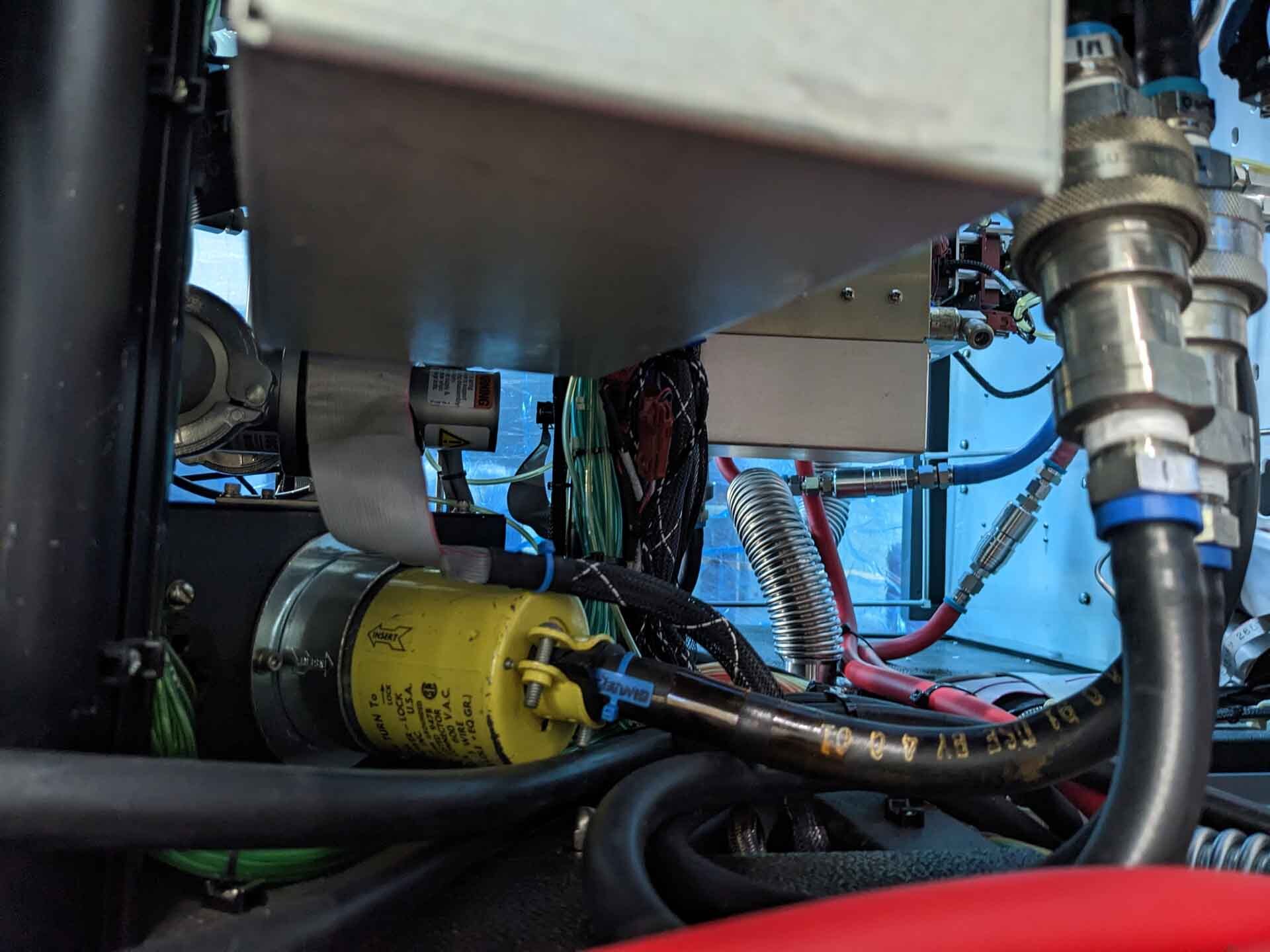

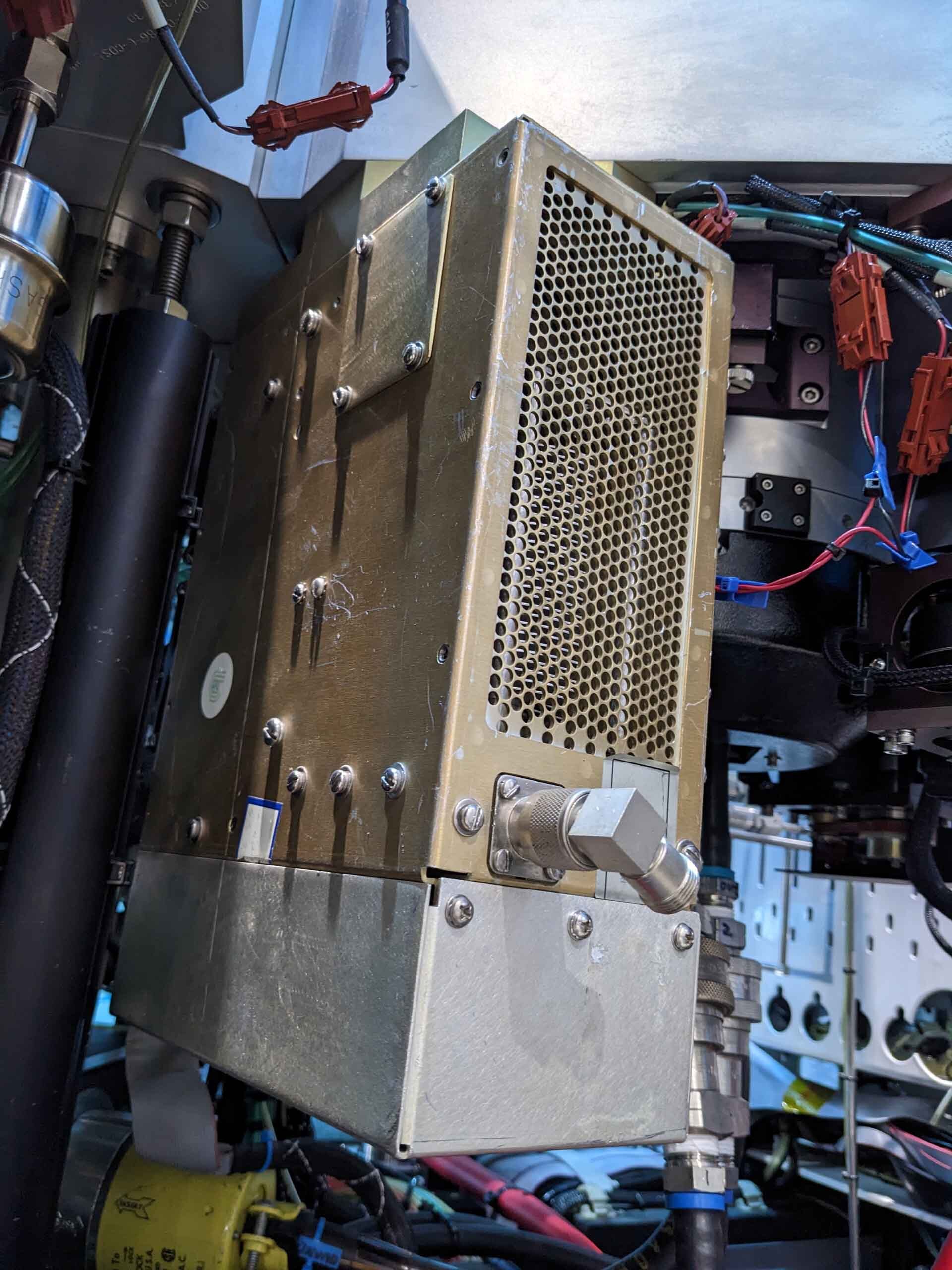

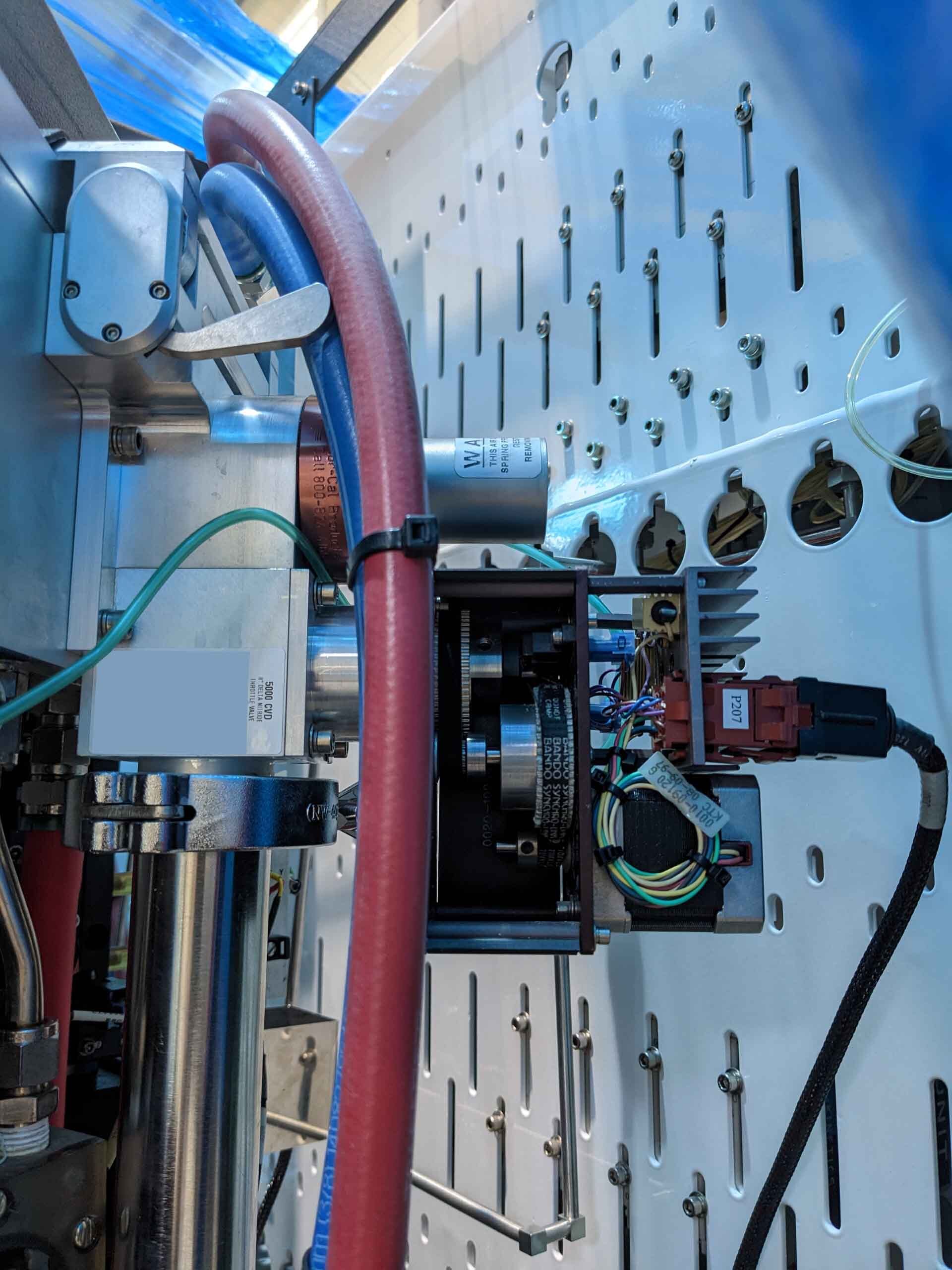

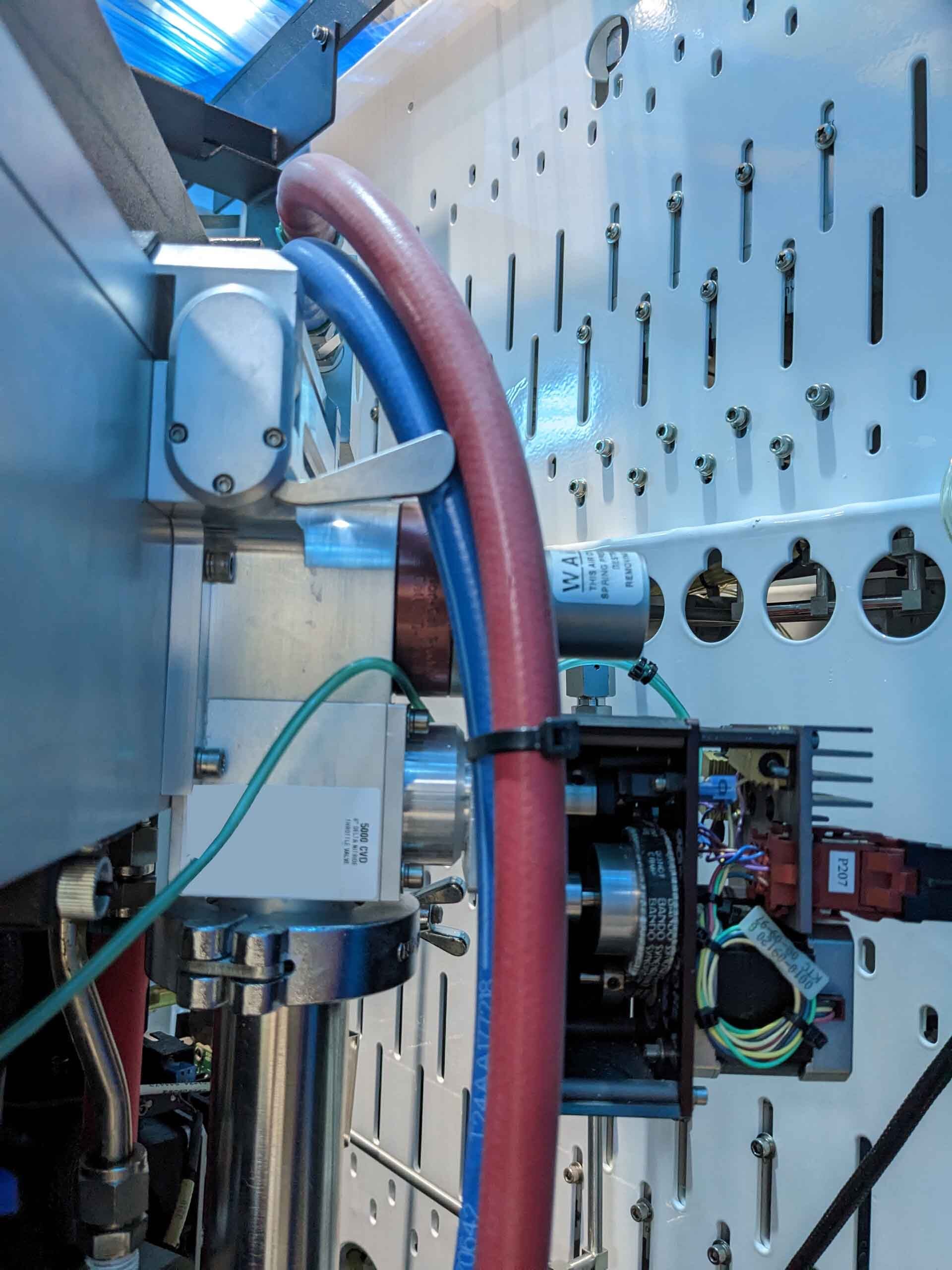

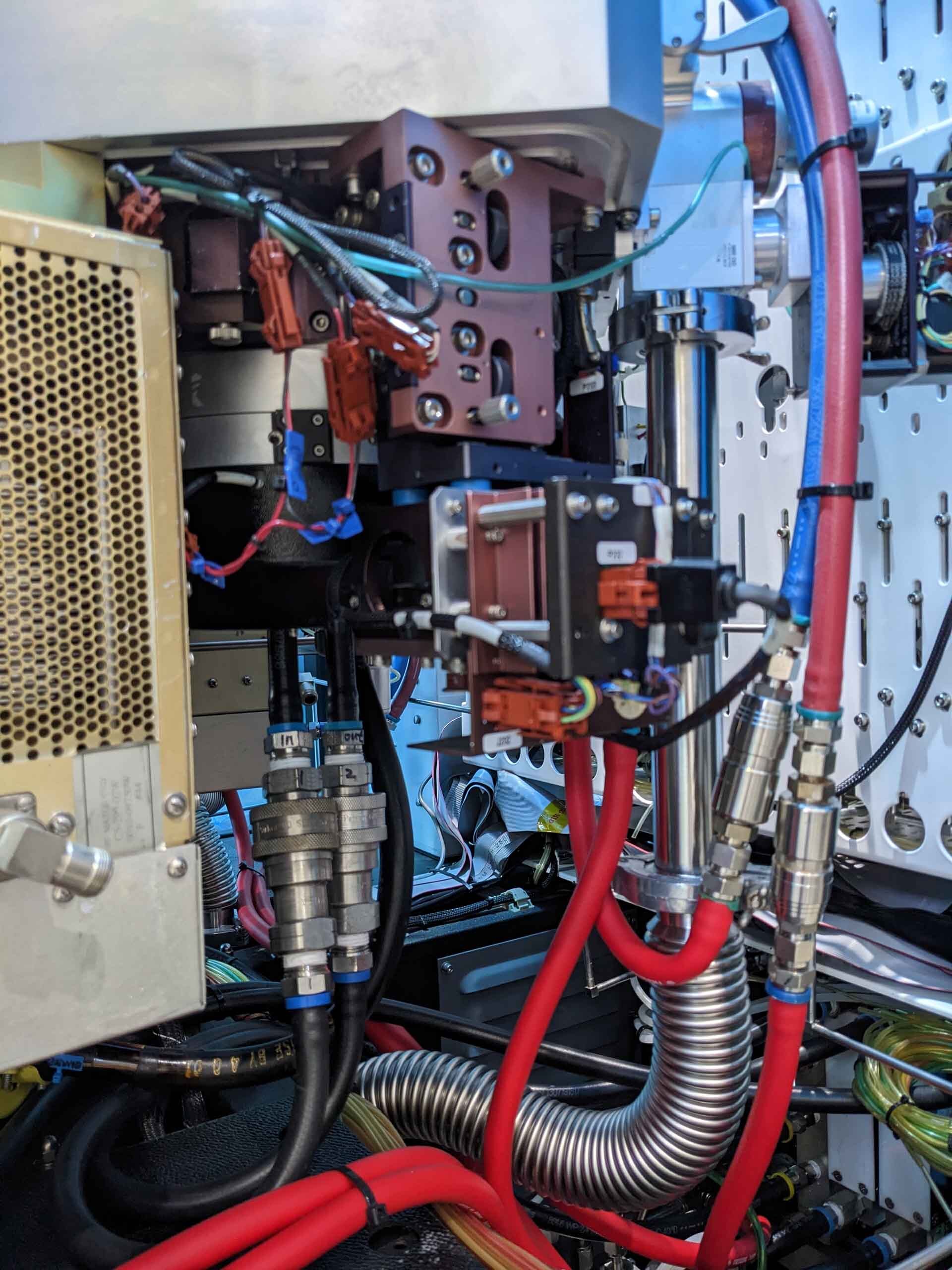

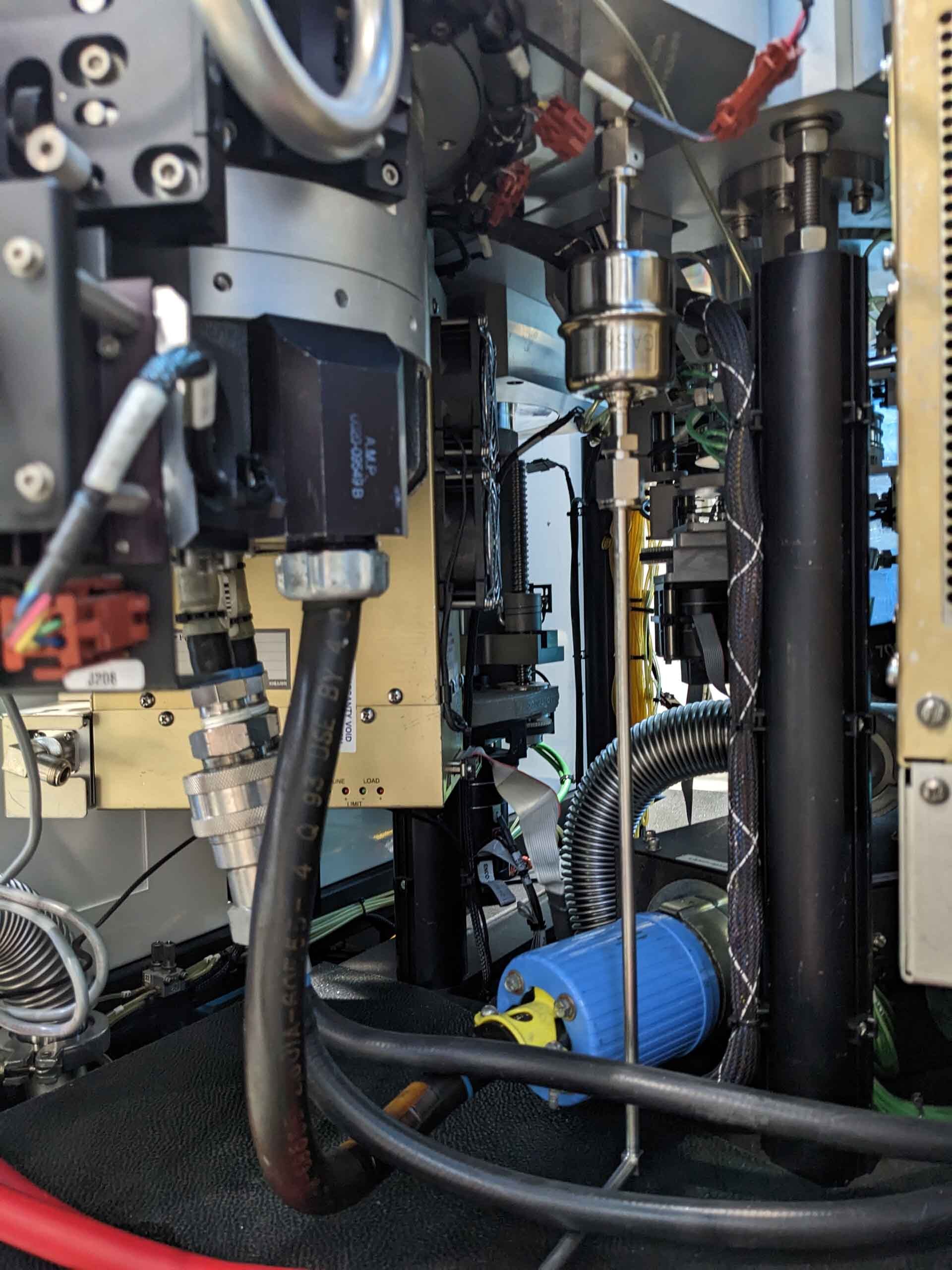

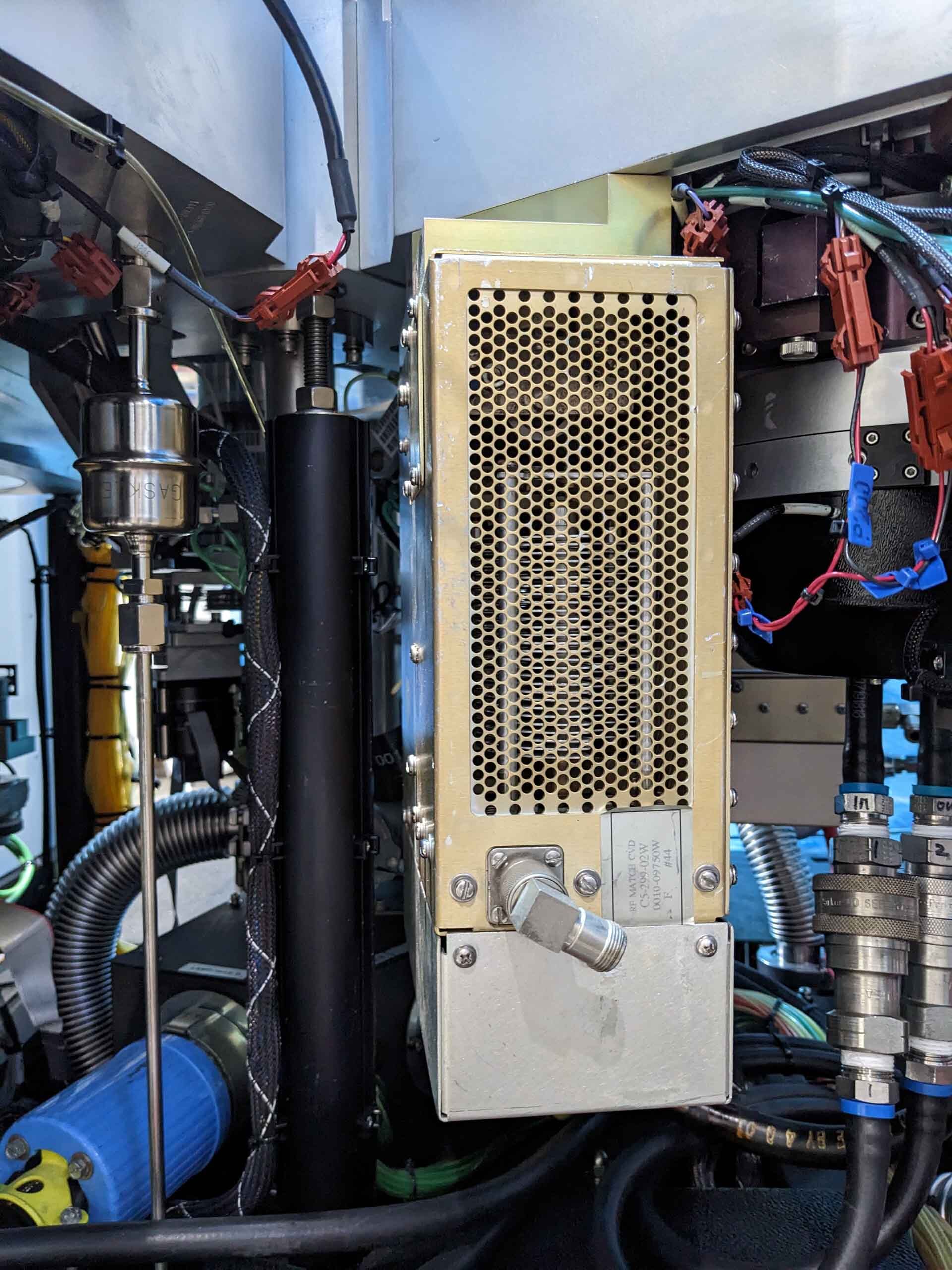

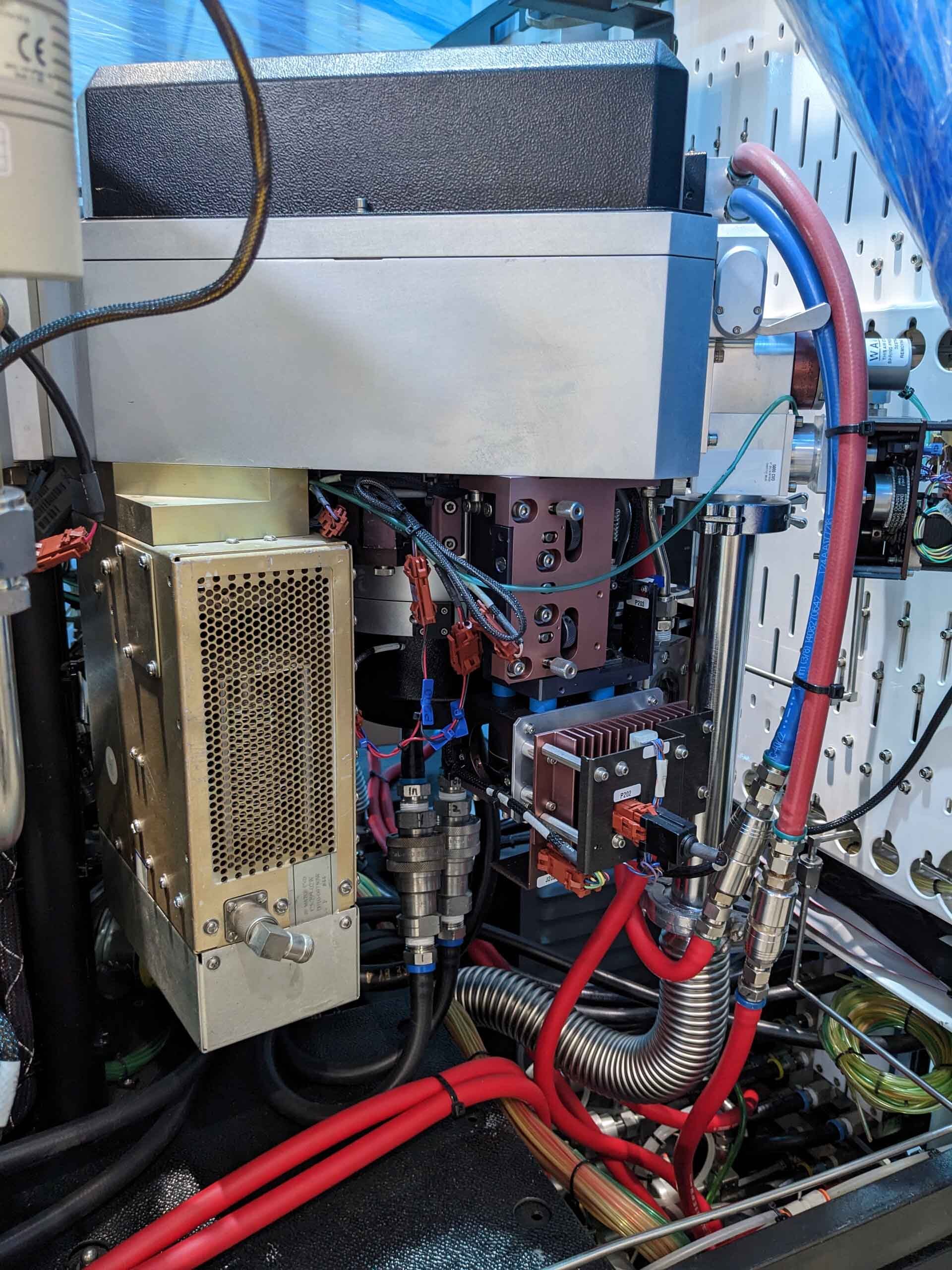

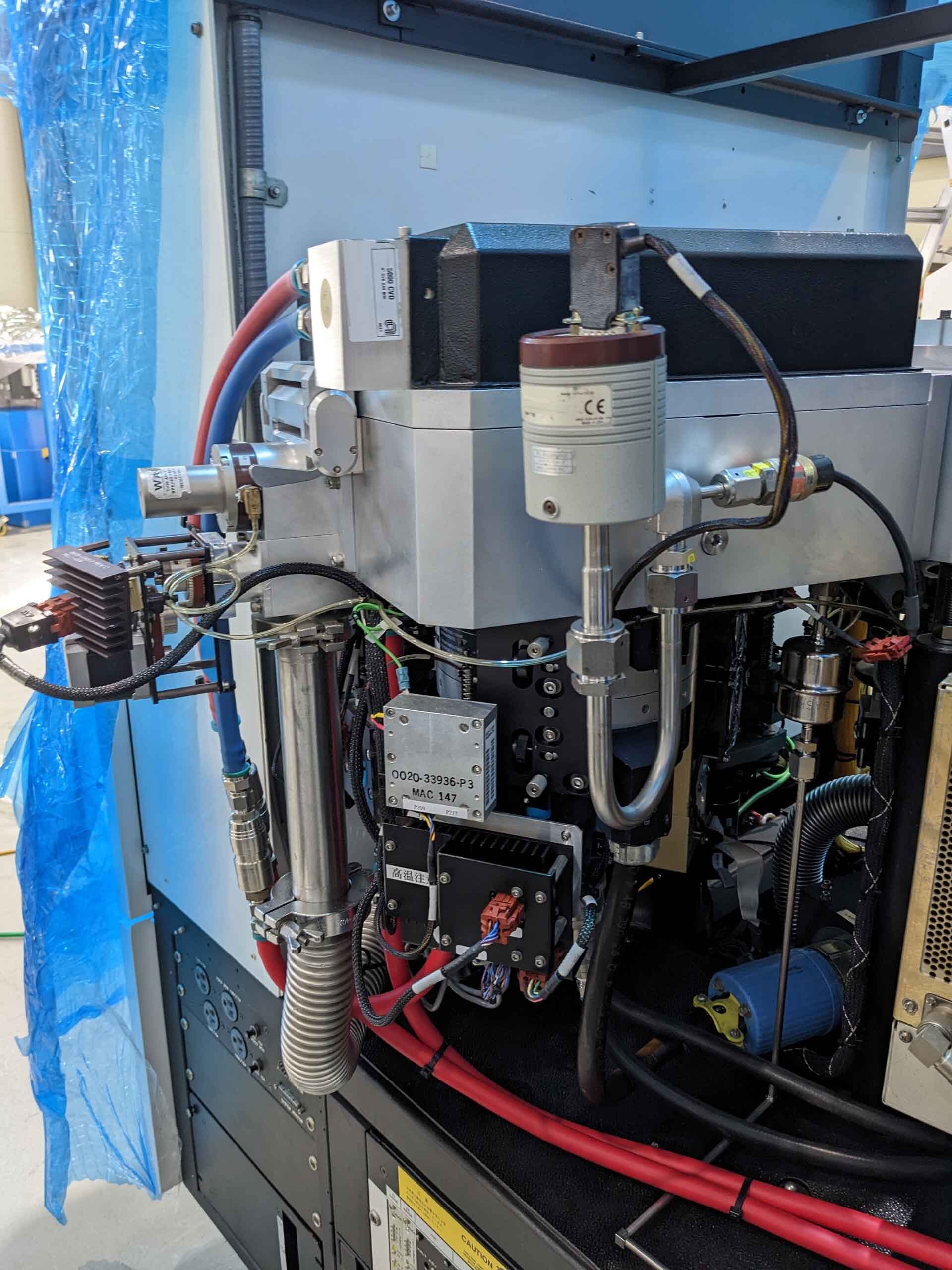

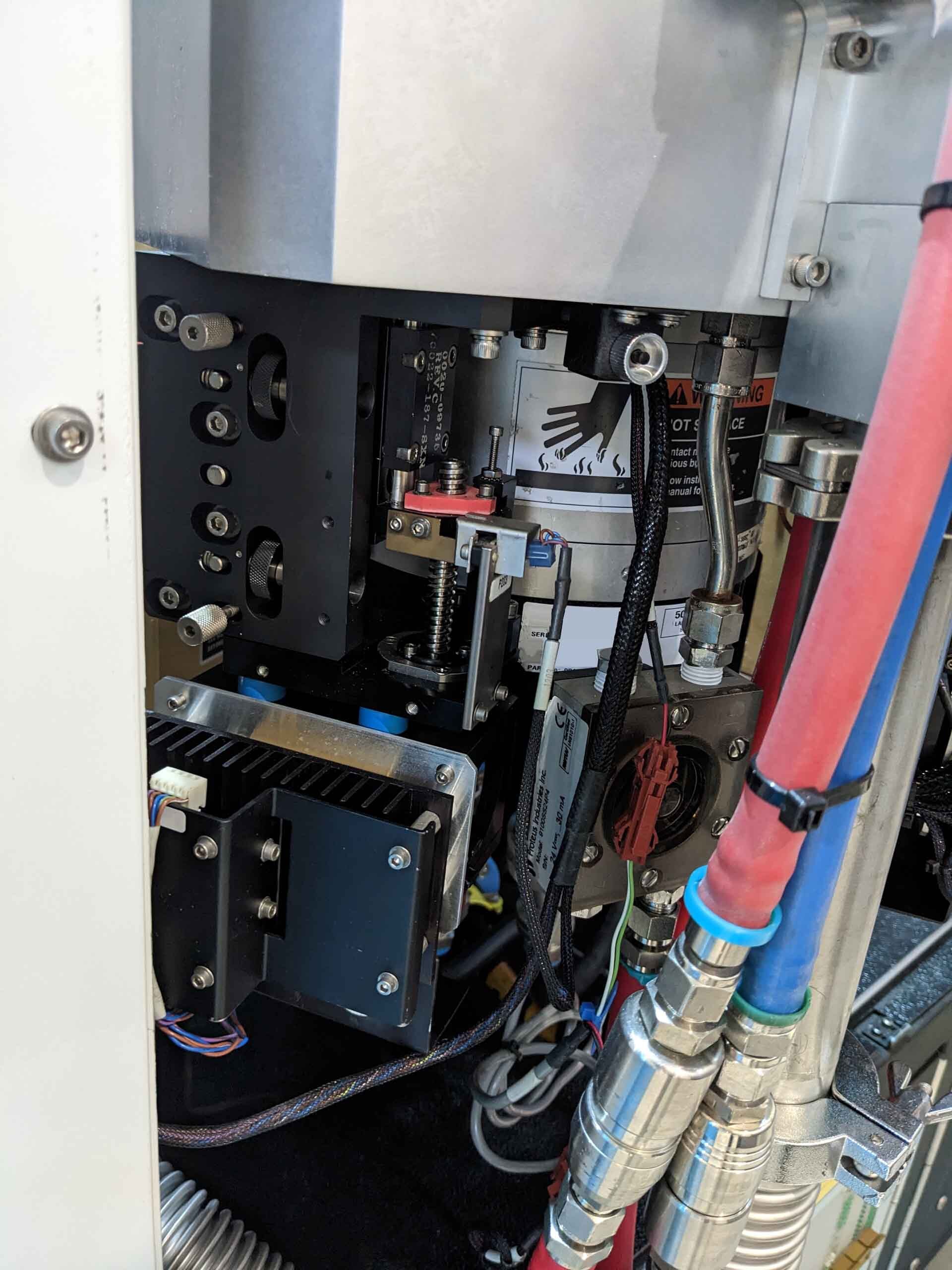

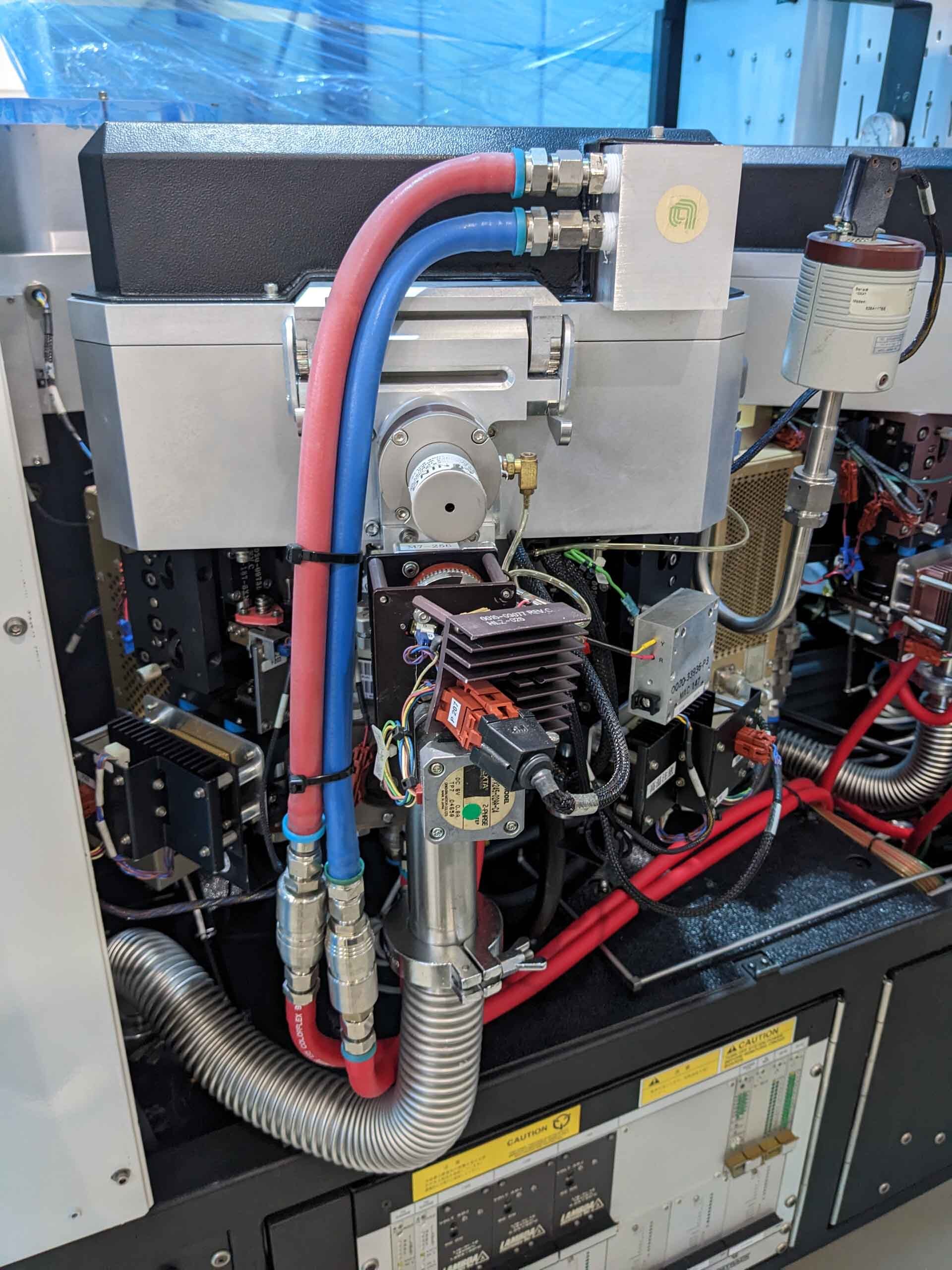

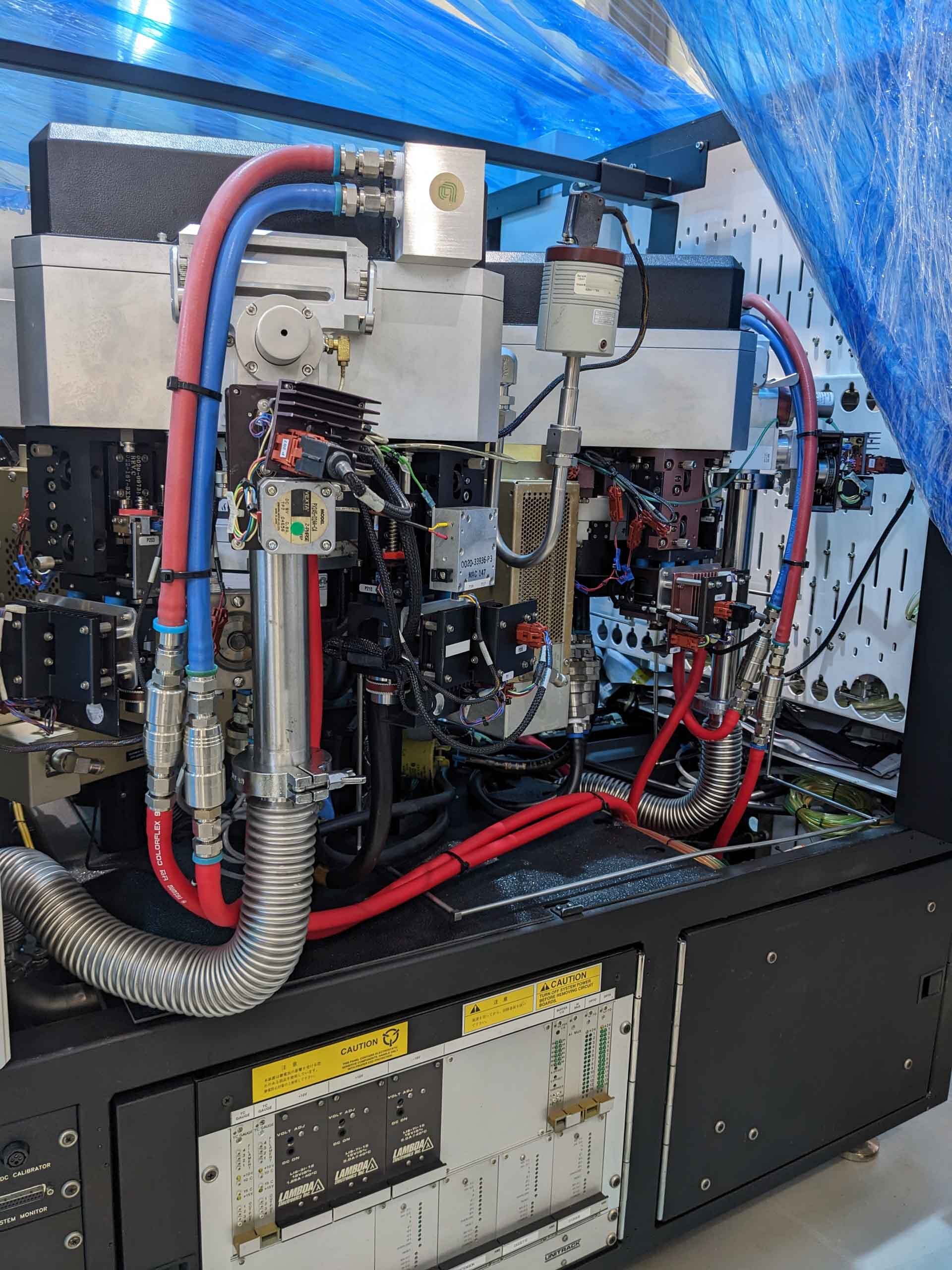

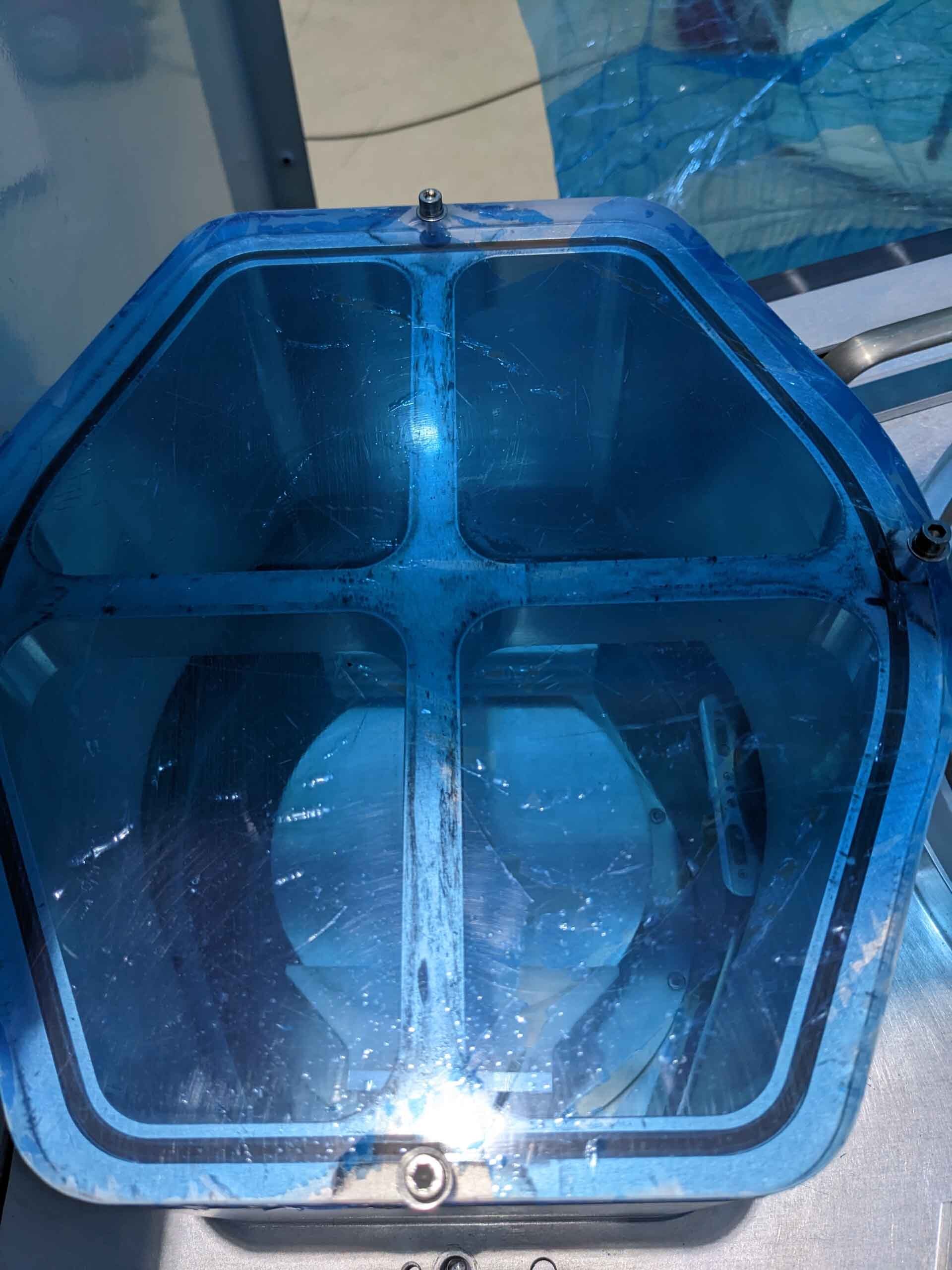

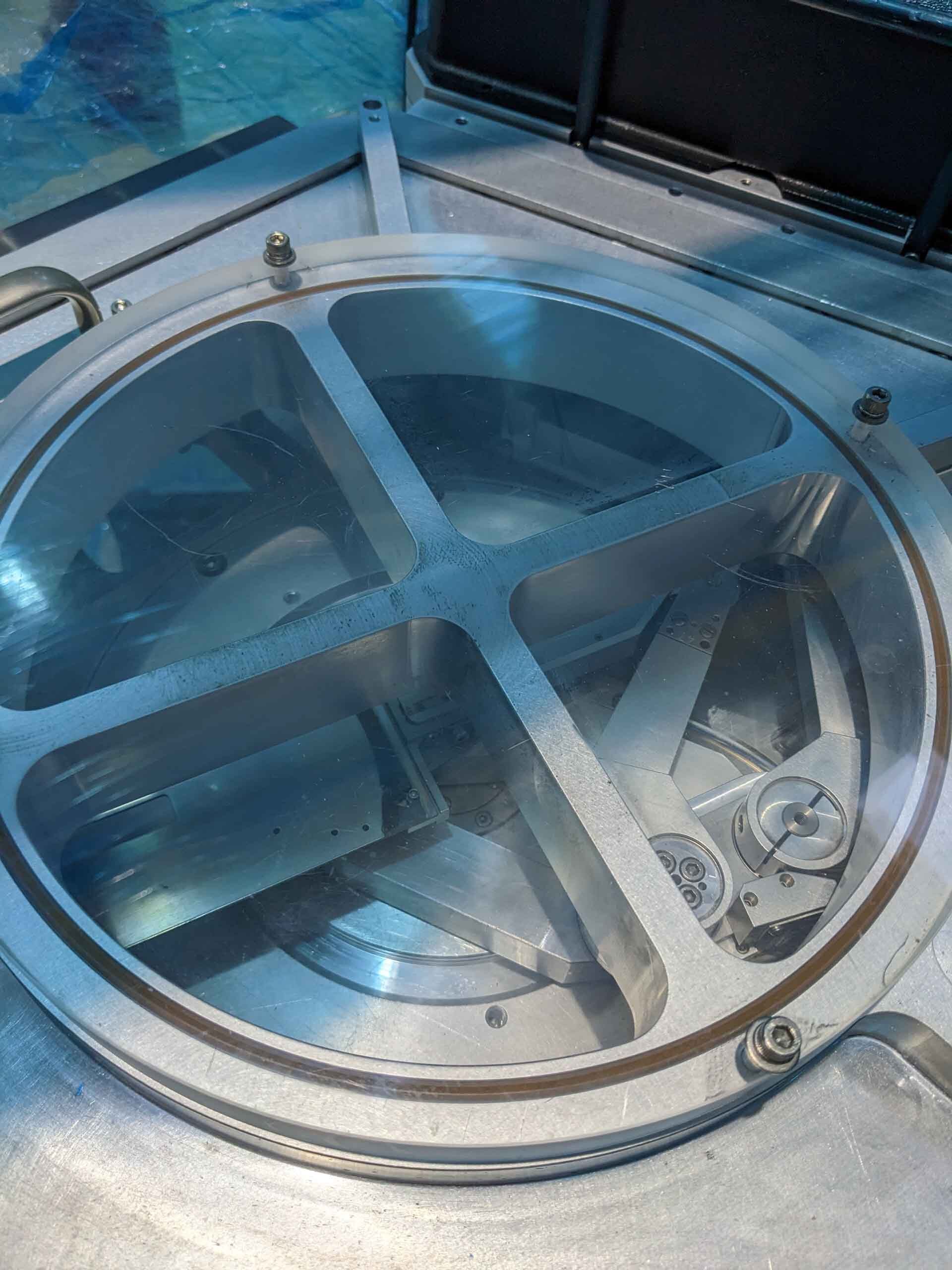

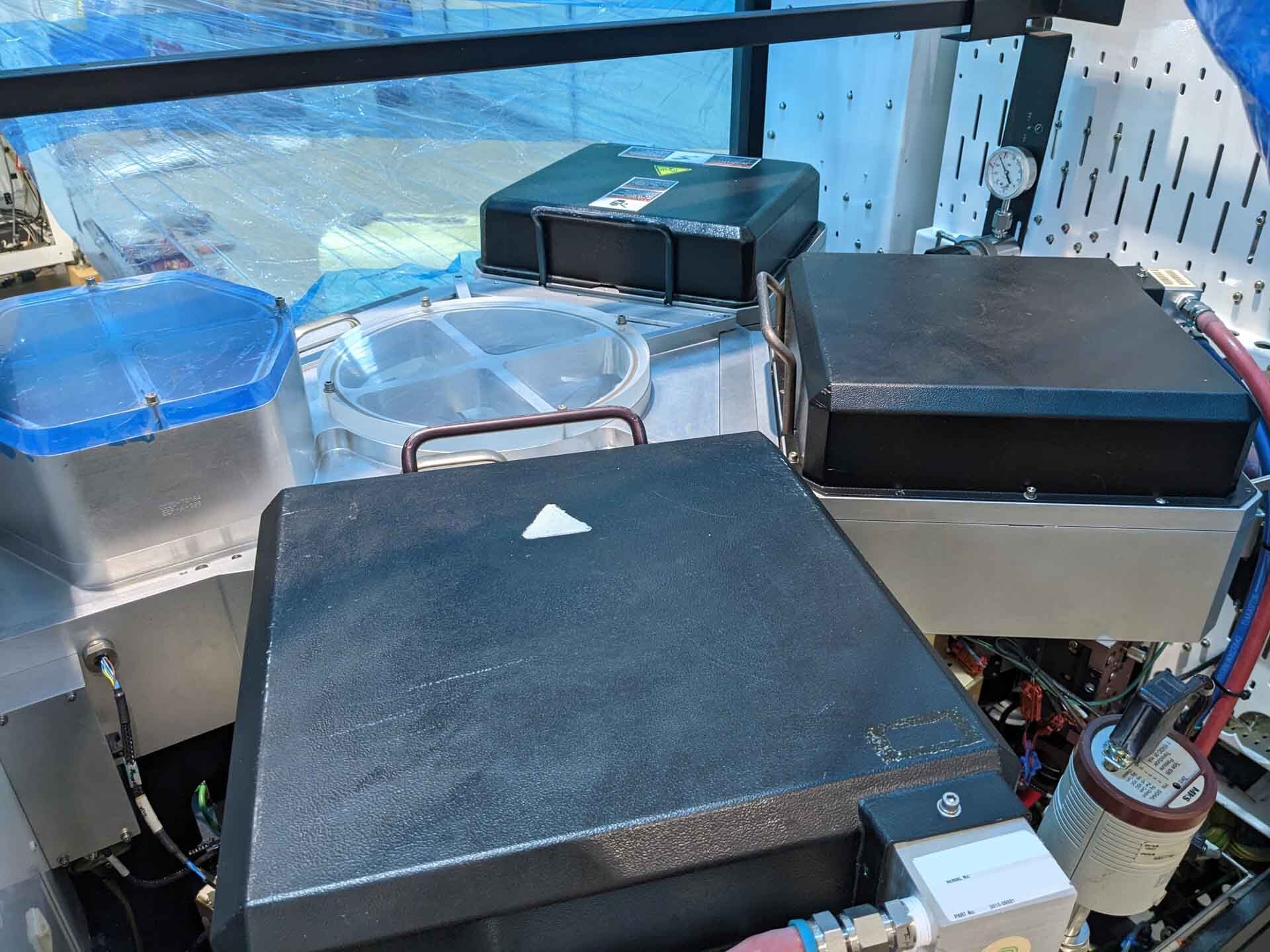

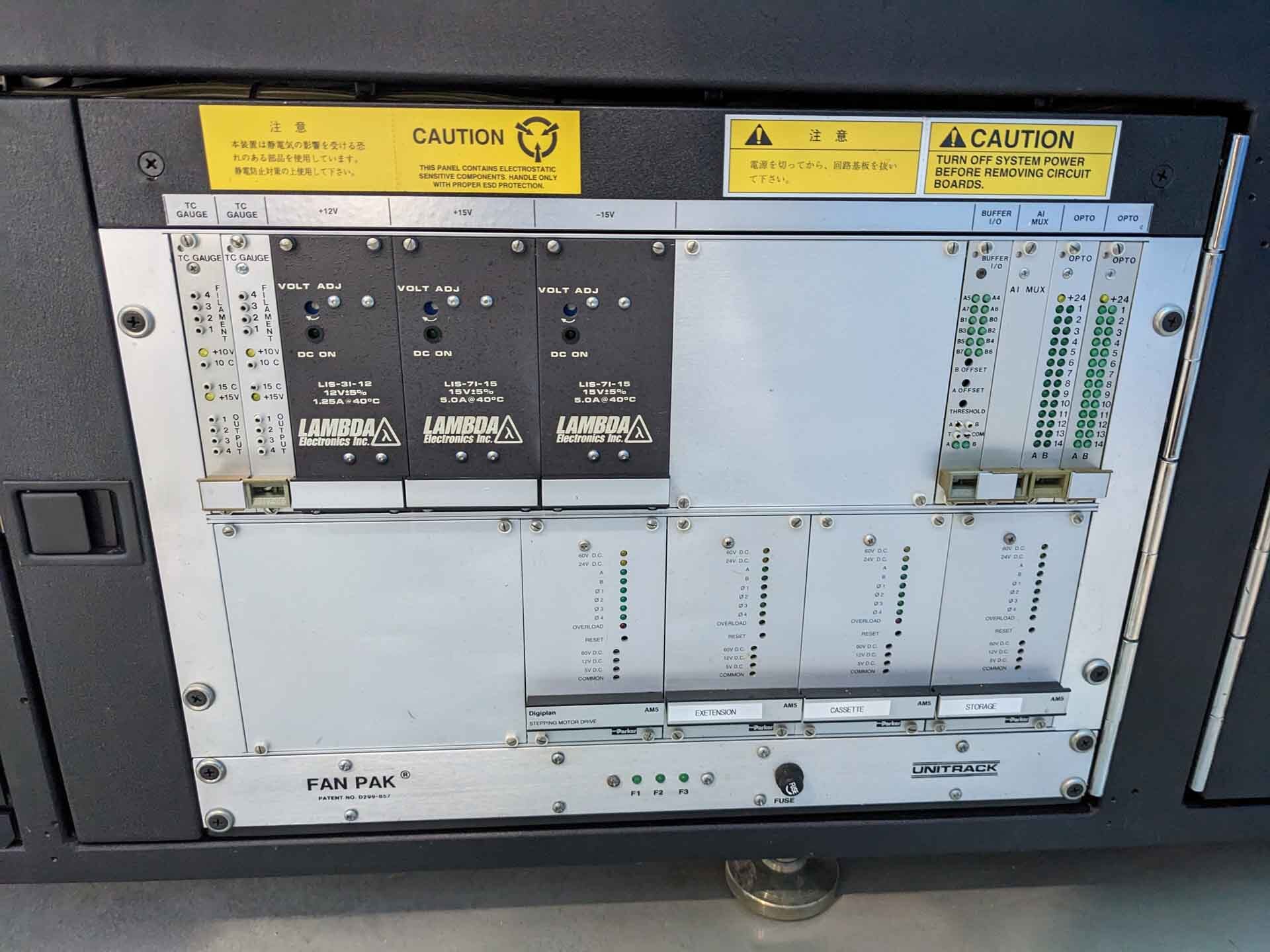

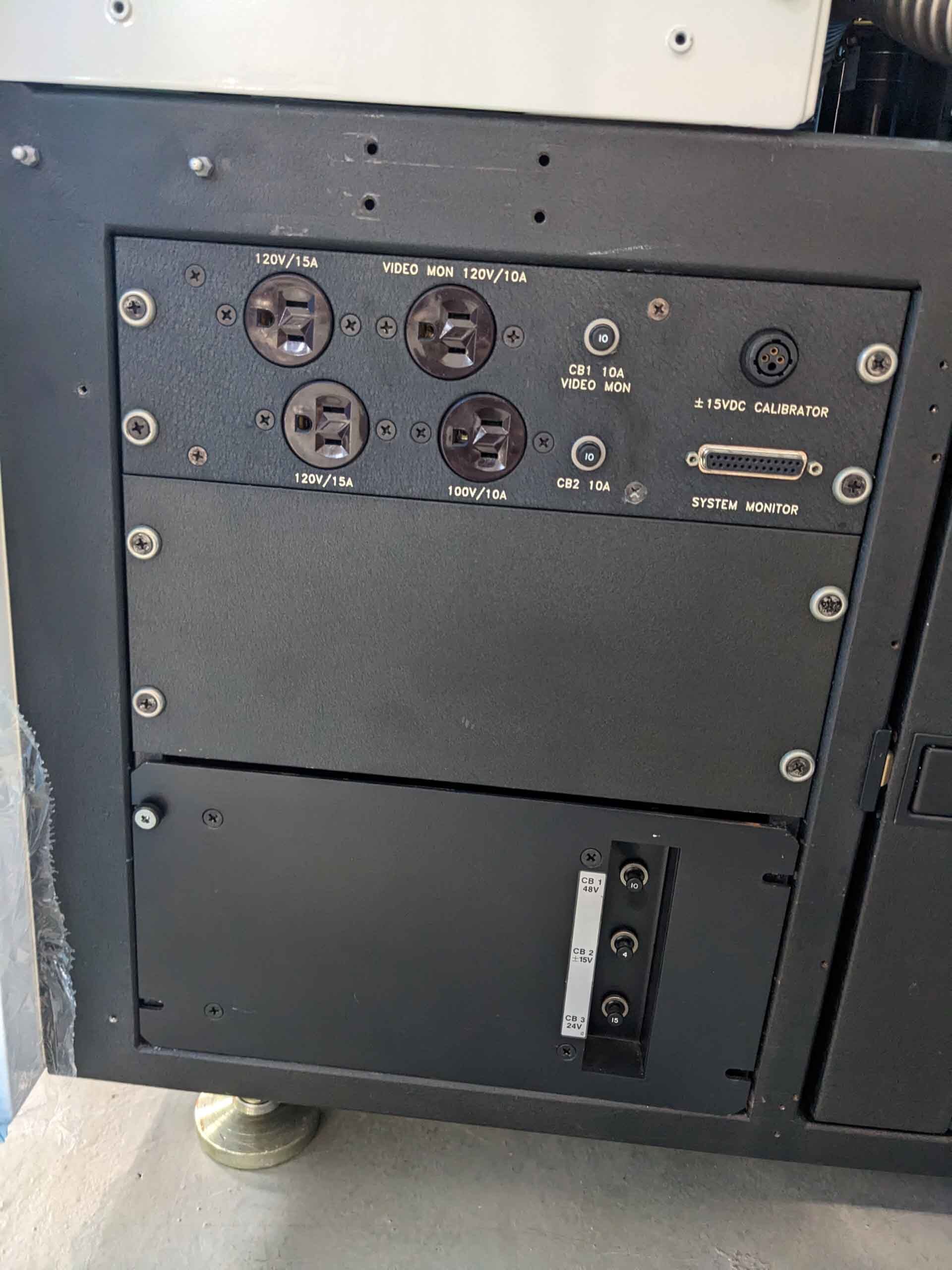

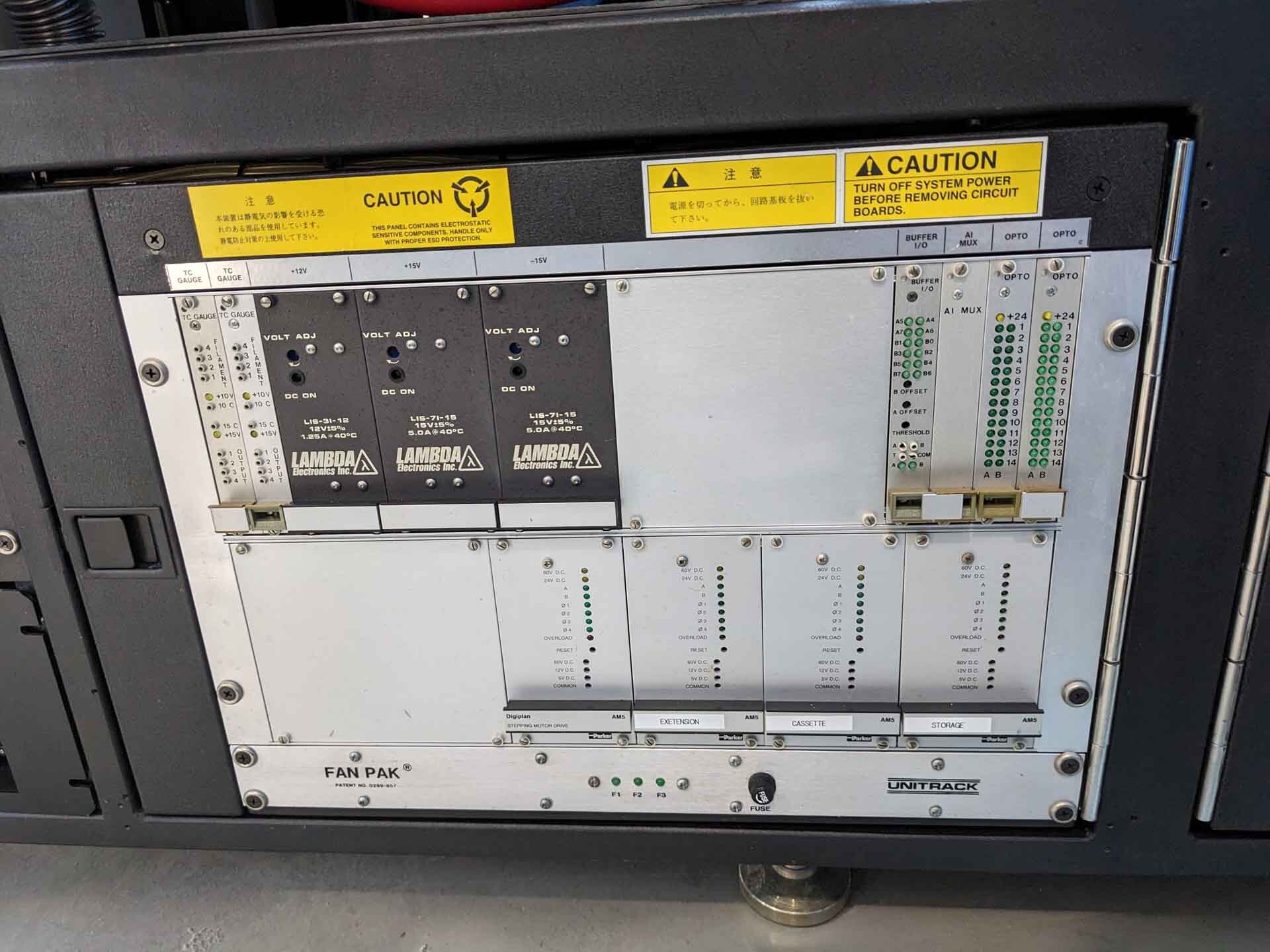

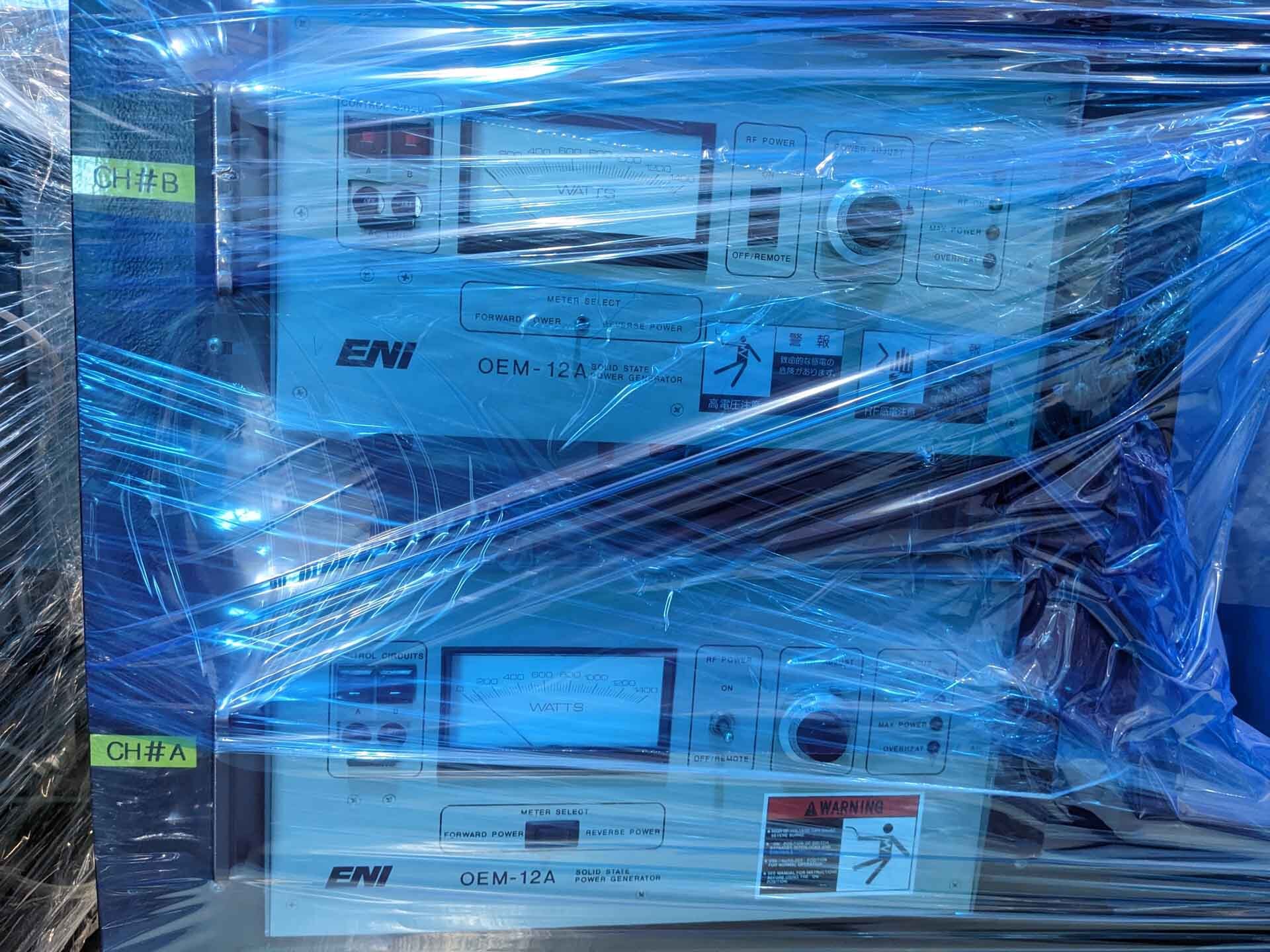

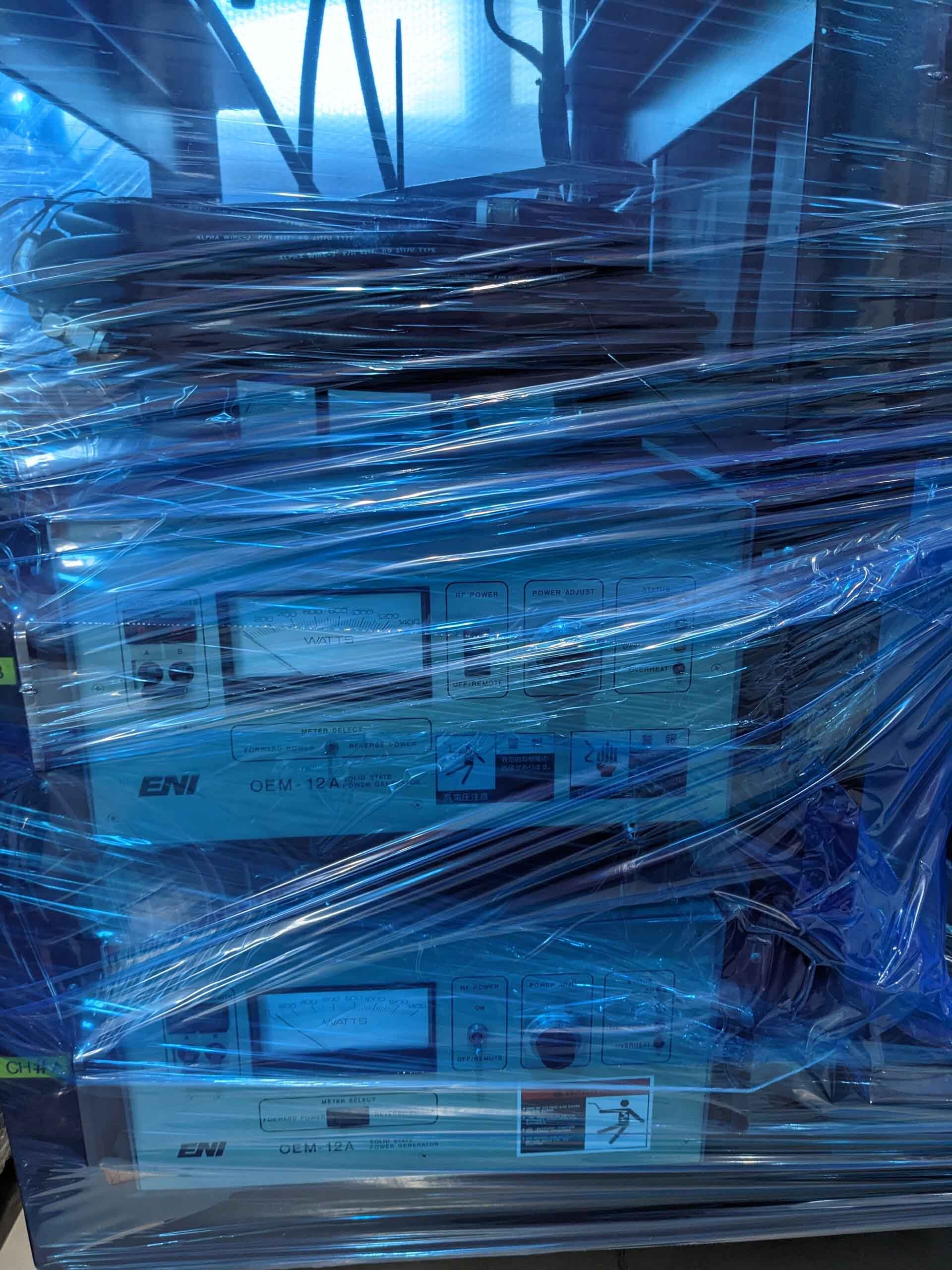

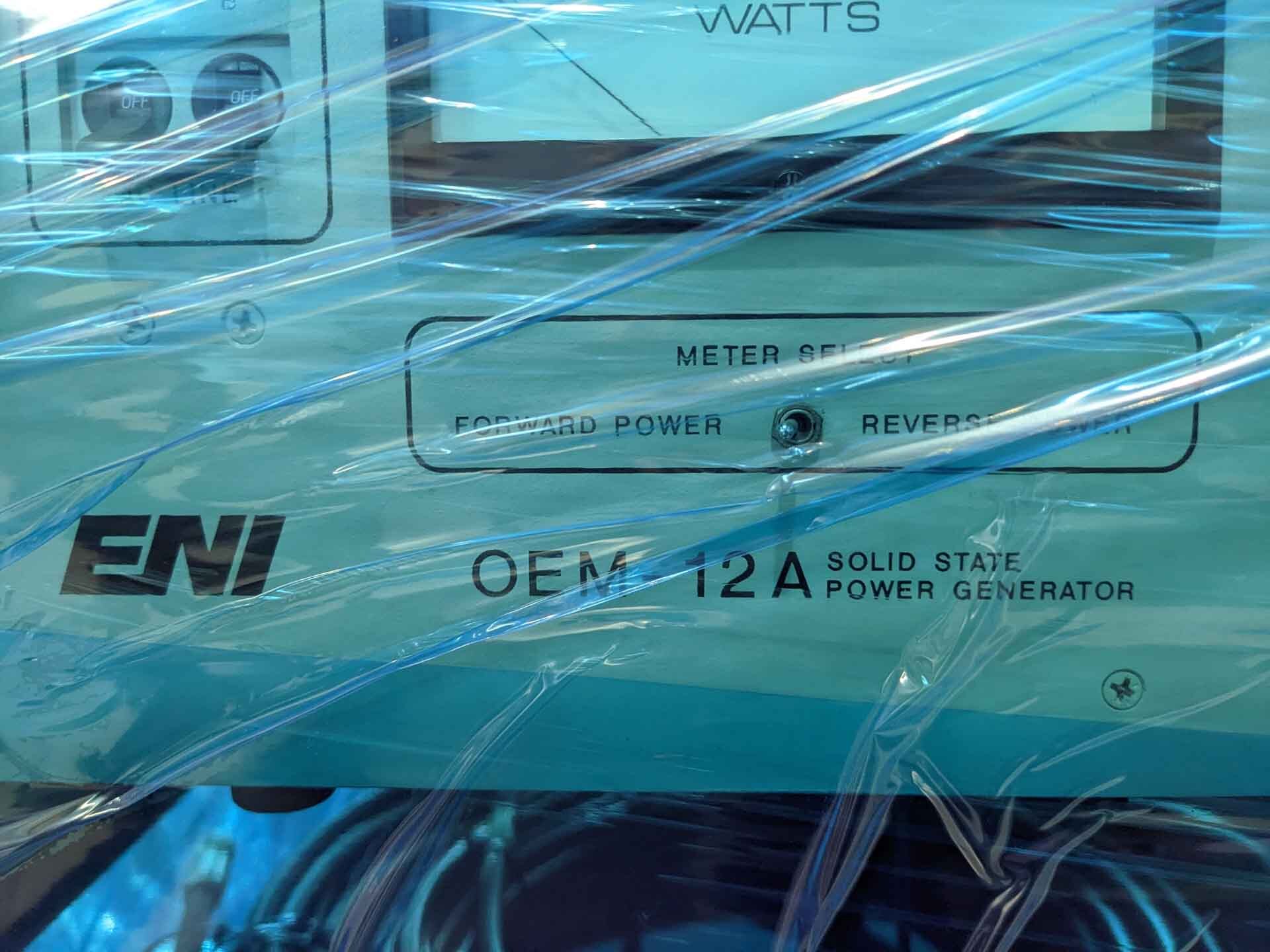

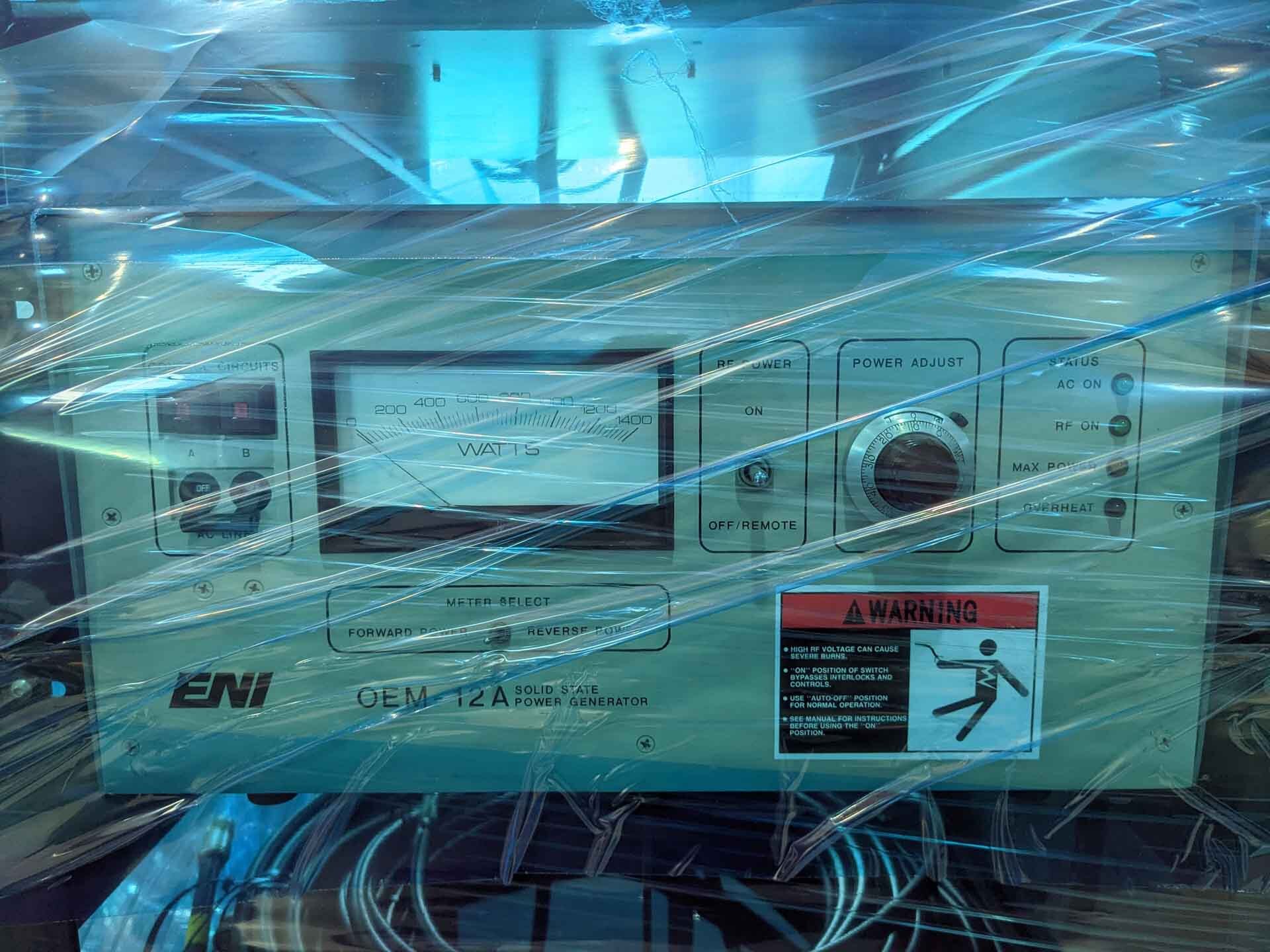

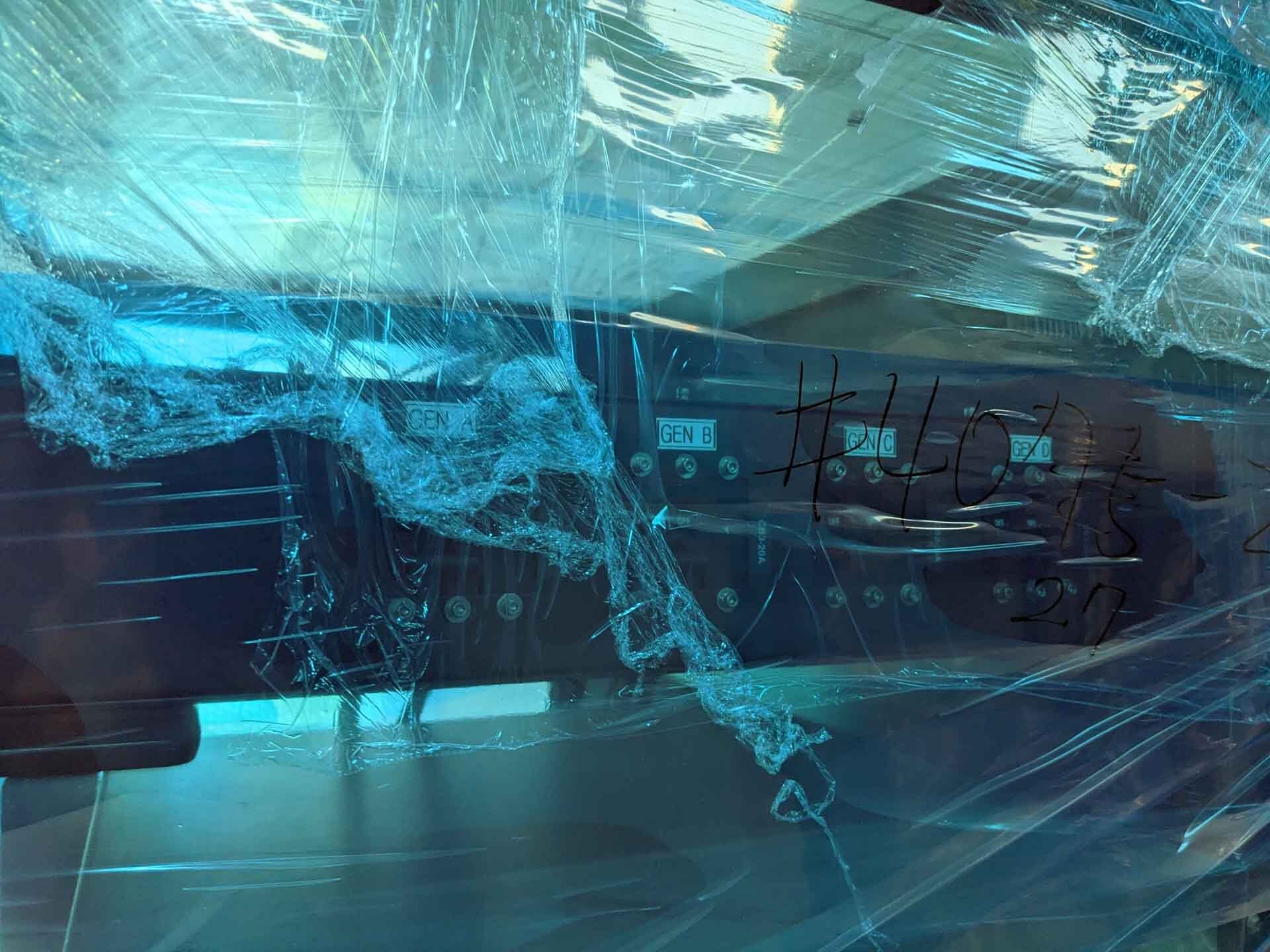

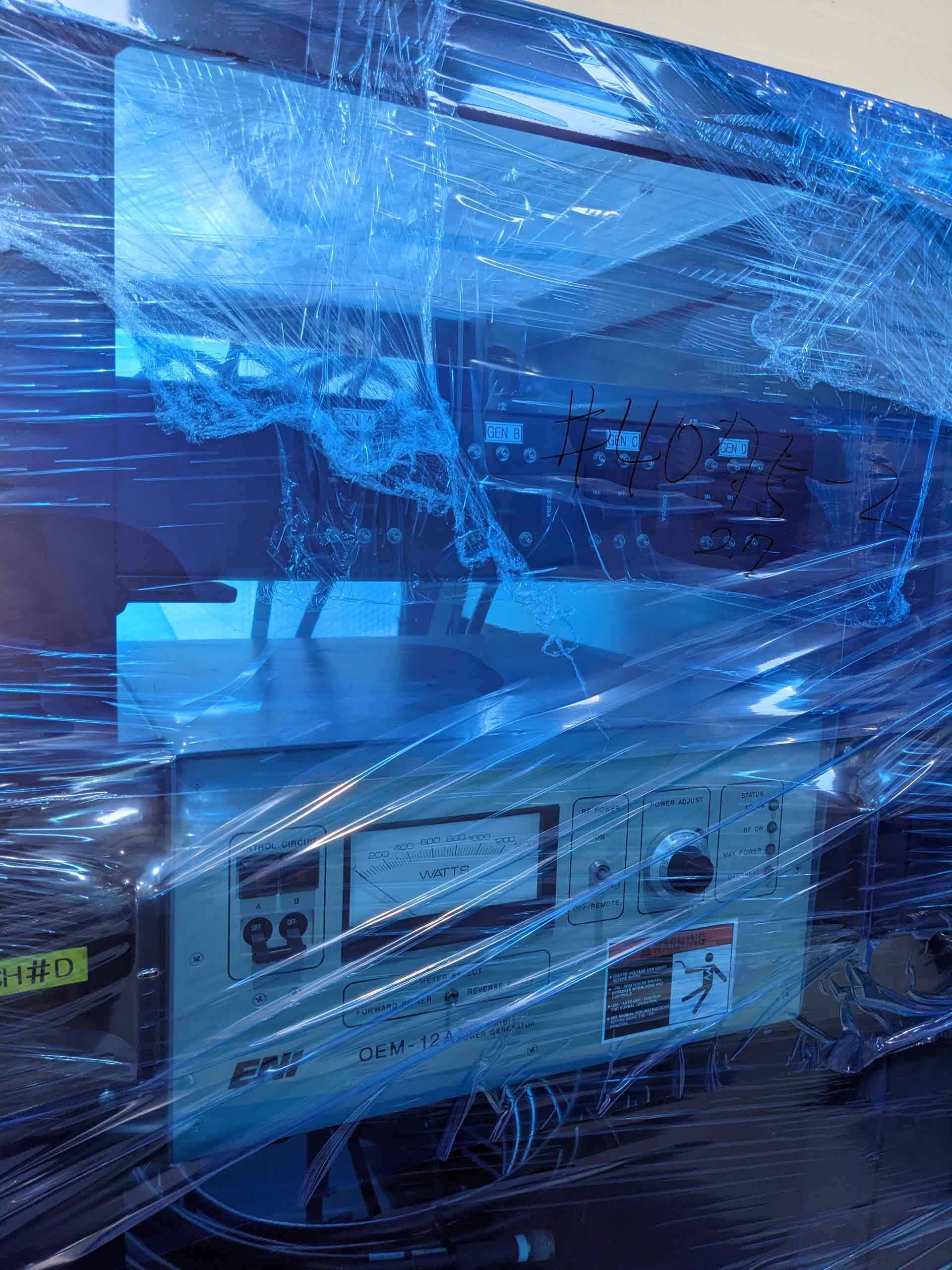

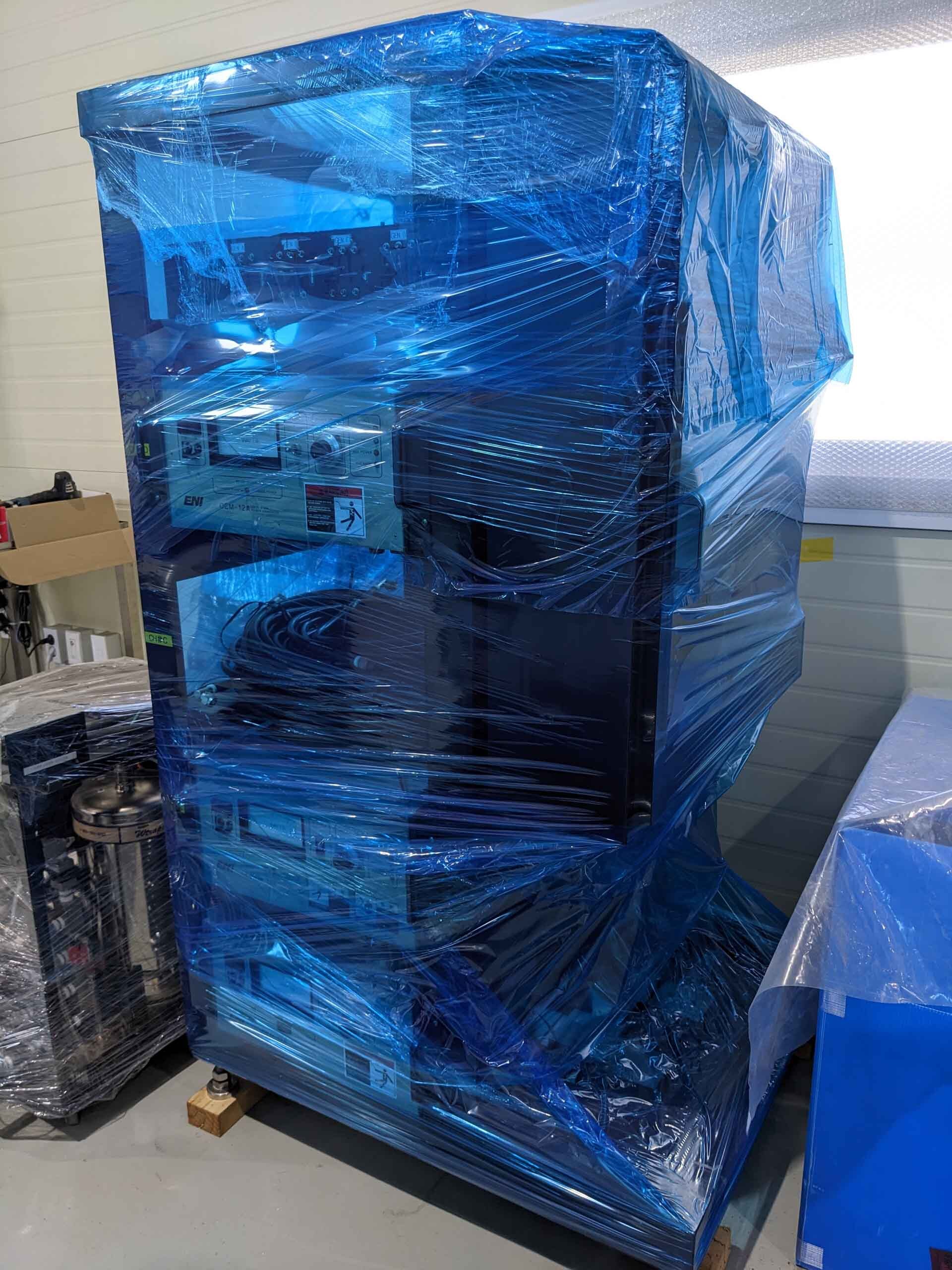

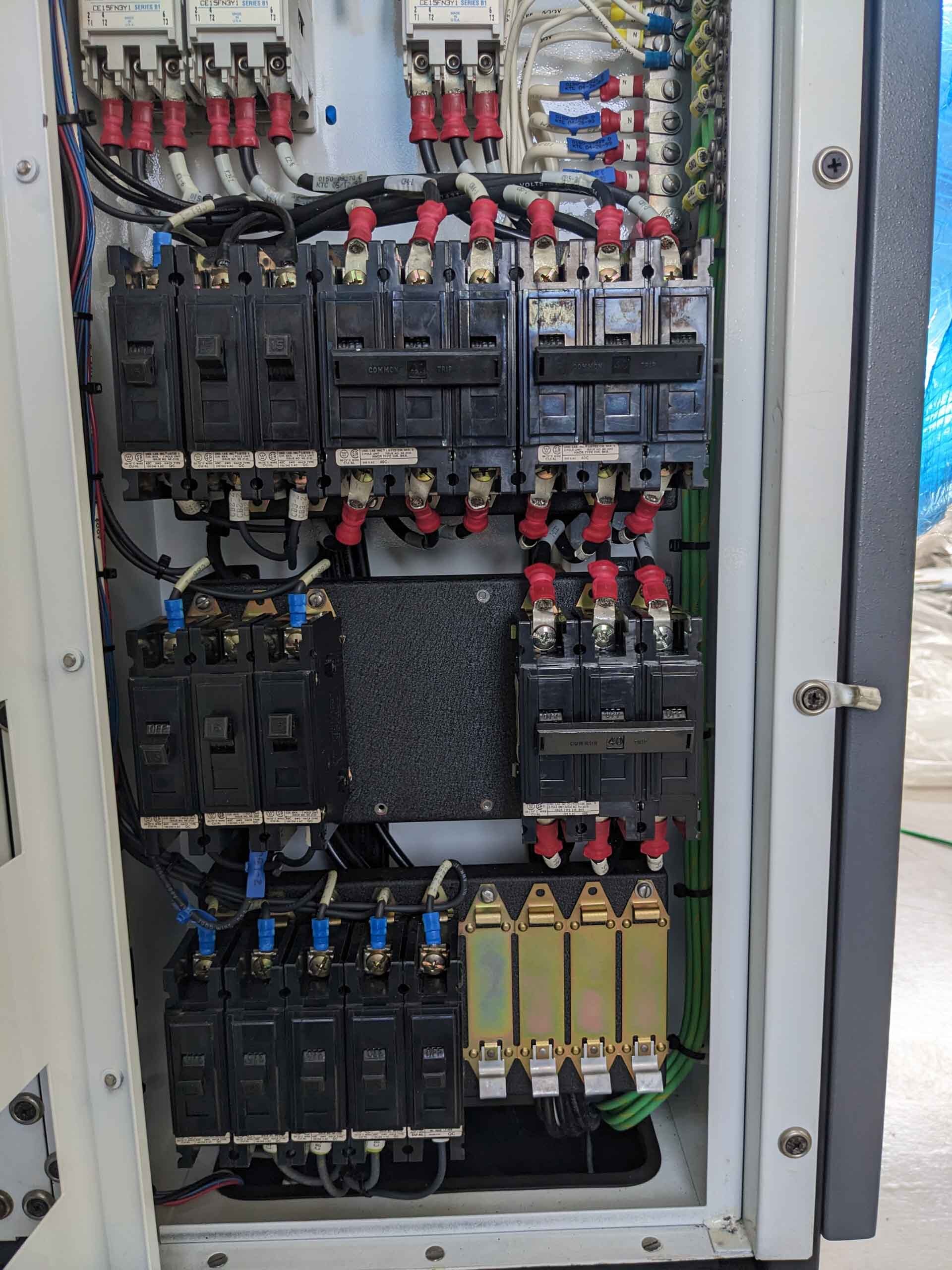

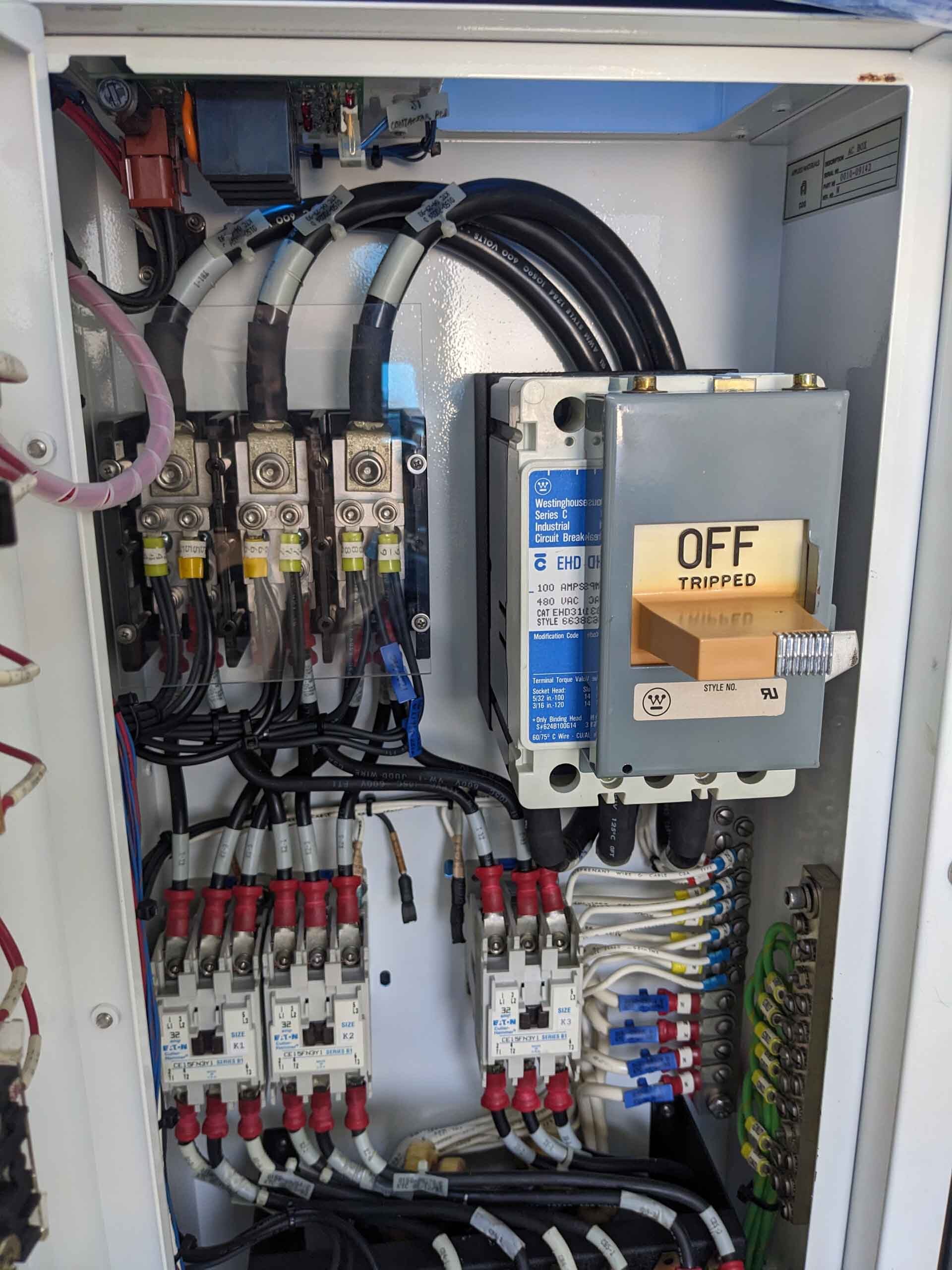

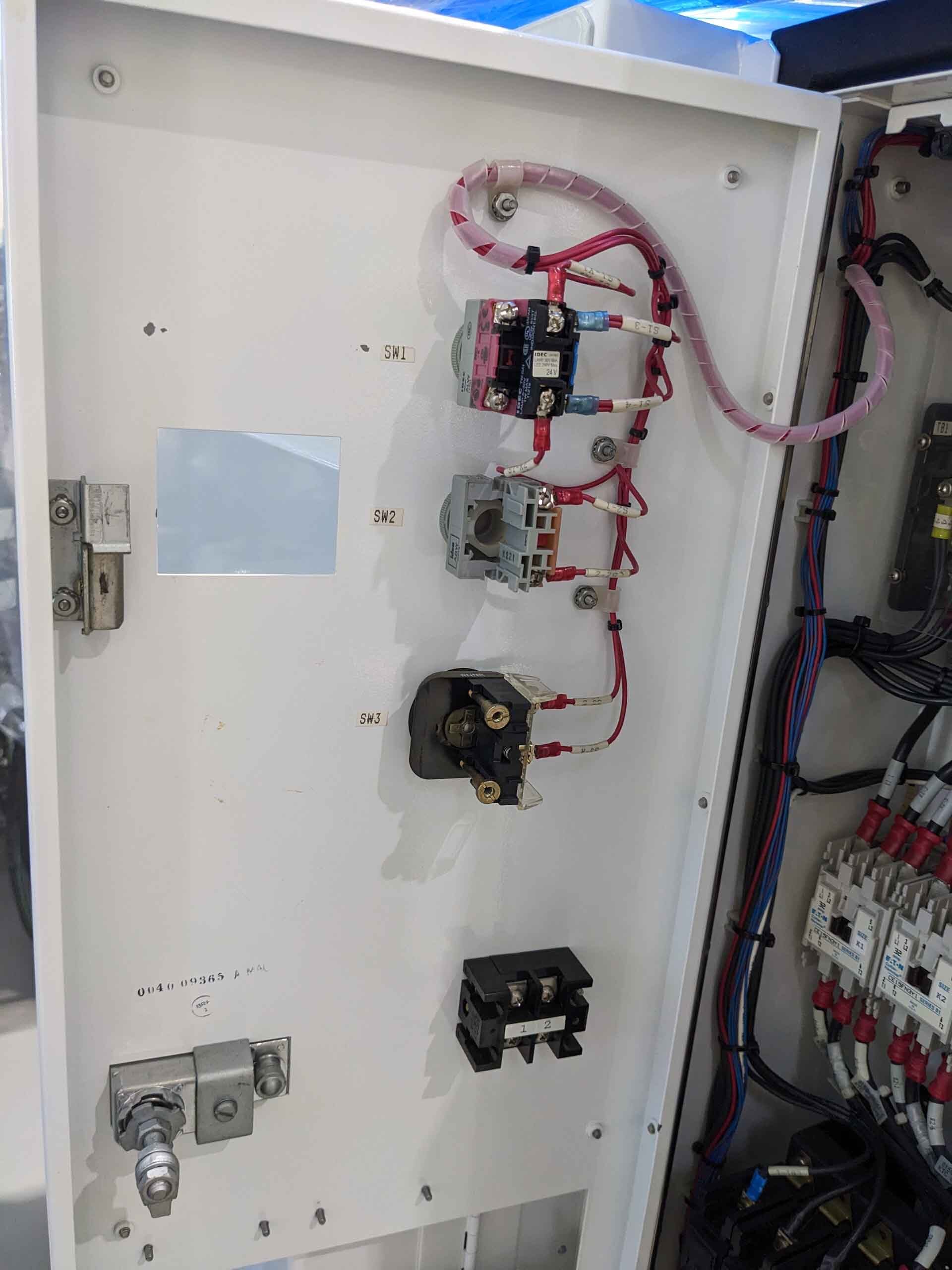

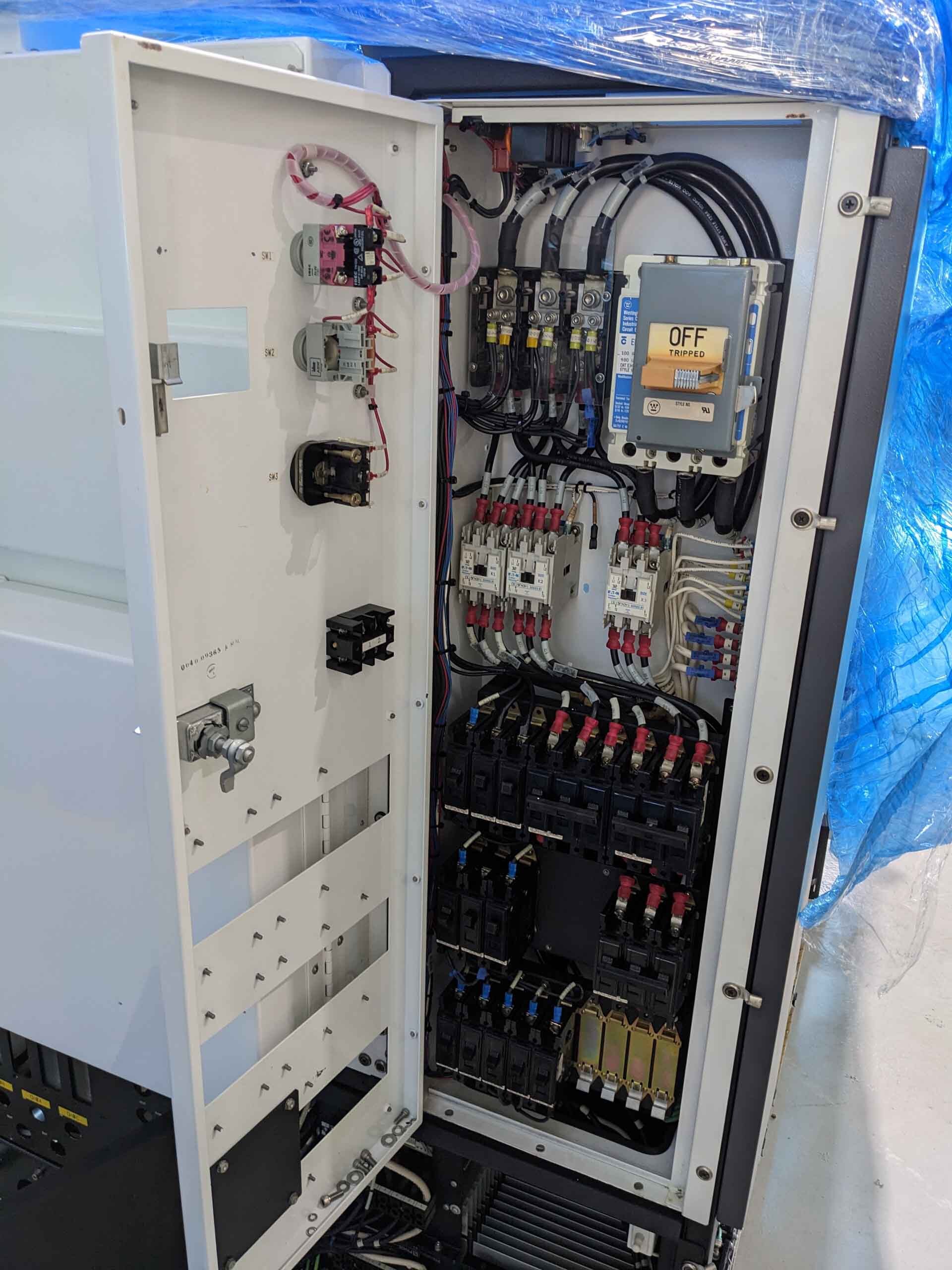

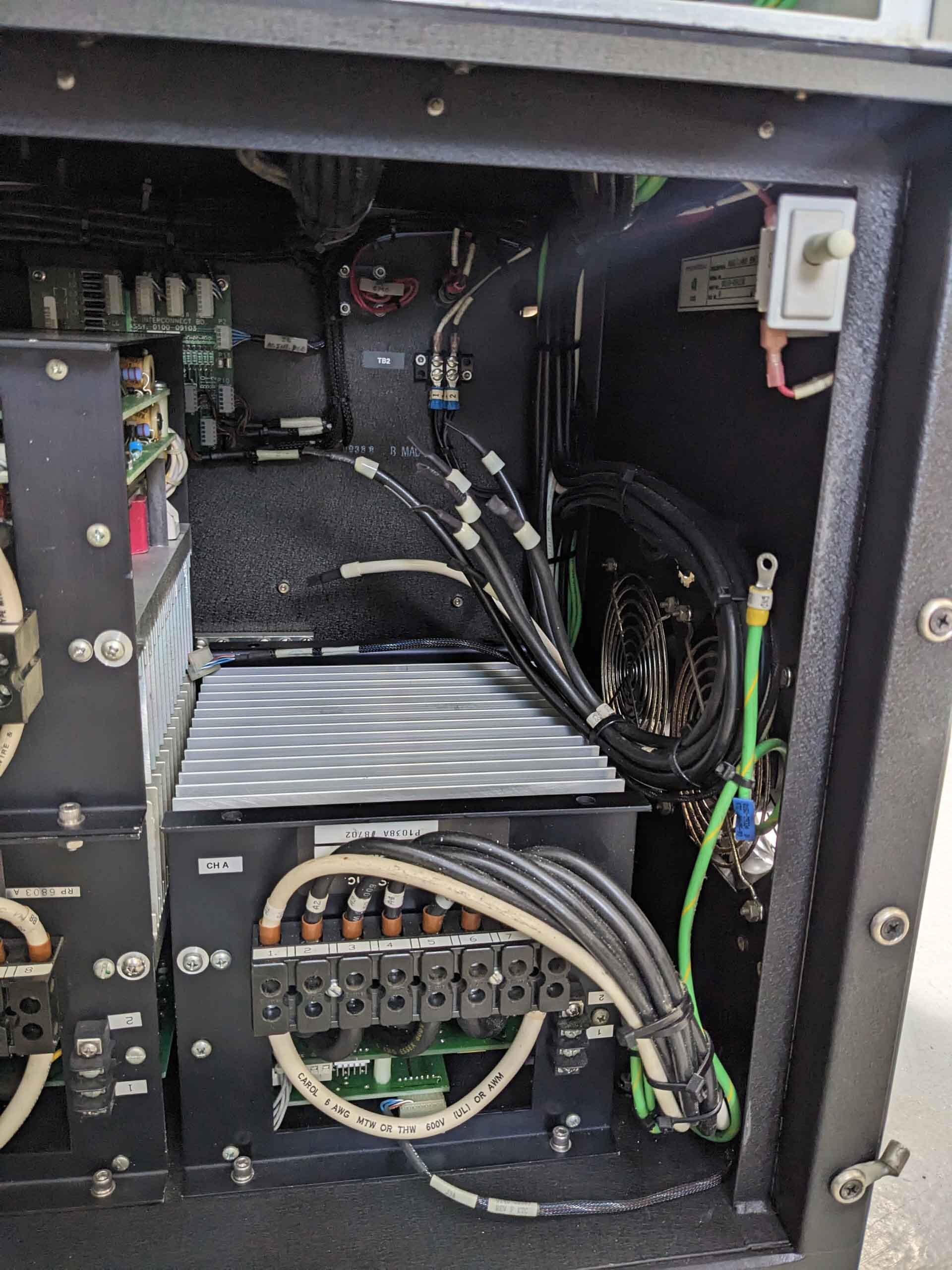

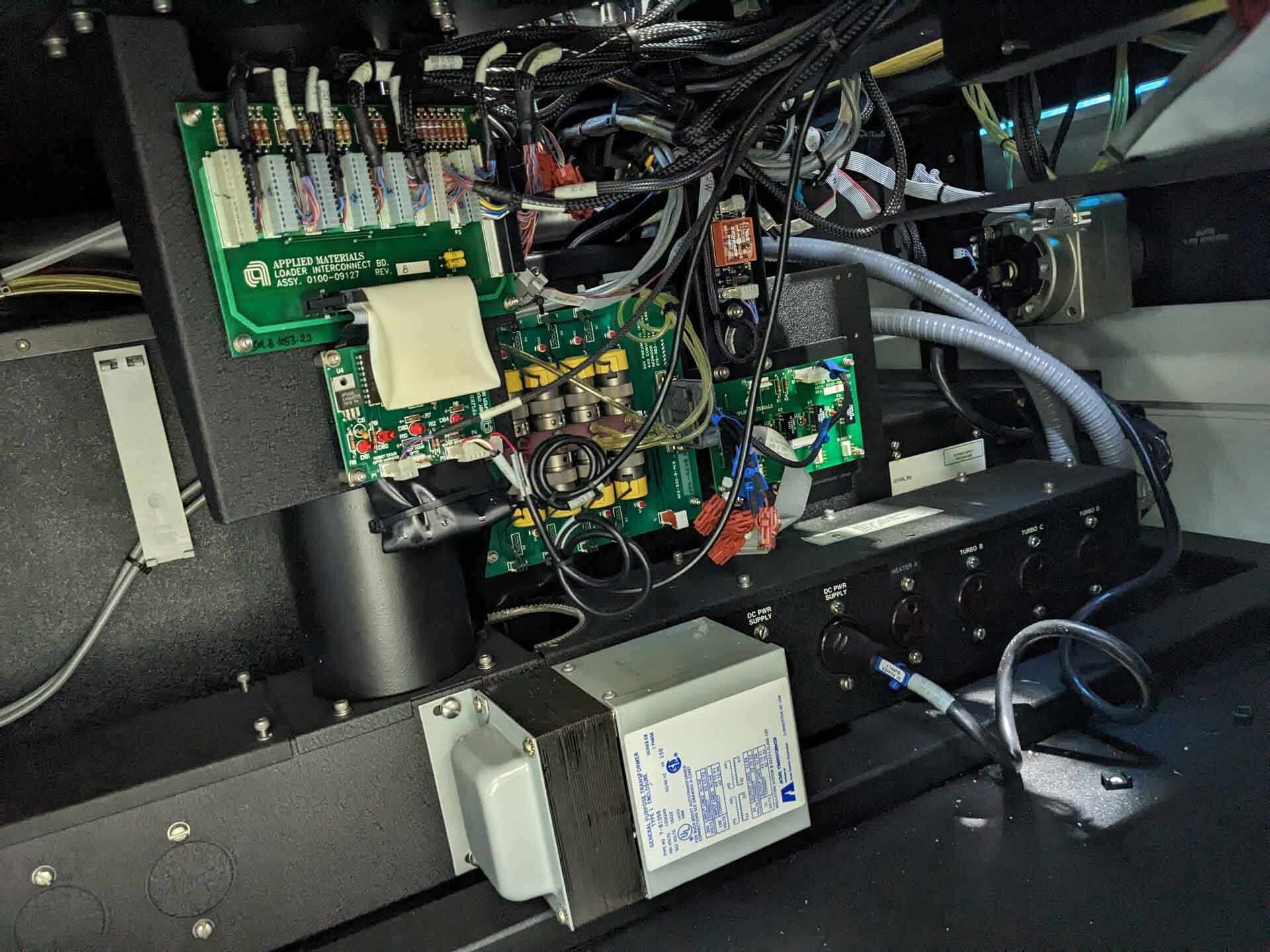

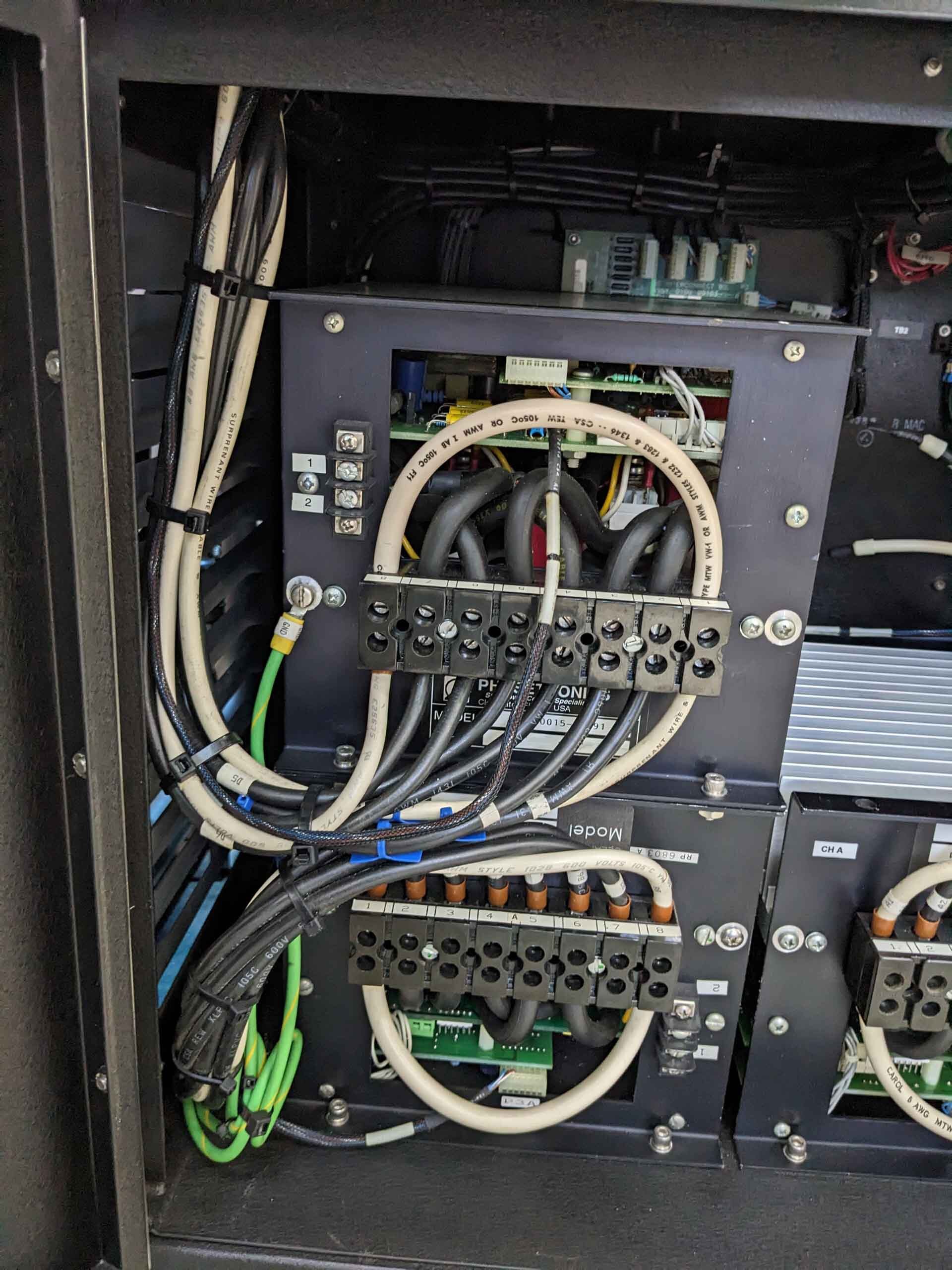

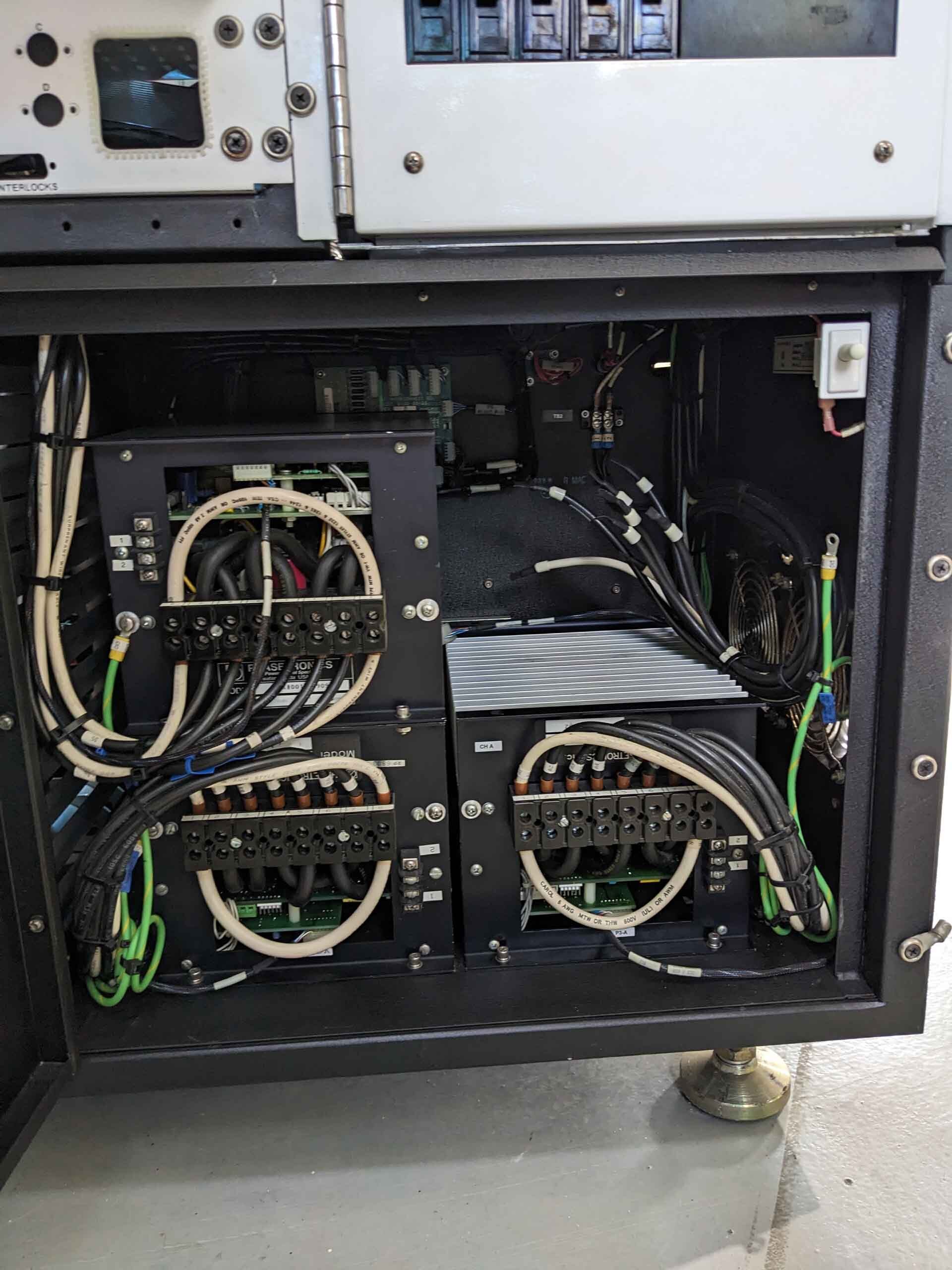

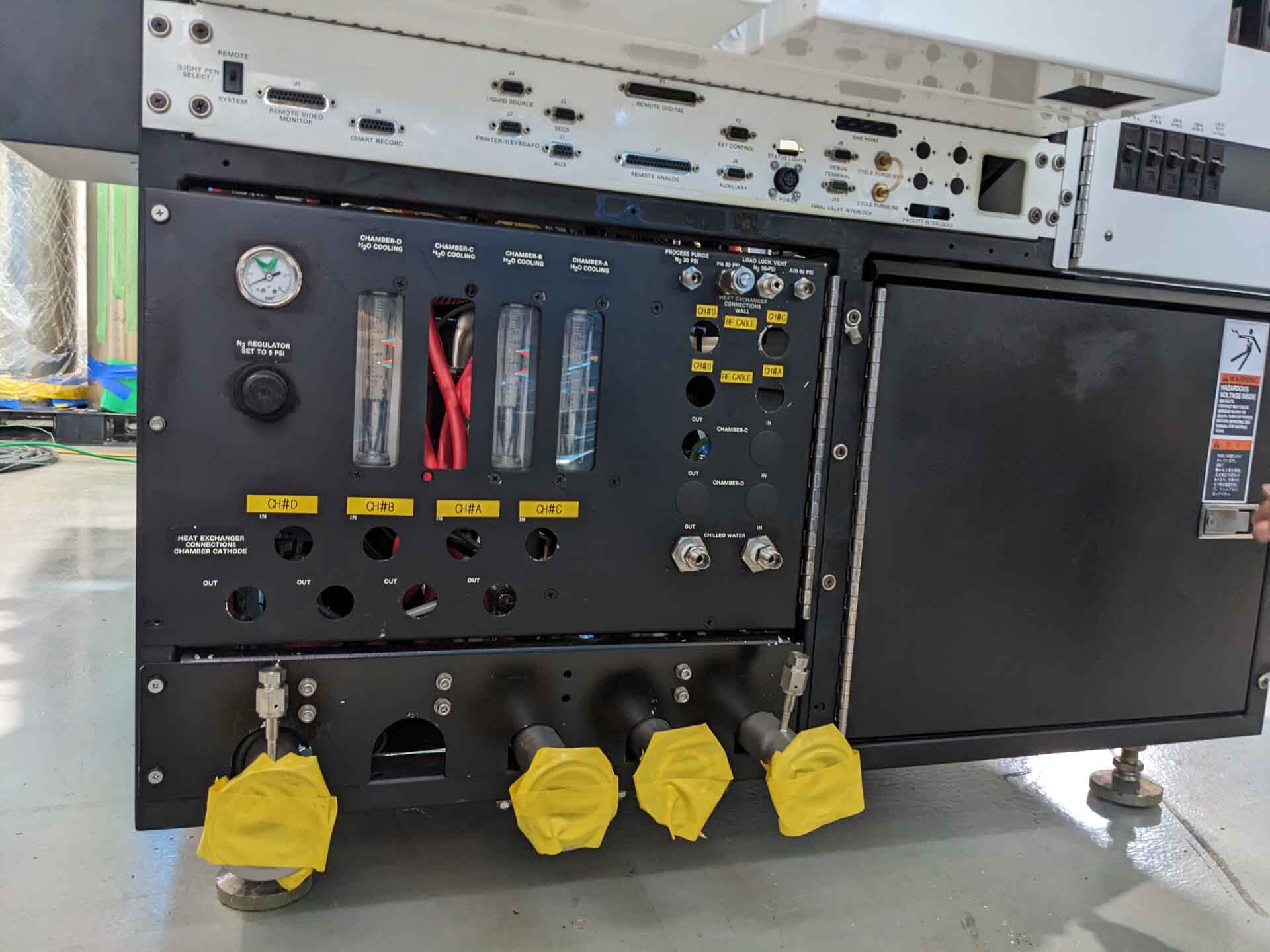

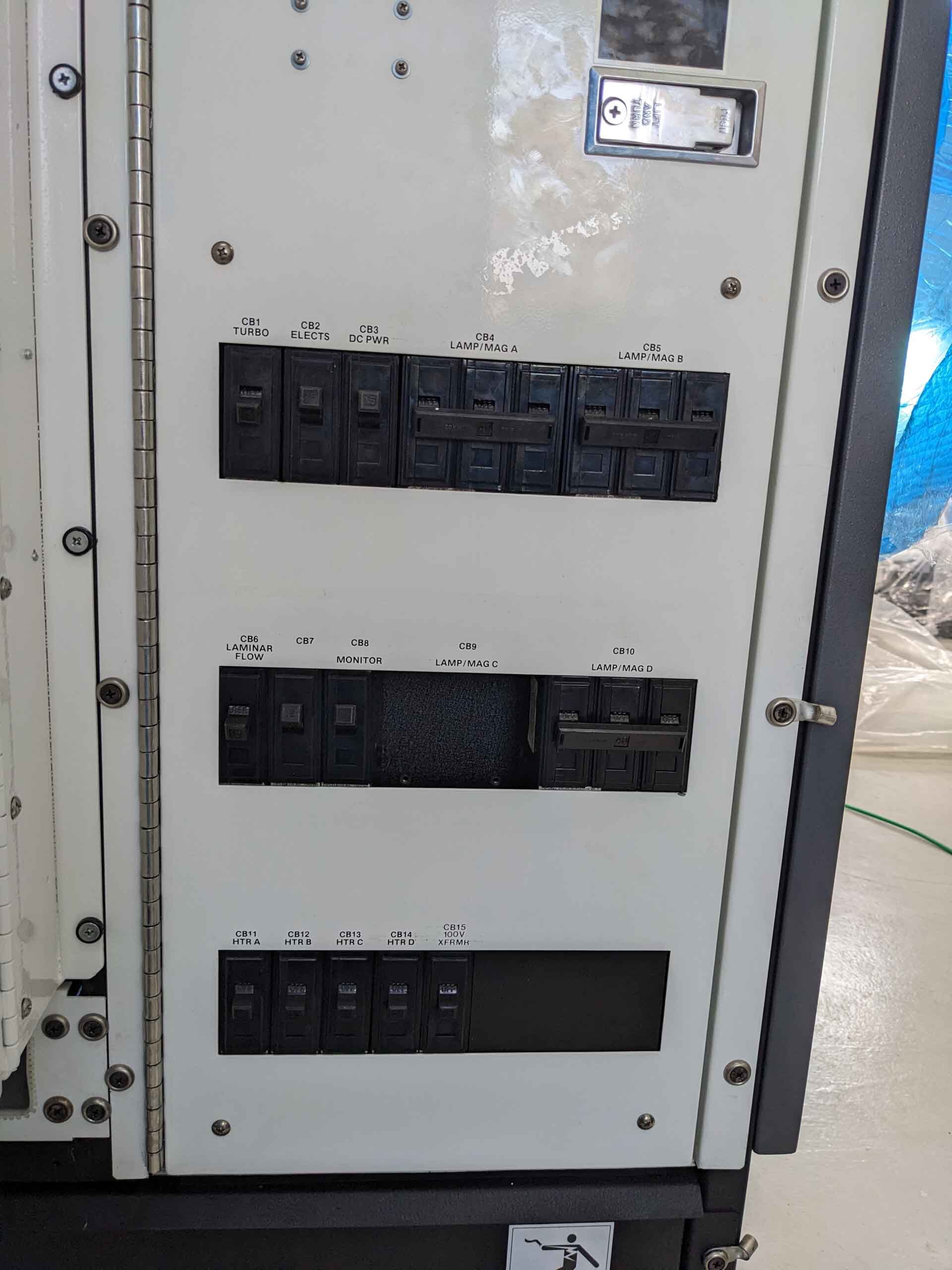

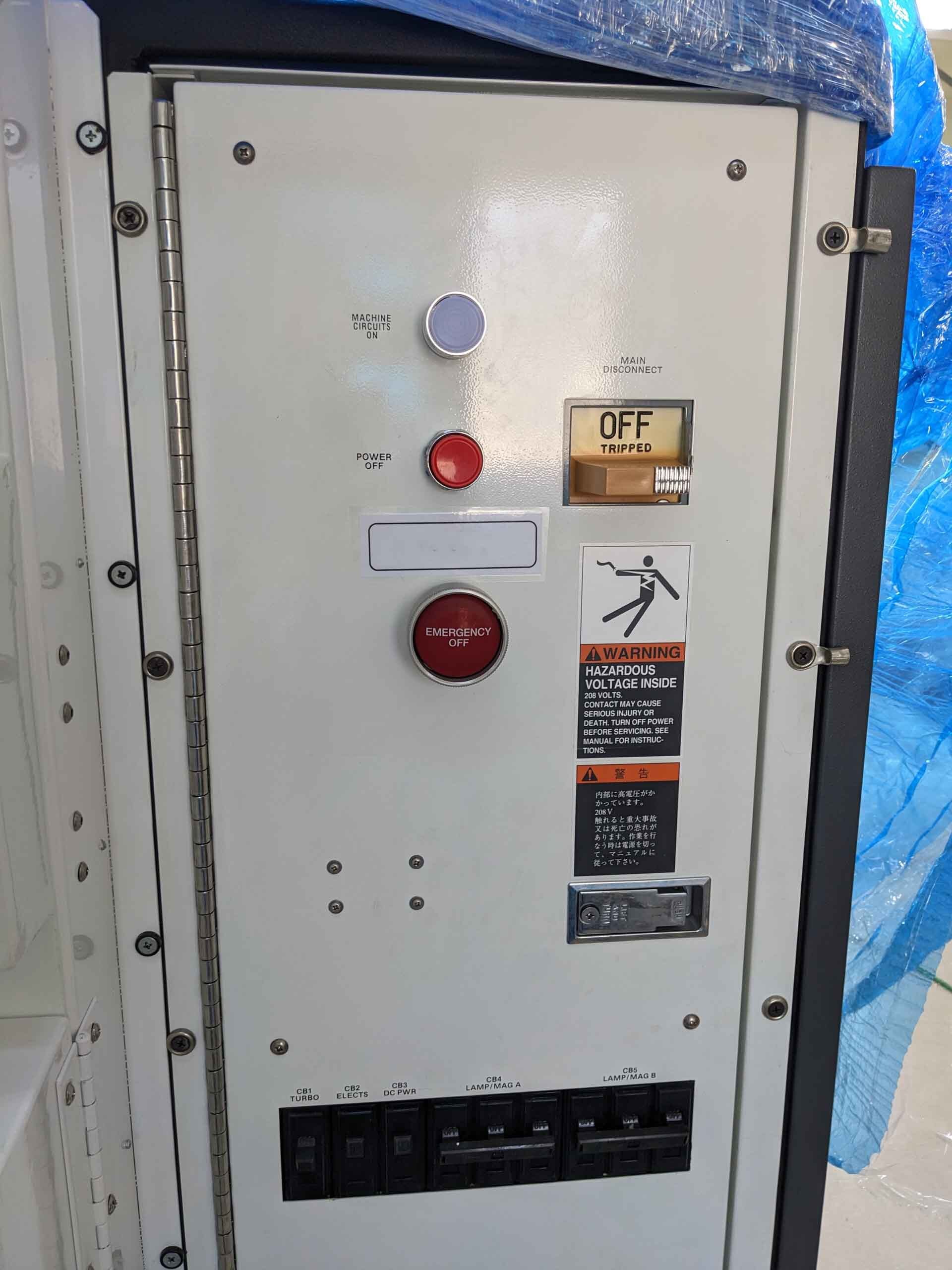

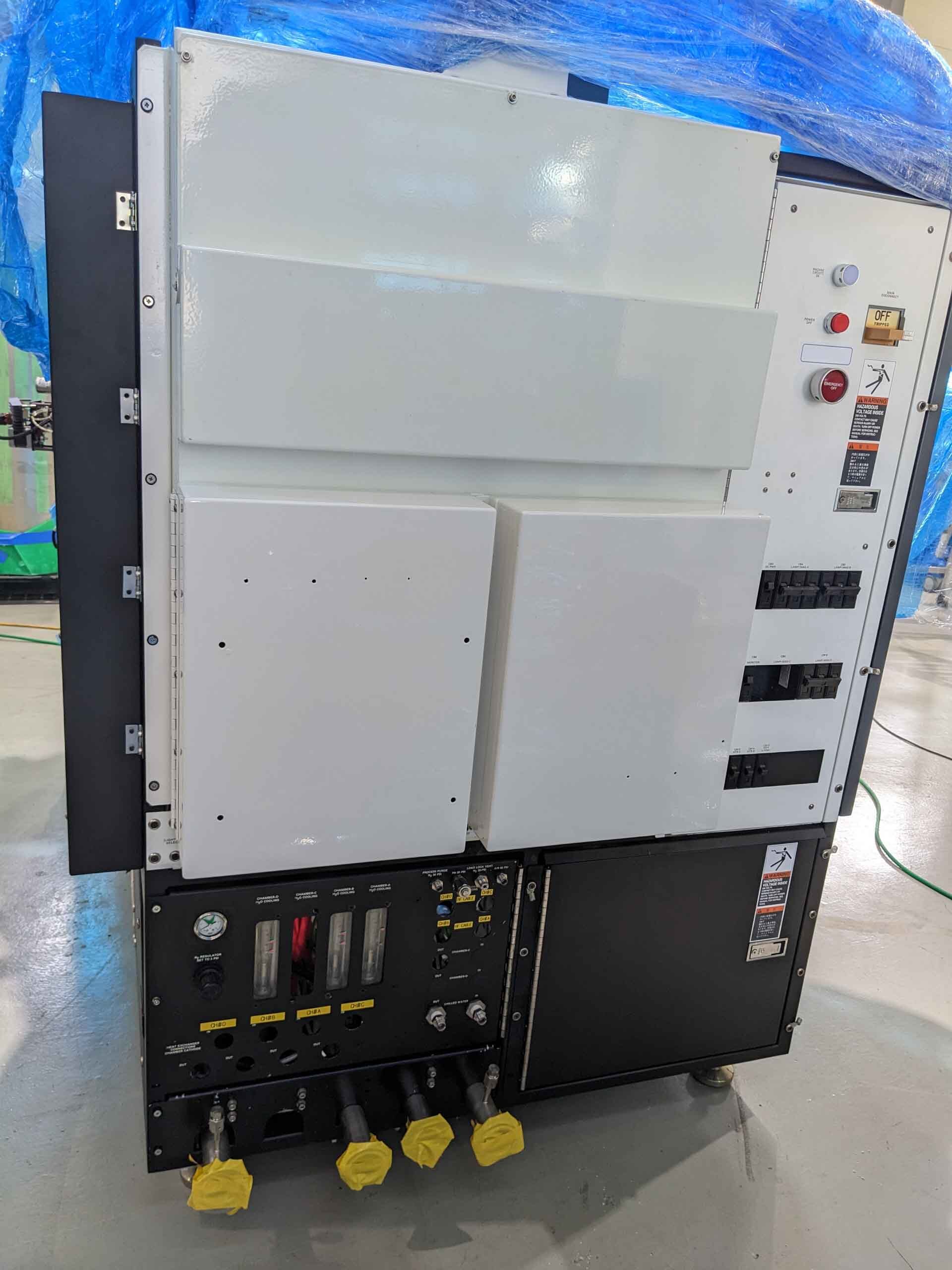

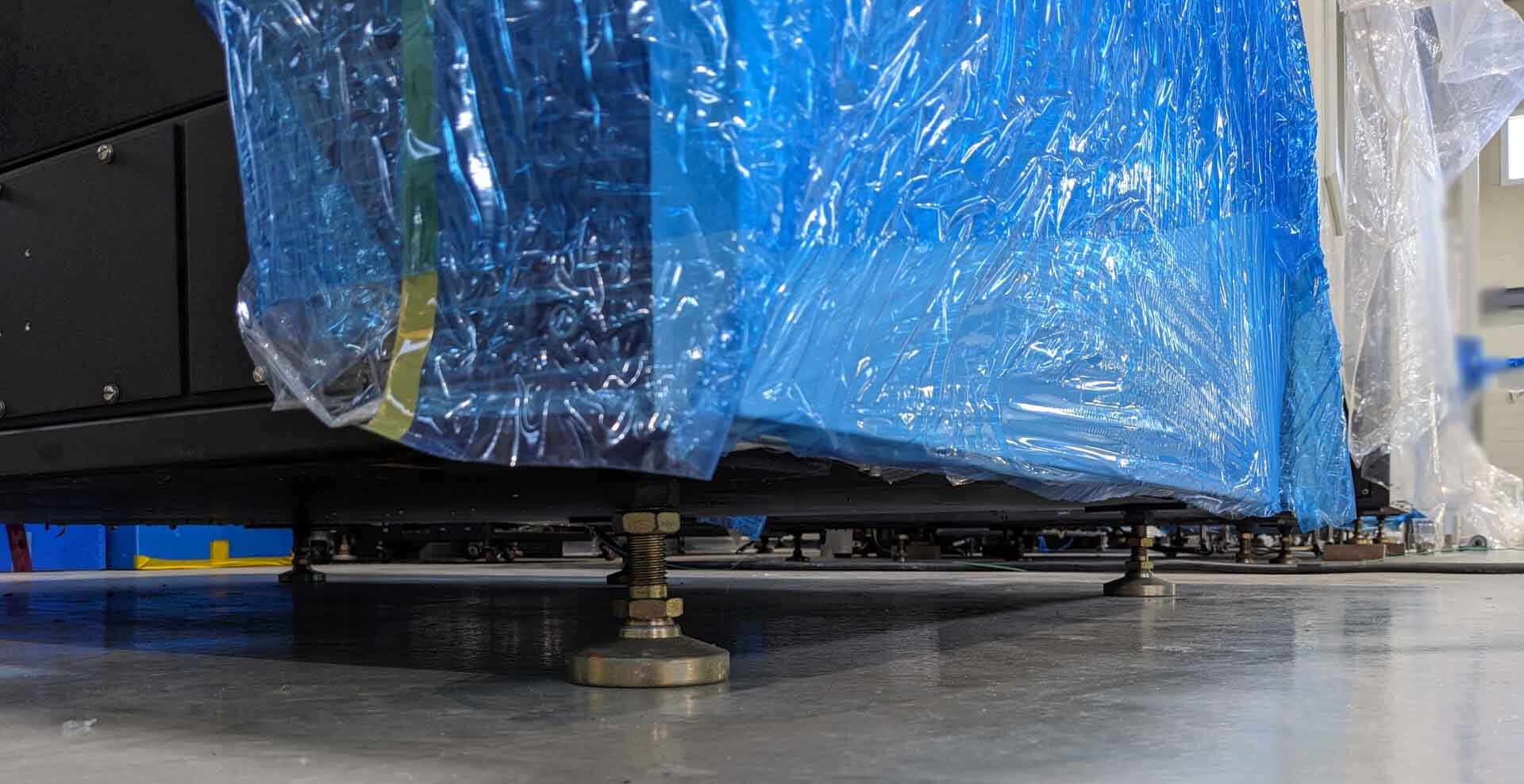

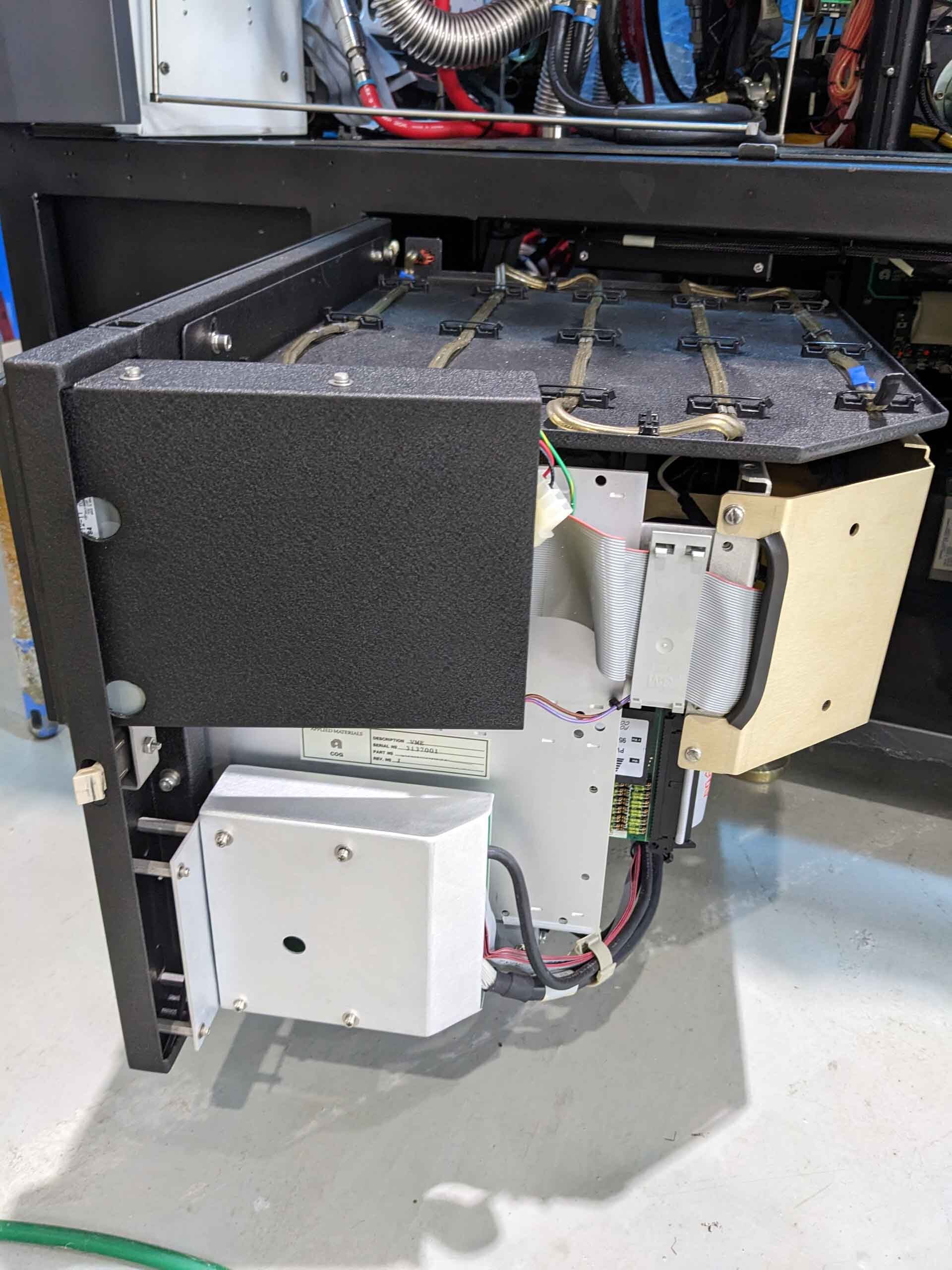

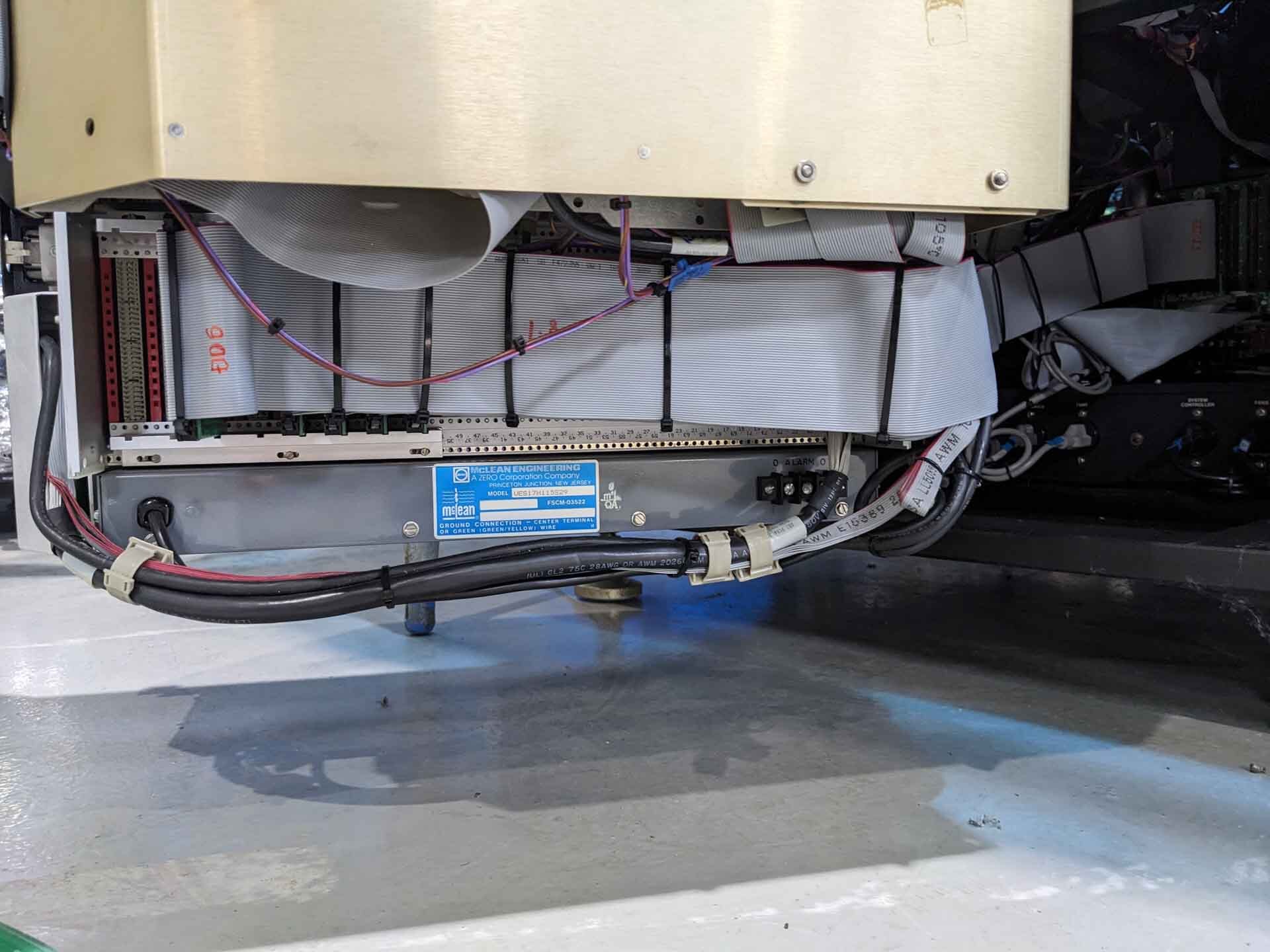

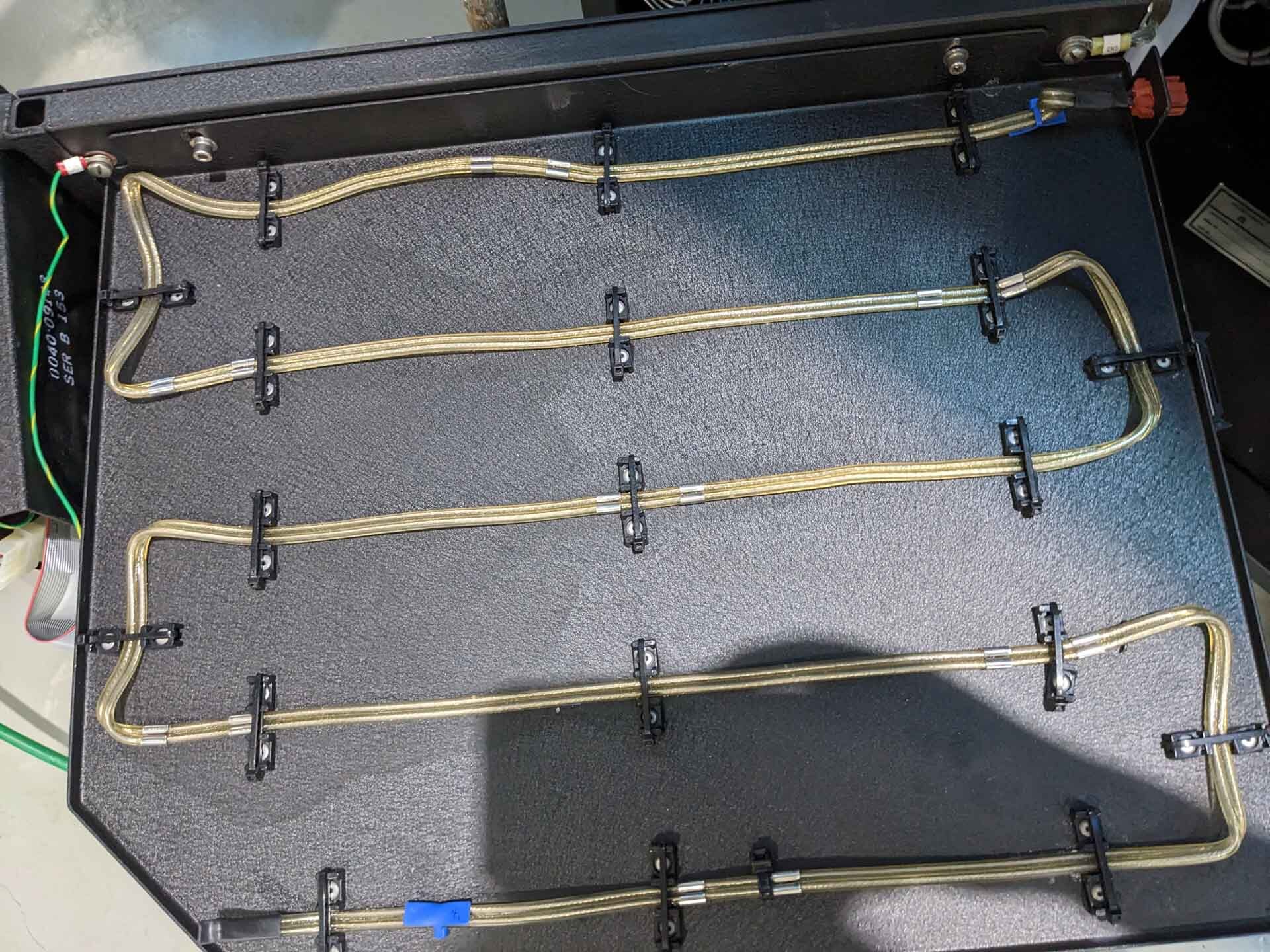

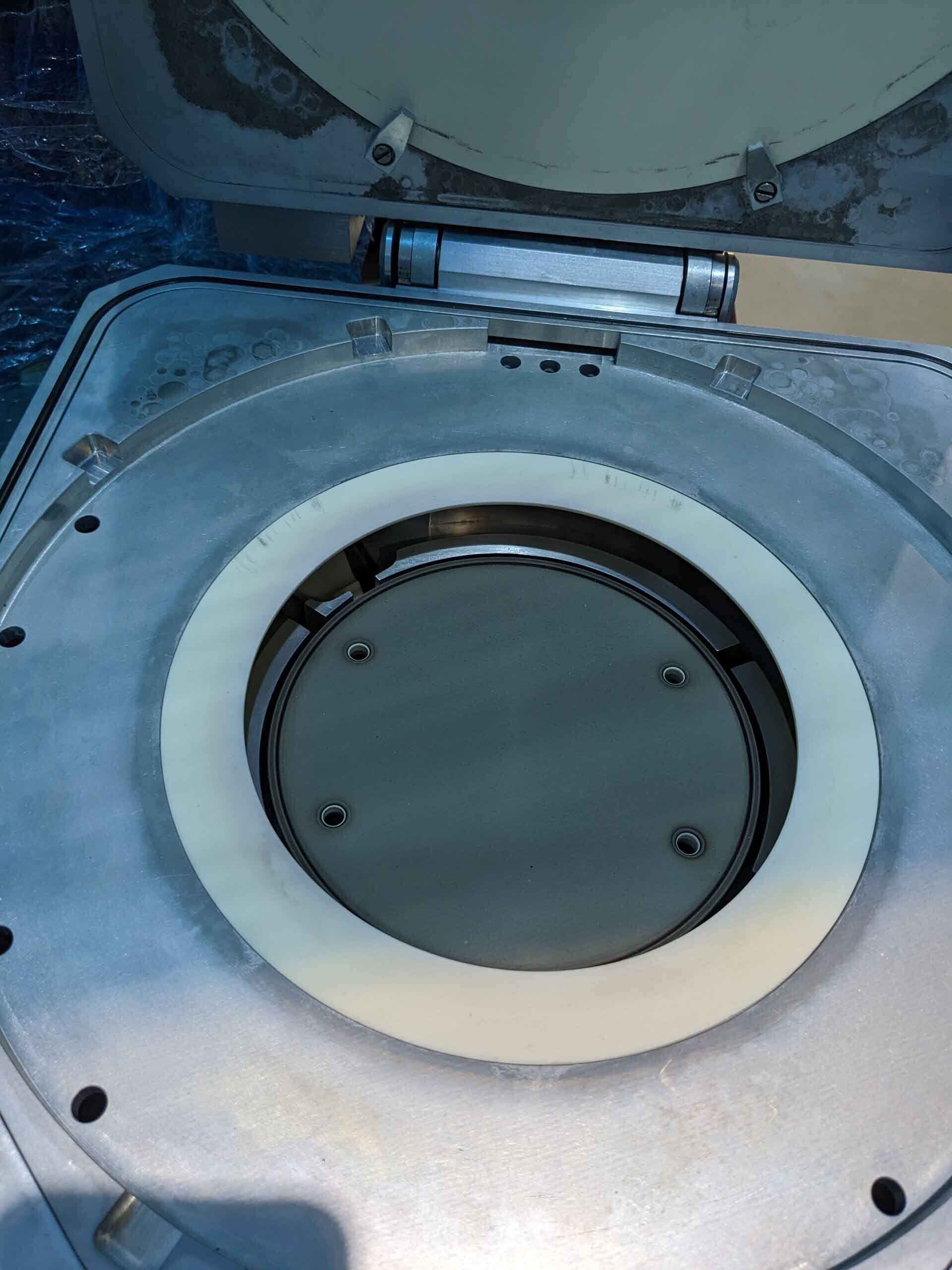

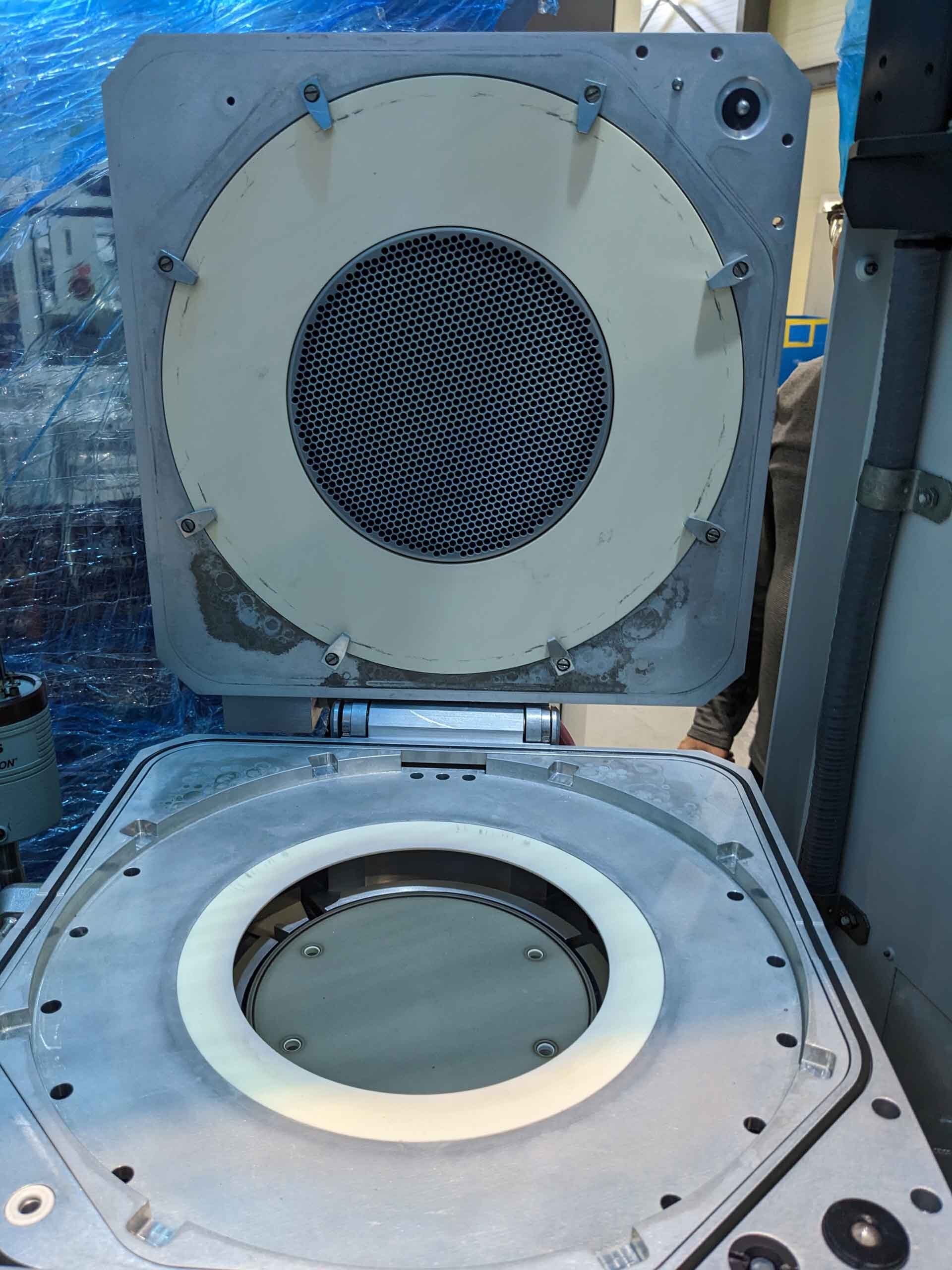

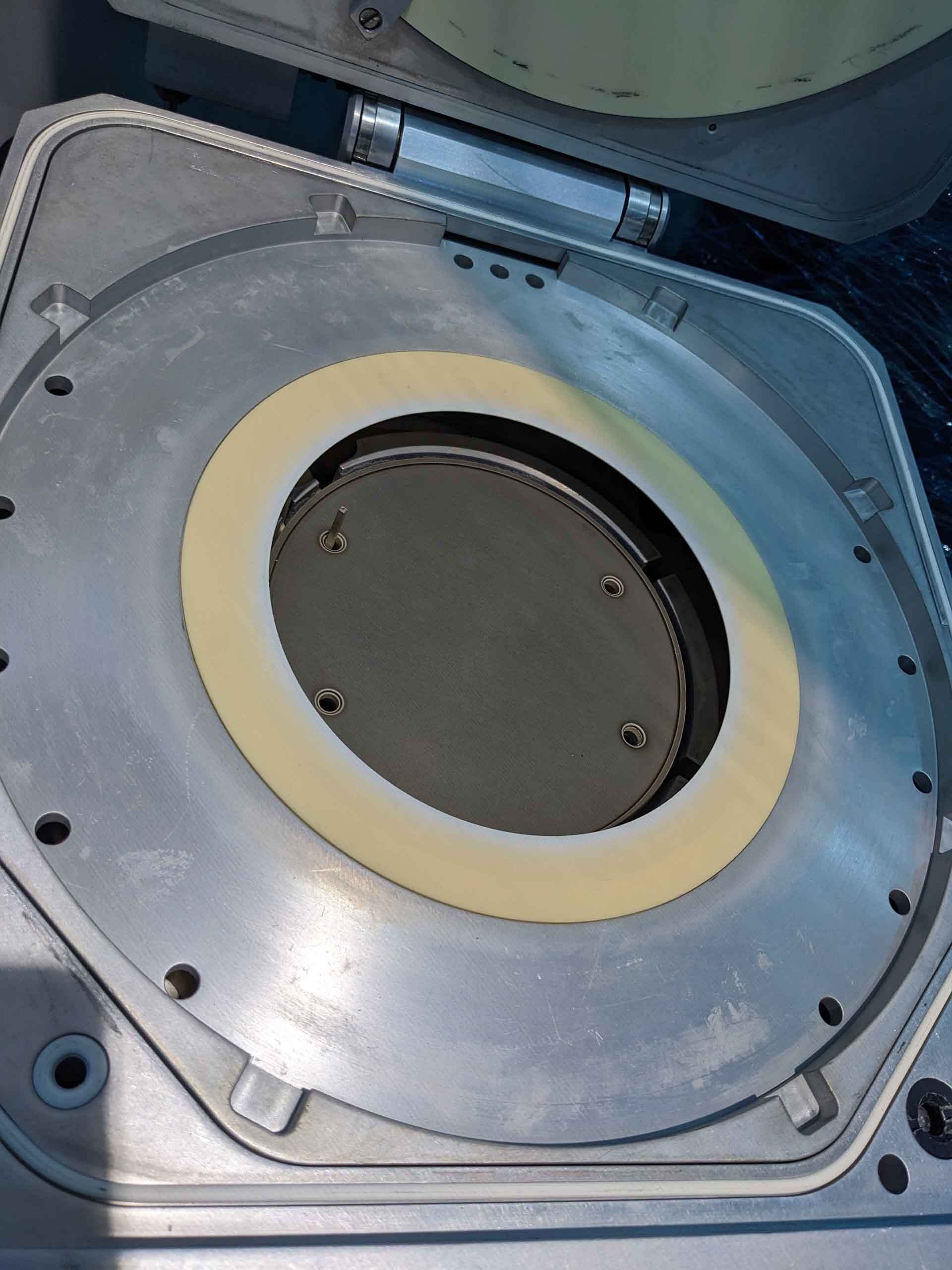

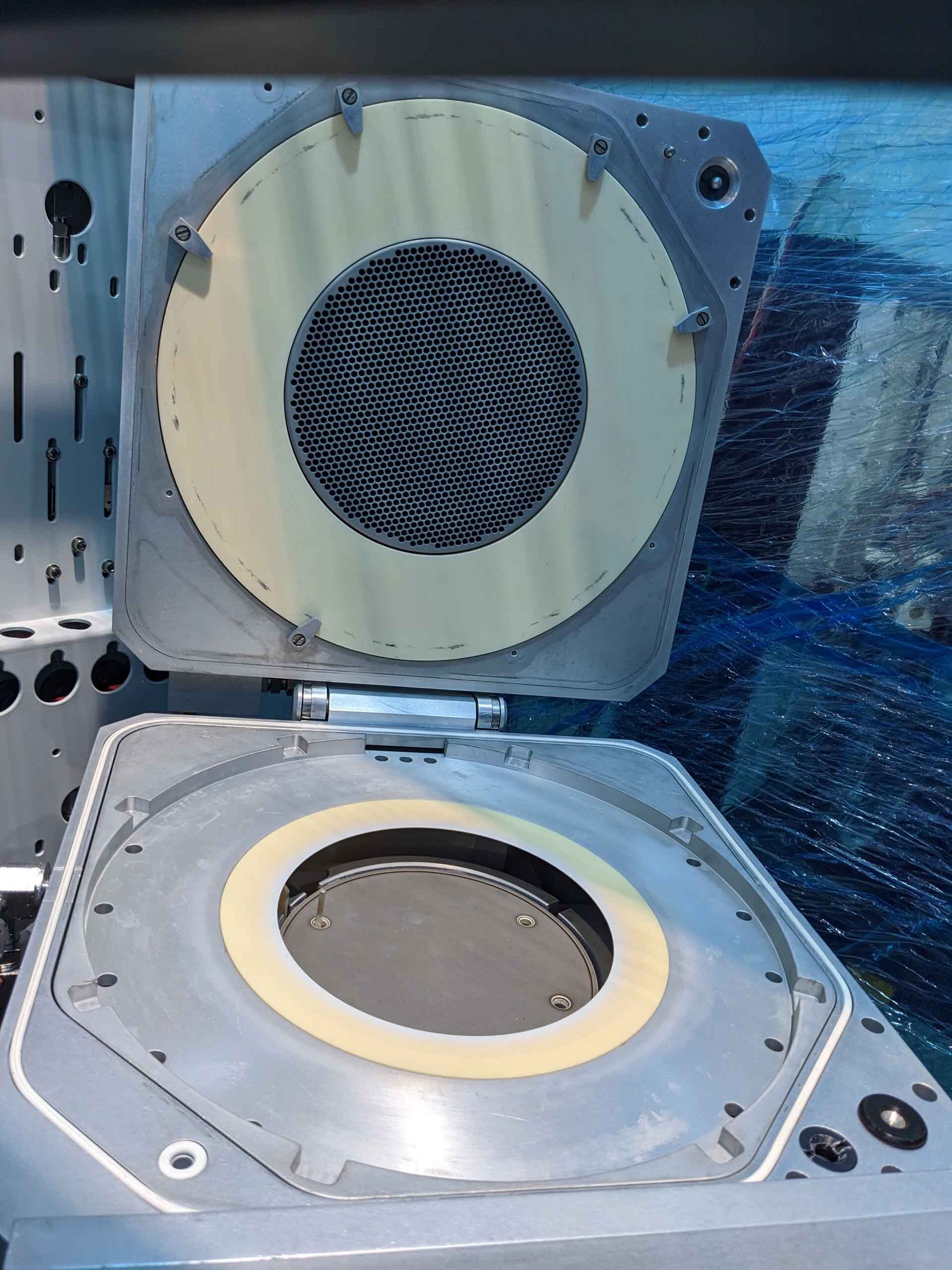

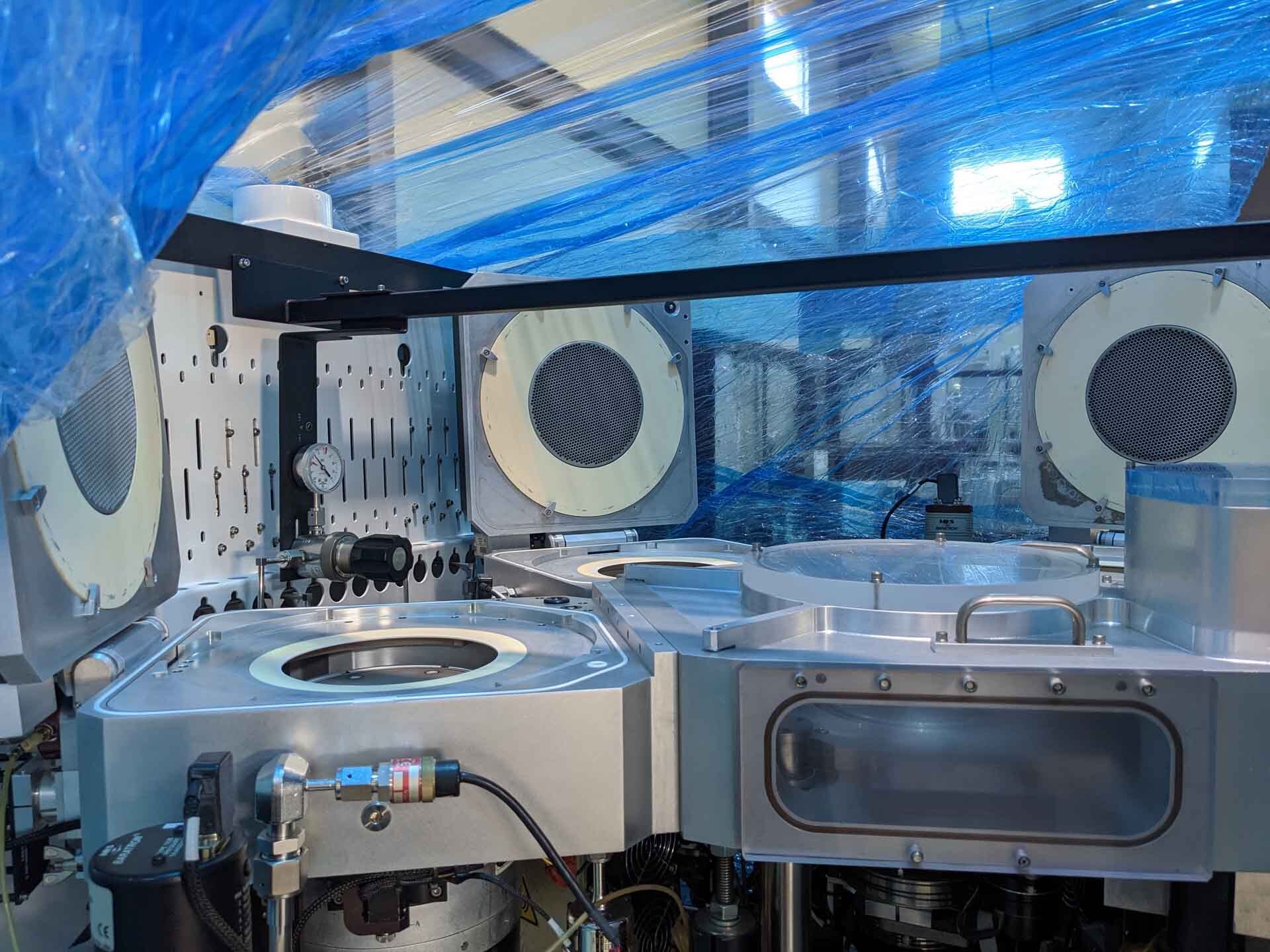

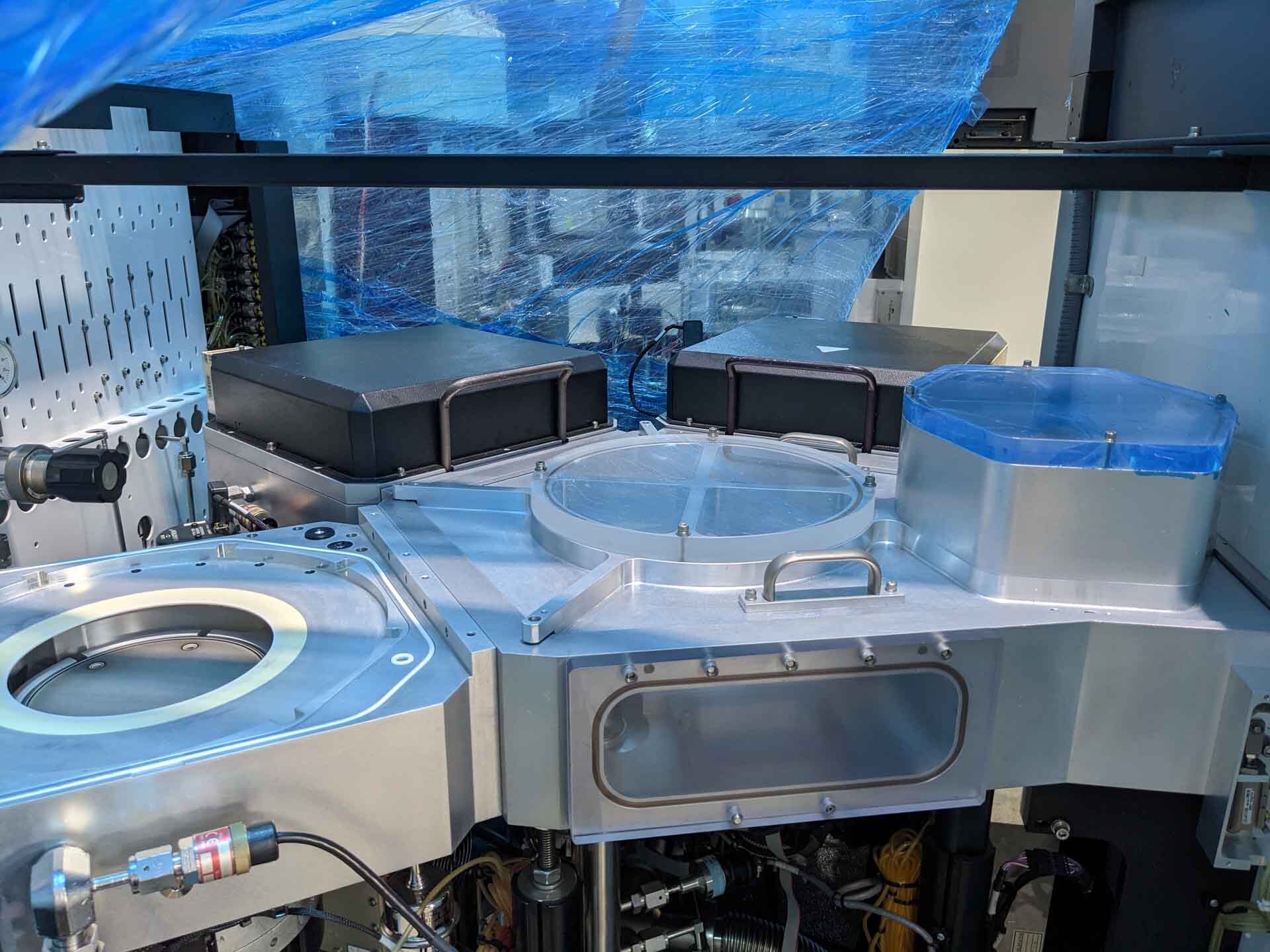



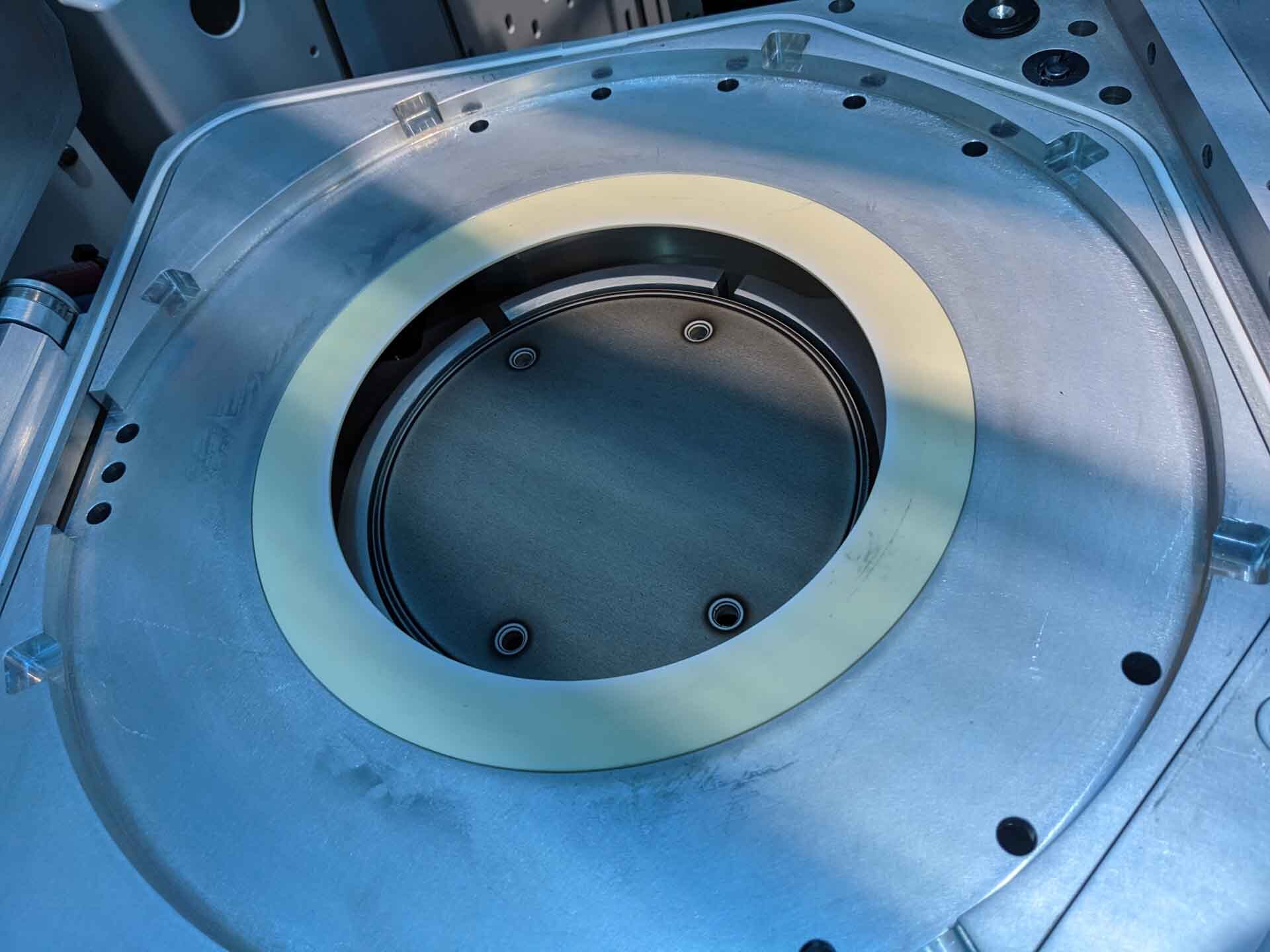

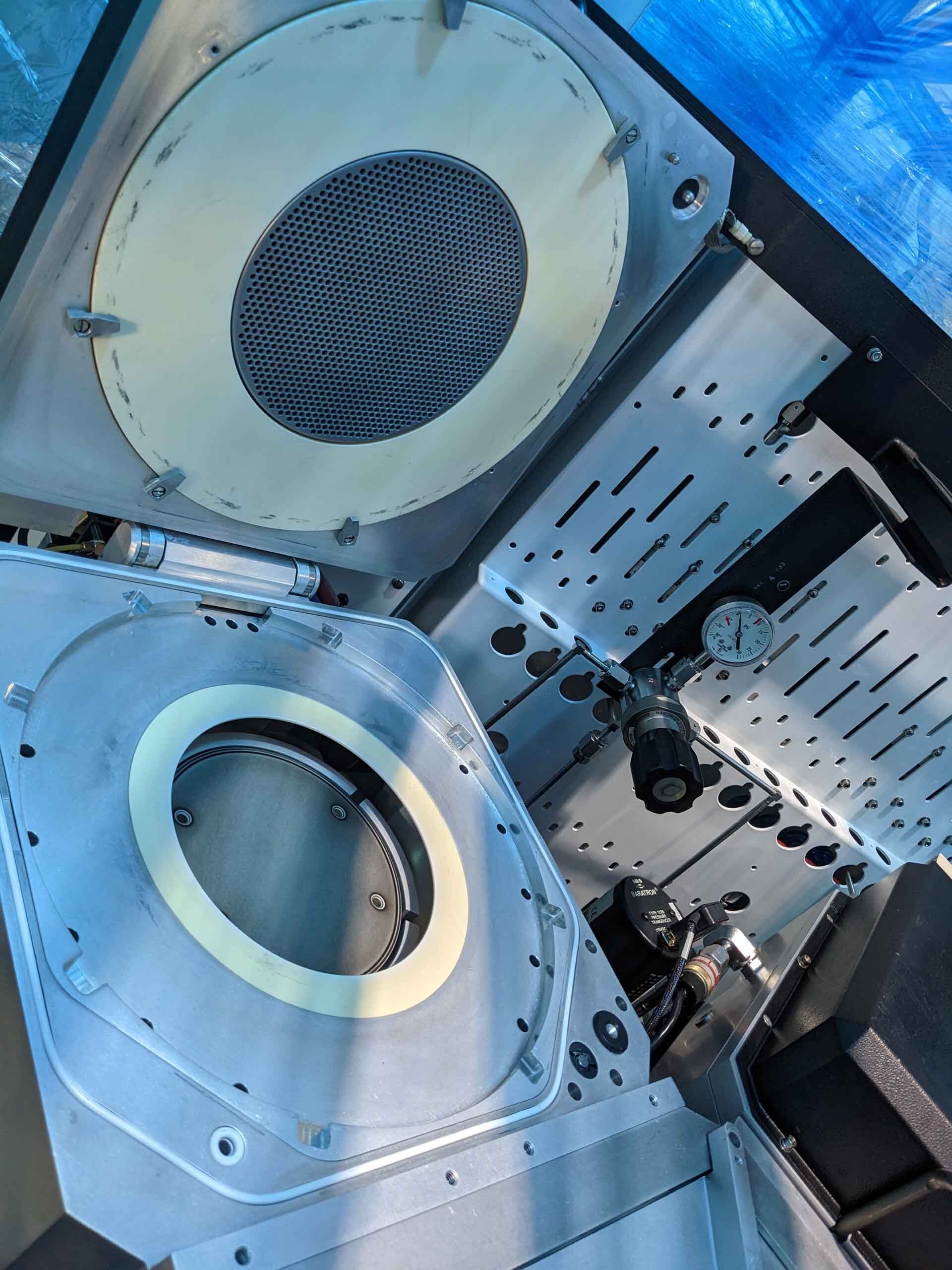

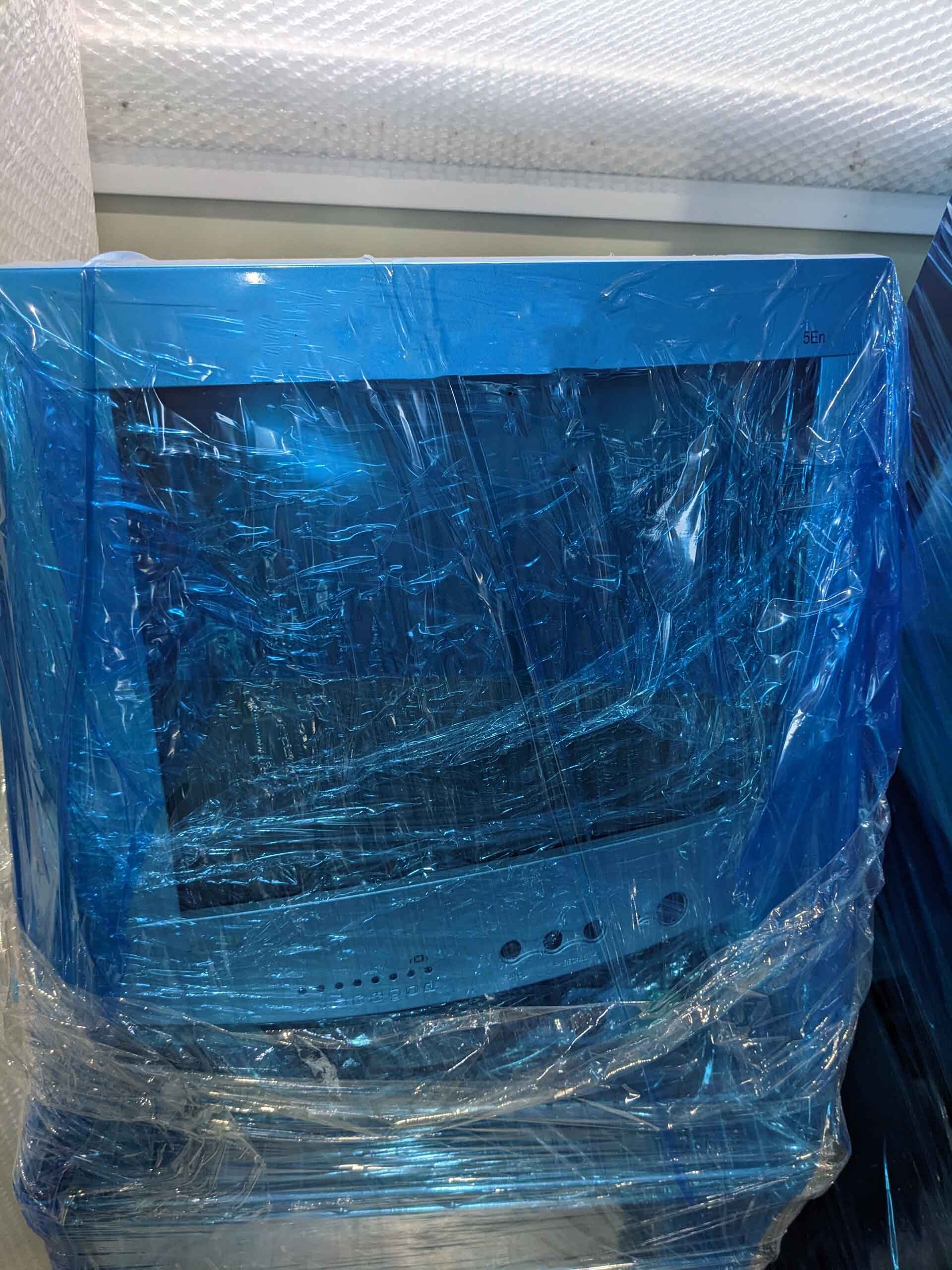

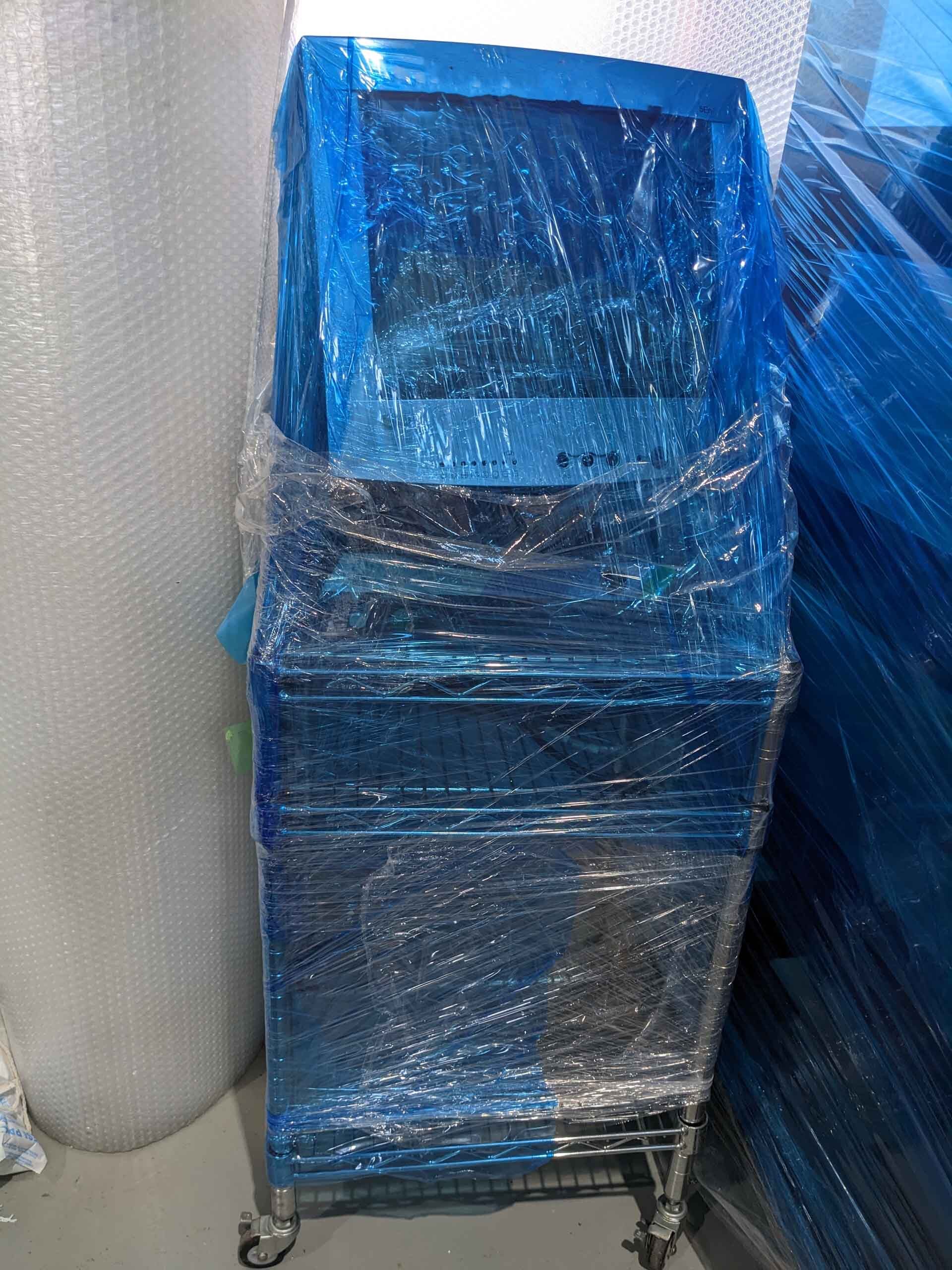

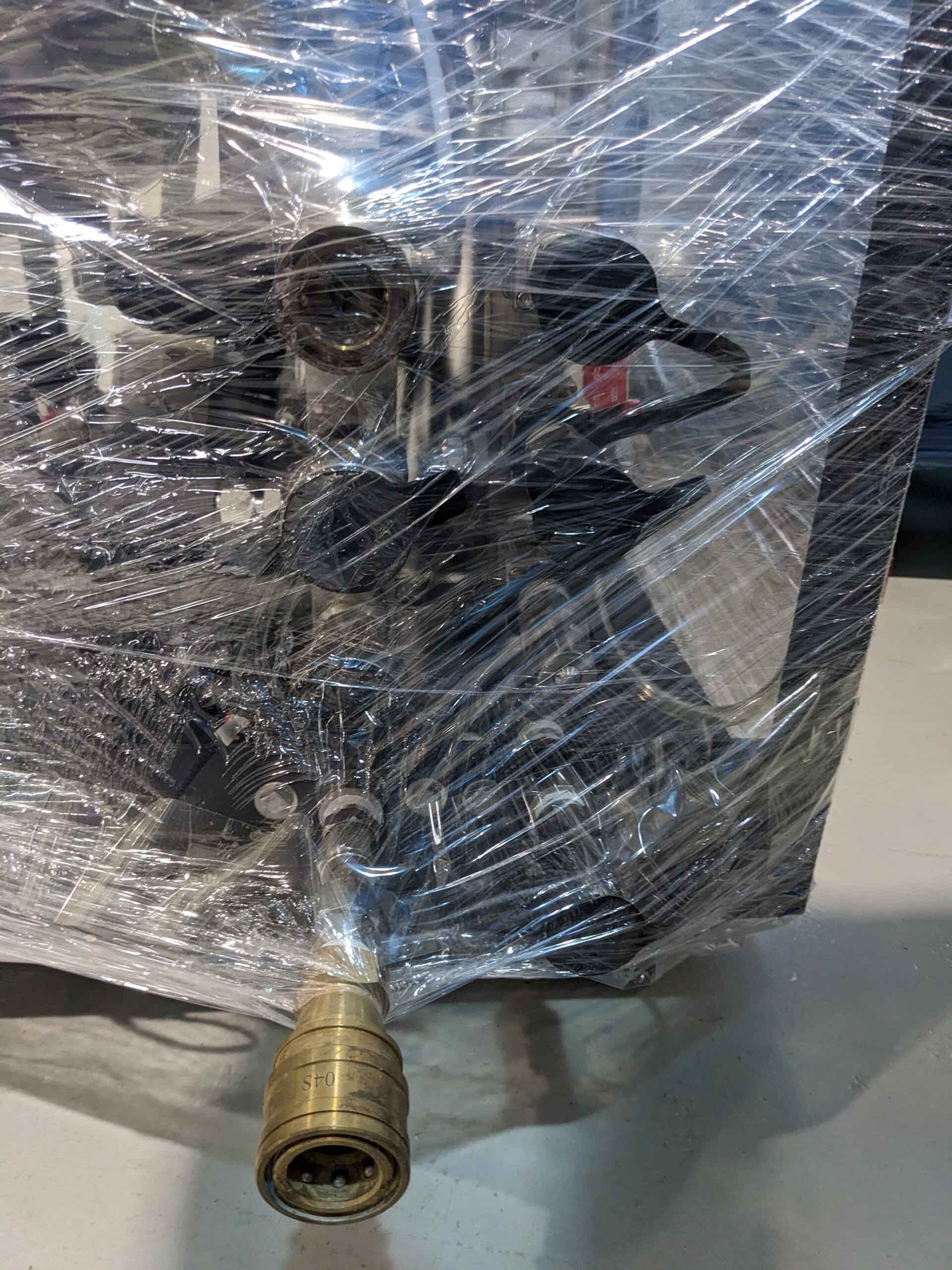

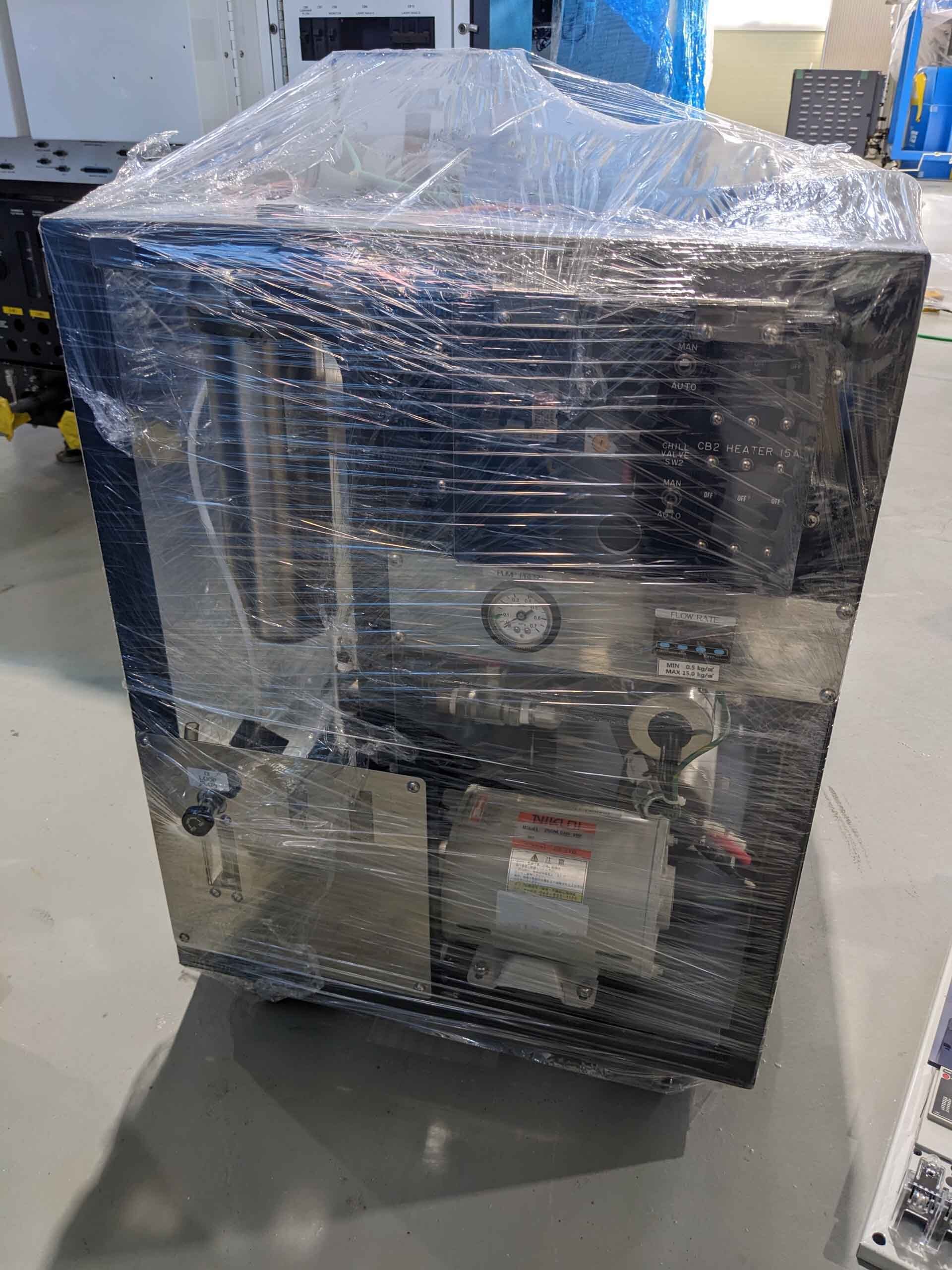

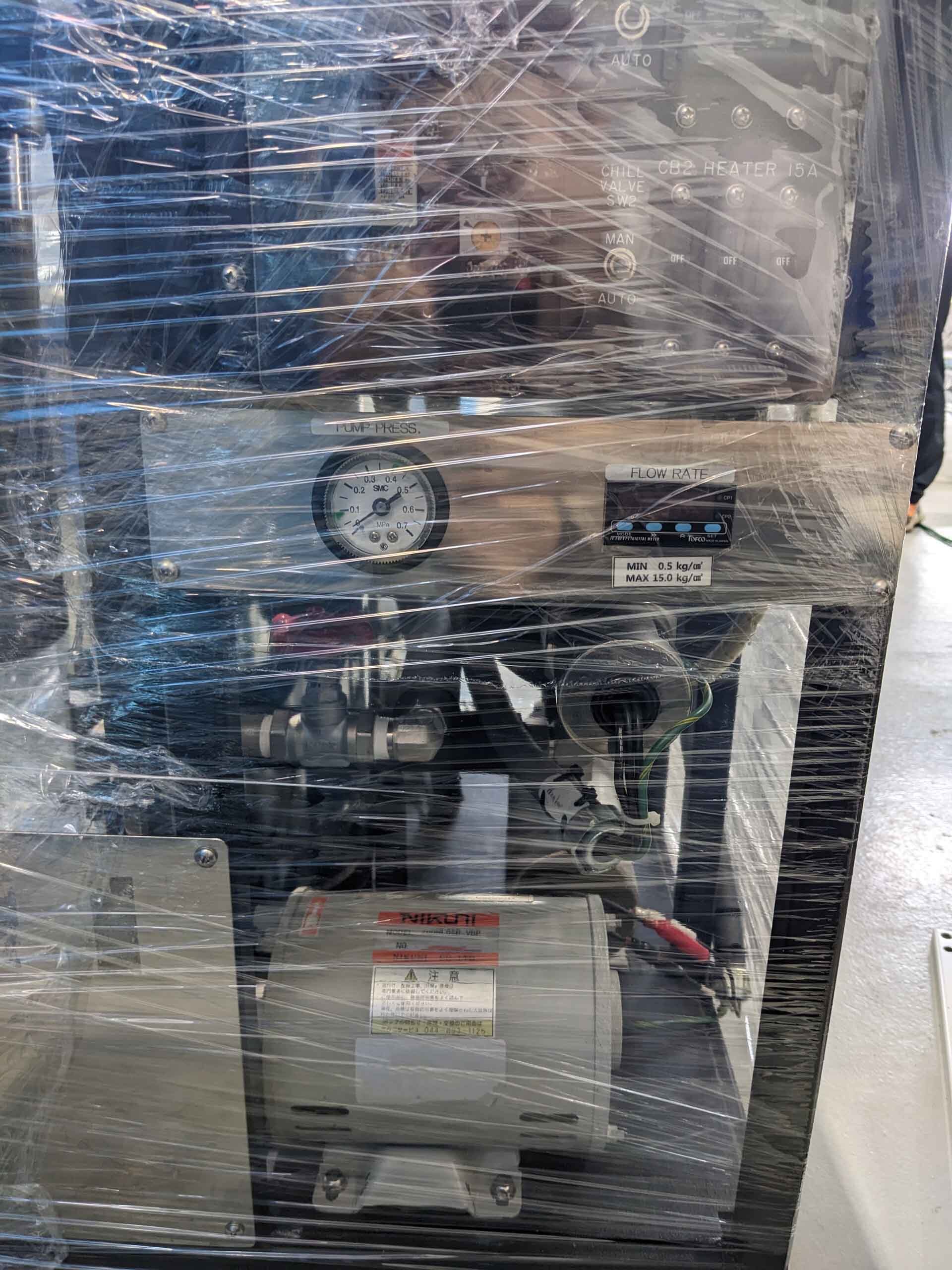

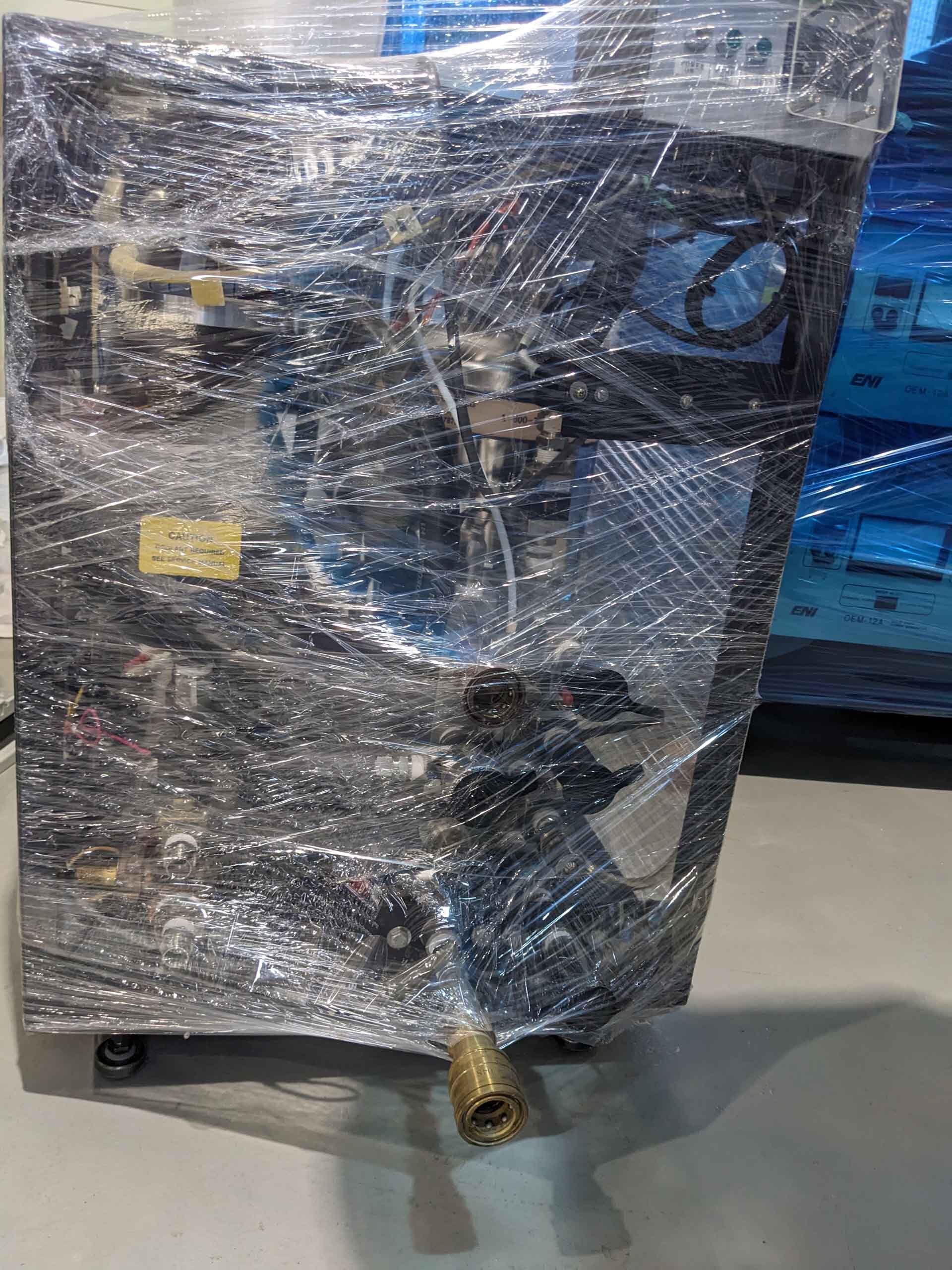

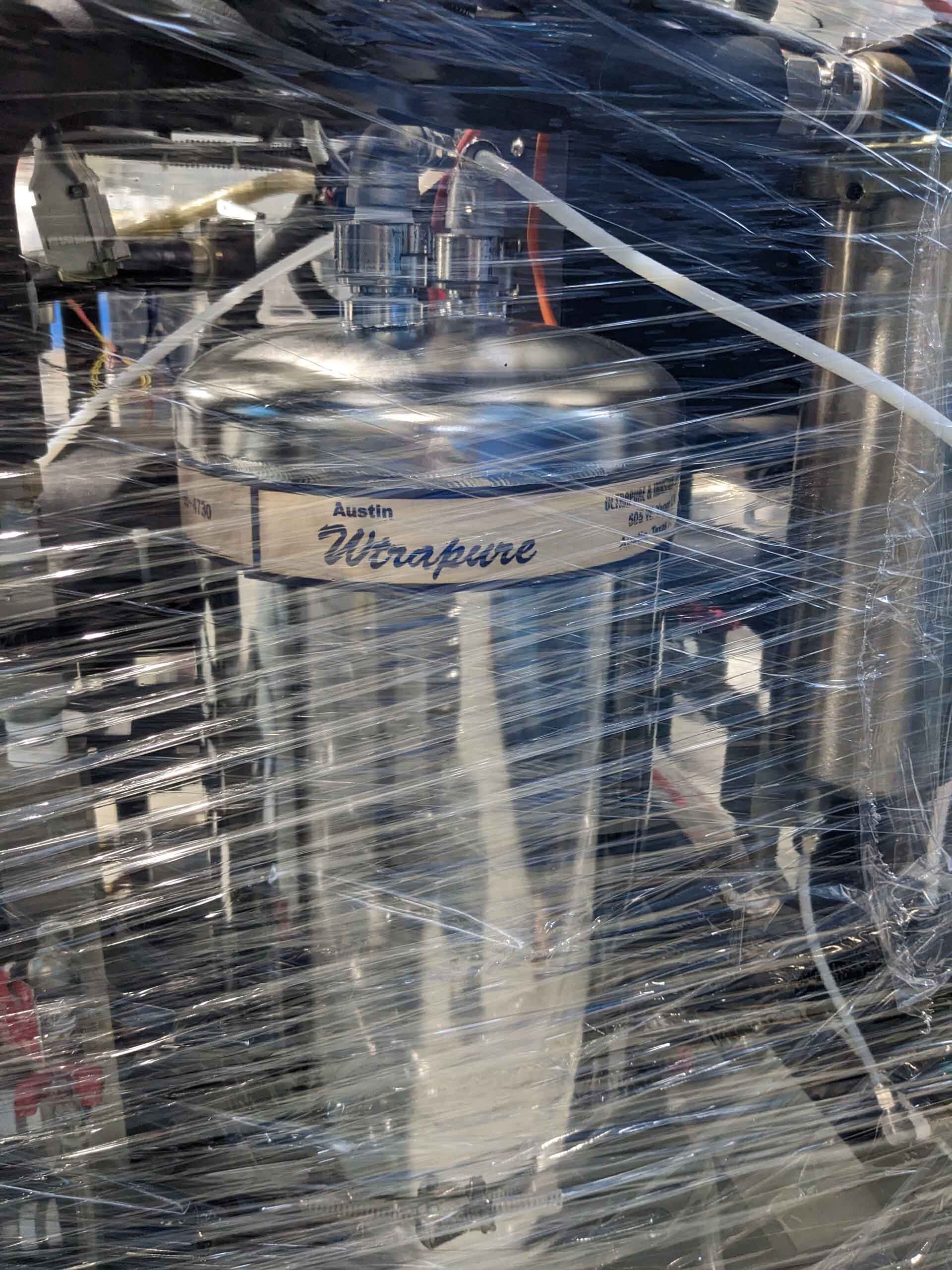

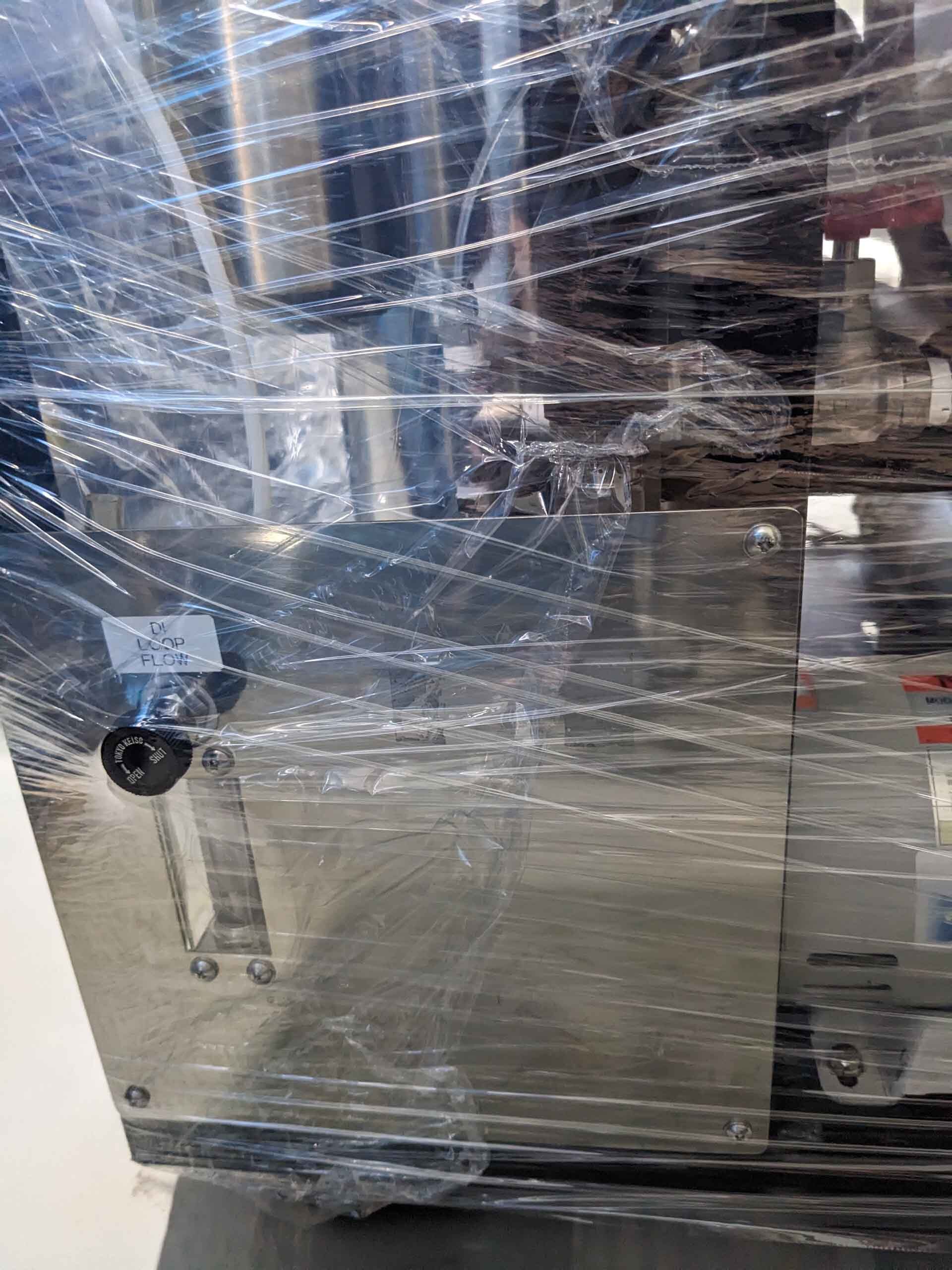

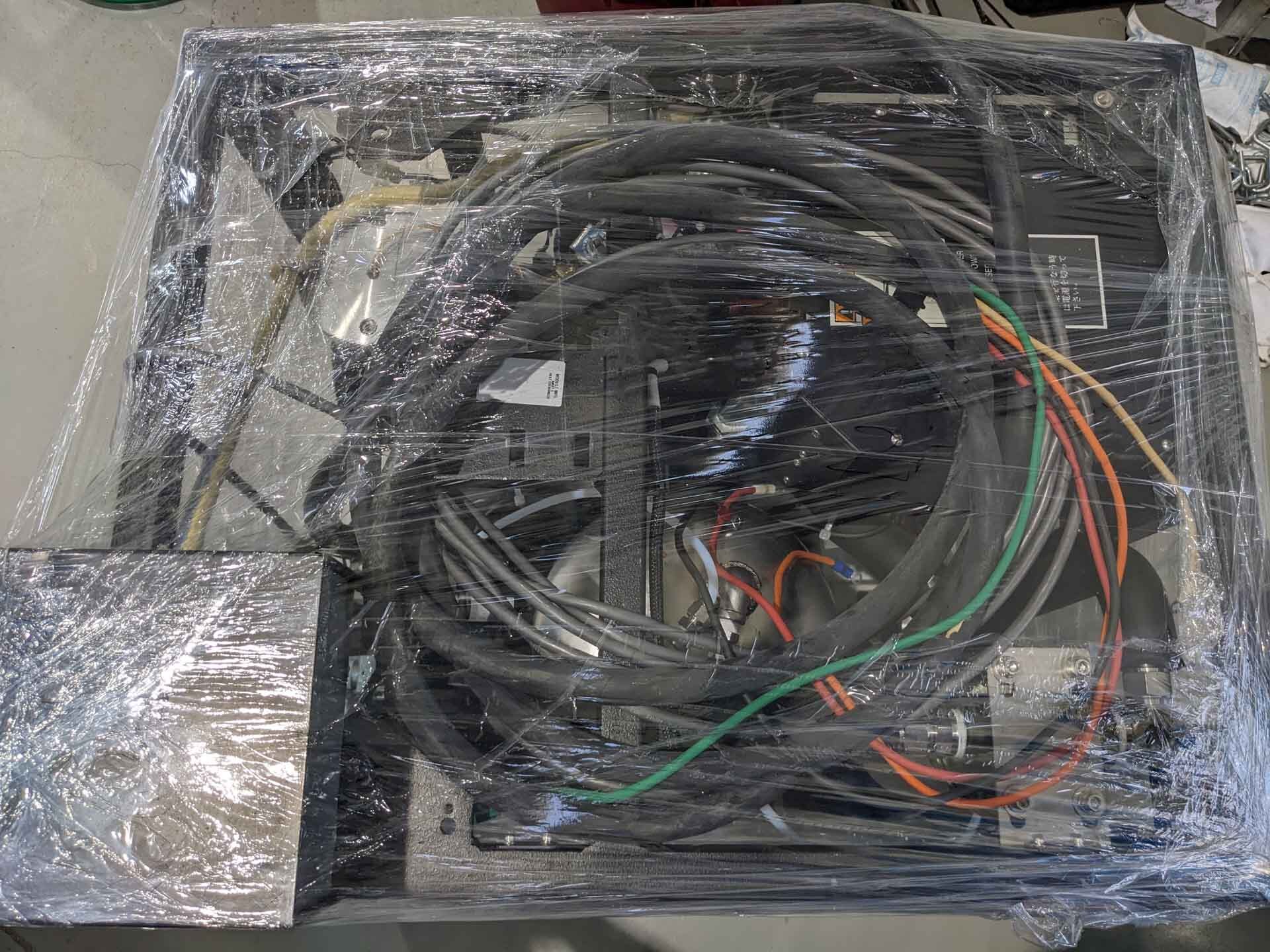

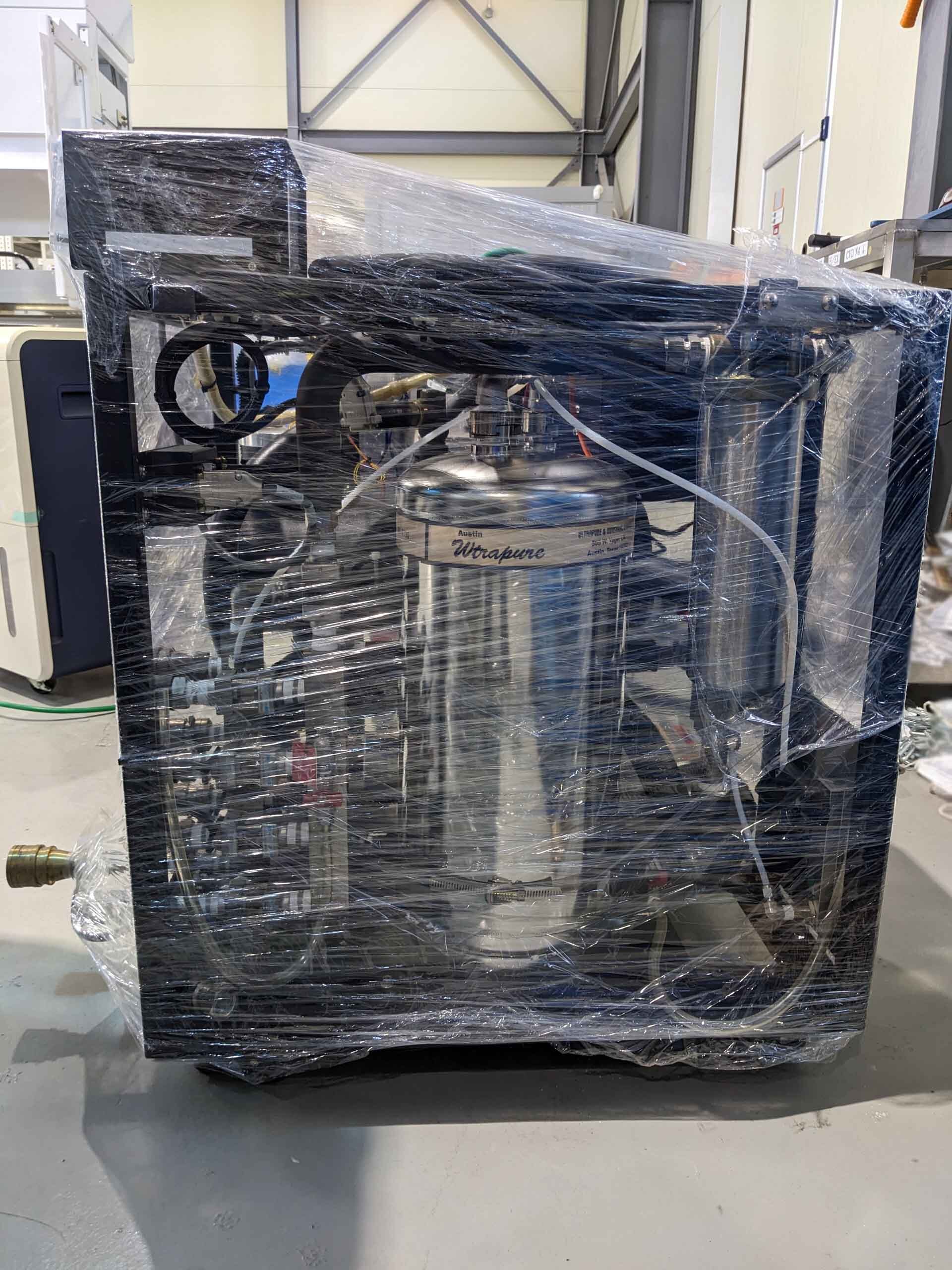

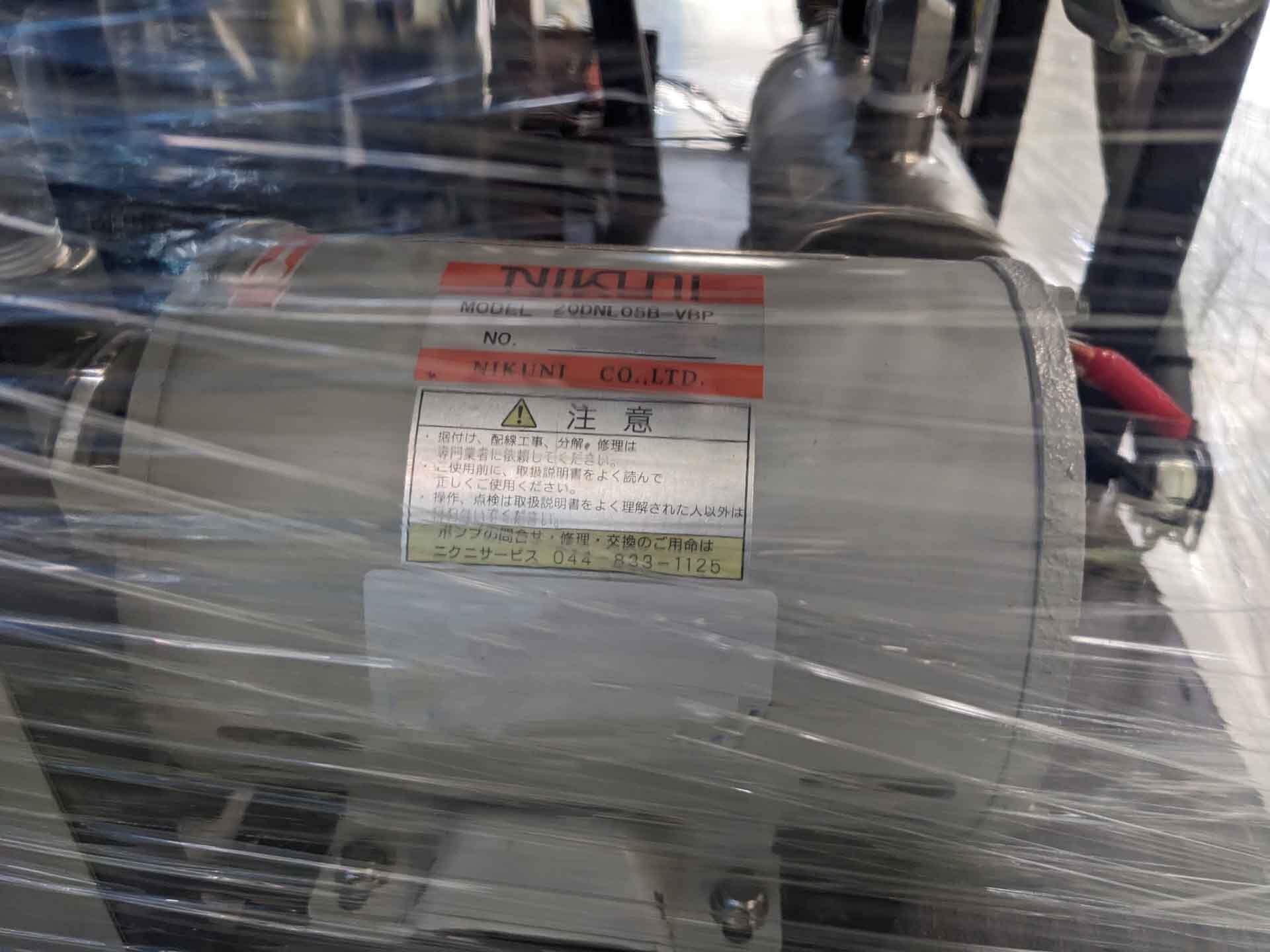

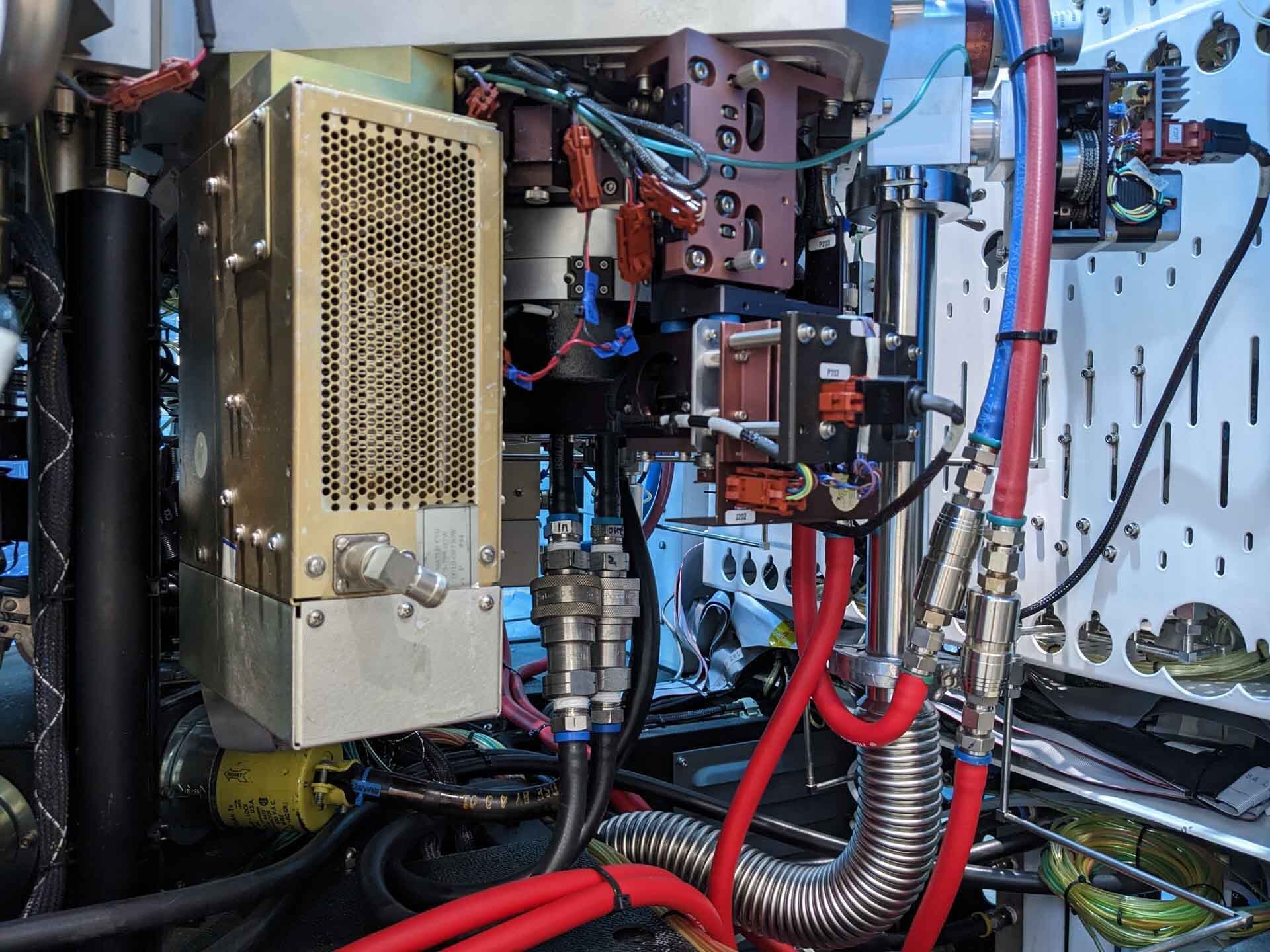

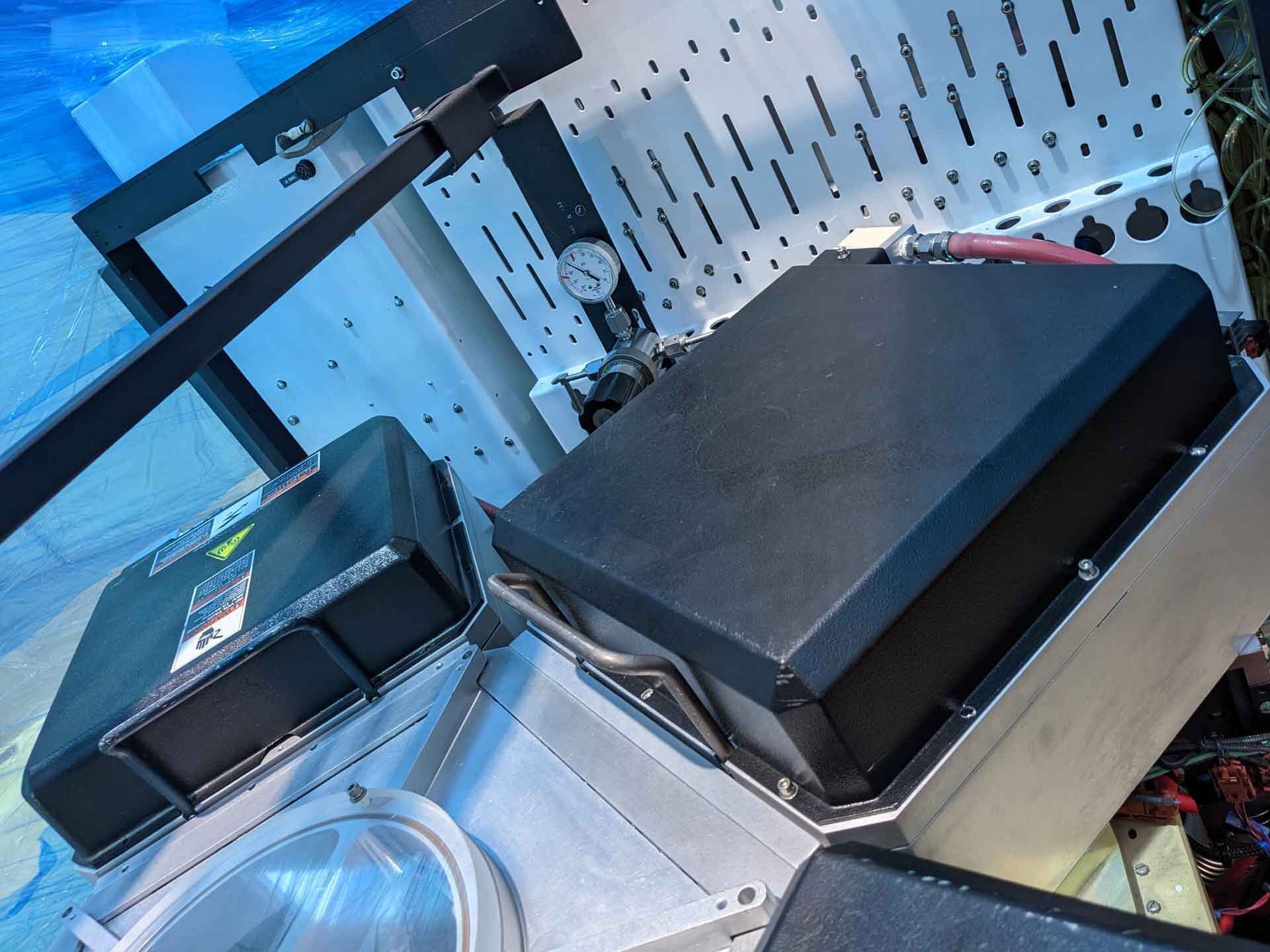

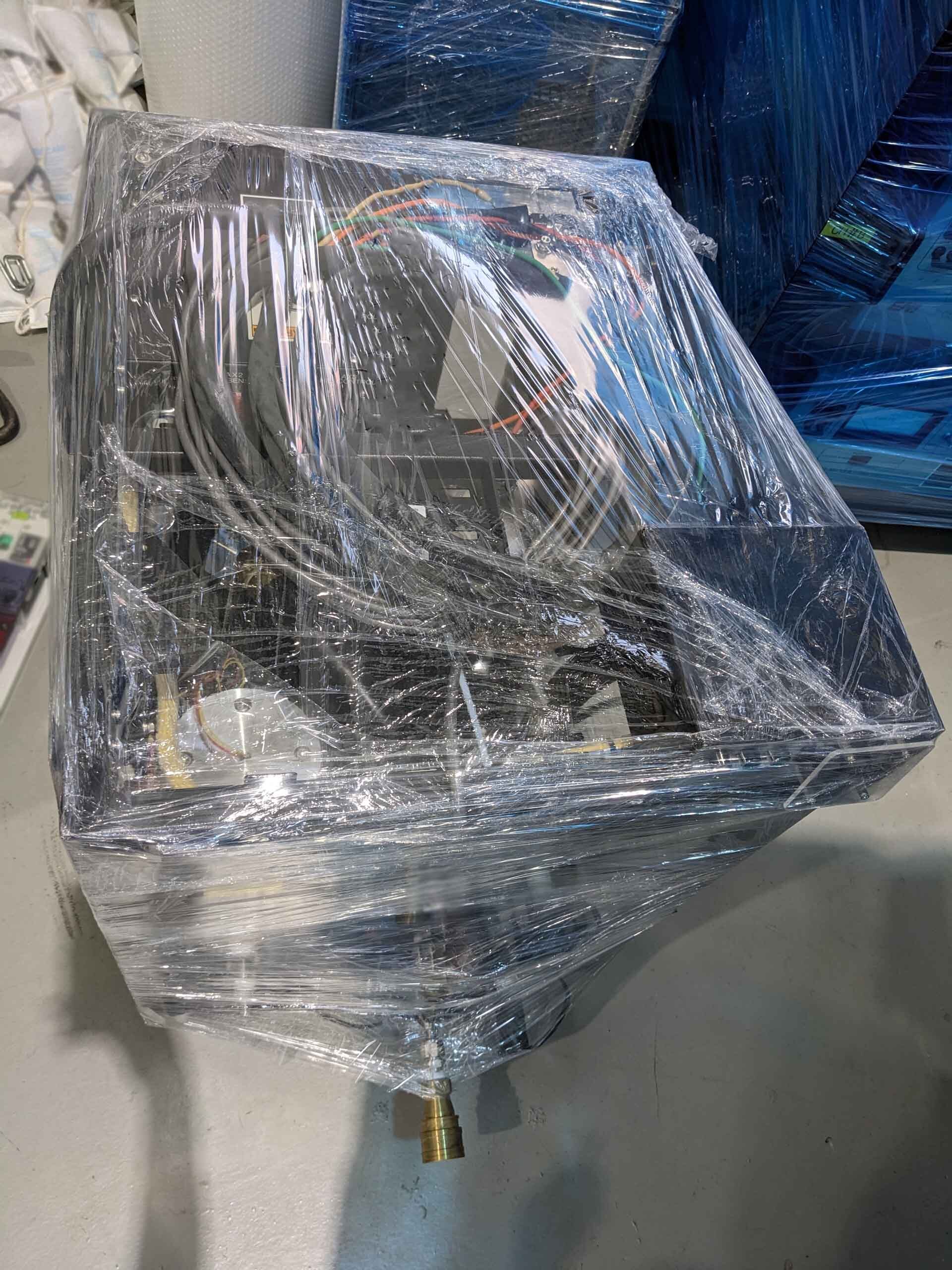

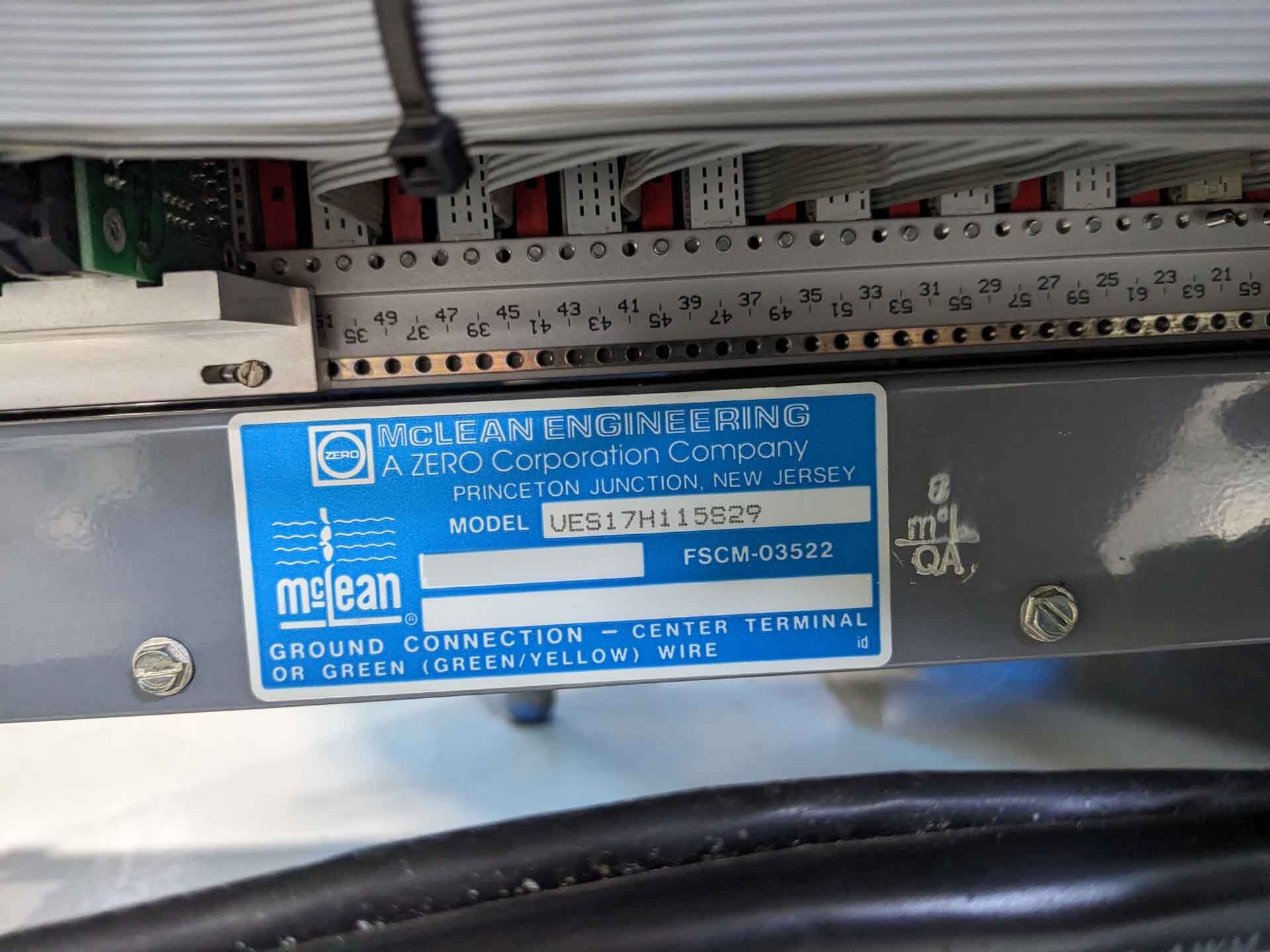

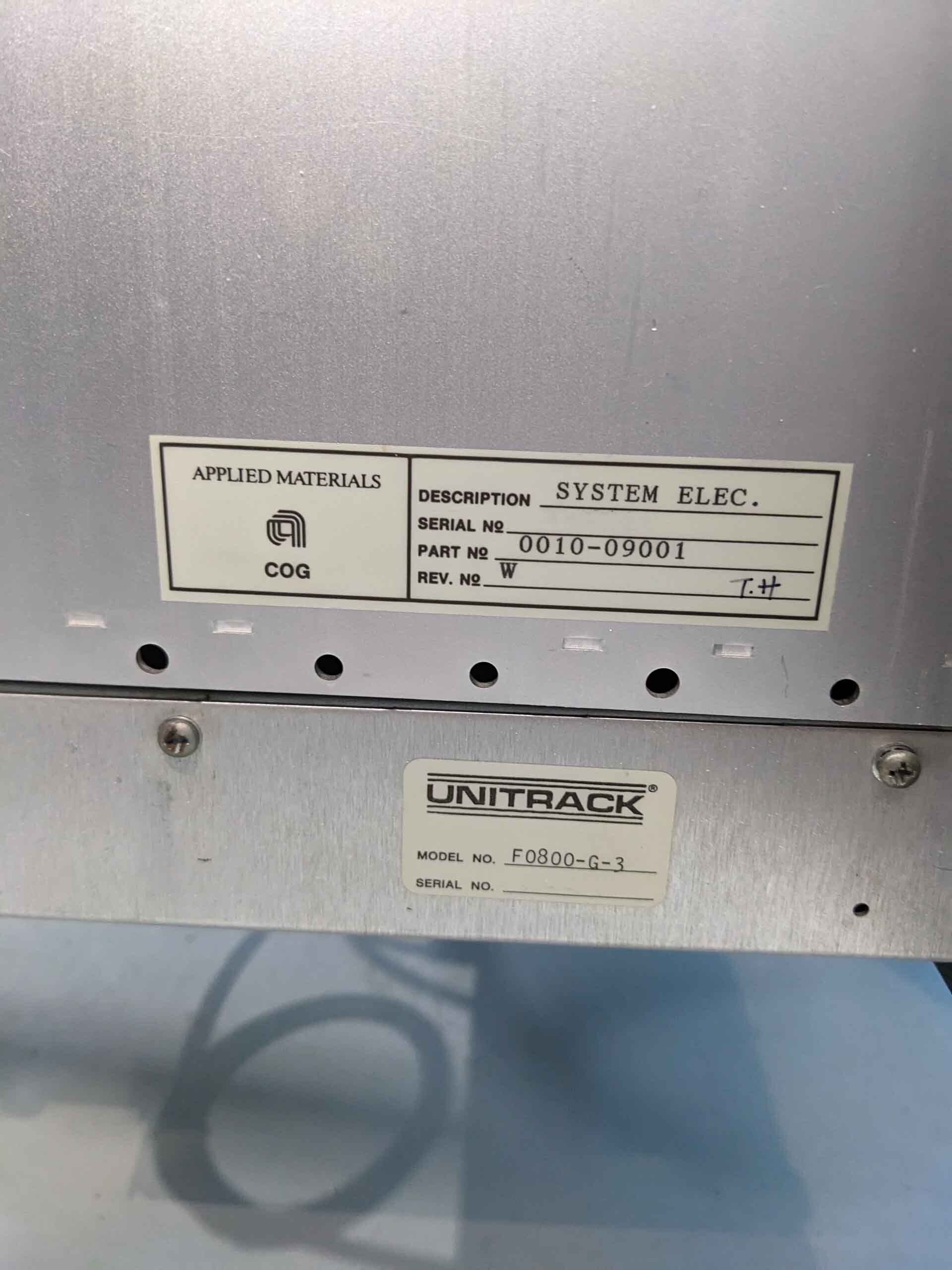

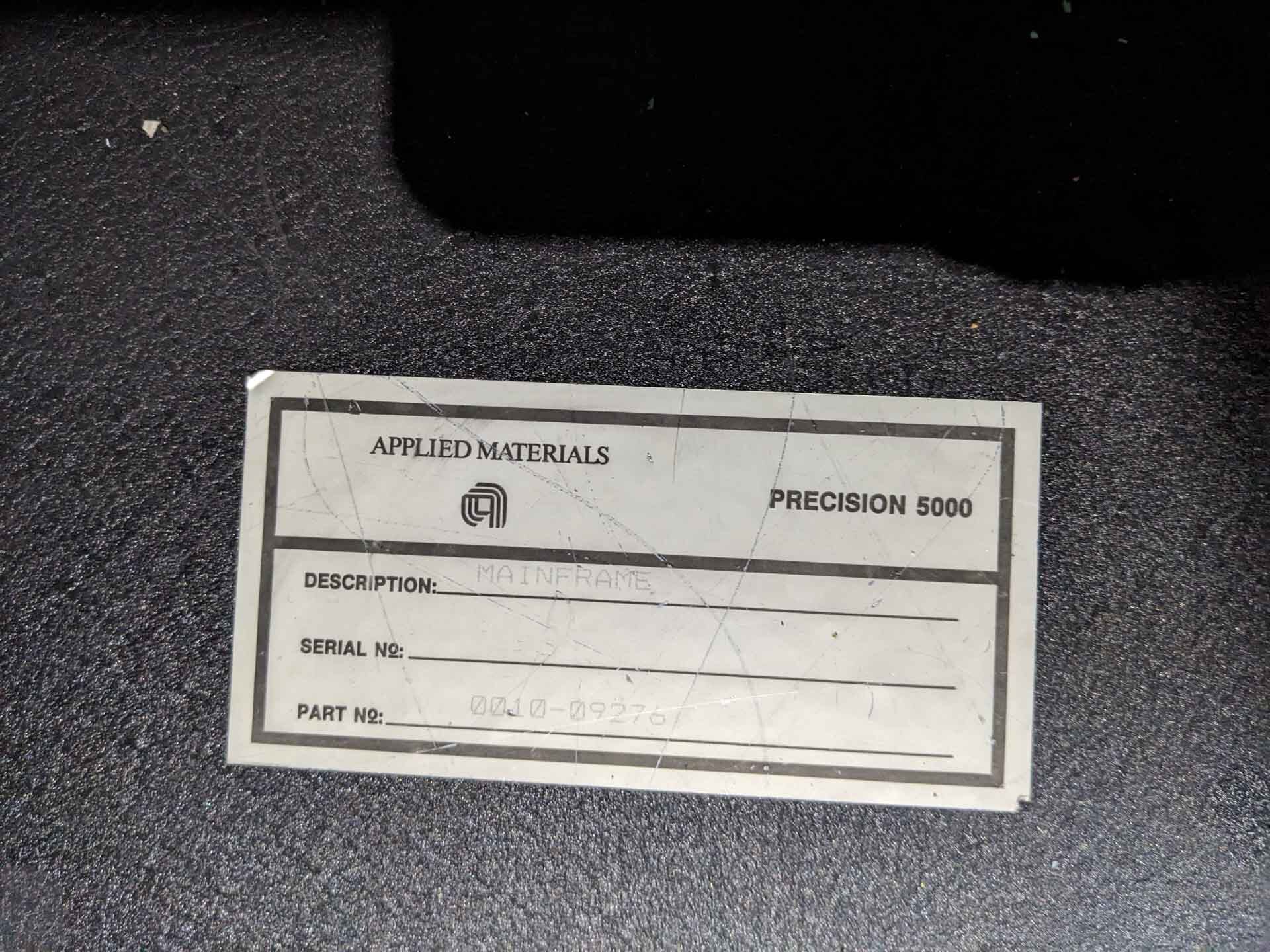

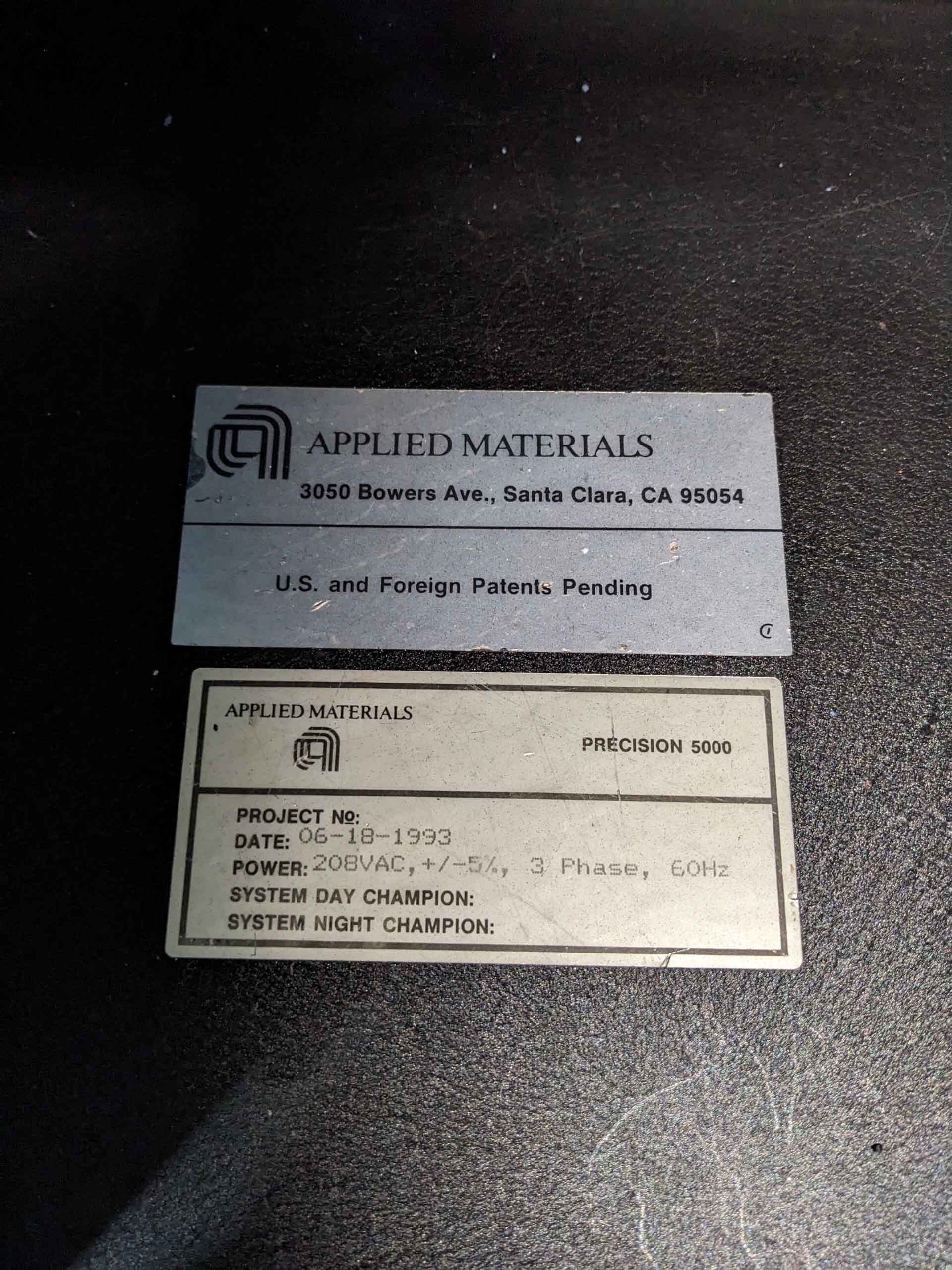

ID: 9389403
Wafer Size: 6"
Vintage: 1993
CVD System, 6"
SV21 SBC Board
Cassette indexer, 6" Clamp
8-Slots elevator
(2) CRT Monitors
Robots: Phase-III
Robot blade: Standard vacuum
Centerfinder: USE
Cap wafer sensor
AC Rack: 1 Shrink
Heat exchanger
Electrical controller
Nupro bellows valve
EMO Option: Turn to release
EMO Button guard rings
(4) ENI OEM-12A RF Generators
HX Seperate mani fold
Status light tower (Color / Position): Red, yellow, green, blue
Signal cable: 25"
Flash Hard Disk Drive (HDD)
Floppy: 3.5" SCSI Driver
Mini-controller
Electrical controller:
(2) TC Gauge boards
Power rack, 12 VDC; (2) 15 VDC
Buffer I/O board
(2) Opto I/O boards
(4) Chopper driver power racks
RF Generator:
Chamber A: OEM12B-02
Chamber B: OEM12B-02
Chamber C: OEM12B-07
Chamber:
Chamber position: A, B, D
Chamber type: DLH 1-Hole
Process: SiH4 Oxide
Heater type: Lamp
Susceptor type: Al
(4) Matchers
Delta nitride dual spring throttle valve
Gas panel: 20 Standard channels
Gas supply: Top down
MFC: SEC 4400MC
Manual valve: Fujikin
Pneumatic 2-Way valve: NUPRO
MKS 122B Baratron gauge, 10 Torr
(4) Pumping plates
(4) Ceramic focus rings
(4) Shower heads
(4) Blocker plates
(4) Heater windows
(4) Bellows susceptors
(4) Bellows wafer lifts
VME Controller:
1 / SBC Board
2 / SV21 SBC Board
3 / SEI Board
6 / VGA
7 / AO-1
8 / AI-1
9-12 / Stepper control board
13-16 / Digital I/O board
17 / -
19-20 / -
Gases:
Gas / Range
N2 / 3 SLM
SiH4 / 100 SCCM
CF4 / 2 SLM
N2O / 2 SLM
1993 vintage.
AMAT / APPLIED MATERIALS P5000 Mark II reactor is a high-tech, high-efficiency production tool for a range of semiconductor fabrication and fabrication-related processes. Using ultra-high vacuum (UHV) annealing technology and a powerful 5-axis motion control equipment, AMAT P5000 Mark II reactor is designed to achieve precise and repeatable process results while operating in a wide range of production atmospheres. APPLIED MATERIALS P 5000 MARK II reactor is a five zone, in-line UHV annealing system, each zone independently controlled and optimized to allow for optimal reactor performance. All three thermal zones are simultaneously temperature-controlled and purified using Helium/Oxygen/Hydrogen plasma chemistry. In addition, the UHV environment creates an inert environment free of molecular species which can introduce non-uniformities in the results. P 5000 MARK II reactor is designed to achieve the highest repeatability and reproducibility of process results. The 5-axis motion control unit automatically adjusts the processing parameters, while the control algorithms provide consistent and highly repeatable processing results. AMAT P 5000 MARK II reactor utilizes a number of advanced features to reduce the thermal budget, while ensuring the process results are repeatable and uniform. Specialized features such as chamber-in-chamber processing, an automated gas delivery machine, an inert atmosphere, and an integrated inductively-coupled plasma (ICP) source allow for optimal chamber performance. AMAT / APPLIED MATERIALS P 5000 MARK II's large 4.7 liter process chamber and quartz-glass tube design ensure efficient transport of process materials. The chamber is constructed to maximize process uniformity, with the reflective walls providing uniform coverage of the chamber for both thermal annealing and plasma processes. With the stainless steel construction, the chamber provides a robust and durable structure with temperature and thermal shock characteristics suitable for longer process times. APPLIED MATERIALS P5000 Mark II is an automated process solution, featuring an automated recipe development library, an integrated monitor and control tool, and an advanced control asset. The intuitive software gives users the ability to create, modify, and download recipes quickly and easily. The integrated monitoring and control model provides the user with real-time process monitoring, allowing the user to make accurate corrections to their process if needed. P5000 Mark II reactor is a powerful, precise and reliable tool suitable for a wide range of processes. Its precision temperature and motion control, intuitive software and robust construction make it an ideal choice for production environments.
There are no reviews yet