Used VEECO / EMCORE E400 #9265822 for sale
URL successfully copied!
Tap to zoom
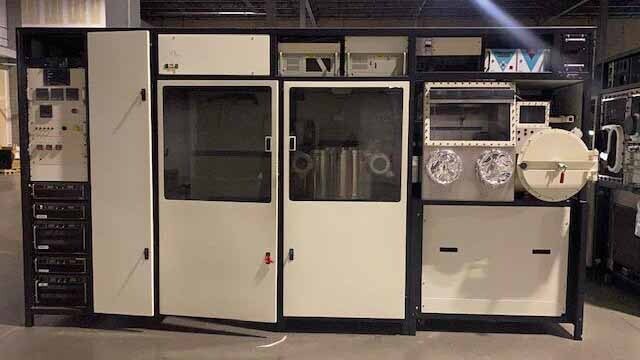

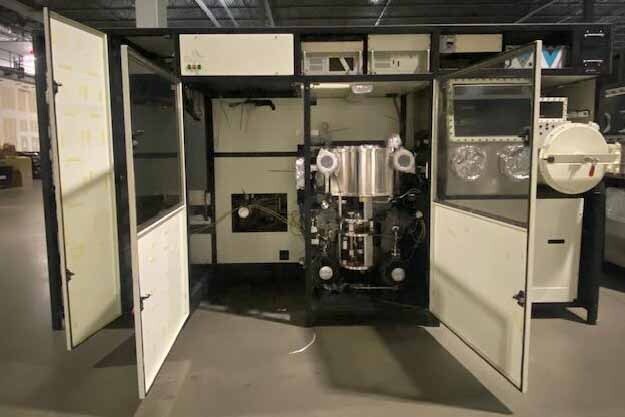

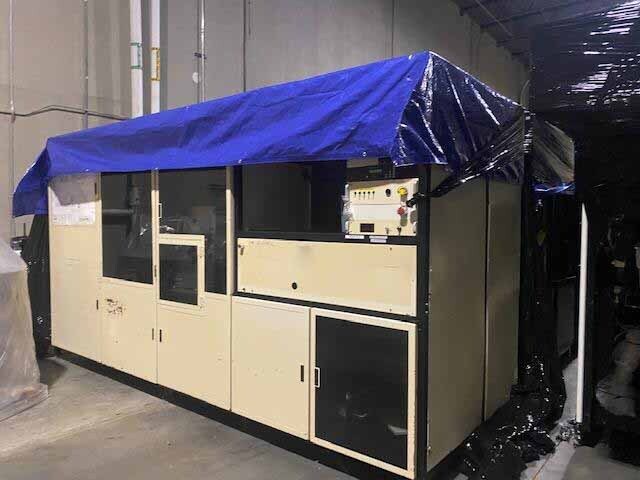

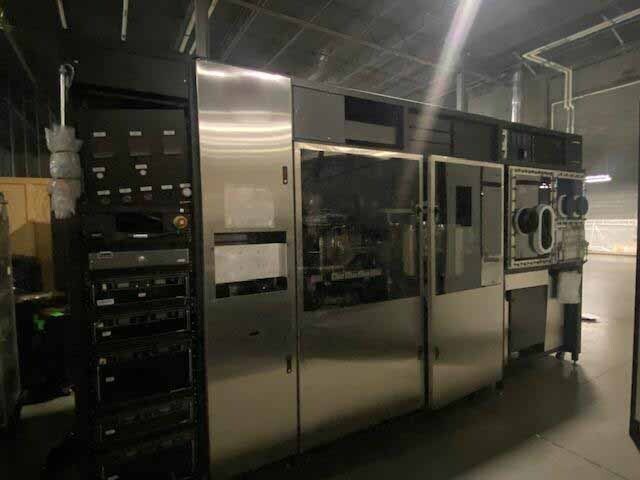

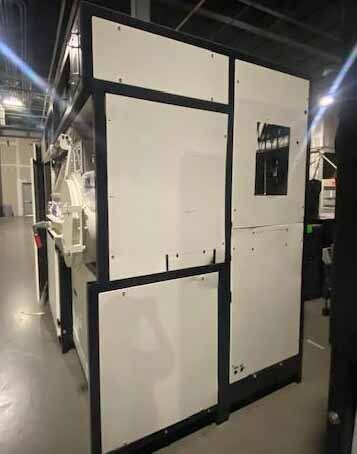



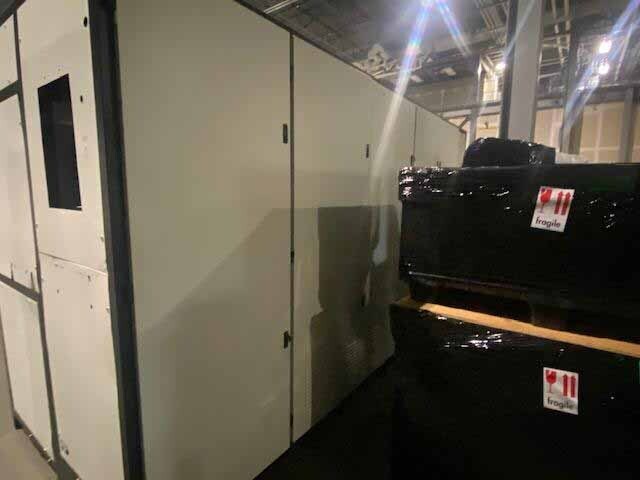

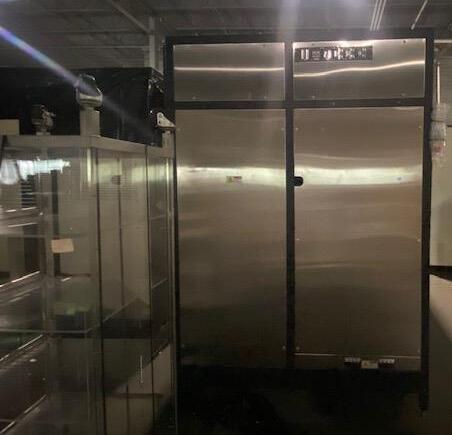

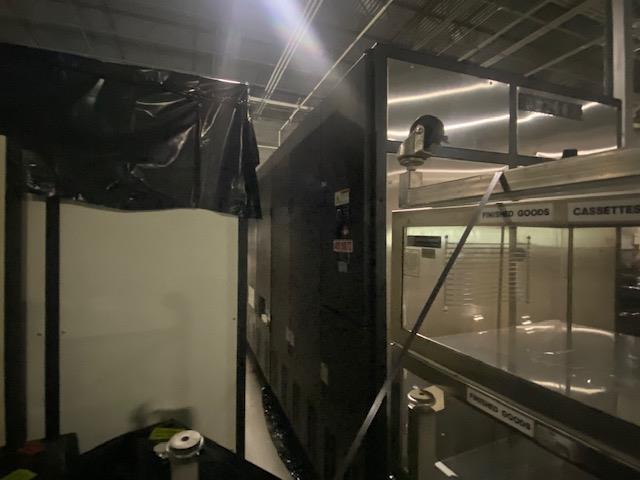

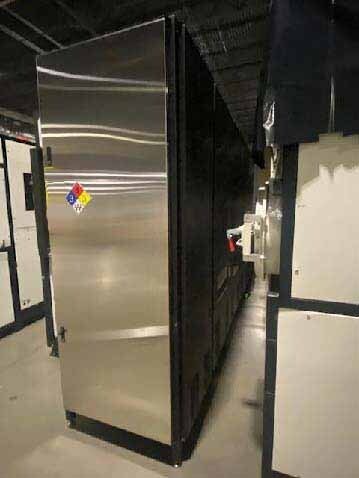

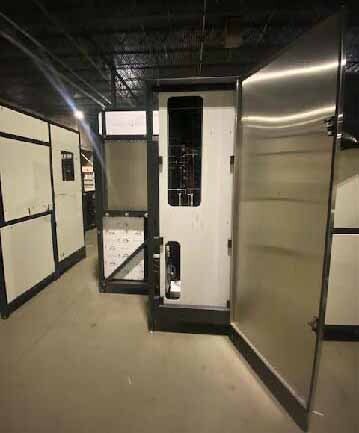

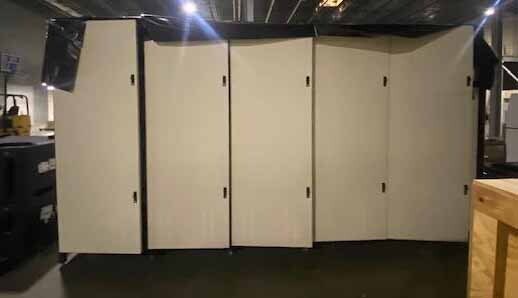

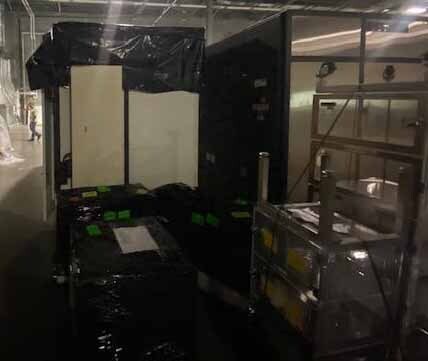

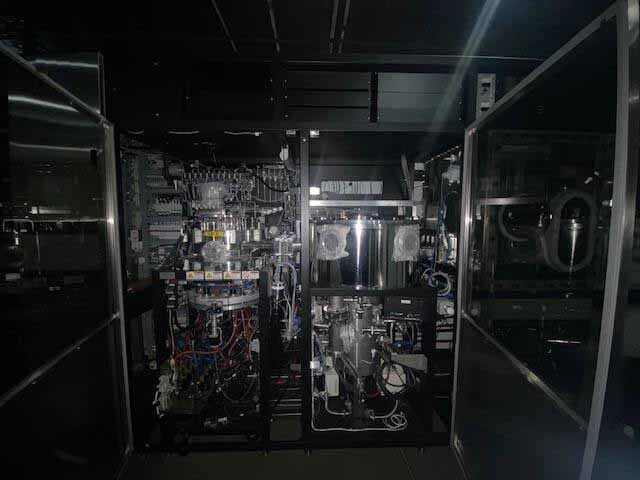

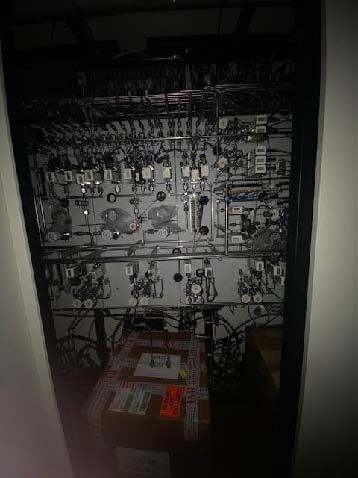

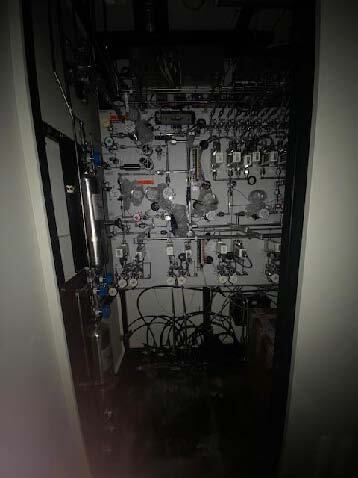

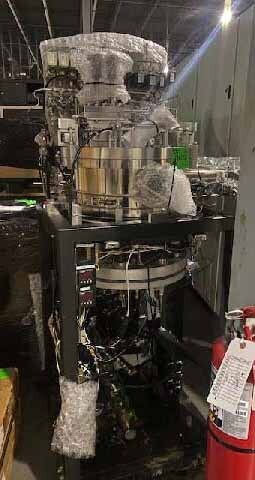

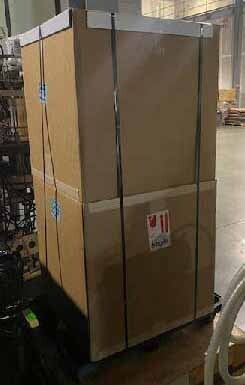

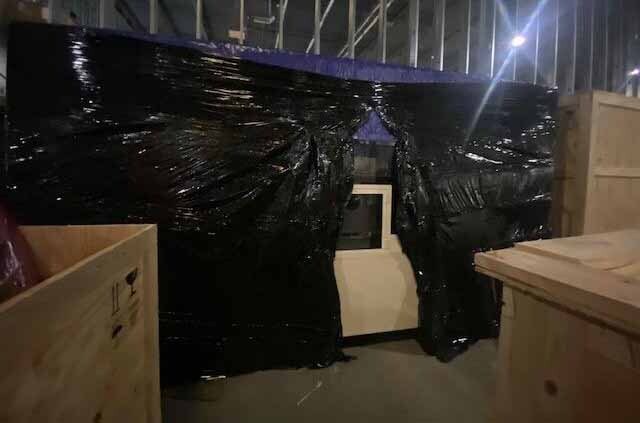



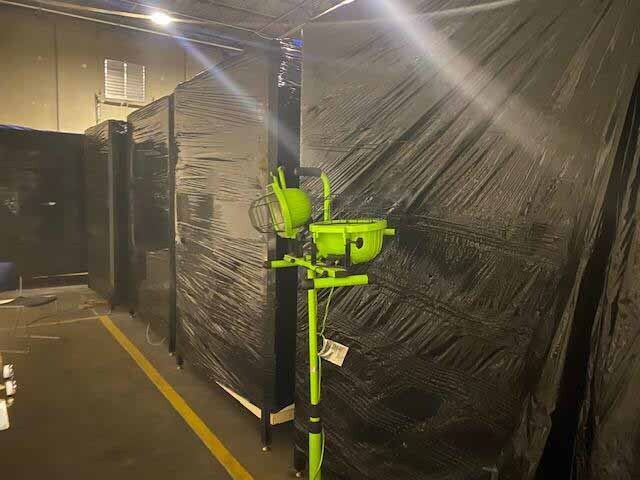

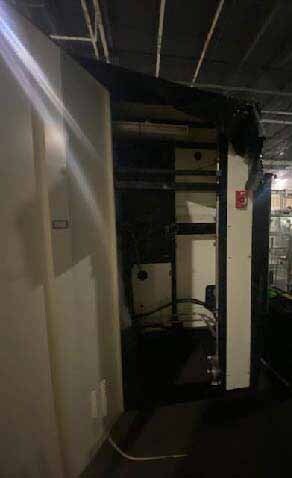

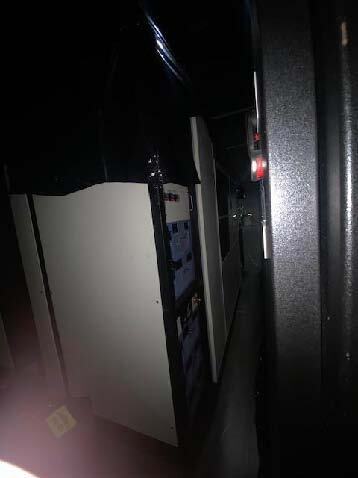

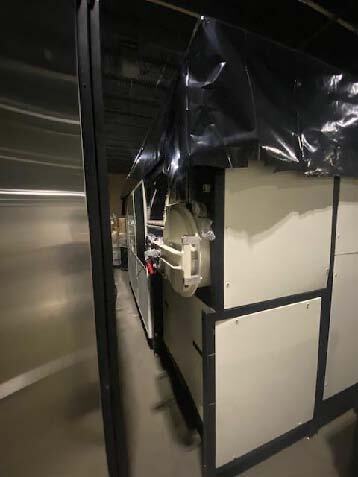

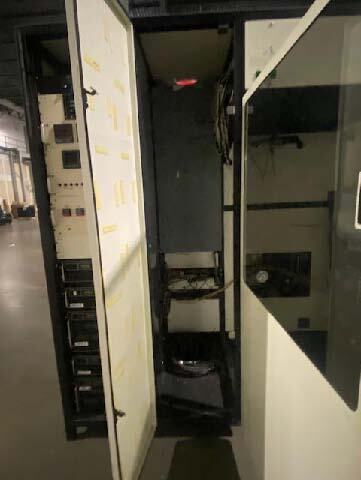

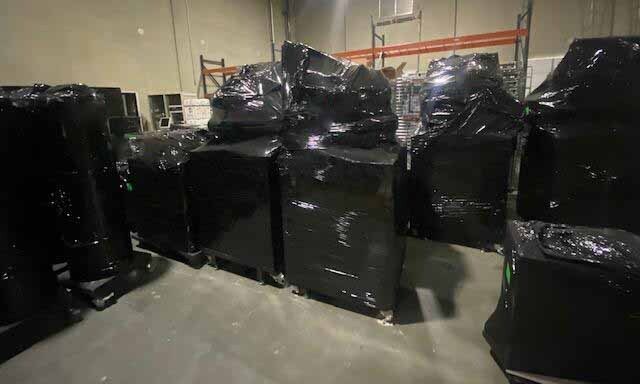

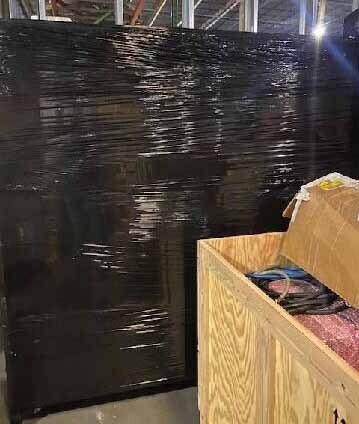

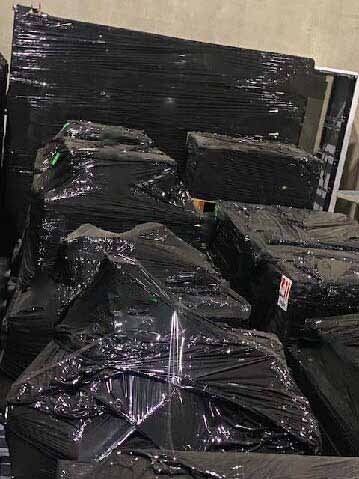

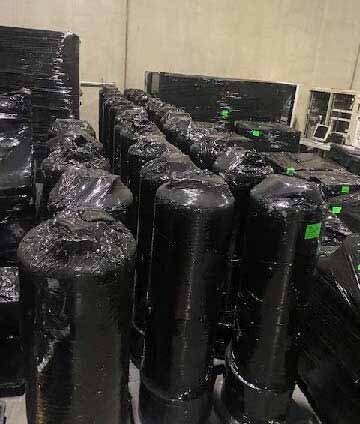

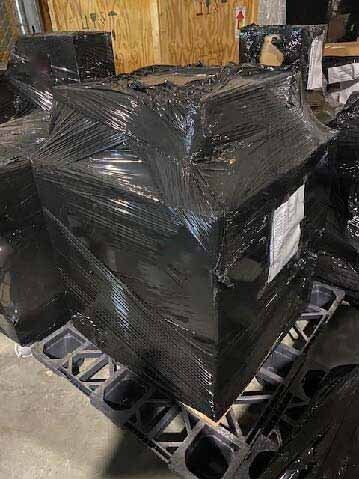

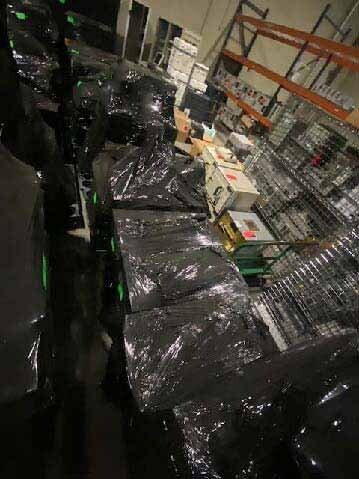

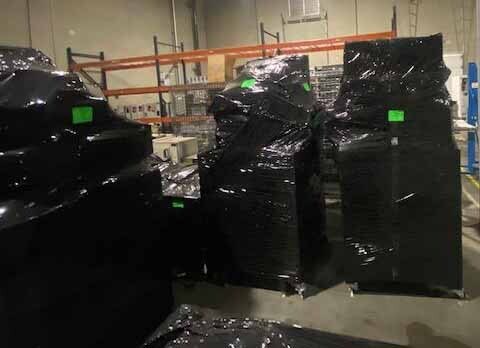

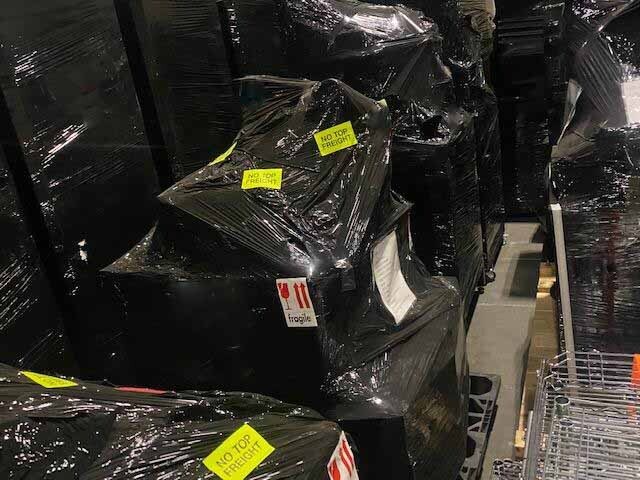

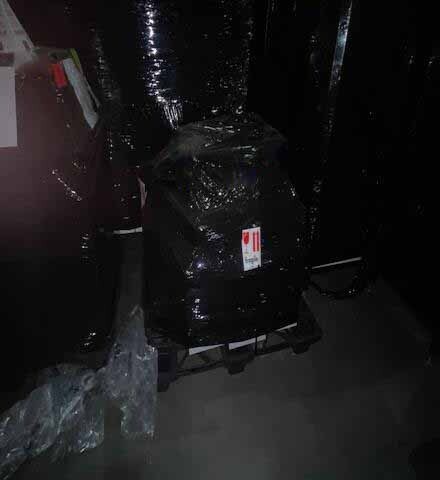

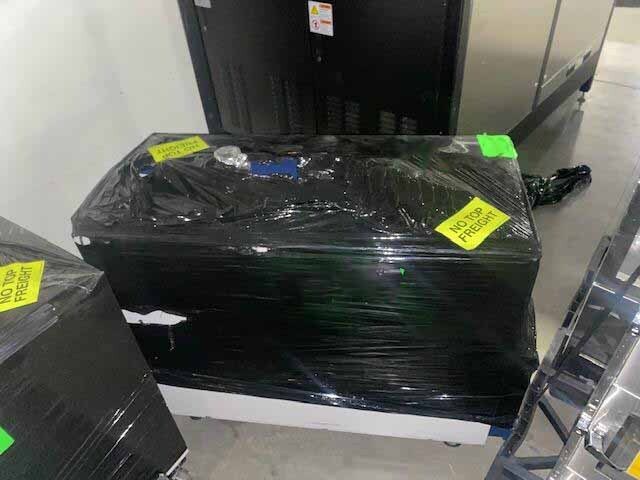

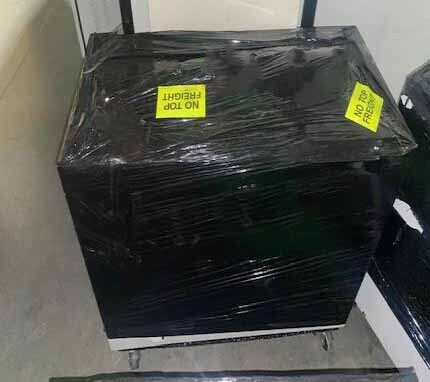

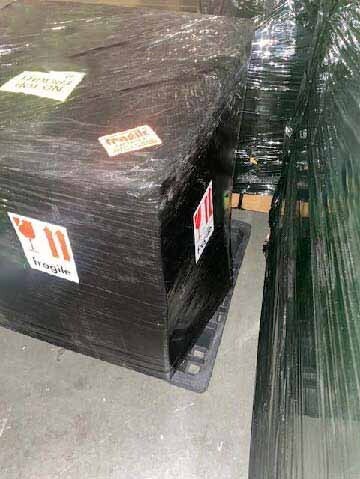

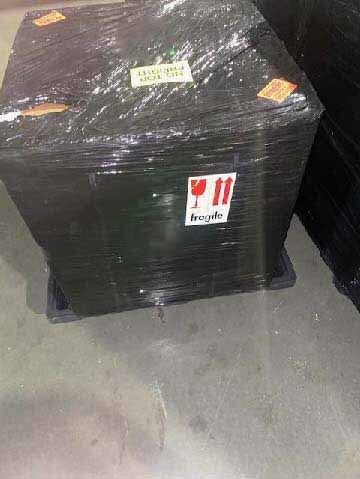

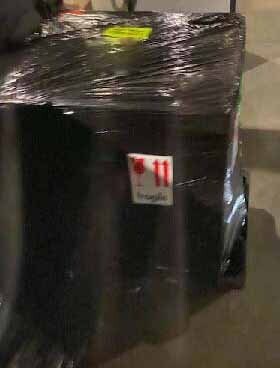

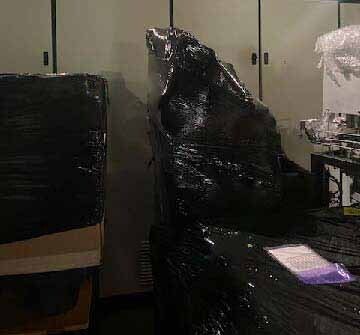

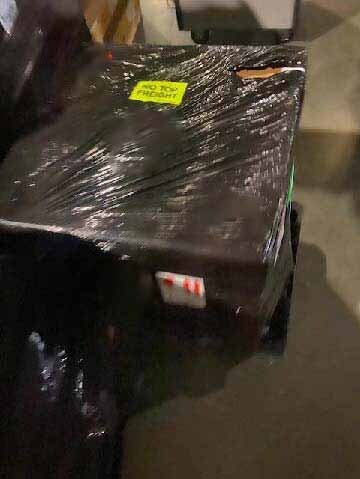

VEECO / EMCORE E400 reactor is a state-of-the-art substrate processing equipment designed for optoelectronic device manufacturing. VEECO E400 reactor utilizes a low-temperature, low-pressure hydrogen and ammonia ambient to create an optimized thin film deposition environment at a low cost. This produces high-quality, uniform coatings of various materials such as silicon and germanium for the fabrication of optoelectronic devices. The reactive plasma formed by dissociation of the hydrogen and ammonia produces a unique deposition process, that is well-suited for creating epitaxial or polycrystalline layers on substrates. The process in EMCORE E400 is carefully and precisely controlled via a computerized, networked controller which can be accessed remotely from anywhere in the world. E400 is a fully automated system for optoelectronic device fabrication, including the creation of thin layers on various substrates. It works by employing an electron beam evaporator, a quartz crystal monitor, and a rotating jig for uniform deposition. The electron beam evaporator vaporizes the source material resulting in a uniform coating of the desired material, while the quartz crystal monitor detects any changes in the layer being deposited and allows the controller to adjust the conditions as required. The rotating jig facilitates precise and even deposition of the layer. VEECO / EMCORE E400 reactor also features advanced monitoring, control, and data acquisition capabilities. All of the processes are monitored and controlled via a computerized network, allowing for full control of the furnace temperature and deposition rate. Additionally, the unit can store data from all monitored processes for later use in quality control and process optimization. VEECO E400 reactor is an efficient and reliable machine for creating high-quality, uniform coatings on substrates. It features advanced automated control and monitoring capabilities, enabling users to achieve optimal thin film deposition conditions at low cost. Moreover, its use of advanced technology allows for consistent quality and uniformity of the layers, thus providing superior optoelectronic device fabrication results.
There are no reviews yet