Used CVC 601 #28214 for sale
URL successfully copied!
Tap to zoom












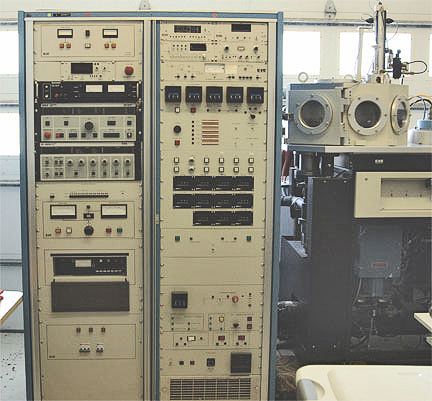

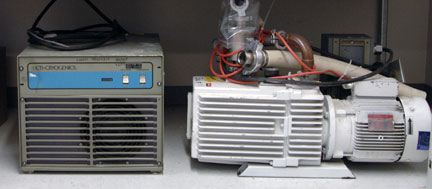

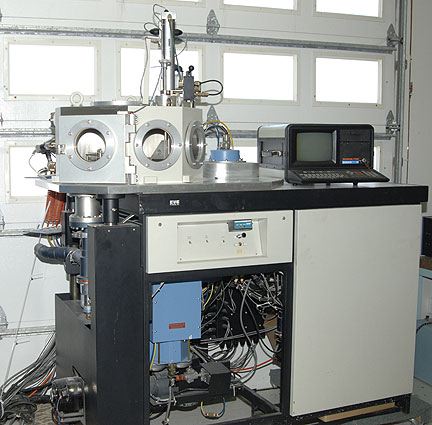

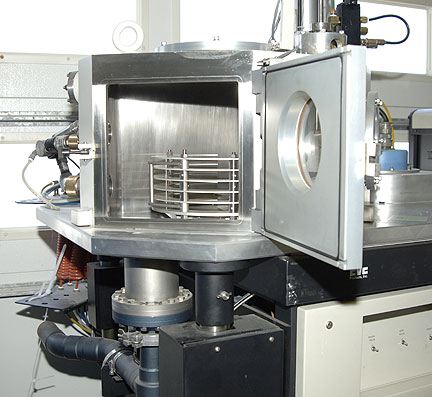

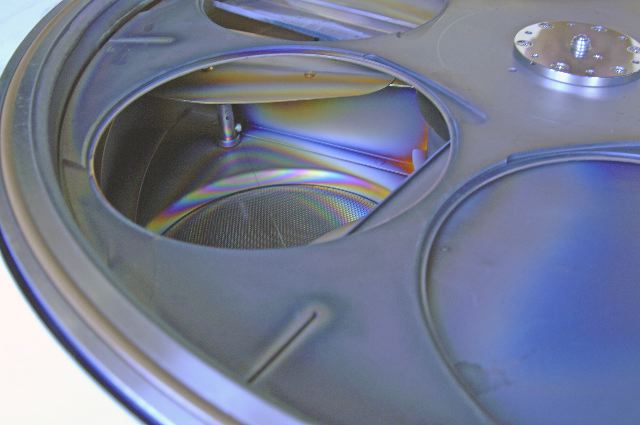

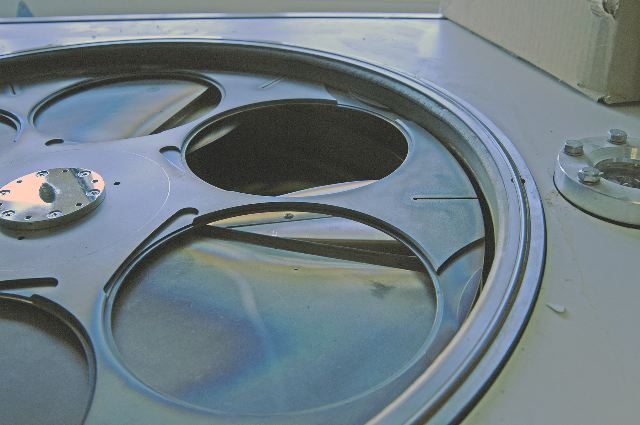

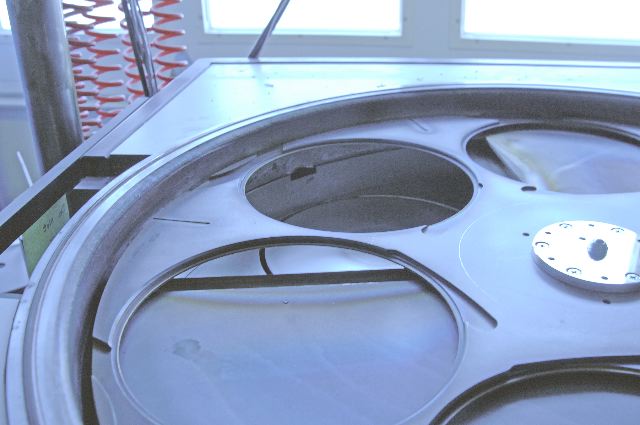

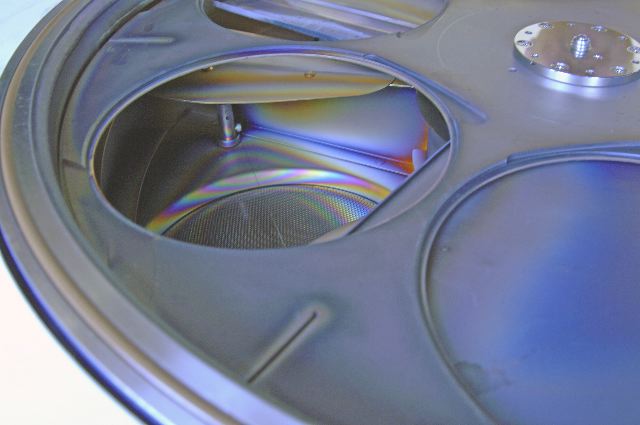

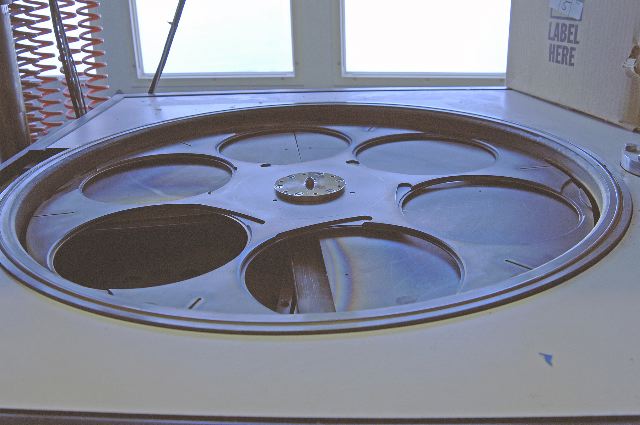

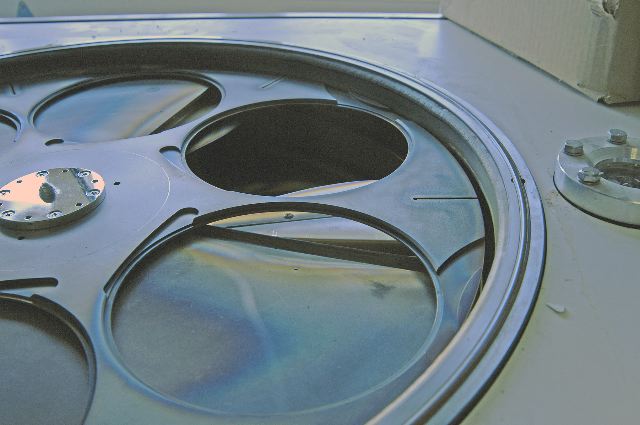

ID: 28214
Wafer Size: Up to 8"
Vintage: 1986
Batch type production sputtering system, up to 8"
Currently setup for Argon and Oxygen with the possibility for Nitrogen
Computer and cryopump included
Works in manual mode
4 targets / wafer holders
Top loading machine
(Qty 4) work stations in the flat bottom of the 7" high work chamber
(Qty 2) DC stations
(Qty 1) RF station
(Qty 1) Ion cleaning station
Work heater / sintering accessory in the lid
Accessories for sputtering in several modes including DC Diode, RF Diode, DC Plasma Enriched Deposition ( PED, planar magnetron) and RF PED
Composed of a relay rack control center and cabinet which contains the vacuum chamber and pumping system
The computer interface is a Gould Model 484 Programmable controller
The DC Sputter Supply is an 10 KW Advanced Energy MDX Magnetron Drive
Unit has a CVC 3 KW AC Power Supply and a CVC 1 KW AC Supply
(Qty 4) Targets include:
Barium Titinate
Molybdenum Trioxide
Inconel
Titanium or Silicon
There are 4 target positions:
(Qty 1) RF Magnetron gun and matching unit
(Qty 2) DC Diode Sputtering unit with magnets in them for magnetron sputtering
The 4th target position has an Ion Cleaning Source
Project used only the RF PED Target position, DC targets were not used, in manual mode
Previous project used system with a P190/484 Programming panel
(Qty 2) Mass Flow Controllers
There is a cryo controller for N2-purge, and regeneration
Log book included
Packaged and stored
As-is
1986 vintage.
CVC 601 is a state-of-the-art sputtering system developed by Cambridge Vacuum for a range of scientific applications. It is composed of a large vacuum chamber with an anode andCathode, which can be adjusted to allow for sample insertion and working distance. The Cathode is made from stainless steel, whereas the anode is constructed of tungsten. The sputtering chamber is enclosed in a glove box through which air is pumped to create a high vacuum. A gas such as helium, argon, or nitrogen can be used to fill the chamber. To charge the cathode, it is connected to a high voltage power supply. The voltage can be set up to 3000V. 601 contains various control systems, including a process control unit (PCU), a power control unit (PCU), and a cooling control unit (CCU). To ensure smooth operation, there are two water cooling channels and high-purity graphite support plates. For additional safety, CVC 601 features a vacuum gauge sensor to monitor the effects of the sputtering. Before use, 601 must be baked to a required temperature (usually 800°C for a few hours) to remove moisture and other potential contaminants. After this is done, the system can be turned on and the process started. The sputtering process begins with the charging of the cathode from the power supply. This creates a DC field and electrons are accelerated to the anode. When the electrons come into contact with the anode, they are absorbed and the material on the anode surface is sputtered off. The sputtered material then coats the target material, forming various layers. After the sputtering process is complete, the remaining material can be removed from the anode with a scraper. CVC 601 is then ready for further processing, such as annealing, etching, and deposition. Overall, 601 sputtering system is an invaluable tool for scientists and engineers involved in thin film processing. Its advanced control systems ensure accuracy and reproducibility of results and the ability to charge, sputter, and anneal at high temperatures is unparalleled. Its flexible design also makes it easy to expand and develop, allowing for optimal customisation for individual applications.
There are no reviews yet