Used DNS / DAINIPPON SU-3100 #293627839 for sale
URL successfully copied!
Tap to zoom
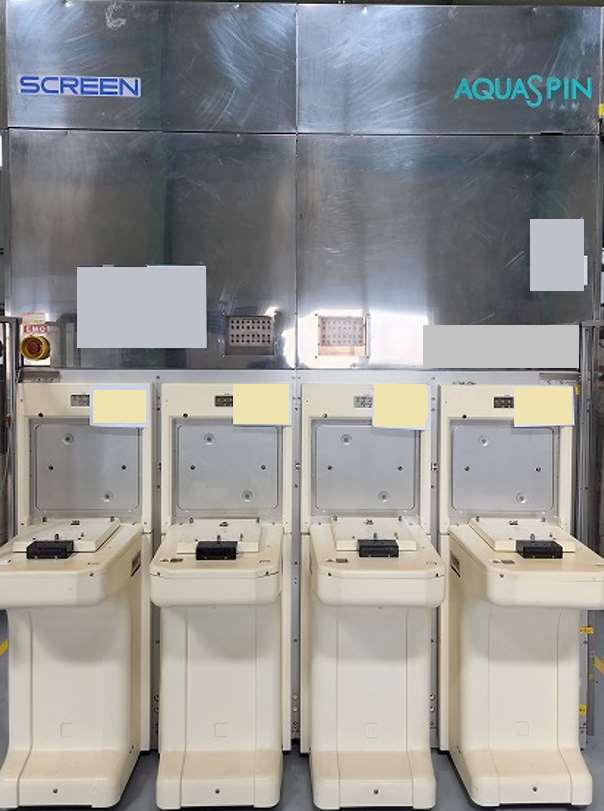

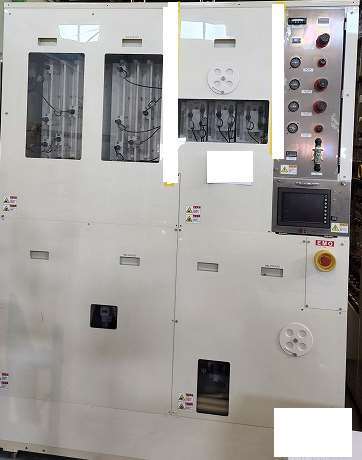

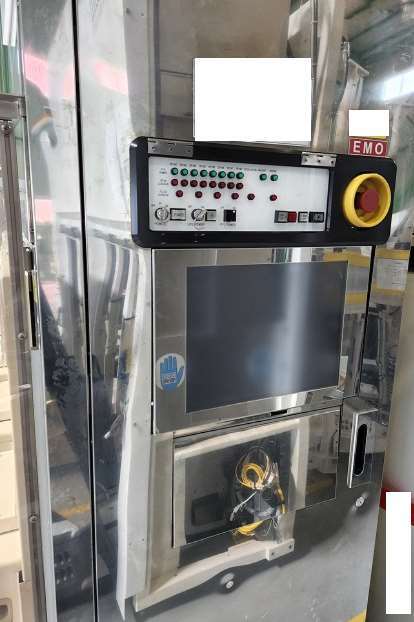

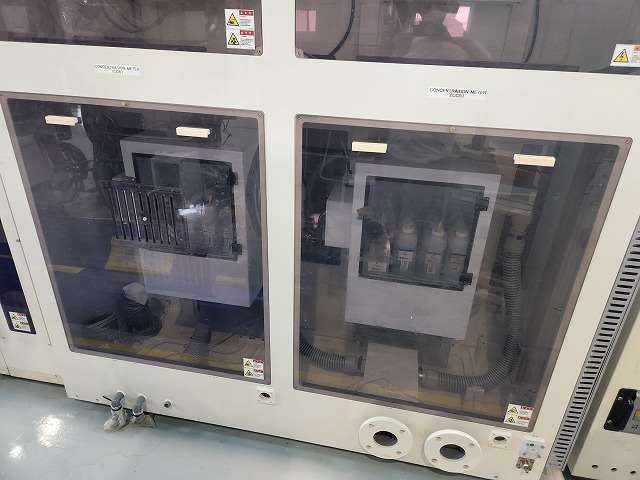

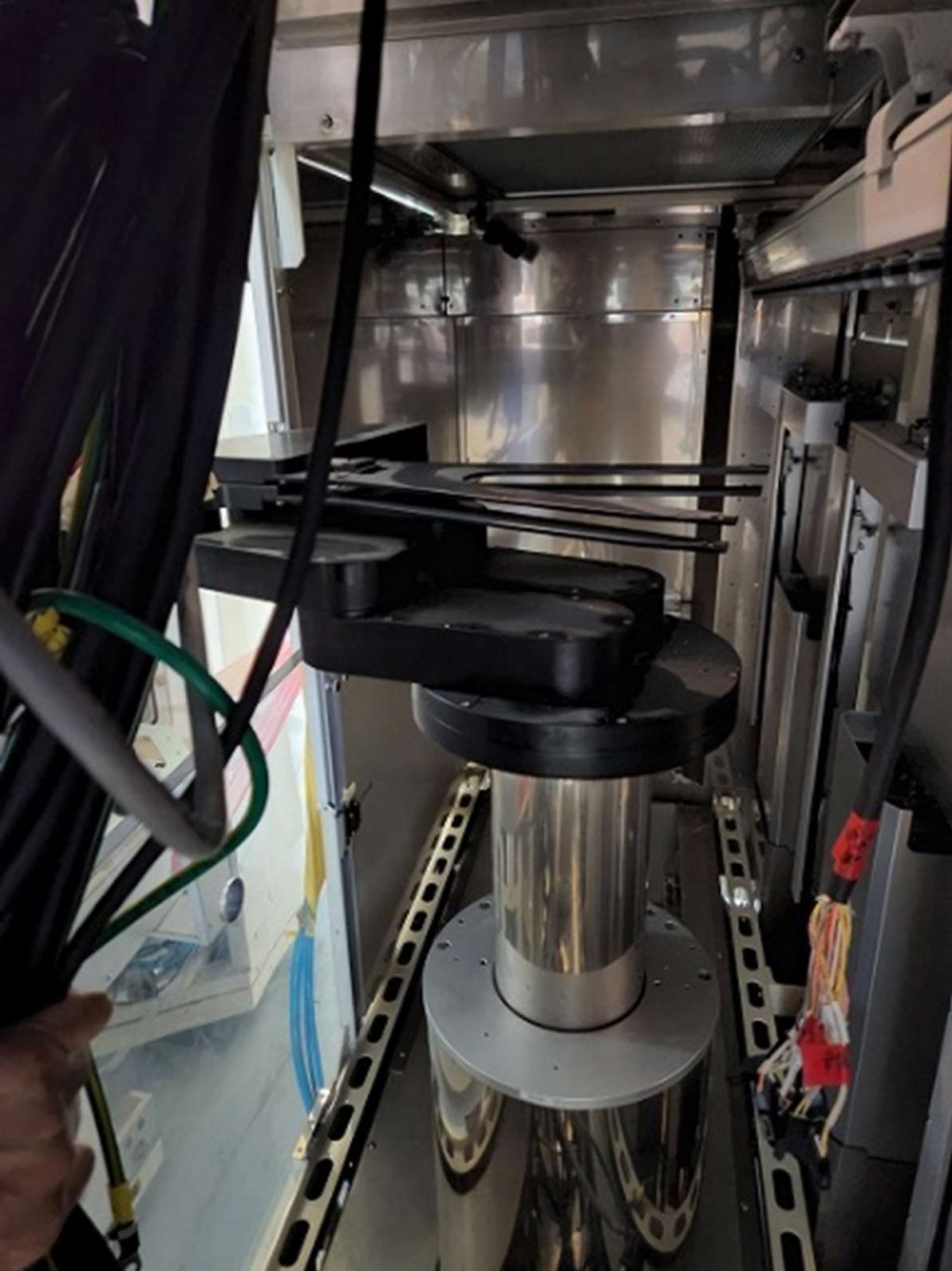

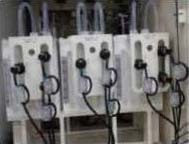

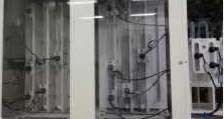

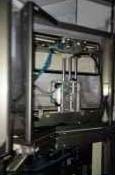

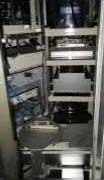

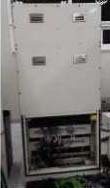

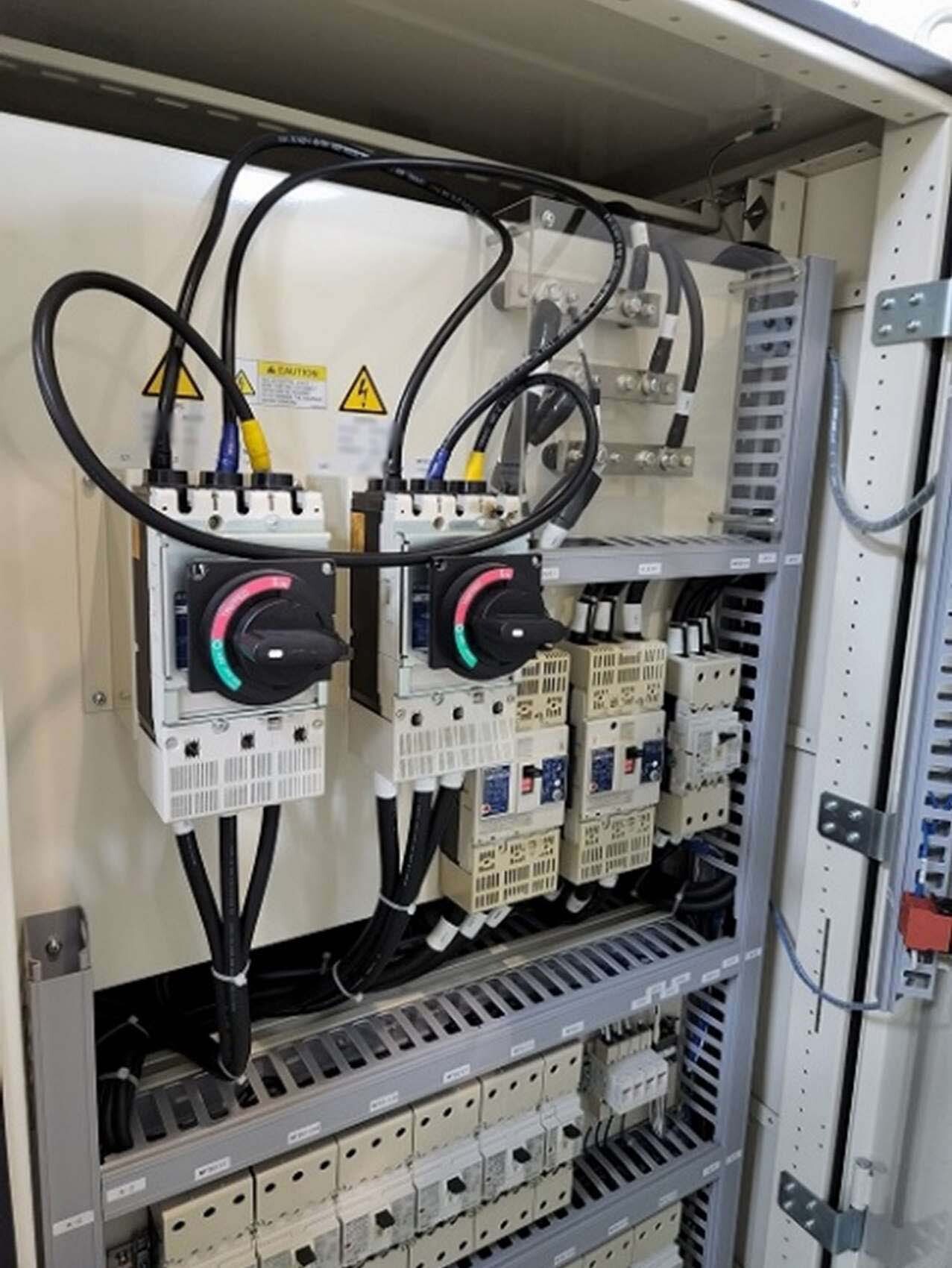



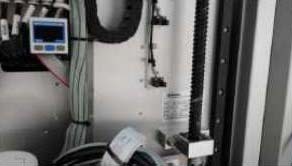

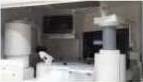

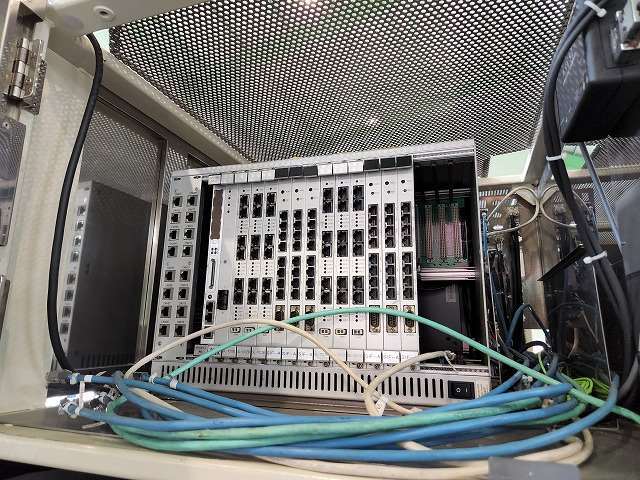

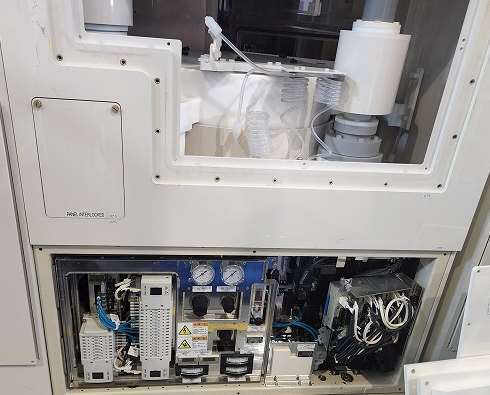



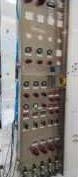

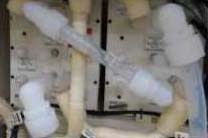

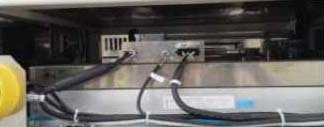

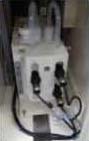

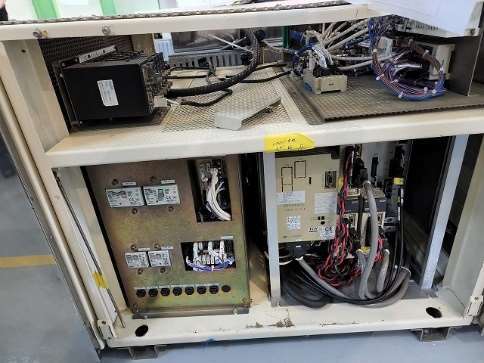

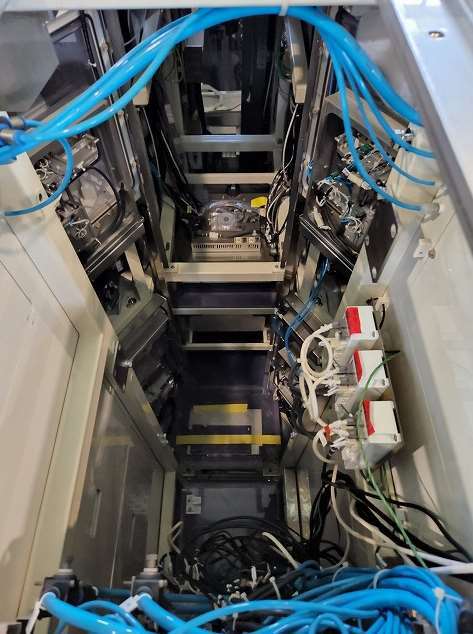

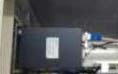

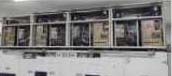

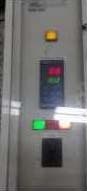

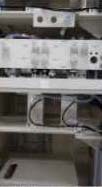

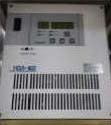

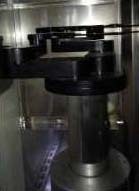

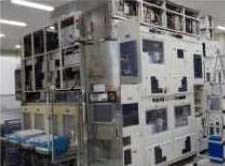

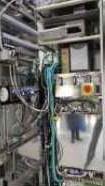



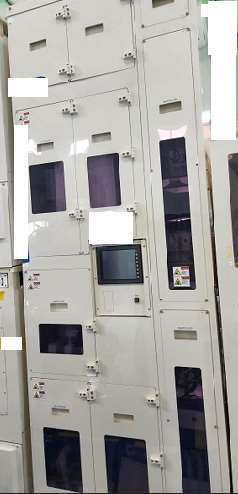

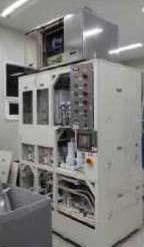

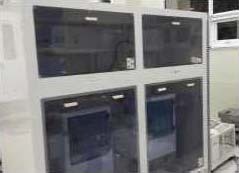

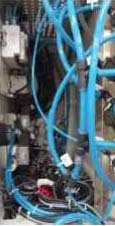

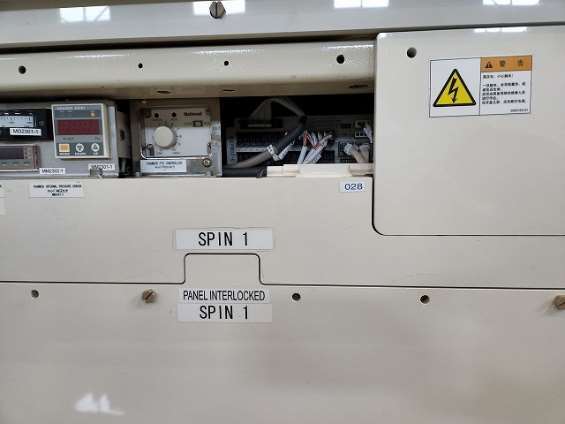

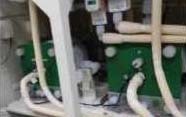

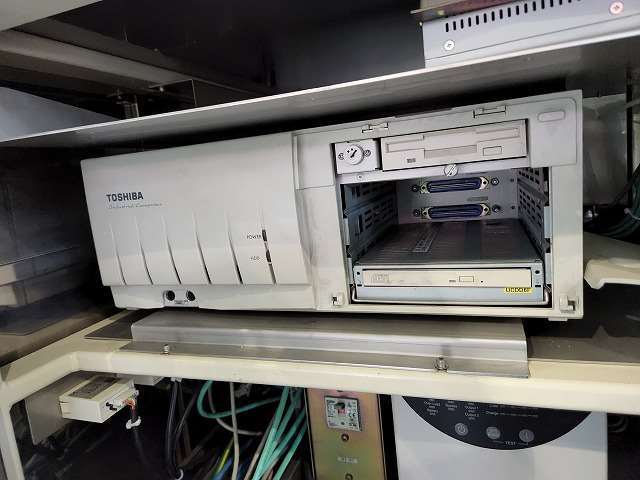

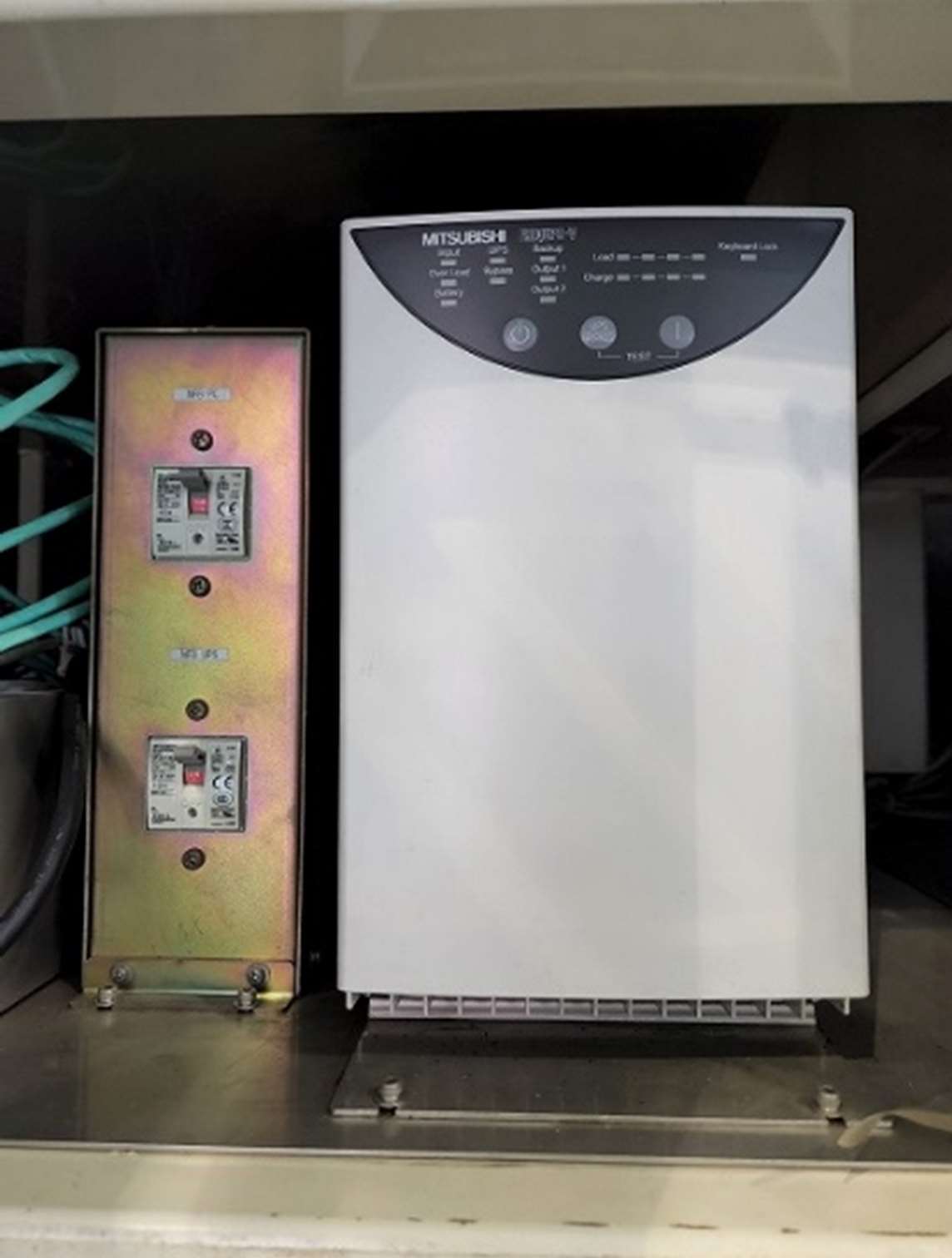

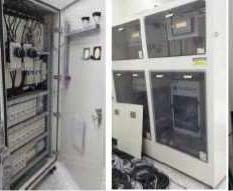

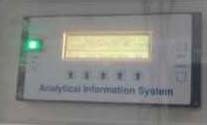

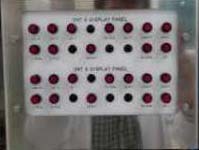

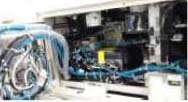

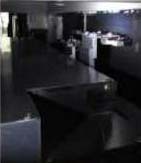

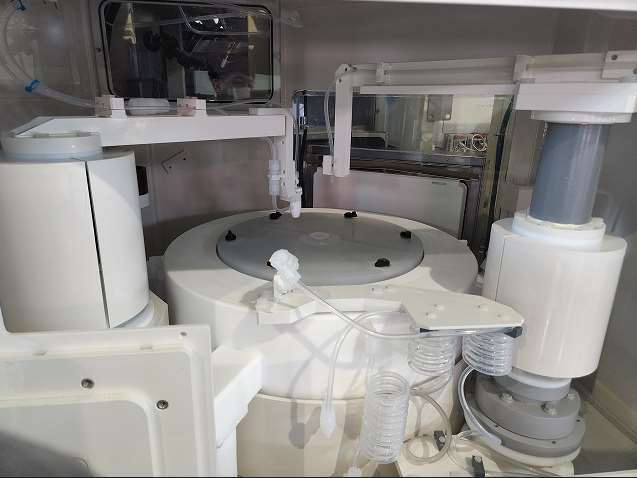

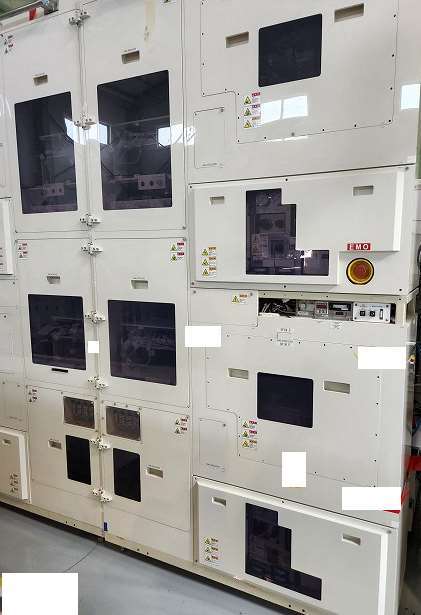

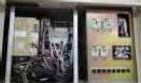

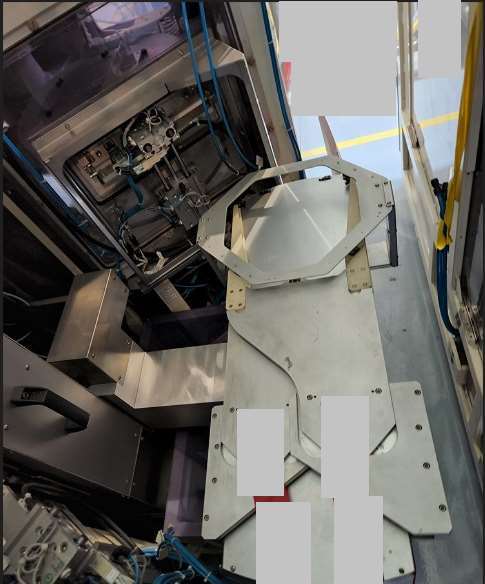

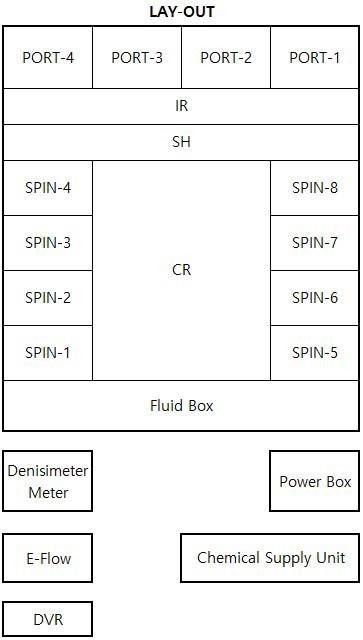

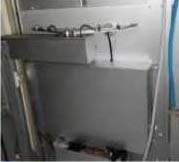

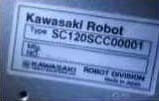

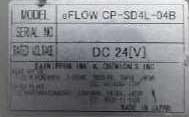

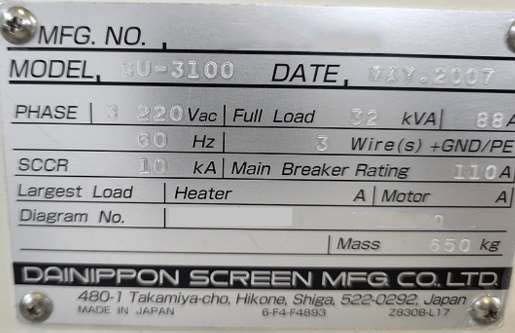

ID: 293627839
Wafer Size: 12"
Vintage: 2007
Wafer cleaning system, 12"
(8) Chambers
(4) Load ports
Powerbox
Densimeter
E-Flow
DVR
Chemical supply: HF, H2SO4, H2O2
Nozzle:
Chemical (Spin 1-8)
Side rinse
E-Flow (Spin 1-8 and front)
Nano spray
Rinse back rinse
UMC Controller
Index R IDA
(2) CR Stages
Spin unit:
Left: 5, 6, 7, 8
Right: 1, 2, 3, 4
IR:
W/F Sensing penetration type: Photo sensor
Arm Y-Axis servo-motor
OARM X, Y-Axis stepping-motor
CR:
W/F Sensing penetration type: Photo sensor
ARM Y,Z AC Servo-motor
Missing:
Hard Disk Drive (HDD)
Fire suppression
DI Resistivity sensor: AS
Flow meter sensor: RK
Power supply: 220 VAC, 60 Hz, 3 Phase
Full Load: 32kVA, 88A, 60 Hz
3 Wires with GND/PE
Breaker rate: 110A
SCCR: 10kA
2007 vintage.
DNS / DAINIPPON SU-3100 is a wet processing station that utilizes reactive ion etching (RIE) and chemical-mechanical polishing (CMP) technologies to create products made from semiconductor materials. The wet station enables precise and reproducible etch and polish processes in order to obtain high-quality substrates with minimal surface roughness. The wet station consists of a chemically-resistant stainless steel chamber with an internal vacuum equipment, an ion source, a resistive heating element, a mechanical wafer carrier, and an array of process gasses. The chamber is also equipped with a number of port plugs for connection to other vacuum systems and process components. The chamber also includes a load lock for transferring wafers in and out of the chamber without exposing them to ambient atmospheric pressure. The ion source is used to energize the process gases and create a plasma with controllable density and composition. The heating element is used to control the pressure and temperature during the etching process, while the mechanical wafer carrier ensures that the wafers are held in place securely throughout the process. The chamber also has high-vacuum pumps for evacuating the process gases, as well as a vent port for venting the by-products of the etching reaction. In order to maintain a safe, clean working environment, the wet station is also equipped with an air scrub system and an automatic nitrogen delivery unit. The air scrub machine removes particulates and other contaminants from the incoming air, while the nitrogen delivery tool maintains a consistent process atmosphere inside the chamber. The wet station offers highly accurate etching capabilities and advanced process monitoring, enabling the production of products with extremely high levels of accuracy and repeatability. It is capable of processing different material types, such as metals, oxides, polymers, and compounds. Furthermore, it is designed with a modular architecture and can be easily upgraded to meet customer needs.
There are no reviews yet